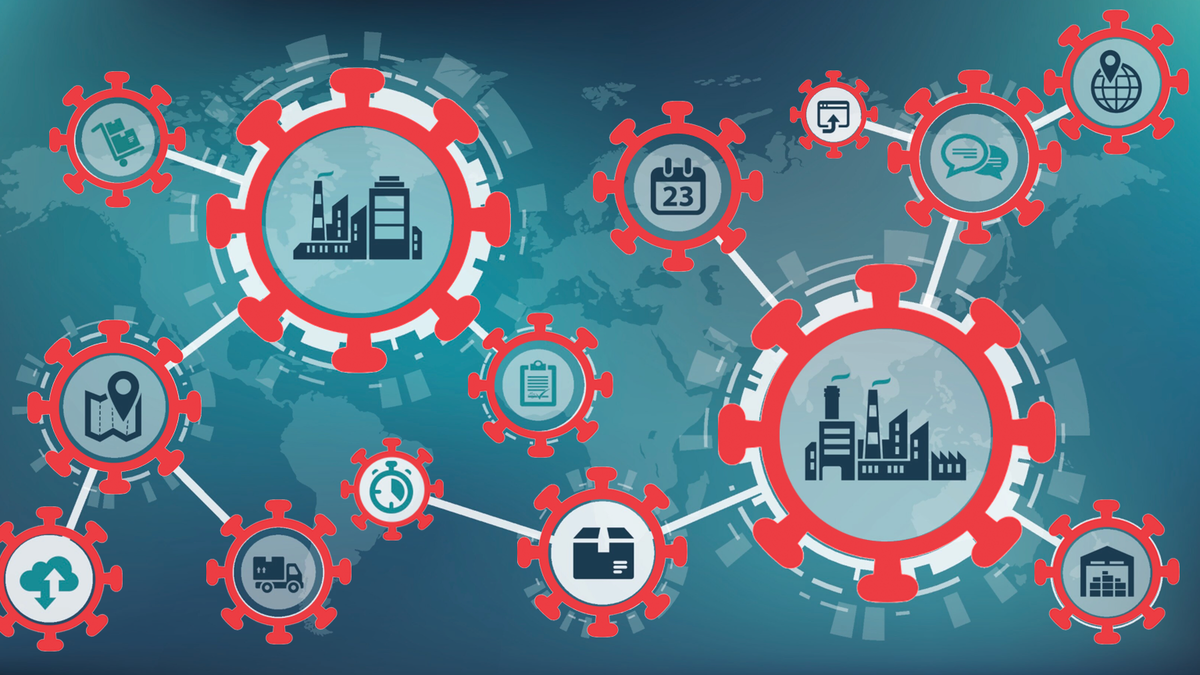
Originally known as Just-in-Time production, Toyota Production System is an integrated socio-technical system that is used to eliminate waste and improve processes. It is designed to efficiently organize manufacturing, logistics, and customer interaction. It promotes continuous improvement, employee development, and encourages employee advancement. It is also the foundation for Lean Manufacturing. Toyota Production System has been applied to many manufacturing facilities in the United States and overseas.
Sakichi Toyoda, the founder of Toyota developed the Toyota Production System. Sakichi Toyoda analyzed each phase of his company's production, and removed all unnecessary parts. This led to a 20% drop in build times. Toyota also had to build a vehicle half the time it took GM. Toyota was at the brink of bankruptcy in the early 1950s.
Taiichi Ohno was a Toyota executive who observed how supermarket shelves were stockpiled in the mid-1940s. He realized that Just in Time production of vehicles could be time-saving. He collaborated with EijiToyoda, Toyota's president, to develop the Toyota Production System in 1948-1975.
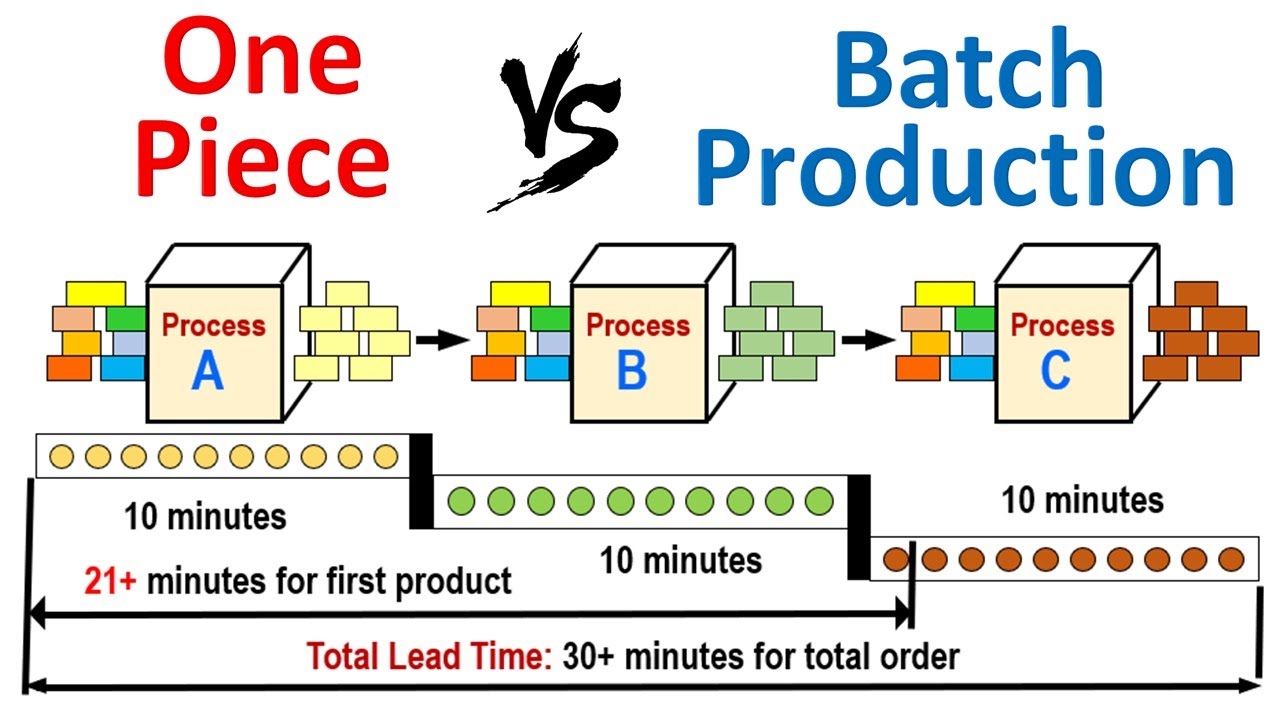
Toyota Production System was built to eliminate waste, inconsistency and inefficiency. Kaizen, the Japanese word for continuous improvement, was the underlying philosophy of the Toyota Production System. Toyota's Production System is continually improved to meet company needs. It fosters learning in the company. It uses simple but efficient low-tech tools, combined with advanced production methods. It also employs advanced information technology, as well as unique social/management methods.
The Toyota Production System was built around six core principles. It has been adapted by numerous companies including Boeing, Porsche, and Honda. These companies reengineered processes in order to copy Toyota's production systems.
Toyota Production System includes activities for team building. These activities include weekly leader safety rounds that evaluate staff's performance with key safety initiatives. The team is encouraged to exchange ideas and look for ways to improve. This has influenced the culture of the company.
Another concept is Jidoka, which refers to automating processes with a human touch. Jidoka encourages workers inspect their work and stop production if they find any problems. Jidoka stresses the importance of correcting mistakes and not ignoring them.
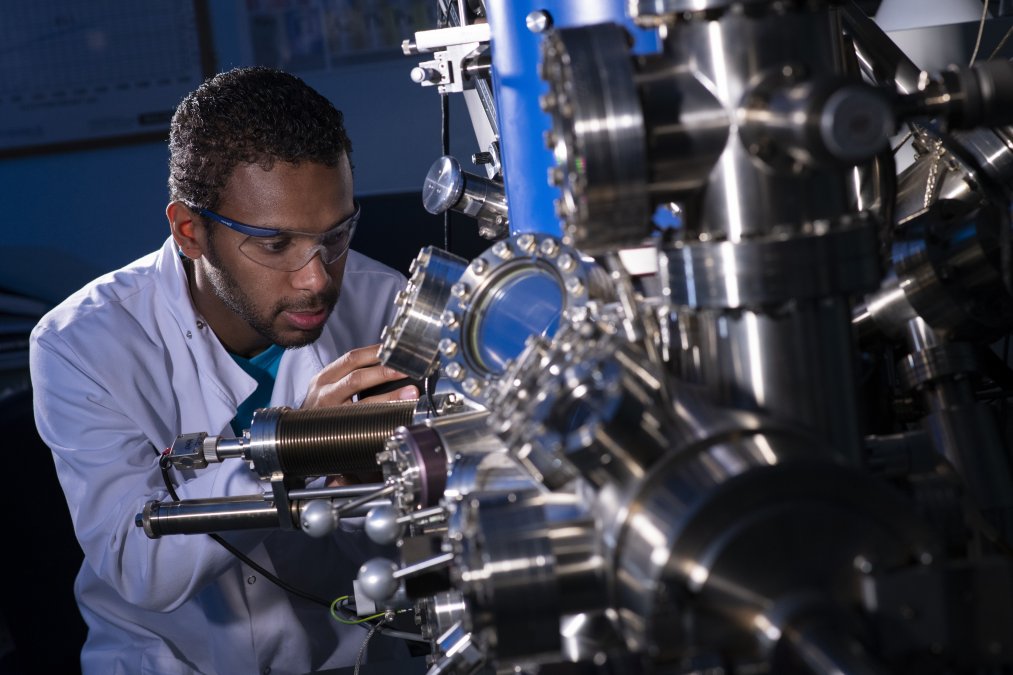
Visual control is also used in the Toyota Production System. This system makes instructions for workers visible on the factory floor. This ensures workers follow the instructions exactly. The poka-yoke device is used to check the quality of products. These devices can also be used for identifying red rabbits.
Toyota Production System can be used to produce plants as well as health care. It can be used to improve patient satisfaction. It can be used in critical care and the operating rooms.
The Toyota Production System can be used to increase patient satisfaction and improve health care delivery. In 2003, an EPA case study reported that Toyota's efforts in waste reduction had caught the EPA’s attention. This led to several partnerships with companies including the St. Bernard Project, which employs military vets.
FAQ
Can we automate some parts of manufacturing?
Yes! Yes. The Egyptians discovered the wheel thousands and years ago. Today, robots assist in the assembly of lines.
There are many applications for robotics in manufacturing today. These include:
-
Robots for assembly line
-
Robot welding
-
Robot painting
-
Robotics inspection
-
Robots that create products
Automation can be applied to manufacturing in many other ways. 3D printing makes it possible to produce custom products in a matter of days or weeks.
What is it like to manage a logistics company?
To be a successful businessman in logistics, you will need many skills and knowledge. You must have good communication skills to interact effectively with your clients and suppliers. You need to understand how to analyze data and draw conclusions from it. You need to be able work under pressure and manage stressful situations. To improve efficiency, you must be innovative and creative. You must be a strong leader to motivate others and direct them to achieve organizational goals.
To meet tight deadlines, you must also be efficient and organized.
What is production planning?
Production planning is the process of creating a plan that covers all aspects of production. This includes scheduling, budgeting and crew, location, equipment, props, and more. This document will ensure everything is in order and ready to go when you need it. This document should also include information on how to get the best result on set. This information includes locations, crew details and equipment requirements.
First, you need to plan what you want to film. You may have decided where to shoot or even specific locations you want to use. Once you have identified your locations and scenes it's time to begin figuring out what elements you will need for each one. For example, you might decide that you need a car but don't know exactly what model you want. To narrow your options, you can search online for available models.
Once you have found the right vehicle, you can think about adding accessories. Do you need people sitting in the front seats? Maybe you need someone to move around in the back. You might want to change your interior color from black and white. These questions will help to determine the style and feel of your car. It is also worth considering the types of shots that you wish to take. Do you want to film close-ups, or wider angles? Maybe you want the engine or the steering wheels to be shown. This will allow you to determine the type of car you want.
Once you've determined the above, it is time to start creating a calendar. A schedule will tell you when you need to start shooting and when you need to finish. You will need to know when you have to be there, what time you have to leave and when your return home. It will help everyone know exactly what they have to do and when. You can also make sure to book extra staff in advance if you have to hire them. It's not worth paying someone to show up if you haven't told him.
Your schedule will also have to be adjusted to reflect the number of days required to film. Some projects are quick and easy, while others take weeks. When you are creating your schedule, you should always keep in mind whether you need more than one shot per day or not. Shooting multiple takes over the same location will increase costs and take longer to complete. It is better to be cautious and take fewer shots than you risk losing money if you are not sure if multiple takes are necessary.
Another important aspect of production planning is setting budgets. Setting a realistic budget is essential as it will allow you to work within your means. You can always lower the budget if you encounter unexpected problems. You shouldn't underestimate the amount you'll spend. If you underestimate the cost of something, you will have less money left after paying for other items.
Planning production is a tedious process. Once you have a good understanding of how everything works together, planning future projects becomes easy.
Why automate your warehouse?
Modern warehousing has seen automation take center stage. The rise of e-commerce has led to increased demand for faster delivery times and more efficient processes.
Warehouses must adapt quickly to meet changing customer needs. To do so, they must invest heavily in technology. Automation warehouses can bring many benefits. Here are some benefits of investing in automation
-
Increases throughput/productivity
-
Reduces errors
-
Improves accuracy
-
Safety Boosts
-
Eliminates bottlenecks
-
Companies can scale up more easily
-
It makes workers more efficient
-
This gives you visibility into what happens in the warehouse
-
Enhances customer experience
-
Improves employee satisfaction
-
It reduces downtime, and increases uptime
-
High quality products delivered on-time
-
Removing human error
-
It helps ensure compliance with regulations
What are the 7 Rs of logistics.
The 7R's of Logistics is an acronym for the seven basic principles of logistics management. It was developed by the International Association of Business Logisticians (IABL) and published in 2004 as part of its "Seven Principles of Logistics Management" series.
The following letters form the acronym:
-
Responsive - ensure all actions are legal and not harmful to others.
-
Reliable - You can have confidence that you will fulfill your promises.
-
It is reasonable to use resources efficiently and not waste them.
-
Realistic - Take into consideration all aspects of operations including cost-effectiveness, environmental impact, and other factors.
-
Respectful – Treat others fairly and equitably.
-
Be resourceful: Look for opportunities to save money or increase productivity.
-
Recognizable is a company that provides customers with value-added solutions.
What skills should a production planner have?
Production planners must be flexible, organized, and able handle multiple tasks. It is also important to be able communicate with colleagues and clients.
Are there any Manufacturing Processes that we should know before we can learn about Logistics?
No. No. Understanding the manufacturing process will allow you to better understand logistics.
Statistics
- You can multiply the result by 100 to get the total percent of monthly overhead. (investopedia.com)
- According to the United Nations Industrial Development Organization (UNIDO), China is the top manufacturer worldwide by 2019 output, producing 28.7% of the total global manufacturing output, followed by the United States, Japan, Germany, and India.[52][53] (en.wikipedia.org)
- Many factories witnessed a 30% increase in output due to the shift to electric motors. (en.wikipedia.org)
- (2:04) MTO is a production technique wherein products are customized according to customer specifications, and production only starts after an order is received. (oracle.com)
- According to a Statista study, U.S. businesses spent $1.63 trillion on logistics in 2019, moving goods from origin to end user through various supply chain network segments. (netsuite.com)
External Links
How To
How to use lean manufacturing in the production of goods
Lean manufacturing is a management system that aims at increasing efficiency and reducing waste. It was developed by Taiichi Okono in Japan, during the 1970s & 1980s. TPS founder Kanji Takoda awarded him the Toyota Production System Award (TPS). Michael L. Watkins published the book "The Machine That Changed the World", which was the first to be published about lean manufacturing.
Lean manufacturing is often defined as a set of principles used to improve the quality, speed, and cost of products and services. It emphasizes the elimination of defects and waste throughout the value stream. Lean manufacturing is called just-in-time (JIT), zero defect, total productive maintenance (TPM), or 5S. Lean manufacturing emphasizes reducing non-value-added activities like inspection, rework and waiting.
In addition to improving product quality and reducing costs, lean manufacturing helps companies achieve their goals faster and reduces employee turnover. Lean manufacturing has been deemed one of the best ways to manage the entire value-chain, including customers, distributors as well retailers and employees. Lean manufacturing can be found in many industries. Toyota's philosophy, for example, is what has enabled it to be successful in electronics, automobiles, medical devices, healthcare and chemical engineering as well as paper and food.
Five principles are the basis of lean manufacturing:
-
Define Value - Determine the value that your business brings to society. Also, identify what sets you apart from your competitors.
-
Reduce waste - Stop any activity that isn't adding value to the supply chains.
-
Create Flow - Ensure work moves smoothly through the process without interruption.
-
Standardize & Simplify - Make processes as consistent and repeatable as possible.
-
Build Relationships - Establish personal relationships with both internal and external stakeholders.
Although lean manufacturing has always been around, it is gaining popularity in recent years because of a renewed interest for the economy after 2008's global financial crisis. Many businesses are now using lean manufacturing to improve their competitiveness. Some economists even believe that lean manufacturing can be a key factor in economic recovery.
Lean manufacturing has many benefits in the automotive sector. These include higher customer satisfaction, lower inventory levels, lower operating expenses, greater productivity, and improved overall safety.
You can apply Lean Manufacturing to virtually any aspect of your organization. This is because it ensures efficiency and effectiveness in all stages of the value chain.
There are three types principally of lean manufacturing:
-
Just-in-Time Manufacturing: Also known as "pull systems", this type of lean manufacturing uses just-in-time manufacturing (JIT). JIT is a method in which components are assembled right at the moment of use, rather than being manufactured ahead of time. This approach aims to reduce lead times, increase the availability of parts, and reduce inventory.
-
Zero Defects Manufacturing: ZDM ensures that no defective units leave the manufacturing plant. Repairing a part that is damaged during assembly should be done, not scrapping. This applies to finished products, which may need minor repairs before they are shipped.
-
Continuous Improvement: Continuous Improvement aims to improve efficiency by continually identifying problems and making adjustments to eliminate or minimize waste. It involves continuous improvement of processes, people, and tools.