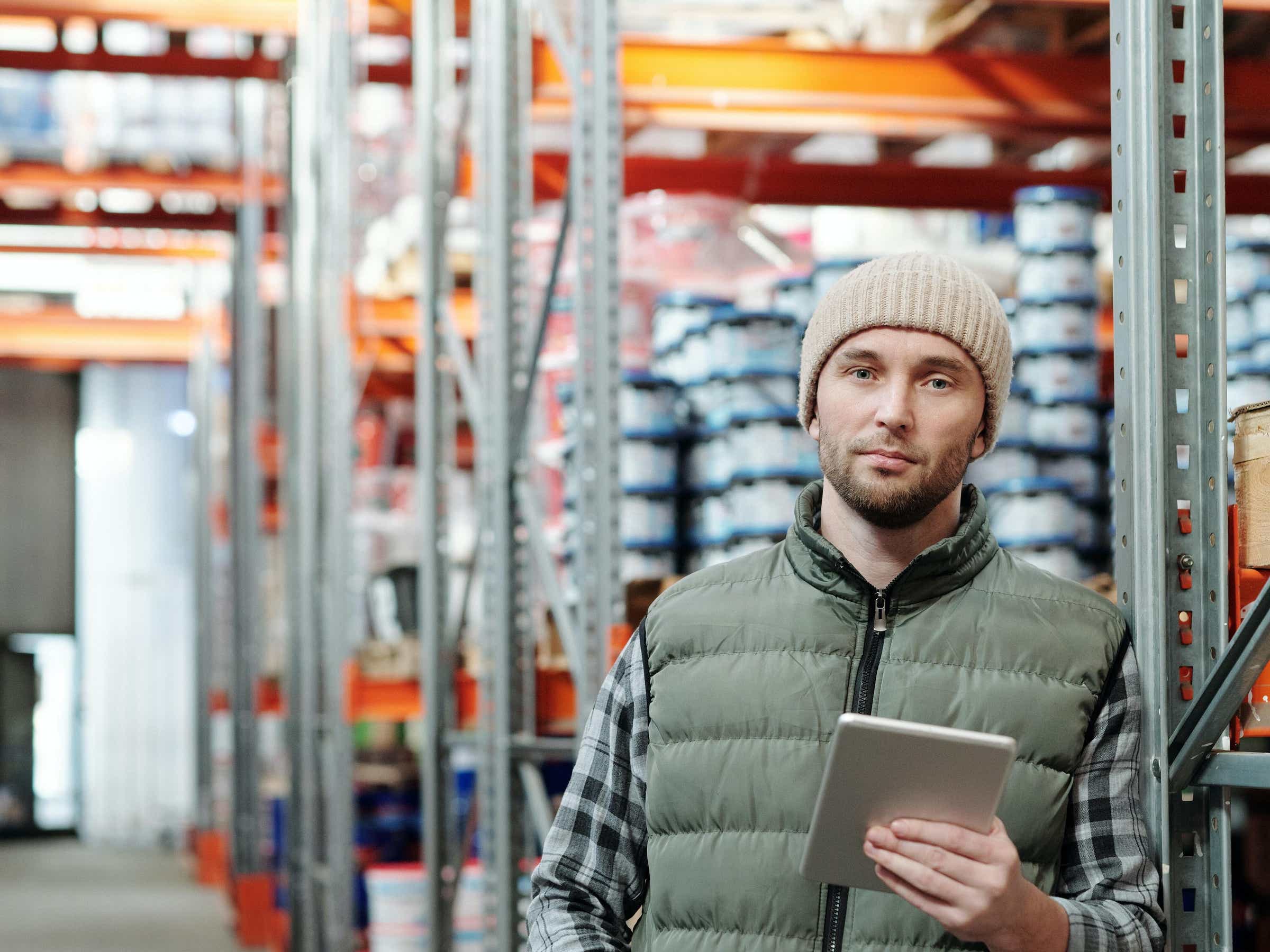
The United States is the third largest country manufacturer in the entire world. Its manufacturing output was almost double that of the Great Recession. Despite having a strong national economy, the United States’ manufacturing industry is taking a very aggressive approach to its current challenges. We need to be more aggressive in addressing the industry's challenges, regardless of whether this is due to a lack or skilled labor.
In 2000, the number of jobs has fallen by 5,000,000
The US has lost five million manufacturing jobs since 2000. Some claim that the rise of trade with China is to blame. However, only about a quarter the decline in manufacturing jobs can be attributed to this. Manufacturing jobs were also lost in countries that couldn't compete with Chinese imports. But there are many factors that contributed to the decline of manufacturing jobs. Among the reasons cited are the following:
During the last two decades, the US manufacturing sector lost nearly a third of its jobs. It was 17,000,000 in 1965. It dropped to just 12,000,000 in 2010. Although the decline of manufacturing jobs is not due solely to trade, it is the result structural problems such as a fall in capital investment and output. These are not sustainable. Although productivity gains had a large role in the decline in manufacturing jobs, they weren't enough. Not productivity gains, but automation is the problem.
The demand for manufactured products is strong
In the United States, the demand for manufactured goods remains strong despite the fact that the share of consumer spending on these items has decreased over the past few decades. In 1945, personal consumption of durable goods accounted to 58%, compared today to 28%. This is because both the manufacturing cost and the sale price have declined, but the content has increased. Computers, televisions, sound equipment, and other electronic devices have seen significant drops in their prices.
The recovery in manufacturing activity has boosted the production of manufactured goods in the US. The Fifth District Manufacturing Activity Survey shows that demand for manufactured goods is strong and production is ramping up, although supply chain bottlenecks are hampering output. The increased production has put stress on supply chains, and respondents have reported supply chain disruptions that affect their ability to maintain necessary inventories. Backlogs have increased as well, and vendors lead times have been longer.
The trade deficit in manufactured products has more than doubled over the past decade
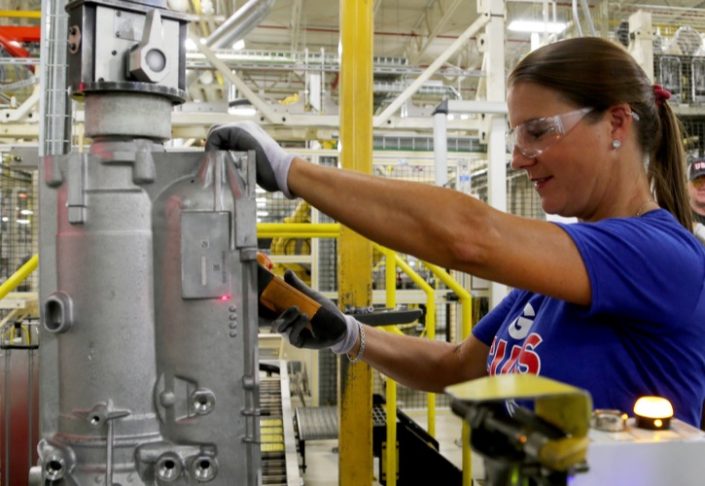
Some economists worry that the U.S.'s trade surplus will lower global growth and create more instability among its trading partners. Some argue that the high imports of manufactured goods from the United States are not necessarily bad for its economy. This is essential to maintaining global economic stability. In fact, the trade deficit could be considered a necessary evil as the U.S. depends heavily on foreign markets to produce its economic output. High levels of foreign consumption may make it harder to achieve full-employment.
Since 2000, the U.S. has almost doubled its trade deficit for manufactured goods. The increase in Chinese imports is partially responsible for the growing US deficit. However, the problem is more serious. This imbalance is concentrated in manufacturing where wages have dropped and employment has declined significantly since 1990. US manufacturing employment has declined dramatically, from 26 percent in 1970 down to 8.5 percent in 2016. Some economists attribute China's increasing competition to the decline, but most blame the decline on automation, productivity increases and the shifting of consumer demand away form goods to services.
The shotgun approach of industry is the best.
The US manufacturing industry is well-respected for its advanced manufacturing efforts and has many other initiatives. However, some countries have chosen to bring the internet of everything into manufacturing. The US, on the other hand, focuses on diverse technologies and combines Internet advertising with traditional mass media. This results in a shotgun approach where companies concentrate on different technologies and seek a wide customer base.
FAQ
How can I learn about manufacturing?
You can learn the most about manufacturing by getting involved in it. However, if that's not possible, you can always read books or watch educational videos.
What are manufacturing & logistics?
Manufacturing is the production of goods using raw materials. Logistics covers all aspects involved in managing supply chains, including procurement and production planning. Manufacturing and logistics can often be grouped together to describe a larger term that covers both the creation of products, and the delivery of them to customers.
What are the logistics products?
Logistics are the activities involved in moving goods from point A to point B.
They cover all aspects of transportation, such as packing, loading, transporting and unloading.
Logisticians ensure the product reaches its destination in the most efficient manner. Logisticians assist companies in managing their supply chains by providing information such as demand forecasts, stock levels and production schedules.
They keep track and monitor the transit of shipments, maintain quality standards, order replenishment and inventories, coordinate with suppliers, vendors, and provide support for sales and marketing.
How can manufacturing avoid production bottlenecks
You can avoid bottlenecks in production by making sure that everything runs smoothly throughout the production cycle, from the moment you receive an order to the moment the product is shipped.
This includes planning to meet capacity requirements and quality control.
Continuous improvement techniques such Six Sigma can help you achieve this.
Six Sigma is a management method that helps to improve quality and reduce waste.
It's all about eliminating variation and creating consistency in work.
What is the role of a manager in manufacturing?
The manufacturing manager should ensure that every manufacturing process is efficient and effective. They should be alert for any potential problems in the company and react accordingly.
They should also be able communicate with other departments, such as sales or marketing.
They should be informed about industry trends and be able make use of this information to improve their productivity and efficiency.
What is the difference between a production planner and a project manager?
The main difference between a production planner and a project manager is that a project manager is usually the person who plans and organizes the entire project, whereas a production planner is mainly involved in the planning stage of the project.
Statistics
- You can multiply the result by 100 to get the total percent of monthly overhead. (investopedia.com)
- According to the United Nations Industrial Development Organization (UNIDO), China is the top manufacturer worldwide by 2019 output, producing 28.7% of the total global manufacturing output, followed by the United States, Japan, Germany, and India.[52][53] (en.wikipedia.org)
- In 2021, an estimated 12.1 million Americans work in the manufacturing sector.6 (investopedia.com)
- According to a Statista study, U.S. businesses spent $1.63 trillion on logistics in 2019, moving goods from origin to end user through various supply chain network segments. (netsuite.com)
- It's estimated that 10.8% of the U.S. GDP in 2020 was contributed to manufacturing. (investopedia.com)
External Links
How To
How to use lean manufacturing in the production of goods
Lean manufacturing is an approach to management that aims for efficiency and waste reduction. It was developed in Japan between 1970 and 1980 by Taiichi Ohno. TPS founder Kanji Tyoda gave him the Toyota Production System, or TPS award. Michael L. Watkins published the first book on lean manufacturing in 1990.
Lean manufacturing, often described as a set and practice of principles, is aimed at improving the quality, speed, cost, and efficiency of products, services, and other activities. It is about eliminating defects and waste from all stages of the value stream. Lean manufacturing is called just-in-time (JIT), zero defect, total productive maintenance (TPM), or 5S. Lean manufacturing emphasizes reducing non-value-added activities like inspection, rework and waiting.
Lean manufacturing improves product quality and costs. It also helps companies reach their goals quicker and decreases employee turnover. Lean manufacturing can be used to manage all aspects of the value chain. Customers, suppliers, distributors, retailers and employees are all included. Lean manufacturing is widely used in many industries. Toyota's philosophy is the foundation of its success in automotives, electronics and appliances, healthcare, chemical engineers, aerospace, paper and food, among other industries.
Lean manufacturing is based on five principles:
-
Define value - Find out what your business contributes to society, and what makes it different from other competitors.
-
Reduce Waste - Eliminate any activity that doesn't add value along the supply chain.
-
Create Flow - Ensure work moves smoothly through the process without interruption.
-
Standardize and Simplify – Make processes as consistent, repeatable, and as simple as possible.
-
Build Relationships- Develop personal relationships with both internal as well as external stakeholders.
Lean manufacturing is not a new concept, but it has been gaining popularity over the last few years due to a renewed interest in the economy following the global financial crisis of 2008. To increase their competitiveness, many businesses have turned to lean manufacturing. According to some economists, lean manufacturing could be a significant factor in the economic recovery.
With many benefits, lean manufacturing is becoming more common in the automotive industry. These include improved customer satisfaction, reduced inventory levels, lower operating costs, increased productivity, and better overall safety.
You can apply Lean Manufacturing to virtually any aspect of your organization. Because it makes sure that all value chains are efficient and effectively managed, Lean Manufacturing is particularly helpful for organizations.
There are three types principally of lean manufacturing:
-
Just-in-Time Manufacturing: Also known as "pull systems", this type of lean manufacturing uses just-in-time manufacturing (JIT). JIT refers to a system in which components are assembled at the point of use instead of being produced ahead of time. This method reduces lead times, increases availability, and decreases inventory.
-
Zero Defects Manufacturing: ZDM ensures that no defective units leave the manufacturing plant. Repairing a part that is damaged during assembly should be done, not scrapping. This is also true for finished products that require minor repairs before shipping.
-
Continuous Improvement (CI: Continuous improvement aims to increase the efficiency of operations by constantly identifying and making improvements to reduce or eliminate waste. Continuous Improvement involves continuous improvement of processes.