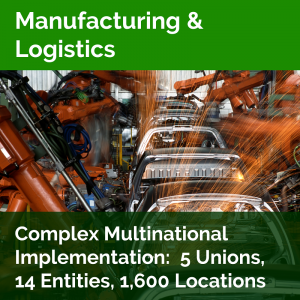
Cellular manufacturing involves dividing a production plant into segments that produce a different component of the finished product. This allows you to reduce waste and shorten lead times. A cellular manufacturing system can be implemented in many different ways. While some methods are simpler, others require complicated computer models. Cellular production is one subset of the lean Manufacturing movement.
Cellular manufacturing, an innovative and highly efficient process, can help lower the cost and time it takes to produce parts. The goal is to minimize waste while moving products along the production line as quickly possible. Cellular manufacturing also addresses issues of group cohesiveness and self-management, as well as issues of employee input and supervision. Cellular manufacturing provides more flexibility and can help companies meet customer needs. It has been proven that cellular manufacturing can also improve productivity.
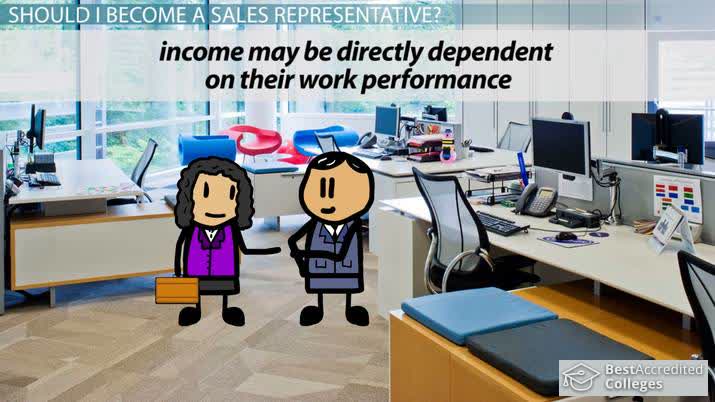
Cellular production can be done in many ways. This includes simple applications such as production flow analysis and more complex computer model. The goal is to produce similar products at the same time, which minimizes wasteful motion and takt time.
The overall takt time can be affected by the layout of the cell. The cells' layout can affect the motion, changing it from non-value to value, which reduces cycle time. Some cells can be configured in a U shape, which allows operators to move faster from one machine to the next. Other cells are arranged in a Z-shape, which can allow workers to work around heavy machines. These designs are especially effective for businesses that make a variety of products.
The first step when creating a new cell is to identify what products will be made there. A process map can help you determine the production rate. In order to create a workcell, engineers must determine the number of workstations in the cell, as well as the process steps in the cell. Next, engineers must decide what tools and equipment will be used in the cells. Modern-day work cells also consider the number of steps and types of holding bins. It also considers how long each machine will take. Which layout is best will depend on the physical structure of your cell.
The success of cell manufacturing depends on the layout of the cells. How much motion is lost, and how much waste created can all be affected by the cell's layout. It can also influence fatigue. Cellular manufacturing not only reduces motion, but can also improve process efficiency as well as quality. Cellular layout can make it easier to spot defects and minimize waste.
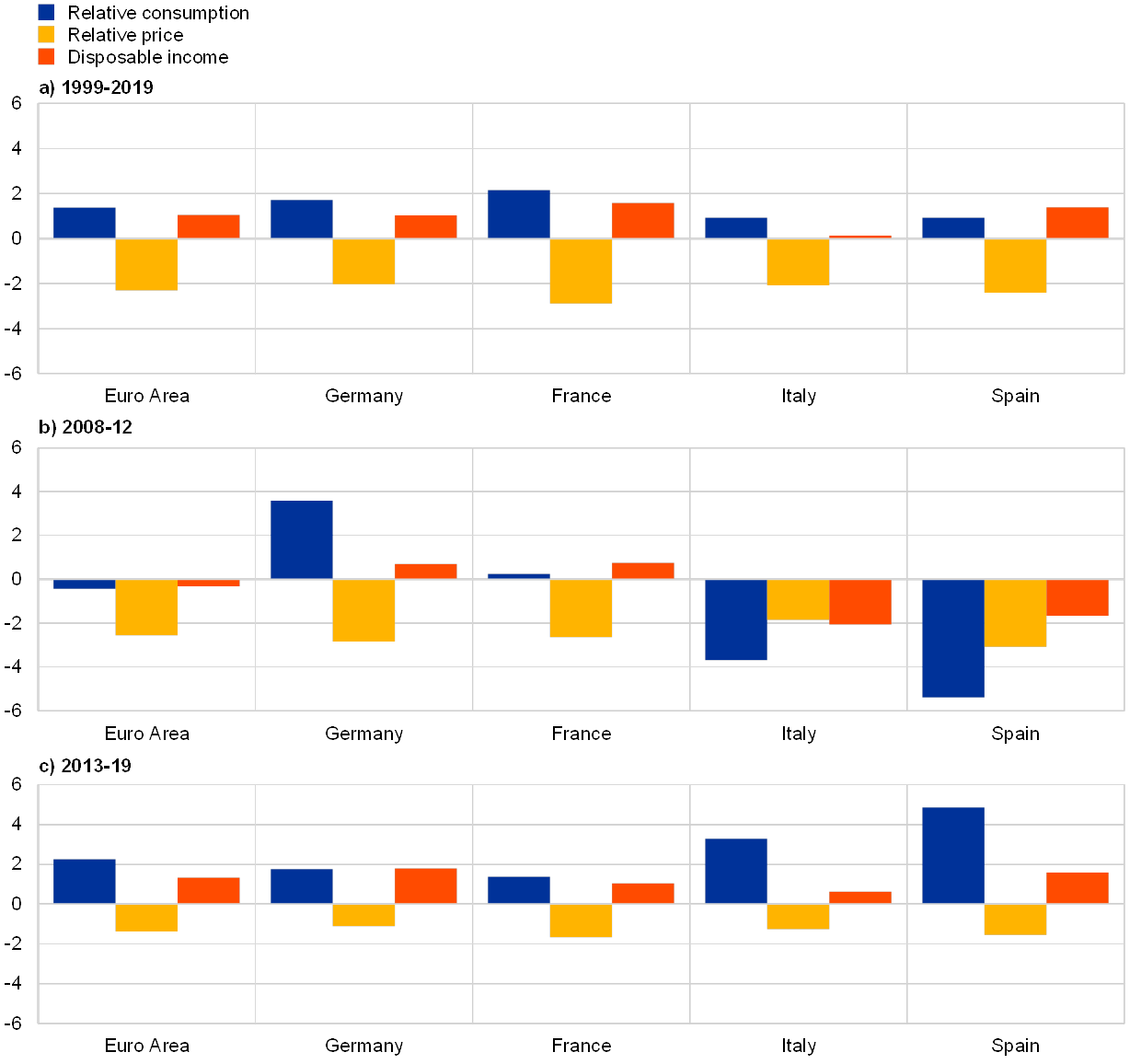
There are three most common layouts. S-shaped cells are also useful for overcoming obstructions. It is possible to customize the layout of cells, as well as reconfigure different cells to meet different requirements in different parts of a factory.
FAQ
How can overproduction in manufacturing be reduced?
Better inventory management is key to reducing excess production. This would reduce the time spent on unproductive activities like purchasing, storing and maintaining excess stock. We could use these resources to do other productive tasks.
A Kanban system is one way to achieve this. A Kanban Board is a visual display that tracks work progress. Kanban systems are where work items travel through a series of states until reaching their final destination. Each state is assigned a different priority.
If work is moving from one stage to the other, then the current task can be completed and moved on to the next. If a task is still in its beginning stages, it will continue to be so until it reaches the end.
This allows work to move forward and ensures that no work is missed. Managers can see how much work has been done and the status of each task at any time with a Kanban Board. This allows them to adjust their workflows based on real-time information.
Lean manufacturing, another method to control inventory levels, is also an option. Lean manufacturing works to eliminate waste throughout every stage of the production chain. Any product that isn't adding value can be considered waste. Here are some examples of common types.
-
Overproduction
-
Inventory
-
Packaging that is not necessary
-
Materials in excess
These ideas can help manufacturers improve efficiency and reduce costs.
Why is logistics important in manufacturing
Logistics is an integral part of every business. They can help you achieve great success by helping you manage product flow from raw material to finished goods.
Logistics also play a major role in reducing costs and increasing efficiency.
Is it necessary to be familiar with Manufacturing Processes before we learn about Logistics.
No. You don't have to know about manufacturing processes before learning about logistics. Knowing about manufacturing processes will help you understand how logistics works.
How does a production planner differ from a project manager?
The difference between a product planner and project manager is that a planer is typically the one who organizes and plans the entire project. A production planner, however, is mostly involved in the planning stages.
Statistics
- Many factories witnessed a 30% increase in output due to the shift to electric motors. (en.wikipedia.org)
- In the United States, for example, manufacturing makes up 15% of the economic output. (twi-global.com)
- Job #1 is delivering the ordered product according to specifications: color, size, brand, and quantity. (netsuite.com)
- You can multiply the result by 100 to get the total percent of monthly overhead. (investopedia.com)
- [54][55] These are the top 50 countries by the total value of manufacturing output in US dollars for its noted year according to World Bank.[56] (en.wikipedia.org)
External Links
How To
Six Sigma and Manufacturing
Six Sigma is "the application statistical process control (SPC), techniques for continuous improvement." It was developed by Motorola's Quality Improvement Department at their plant in Tokyo, Japan, in 1986. Six Sigma's main goal is to improve process quality by standardizing processes and eliminating defects. Many companies have adopted Six Sigma in recent years because they believe that there are no perfect products and services. Six Sigma aims to reduce variation in the production's mean value. You can calculate the percentage of deviation from the norm by taking a sample of your product and comparing it to the average. If there is a significant deviation from the norm, you will know that something needs to change.
Understanding the nature of variability in your business is the first step to Six Sigma. Once you understand this, you can then identify the causes of variation. These variations can also be classified as random or systematic. Random variations are caused when people make mistakes. While systematic variations are caused outside of the process, they can occur. For example, if you're making widgets, and some of them fall off the assembly line, those would be considered random variations. If however, you notice that each time you assemble a widget it falls apart in exactly the same spot, that is a problem.
Once you identify the problem areas, it is time to create solutions. You might need to change the way you work or completely redesign the process. To verify that the changes have worked, you need to test them again. If they didn't work, then you'll need to go back to the drawing board and come up with another plan.