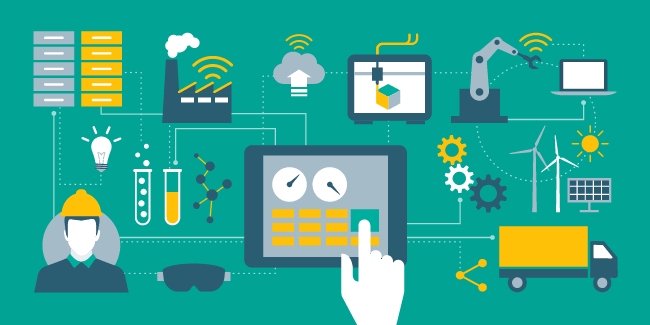
In lean manufacturing, an andon is a visible indicator that draws the attention of the user to specific problems in order to resolve them. It is a tool that empowers plant floor operators and accelerates teamwork in production.
Andon
( ) – a Japanese term, it is derived from the paper-enclosed fixed lanterns that were used during the Edo period between the 17th Century and the 19th Century. It can also be used in Japanese to refer to a method of alerting operators and managers by using light signals or sounds.
Toyota uses Jidoka as the key principle behind their TPS, Toyota Production System. In the US, it is often cited as the root of a commercial concept that allows production line employees to stop the line when a safety or quality problem exists.
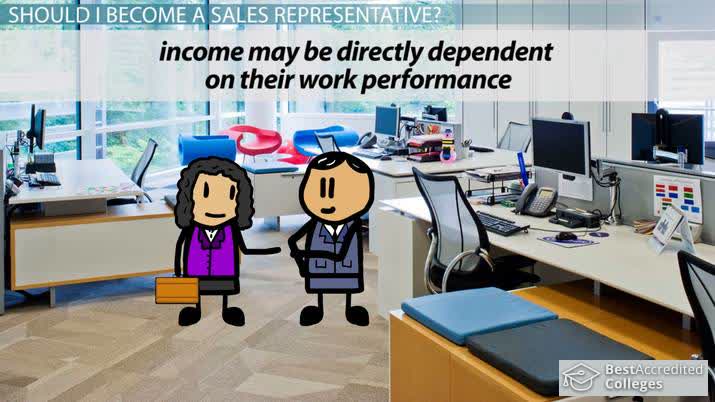
What is andon?
Toyota pioneered the Andon lean manufacturing system. The system is simple and consists of an LED board with three colors: green, yellow, and red. Each color indicates the different status of production. When the light is green, production is proceeding normally. The yellow light indicates that a problem was found and is currently being resolved. If the red light appears, production will stop. Workers may take a short break, prepare spare parts, ask for help or even fill their bins.
The Andon board allows supervisors to understand the situation immediately. The system is designed to provide immediate feedback and ensure all problems are resolved as soon as possible.
There are many types of andons, but most common is a red light with a sound or buzzer to alert production teams. These signal alert and resolve systems help identify problems that might lead to downtime, or repeat issues.
Good andon boards help keep production running when problems arise. It is a simple but effective tool which increases productivity and reduces downtime. It also improves the product quality and safety.
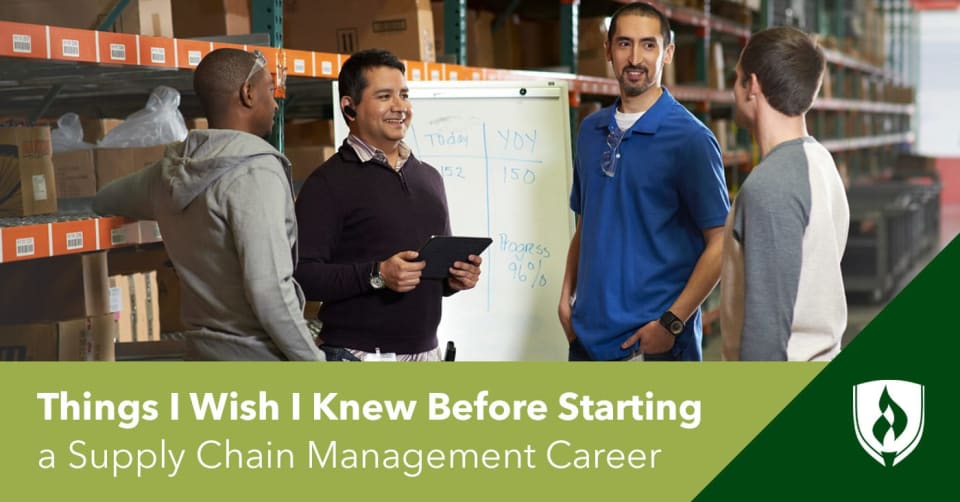
What is andon toyota?
Toyota has a special cord which any employee can pull when they see a possible issue with their car. The cord was used by workers to stop production if they thought the car's integrity had been compromised.
Modern andon uses technology to deliver curated information to make it easier to identify problems as they arise, to send real-time notifications to all stakeholders, and to pinpoint the root causes that need a permanent fix. However, human touch is still essential in interpreting and acting upon this information.
How to make andon work?
In order to begin with, it's important to create a workplace culture that encourages workers and management to not hesitate to identify and solve problems. The more hesitant they are, the more likely they will hide problems and miss an opportunity to resolve them. The quickest way to improve this is to tie line stops to problem resolution, so that workers are more likely to hit the button and pull the cord when they see something amiss.
FAQ
What are the 7 Rs of logistics management?
The acronym 7R's of Logistic is an acronym that stands for seven fundamental principles of logistics management. It was developed by the International Association of Business Logisticians (IABL) and published in 2004 as part of its "Seven Principles of Logistics Management" series.
The following letters make up the acronym:
-
Responsible - ensure that all actions taken are within legal requirements and are not harmful to others.
-
Reliable - You can have confidence that you will fulfill your promises.
-
Use resources effectively and sparingly.
-
Realistic – Consider all aspects, including cost-effectiveness as well as environmental impact.
-
Respectful: Treat others with fairness and equity
-
Reliable - Find ways to save money and increase your productivity.
-
Recognizable: Provide customers with value-added service
What is the role of a manager in manufacturing?
A manufacturing manager must make sure that all manufacturing processes run smoothly and effectively. They must also be alert to any potential problems and take appropriate action.
They should also know how to communicate with other departments such as sales and marketing.
They should be up to date on the latest trends and be able apply this knowledge to increase productivity and efficiency.
What are the essential elements of running a logistics firm?
To be a successful businessman in logistics, you will need many skills and knowledge. For clients and suppliers to be successful, you need to have excellent communication skills. You need to understand how to analyze data and draw conclusions from it. You must be able to work well under pressure and handle stressful situations. You must be creative and innovative to develop new ideas to improve efficiency. You will need strong leadership skills to motivate and direct your team members towards achieving their organizational goals.
You should also be organized and efficient to meet tight deadlines.
What is the job of a production plan?
Production planners ensure that all project aspects are completed on time, within budget and within the scope. They also ensure that the product/service meets the client’s needs.
Statistics
- According to the United Nations Industrial Development Organization (UNIDO), China is the top manufacturer worldwide by 2019 output, producing 28.7% of the total global manufacturing output, followed by the United States, Japan, Germany, and India.[52][53] (en.wikipedia.org)
- In the United States, for example, manufacturing makes up 15% of the economic output. (twi-global.com)
- According to a Statista study, U.S. businesses spent $1.63 trillion on logistics in 2019, moving goods from origin to end user through various supply chain network segments. (netsuite.com)
- It's estimated that 10.8% of the U.S. GDP in 2020 was contributed to manufacturing. (investopedia.com)
- In 2021, an estimated 12.1 million Americans work in the manufacturing sector.6 (investopedia.com)
External Links
How To
How to use the Just-In Time Method in Production
Just-intime (JIT), which is a method to minimize costs and maximize efficiency in business process, is one way. It allows you to get the right amount resources at the right time. This means that only what you use is charged to your account. Frederick Taylor first coined this term while working in the early 1900s as a foreman. After observing how workers were paid overtime for late work, he realized that overtime was a common practice. He decided that workers would be more productive if they had enough time to complete their work before they started to work.
JIT is about planning ahead. You should have all the necessary resources ready to go so that you don’t waste money. Also, you should look at the whole project from start-to-finish and make sure you have the resources necessary to address any issues. You can anticipate problems and have enough equipment and people available to fix them. This will ensure that you don't spend more money on things that aren't necessary.
There are several types of JIT techniques:
-
Demand-driven JIT: You order the parts and materials you need for your project every other day. This will let you track the amount of material left over after you've used it. This will let you know how long it will be to produce more.
-
Inventory-based : You can stock the materials you need in advance. This allows one to predict how much they will sell.
-
Project-driven: This approach involves setting aside sufficient funds to cover your project's costs. You will be able to purchase the right amount of materials if you know what you need.
-
Resource-based JIT: This is the most popular form of JIT. You allocate resources based on the demand. You might assign more people to help with orders if there are many. If there aren't many orders, you will assign fewer people.
-
Cost-based: This is similar to resource-based, except that here you're not just concerned about how many people you have but how much each person costs.
-
Price-based pricing: This is similar in concept to cost-based but instead you look at how much each worker costs, it looks at the overall company's price.
-
Material-based: This approach is similar to cost-based. However, instead of looking at the total cost for the company, you look at how much you spend on average on raw materials.
-
Time-based JIT: This is another variant of resource-based JIT. Instead of focusing on how much each employee costs, you focus on how long it takes to complete the project.
-
Quality-based JIT is another variant of resource-based JIT. Instead of looking at the labor costs and time it takes to make a product, think about its quality.
-
Value-based JIT : This is the newest type of JIT. This is where you don't care about how the products perform or whether they meet customers' expectations. Instead, you are focused on adding value to the marketplace.
-
Stock-based: This stock-based method focuses on the actual quantity of products being made at any given time. It is used when production goals are met while inventory is kept to a minimum.
-
Just-intime (JIT), planning is a combination JIT management and supply chain management. It refers to the process of scheduling the delivery of components as soon as they are ordered. It's important because it reduces lead times and increases throughput.