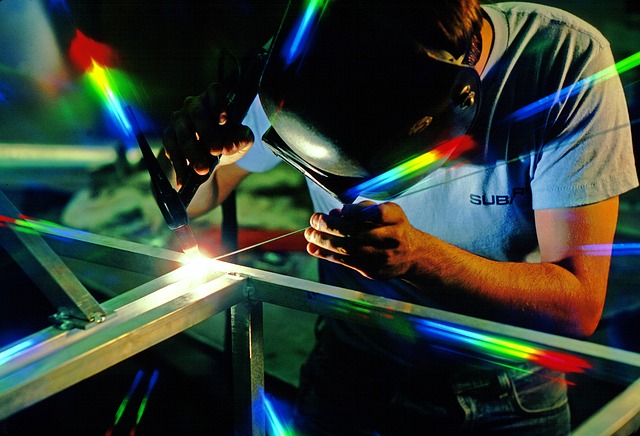
Reshoring, Opportunity zones, Deregulatory policy, and reduced transportation costs are all important aspects of bringing manufacturing back to America. What can the United States be doing to help? Here are some ideas:
Relocation
Many companies have started to reshoring production to the U.S., such as Intel, which has invested $20 billion to construct two new Arizona semiconductor plants. General Motors and other companies are moving their battery production to Michigan. Michigan is poised for growth as a center for lithium-based products. US Steel is instead building a plant in Alabama and Arkansas, rather than investing $3 billion to build its new steelmaking facility abroad. Other companies that are interested in reshoring include Lockheed, General Electric, or Thermo Fisher.
Opportunity zones
Trump is a passionate supporter for opportunity zones. To further support the creation of these zones, it created the White House Opportunity and Revitalization Council. The council has expanded quoting forms and prioritized them. However, local investors in California have one arm tied when it comes to opportunity zones. Listed below are five strategies that local investors can follow to maximize their investment opportunities.
Deregulatory policy
The United States is struggling to attract major companies and is currently losing to countries like China. China subsidizes the construction of new production facilities. The tide is beginning to turn, however. Major companies like Walmart are increasing their investments in the U.S., and a recent study released by the Manufacturing Institute shows that American manufacturing is 9 percent cheaper than manufacturing in nine other high-cost countries.
Transport costs lower
Transport costs can be a major factor in companies moving their manufacturing to America. Companies are able to move manufacturing jobs to the United States because labor costs are less than in other countries. It is not easy to move manufacturing operations to the United States. However, it can take several years to bring new jobs to the United States. While the price of goods would go up, the benefits would outweigh the inconvenience. Covid-19, a pandemic that ravaged the supply chain in the United States, brought these issues to the attention of the American public. Toilet paper and pharmaceuticals were among the affected products.
Qualified labor
Manufacturing is a key political issue, as has the surprise revelation of recent presidential election results. Commentators declared that "U.S. manufacturing is having a moment." Campaign rhetoric is not enough to translate into long-term commitment. Washington D.C.'s debate topics tend to be focused on trade and other issues that do not directly benefit manufacturing. This means that they fail to discuss strategies that would strengthen clusters and communities of manufacturing.
FAQ
What are the responsibilities of a manufacturing manager
A manufacturing manager must make sure that all manufacturing processes run smoothly and effectively. They should also be aware of any problems within the company and act accordingly.
They should also learn how to communicate effectively with other departments, including sales and marketing.
They should also be aware of the latest trends in their industry and be able to use this information to help improve productivity and efficiency.
What are manufacturing & logistics?
Manufacturing is the act of producing goods from raw materials using machines and processes. Logistics manages all aspects of the supply chain, including procurement, production planning and distribution, inventory control, transportation, customer service, and transport. Logistics and manufacturing are often referred to as one thing. It encompasses both the creation of products and their delivery to customers.
How can manufacturing efficiency be improved?
The first step is to determine the key factors that impact production time. Next, we must find ways to improve those factors. If you don’t know how to start, look at which factors have the greatest impact upon production time. Once you have identified the factors, then try to find solutions.
What are the 7 R's of logistics?
The acronym "7R's" of Logistics stands for seven principles that underpin logistics management. It was developed and published by the International Association of Business Logisticians in 2004 as part of the "Seven Principles of Logistics Management".
The acronym consists of the following letters:
-
Responsible - to ensure that all actions are within the legal requirements and are not detrimental to others.
-
Reliable – have faith in your ability and capability to keep promises.
-
It is reasonable to use resources efficiently and not waste them.
-
Realistic – Consider all aspects, including cost-effectiveness as well as environmental impact.
-
Respectful - treat people fairly and equitably.
-
You are resourceful and look for ways to save money while increasing productivity.
-
Recognizable provides value-added products and services to customers
How does manufacturing avoid bottlenecks in production?
The key to avoiding bottlenecks in production is to keep all processes running smoothly throughout the entire production cycle, from the time you receive an order until the time when the product ships.
This includes planning to meet capacity requirements and quality control.
This can be done by using continuous improvement techniques, such as Six Sigma.
Six Sigma can be used to improve the quality and decrease waste in all areas of your company.
It emphasizes consistency and eliminating variance in your work.
Statistics
- (2:04) MTO is a production technique wherein products are customized according to customer specifications, and production only starts after an order is received. (oracle.com)
- You can multiply the result by 100 to get the total percent of monthly overhead. (investopedia.com)
- According to the United Nations Industrial Development Organization (UNIDO), China is the top manufacturer worldwide by 2019 output, producing 28.7% of the total global manufacturing output, followed by the United States, Japan, Germany, and India.[52][53] (en.wikipedia.org)
- In 2021, an estimated 12.1 million Americans work in the manufacturing sector.6 (investopedia.com)
- In the United States, for example, manufacturing makes up 15% of the economic output. (twi-global.com)
External Links
How To
How to Use the Just-In-Time Method in Production
Just-intime (JIT), a method used to lower costs and improve efficiency in business processes, is called just-in-time. It is a process where you get the right amount of resources at the right moment when they are needed. This means that your only pay for the resources you actually use. The term was first coined by Frederick Taylor, who developed his theory while working as a foreman in the early 1900s. Taylor observed that overtime was paid to workers if they were late in working. He concluded that if workers were given enough time before they start work, productivity would increase.
JIT teaches you to plan ahead and prepare everything so you don’t waste time. Look at your entire project, from start to end. Make sure you have enough resources in place to deal with any unexpected problems. You can anticipate problems and have enough equipment and people available to fix them. This way, you won't end up paying extra money for things that weren't really necessary.
There are many types of JIT methods.
-
Demand-driven JIT: This is a JIT that allows you to regularly order the parts/materials necessary for your project. This will enable you to keep track of how much material is left after you use it. This will allow to you estimate the time it will take for more to be produced.
-
Inventory-based : You can stock the materials you need in advance. This allows one to predict how much they will sell.
-
Project-driven : This is a method where you make sure that enough money is set aside to pay the project's cost. You will be able to purchase the right amount of materials if you know what you need.
-
Resource-based JIT: This type of JIT is most commonly used. Here, you allocate certain resources based on demand. You will, for example, assign more staff to deal with large orders. If there aren't many orders, you will assign fewer people.
-
Cost-based : This is similar in concept to resource-based. But here, you aren't concerned about how many people your company has but how much each individual costs.
-
Price-based: This is a variant of cost-based. However, instead of focusing on the individual workers' costs, this looks at the total price of the company.
-
Material-based: This is quite similar to cost-based, but instead of looking at the total cost of the company, you're concerned with how much raw materials you spend on average.
-
Time-based JIT: A variation on resource-based JIT. Instead of focusing on how much each employee costs, you focus on how long it takes to complete the project.
-
Quality-based JIT: This is another variation of resource based JIT. Instead of thinking about the cost of each employee or the time it takes to produce something, you focus on how good your product quality.
-
Value-based JIT: One of the most recent forms of JIT. In this scenario, you're not concerned about how products perform or whether customers expect them to meet their expectations. Instead, you are focused on adding value to the marketplace.
-
Stock-based. This method is inventory-based and focuses only on the actual production at any given point. This is used to increase production and minimize inventory.
-
Just-in time (JIT), planning: This is a combination JIT/supply chain management. It is the process of scheduling components' delivery as soon as they have been ordered. It reduces lead times and improves throughput.