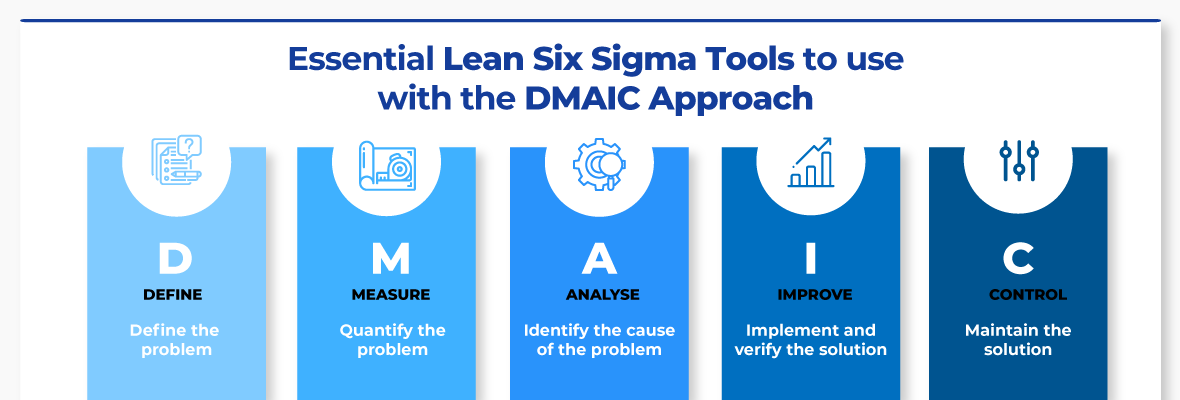
About Industrial Engineering Jobs Houston
There are many industrial engineering positions in houston. These positions are highly sought after because they offer a competitive wage, a challenging work environment, and room for career growth.
Find entry-level industrial engineering jobs in Houston
Anyone seeking to enter the industry will find this position a great way to begin. It's a good way to learn more about a company, its culture and its employees.
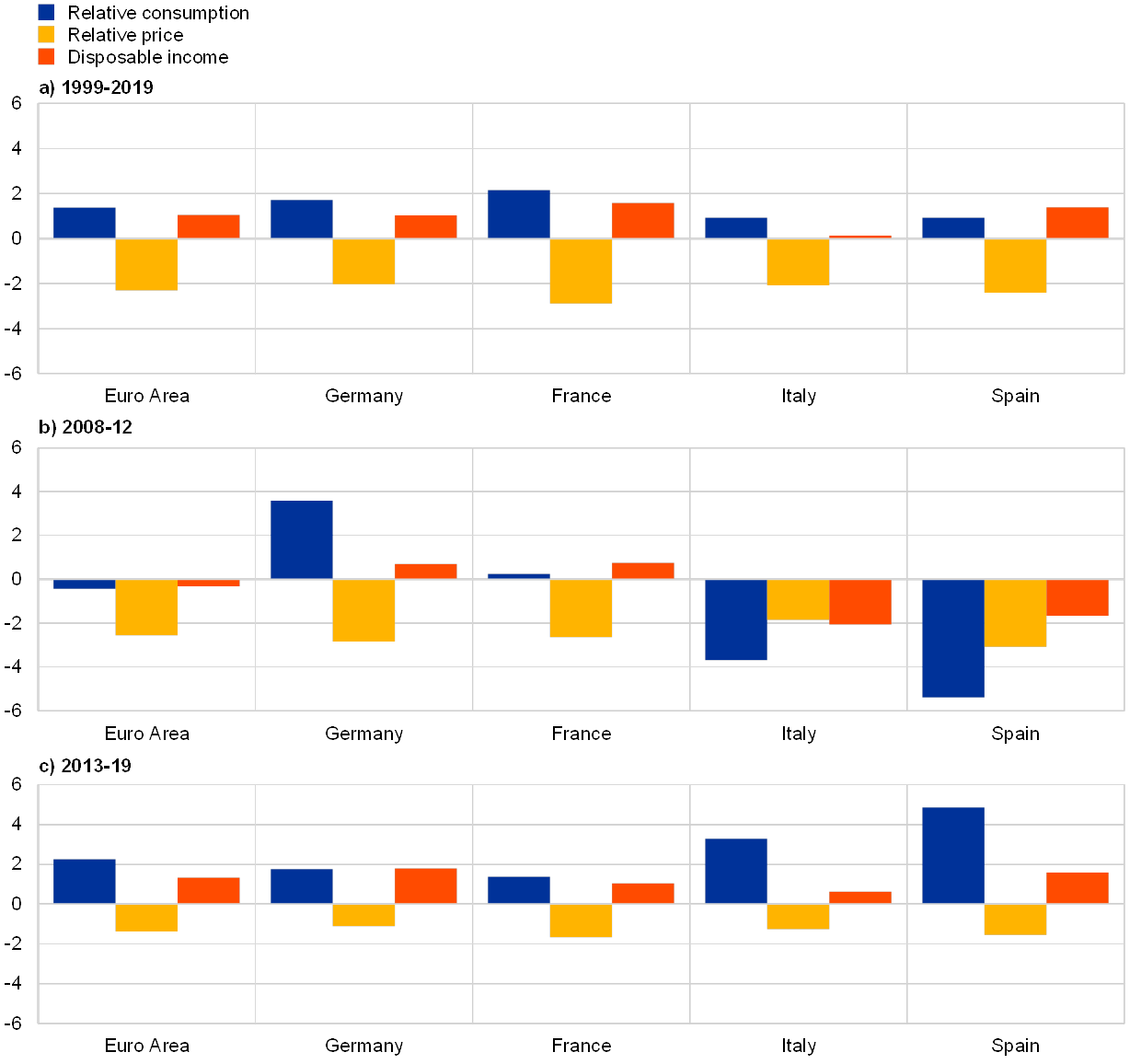
Besides being an important part of the business, this entry-level position offers opportunities to grow your skills and knowledge through the aforementioned mentorship program. The position offers a variety of benefits, including paid time-off, health insurance and flexible spending accounts. You can also take advantage of tuition assistance and 401K with a company match.
Best of all, this is an entry-level position that pays just enough to get you out of your current cubicle and onto the job floor. You will have the opportunity for lasting relationships to be formed with C&S's employees and other C&S peers.
You'll also be rewarded with an amazing team for all your hard work. If you feel this would be a good fit for you, please apply!
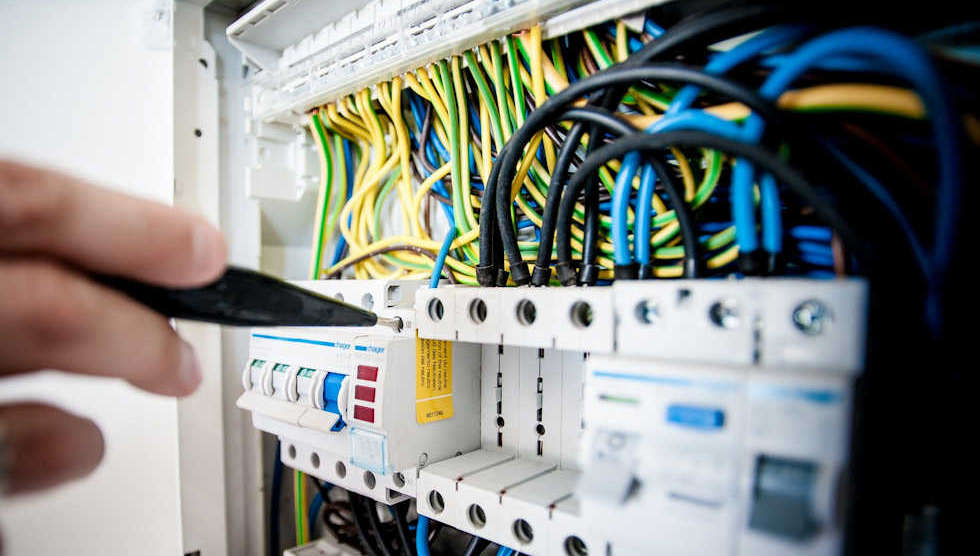
ARCXIS has been the leader in inspection, design and engineer services for residential building construction across more than 50 states.
FAQ
What is the job of a logistics manger?
Logistics managers ensure that goods arrive on time and are unharmed. This is accomplished by using the experience and knowledge gained from working with company products. He/she must also ensure sufficient stock to meet the demand.
How important is automation in manufacturing?
Not only are service providers and manufacturers important, but so is automation. It allows them to offer services faster and more efficiently. It reduces human errors and improves productivity, which in turn helps them lower their costs.
What are the products of logistics?
Logistics refers to all activities that involve moving goods from A to B.
They cover all aspects of transportation, such as packing, loading, transporting and unloading.
Logisticians ensure that products reach the right destination at the right moment and under safe conditions. Logisticians help companies improve their supply chain efficiency by providing information about demand forecasts and stock levels, production schedules, as well as availability of raw materials.
They can also track shipments in transit and monitor quality standards.
What are the 7 Rs of logistics?
The acronym 7R's for Logistics stands to represent the seven basic principles in logistics management. It was created by the International Association of Business Logisticians and published in 2004 under its "Seven Principles of Logistics Management".
The acronym consists of the following letters:
-
Responsible - ensure that all actions taken are within legal requirements and are not harmful to others.
-
Reliable - You can have confidence that you will fulfill your promises.
-
Reasonable - make sure you use your resources well and don't waste them.
-
Realistic – Consider all aspects, including cost-effectiveness as well as environmental impact.
-
Respectful - show respect and treat others fairly and fairly
-
Reliable - Find ways to save money and increase your productivity.
-
Recognizable is a company that provides customers with value-added solutions.
Why is logistics so important in manufacturing?
Logistics are an essential part of any business. They can help you achieve great success by helping you manage product flow from raw material to finished goods.
Logistics plays a significant role in reducing cost and increasing efficiency.
What is production planning?
Production Planning is the creation of a plan to cover all aspects, such as scheduling, budgeting. Location, crew, equipment, props and other details. This document will ensure everything is in order and ready to go when you need it. It should also contain information on achieving the best results on set. This includes location information, crew details, equipment specifications, and casting lists.
The first step is to outline what you want to film. You may already know where you want the film to be shot, or perhaps you have specific locations and sets you wish to use. Once you have determined your scenes and locations, it is time to start figuring out the elements that you will need for each scene. You might decide you need a car, but not sure what make or model. To narrow your options, you can search online for available models.
After you have chosen the right car, you will be able to begin thinking about accessories. You might need to have people in the front seats. Perhaps you have someone who needs to be able to walk around the back of your car. Maybe you want to change the interior color from black to white? These questions can help you decide the right look for your car. You can also think about the type of shots you want to get. Will you be filming close-ups or wide angles? Maybe the engine or steering wheel is what you are looking to film. All of these things will help you identify the exact style of car you want to film.
Once you have determined all of the above, you can move on to creating a schedule. You will know when you should start and when you should finish shooting. Each day will include the time when you need to arrive at the location, when you need to leave and when you need to return home. Everyone will know what they need and when. It is possible to make arrangements in advance for additional staff if you are looking to hire. It is not worth hiring someone who won’t show up because you didn’t tell him.
Your schedule will also have to be adjusted to reflect the number of days required to film. Some projects only take one or two days, while others may last weeks. You should consider whether you will need more than one shot per week when creating your schedule. Multiplying takes in the same area will result both in increased costs and a longer time. It is better to be cautious and take fewer shots than you risk losing money if you are not sure if multiple takes are necessary.
Budget setting is another important aspect in production planning. You will be able to manage your resources if you have a realistic budget. Remember that you can always reduce the budget later on if you run into unforeseen problems. But, don't underestimate how much money you'll spend. You'll end up with less money after paying for other things if the cost is underestimated.
Production planning can be a complex process. However, once you know how everything works together it will become easier to plan future projects.
Statistics
- In 2021, an estimated 12.1 million Americans work in the manufacturing sector.6 (investopedia.com)
- It's estimated that 10.8% of the U.S. GDP in 2020 was contributed to manufacturing. (investopedia.com)
- [54][55] These are the top 50 countries by the total value of manufacturing output in US dollars for its noted year according to World Bank.[56] (en.wikipedia.org)
- According to a Statista study, U.S. businesses spent $1.63 trillion on logistics in 2019, moving goods from origin to end user through various supply chain network segments. (netsuite.com)
- (2:04) MTO is a production technique wherein products are customized according to customer specifications, and production only starts after an order is received. (oracle.com)
External Links
How To
How to Use Six Sigma in Manufacturing
Six Sigma is defined as "the application of statistical process control (SPC) techniques to achieve continuous improvement." It was developed by Motorola's Quality Improvement Department at their plant in Tokyo, Japan, in 1986. Six Sigma's basic concept is to improve quality and eliminate defects through standardization. In recent years, many companies have adopted this method because they believe there is no such thing as perfect products or services. Six Sigma aims to reduce variation in the production's mean value. It is possible to measure the performance of your product against an average and find the percentage of time that it differs from the norm. If the deviation is excessive, it's likely that something needs to be fixed.
Understanding the dynamics of variability within your business is the first step in Six Sigma. Once you understand this, you can then identify the causes of variation. Also, you will need to identify the sources of variation. Random variations occur when people do mistakes. Symmetrical variations are caused due to factors beyond the process. Random variations would include, for example, the failure of some widgets to fall from the assembly line. You might notice that your widgets always fall apart at the same place every time you put them together.
After identifying the problem areas, you will need to devise solutions. That solution might involve changing the way you do things or redesigning the process altogether. You should then test the changes again after they have been implemented. If they don’t work, you’ll need to go back and rework the plan.