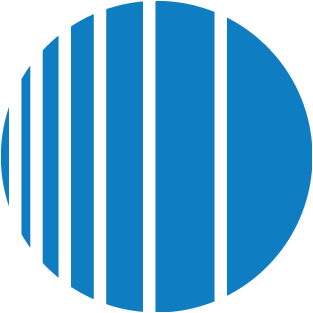
Heijunka, originally created by Toyota in Japan, is a lean production process that improves efficiency in multistep production processes. This method reduces waste and ensures that production schedules are consistent with customer demands. It reduces waste by eliminating abrupt fluctuations in production. Heijunka helps manufacturers meet customer demand and improve profits.
Heijunka is the process of coordinating small production batches across manufacturing line lines. It's used to improve efficiency when multi-step production is being done, particularly when just-in time principles are used. It is also part the Toyota Production System. It helps reduce waste by leveling production, mixing products and minimizing batch sizes.
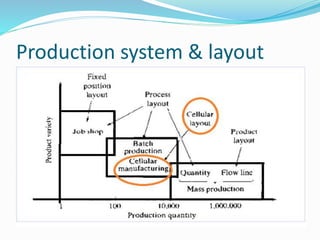
Heijunka can be implemented through two methods. One option is the use a "heijunka" box. This is a grid of small boxes which are mounted or fixed to a wall. It allows production personnel visualize the production process and schedules them. Another way to implement heijunka is with magnetic cards.
Toyota dealers use Heijunka to reduce changeover times. It is also the core method of Toyota's Lean framework. Heijunka can be used to improve production and inventory management. Heijunka also facilitates better use of labor and equipment. It promotes a lean production process that reduces waste and makes better products for customers.
You must be able to understand the takt time (also known as the customer purchasing rate) before you can use heijunka. This refers to the time taken to complete a product in order for it to meet customer demand. Heijunka uses the takt time to determine the pace of production. You can use the takt to determine the product quantity and the pace at which customers buy the company's products. The takttime can also be used in back-office settings to determine the customer's purchase pace.
The heijunka box allows production personnel to visually plan and schedule the production process. You can also use the heijunka to help you visualize the production flow. The heijunka box is made up of rows and columns which represent each product type or component. The columns of boxes represent the time period and the rows of boxes each product type.
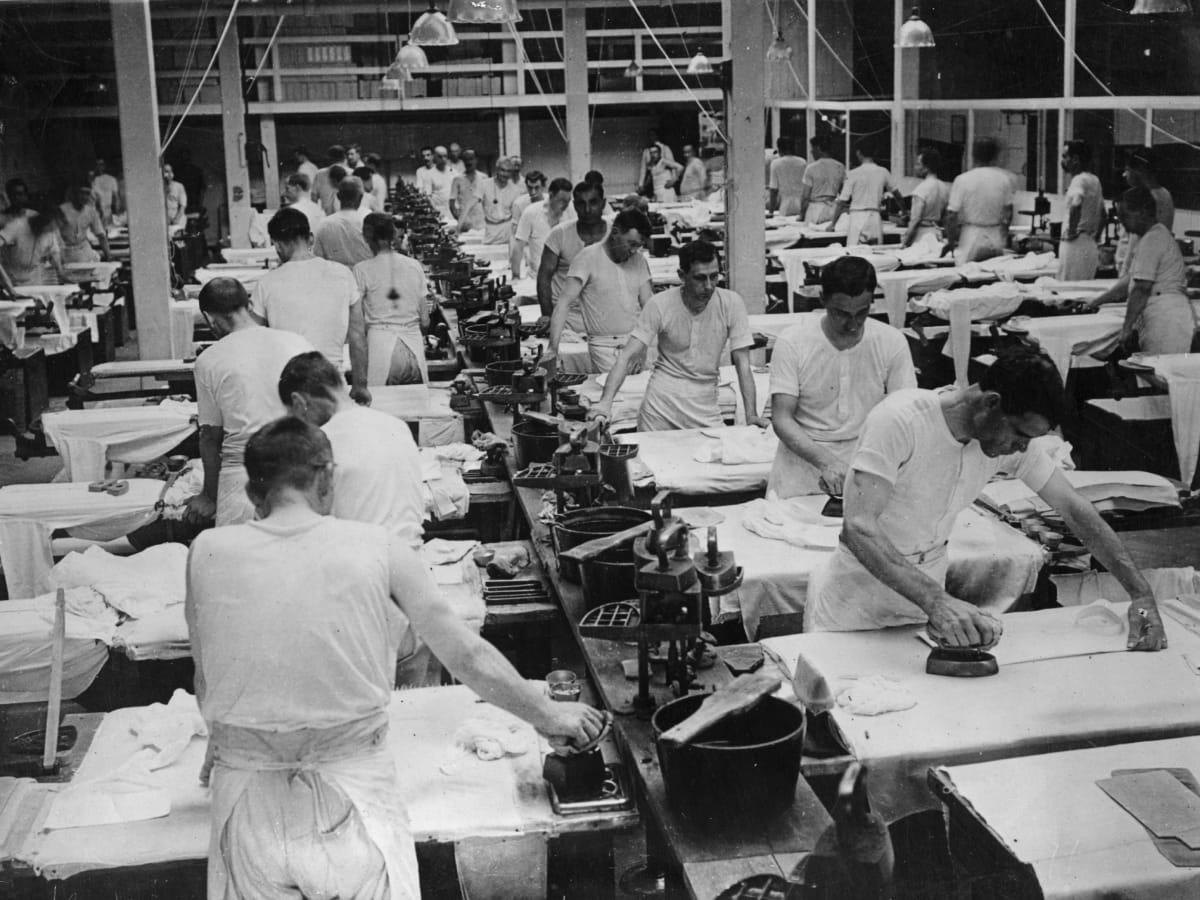
Heijunka Box (or Heijunka Box) is one of most commonly used visual management tools in manufacturing. This tool displays the relationships between component and product production. This tool provides visual representations of the production workload for each week. It is used together with the kanban deck, which is a set of colored cards that represents the product required for each production step. Kanban cards are normally taken from the heijunka container at a certain time and delivered to appropriate production areas.
FAQ
What does "warehouse" mean?
A warehouse or storage facility is where goods are stored before they are sold. You can have it indoors or outdoors. In some cases, it may be a combination of both.
What is the difference between Production Planning and Scheduling?
Production Planning (PP) refers to the process of determining how much production is needed at any given moment. Forecasting demand is one way to do this.
Scheduling refers the process by which tasks are assigned dates so that they can all be completed within the given timeframe.
How can manufacturing avoid production bottlenecks
Avoiding production bottlenecks is as simple as keeping all processes running smoothly, from the time an order is received until the product ships.
This includes planning for capacity requirements as well as quality control measures.
Continuous improvement techniques like Six Sigma are the best way to achieve this.
Six Sigma can be used to improve the quality and decrease waste in all areas of your company.
It focuses on eliminating variation and creating consistency in your work.
What are the goods of logistics?
Logistics refers to all activities that involve moving goods from A to B.
They encompass all aspects transport, including packaging and loading, transporting, storage, unloading.
Logisticians ensure that the product is delivered to the correct place, at the right time, and under safe conditions. They help companies manage their supply chain efficiency by providing information on demand forecasts, stock levels, production schedules, and availability of raw materials.
They coordinate with vendors and suppliers, keep track of shipments, monitor quality standards and perform inventory and order replenishment.
What are manufacturing and logistic?
Manufacturing is the production of goods using raw materials. Logistics encompasses the management of all aspects associated with supply chain activities such as procurement, production planning, distribution and inventory control. It also includes customer service. As a broad term, manufacturing and logistics often refer to both the creation and delivery of products.
How can I find out more about manufacturing?
Practical experience is the best way of learning about manufacturing. But if that is not possible you can always read books and watch educational videos.
Statistics
- In the United States, for example, manufacturing makes up 15% of the economic output. (twi-global.com)
- You can multiply the result by 100 to get the total percent of monthly overhead. (investopedia.com)
- According to the United Nations Industrial Development Organization (UNIDO), China is the top manufacturer worldwide by 2019 output, producing 28.7% of the total global manufacturing output, followed by the United States, Japan, Germany, and India.[52][53] (en.wikipedia.org)
- [54][55] These are the top 50 countries by the total value of manufacturing output in US dollars for its noted year according to World Bank.[56] (en.wikipedia.org)
- Job #1 is delivering the ordered product according to specifications: color, size, brand, and quantity. (netsuite.com)
External Links
How To
How to Use 5S for Increasing Productivity in Manufacturing
5S stands for "Sort", 'Set In Order", 'Standardize', & Separate>. Toyota Motor Corporation developed the 5S method in 1954. It assists companies in improving their work environments and achieving higher efficiency.
This method aims to standardize production processes so that they are repeatable, measurable and predictable. This means that tasks such as cleaning, sorting, storing, packing, and labeling are performed daily. Because workers know what they can expect, this helps them perform their jobs more efficiently.
There are five steps that you need to follow in order to implement 5S. Each step involves a different action which leads to increased efficiency. If you sort items, it makes them easier to find later. When you arrange items, you place them together. After you have divided your inventory into groups you can store them in easy-to-reach containers. Finally, label all containers correctly.
Employees will need to be more critical about their work. Employees need to understand the reasons they do certain jobs and determine if there is a better way. To be successful in the 5S system, employees will need to acquire new skills and techniques.
In addition to improving efficiency, the 5S system also increases morale and teamwork among employees. They are more motivated to achieve higher efficiency levels as they start to see improvement.