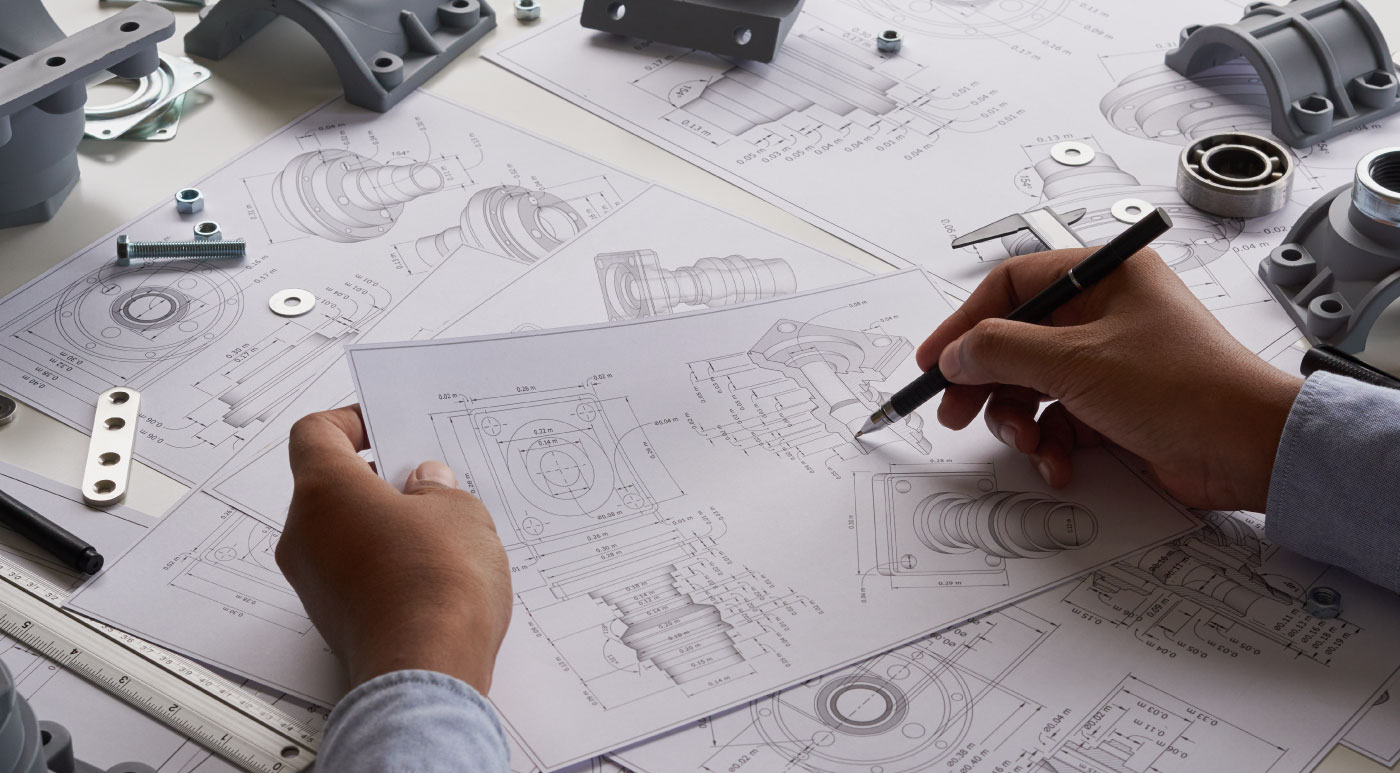
While experience is important for food manufacturers, so is OSHA compliance. When choosing a company who will automate your production, there are three important things to remember:
Food manufacturers must have experience
A high level of industry experience is often required for a position in a food manufacturer. There are opportunities for people with less or no experience. Many food companies prefer to hire from their own ranks. While high school education is beneficial, it is not always essential. Entry-level employees start out as assistants to more experienced workers. They then learn on their own. Some entry-level jobs are straightforward and can be completed in a few days. You may find entry-level work in common areas such as operating bread slicers or washing vegetables before they are processed, transporting carcasses and packaging bottles as they leave the production line. In every aspect of food manufacturing, experience is essential.
Respect for OSHA regulations
OSHA regulations governing food manufacturers require that an inspection be conducted. This inspection is either triggered through an incident, complaint or "programmed inspection". For example, an OSHA enforcement visit to a yogurt manufacturing plant was initiated by a complaint. It was preceded also by a planned inspection. Multiple violations of the process safety standard are common in many cases. These include standards on hazard communications, guarding machines, stairs and platforms and emergency egress. Forklift operation and hearing protection are also included.
Develop a plan that will prevent food safety hazards
Most companies are subject to federal regulations. However, there are some exceptions. While it is impossible to anticipate every food safety issue, there are ways to prevent and manage potential hazards in the food manufacturing process. Food safety is not only a concern for consumers' health but also can have negative consequences for businesses. Recalls can impact both the direct operations and those in the supply chains. There are many reasons for recalls, such as adulteration and misbranding. A food manufacturer can face costly recalls if they have to recall food due to health concerns.
Automation cost
The cost of automation for food manufacturers is increasing as utility costs increase, and some regions are forced to import ingredients to compete with local producers. The suppliers also have a decreasing profit margin as they pass on the cost to consumers. Automation can reduce production costs and improve efficiency. In this article we will talk about how automation can increase food manufacturer's efficiency. You can also reach out to us for our industry knowledge.
Competing with established food companies presents challenges
Three broad strategies are used by dominant food companies to maintain market dominance, avoid unwanted competition, and increase their profit margins. The strategies are about acquiring and developing valuable assets, as well as enforcing marketing and production efficiencies and controlling the supply chains. In essence, these strategies create barriers to entry. Here are some of the most important challenges faced by emerging food and beverage companies. Let's look into each strategy more in detail.
FAQ
Is automation important for manufacturing?
Automation is essential for both manufacturers and service providers. Automation allows them to deliver services quicker and more efficiently. In addition, it helps them reduce costs by reducing human errors and improving productivity.
Are there ways to automate parts of manufacturing?
Yes! Yes. Automation has been around since ancient time. The Egyptians invent the wheel thousands of year ago. To help us build assembly lines, we now have robots.
There are many applications for robotics in manufacturing today. These include:
-
Line robots
-
Robot welding
-
Robot painting
-
Robotics inspection
-
Robots that make products
Automation can be applied to manufacturing in many other ways. 3D printing, for example, allows us to create custom products without waiting for them to be made.
What are the products of logistics?
Logistics are the activities involved in moving goods from point A to point B.
These include all aspects related to transport such as packaging, loading and transporting, storing, transporting, unloading and warehousing inventory management, customer service. Distribution, returns, recycling are some of the options.
Logisticians ensure that products reach the right destination at the right moment and under safe conditions. They provide information on demand forecasts as well stock levels, production schedules and availability of raw material.
They coordinate with vendors and suppliers, keep track of shipments, monitor quality standards and perform inventory and order replenishment.
How can manufacturing excess production be decreased?
The key to reducing overproduction lies in developing better ways to manage inventory. This would reduce the amount of time spent on unnecessary activities such as purchasing, storing, and maintaining excess stock. We could use these resources to do other productive tasks.
A Kanban system is one way to achieve this. A Kanbanboard is a visual tool that allows you to keep track of the work being done. Kanban systems are where work items travel through a series of states until reaching their final destination. Each state has a different priority level.
For instance, when work moves from one stage to another, the current task is complete enough to be moved to the next stage. It is possible to keep a task in the beginning stages until it gets to the end.
This keeps work moving and ensures no work is lost. Managers can see how much work has been done and the status of each task at any time with a Kanban Board. This information allows them to adjust their workflow based on real-time data.
Lean manufacturing can also be used to reduce inventory levels. Lean manufacturing seeks to eliminate waste from every step of the production cycle. Anything that doesn't add value to the product is considered waste. There are several types of waste that you might encounter:
-
Overproduction
-
Inventory
-
Unnecessary packaging
-
Material surplus
Manufacturers can reduce their costs and improve their efficiency by using these ideas.
Statistics
- You can multiply the result by 100 to get the total percent of monthly overhead. (investopedia.com)
- In the United States, for example, manufacturing makes up 15% of the economic output. (twi-global.com)
- According to a Statista study, U.S. businesses spent $1.63 trillion on logistics in 2019, moving goods from origin to end user through various supply chain network segments. (netsuite.com)
- Many factories witnessed a 30% increase in output due to the shift to electric motors. (en.wikipedia.org)
- (2:04) MTO is a production technique wherein products are customized according to customer specifications, and production only starts after an order is received. (oracle.com)
External Links
How To
Six Sigma: How to Use it in Manufacturing
Six Sigma can be described as "the use of statistical process control (SPC), techniques to achieve continuous improvement." Motorola's Quality Improvement Department, Tokyo, Japan, developed it in 1986. Six Sigma's basic concept is to improve quality and eliminate defects through standardization. Many companies have adopted this method in recent years. They believe there is no such thing a perfect product or service. Six Sigma aims to reduce variation in the production's mean value. If you take a sample and compare it with the average, you will be able to determine how much of the production process is different from the norm. If the deviation is excessive, it's likely that something needs to be fixed.
The first step toward implementing Six Sigma is understanding how variability works in your business. Once you have a good understanding of the basics, you can identify potential sources of variation. You'll also want to determine whether these variations are random or systematic. Random variations occur when people do mistakes. Symmetrical variations are caused due to factors beyond the process. If you make widgets and some of them end up on the assembly line, then those are considered random variations. You might notice that your widgets always fall apart at the same place every time you put them together.
Once you've identified the problem areas you need to find solutions. It might mean changing the way you do business or redesigning it entirely. Once you have implemented the changes, it is important to test them again to ensure they work. If they didn't work, then you'll need to go back to the drawing board and come up with another plan.