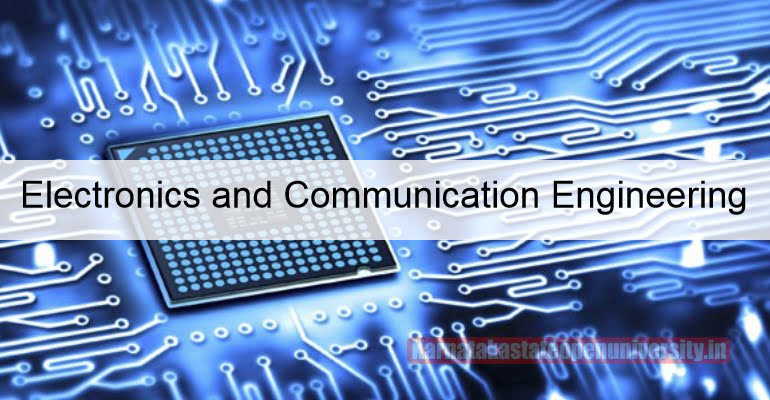
Advanced manufacturing refers to the application of advanced technology to enhance products and processes. The technology used in this process can be classified either as "innovative," "advanced" or "cutting edge". As advanced manufacturing becomes more popular, companies are incorporating new and innovative technologies to their manufacturing processes. These are just a few examples of advanced manufacturing. Here are some of the most commonly used technologies in advanced production.
Continuous manufacturing
Continuous manufacturing is first mentioned in the 1700s as a method of making pig iron in blast ovens. Since then, continuous manufacturing has been used in many industries including automotive, food and oil refining and chemical, as well as pulp and paper. Continuous manufacturing has captured the attention of CMOs from top pharma and other big players in the biopharmaceutical market.
Recent comments from the FDA and partners highlighted the advantages of continuous manufacturing in the production of therapeutic proteins. The legislation will create national centers that can help advance the field and create standards for companies. This legislation will help improve the manufacturing and use of medical devices. The goal is to encourage continuous manufacturing by companies to create and improve products. But, it is crucial to ensure that continuous production processes are safe.
Automated processes
Automating advanced manufacturing processes is a great way to increase efficiency and reduce costs. In many cases, automation is the most effective way to make the most of floor space while also maximizing production efficiency. Manufacturers can cut costs and improve productivity by leveraging automation technology and collecting data. Automation of the process industry can also help save time and money. Although initial investments can be costly, automation will eventually improve a company's bottom line.
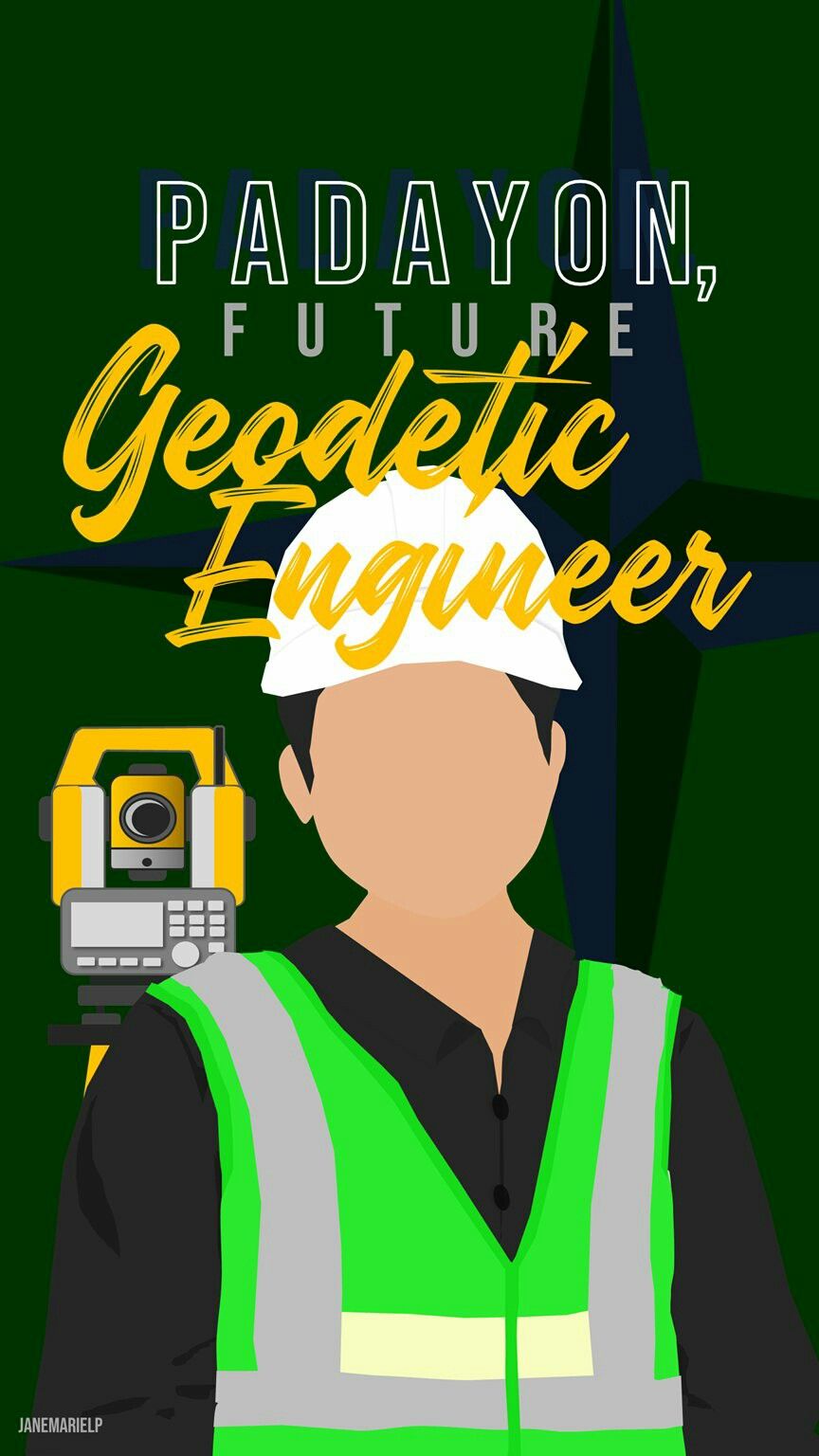
Companies combine automated processes with advanced manufacturing techniques today. Audi, for example, uses automated welding and bonding to reduce production times and save energy and weight. They also use advanced manufacturing techniques such as regenerative-braking conveyor systems. 3D printing is the most recent advancement in manufacturing. Although it has been around since 1980s, it has just recently become mainstream. But what makes it so appealing to manufacturers, you ask?
Internet of Things
Manufacturing is being transformed by the IIoT revolution. This revolution uses sensors to monitor machinery and processes. These sensors gather data from many parts of manufacturing and feed this data to a central center station. Data is then analysed to aid in optimizing processes and eliminating waste. Advanced manufacturers are already using IIoT sensors to monitor processes and optimize production. The IIoT sensors are the industrial version connected key fobs.
IIoT deployment needs a detailed roadmap and development capabilities in order to deploy use cases efficiently and scale effectively. The following roadmap is provided by an automaker. It shows three phases of deployment.
Cost-effectiveness
The costs of advanced manufacturing are not always directly comparable with conventional production systems. Rather, the traditional cost-benefit analysis is an insufficient basis for evaluating economic benefits. However, a holistic model that considers both costs and benefits of technology can help to identify new benefits and accelerate decision-making processes. In this paper, Schroer and Munker develop an advanced cost-benefit tool that addresses the key issues associated with AMS implementation.
Advances in information technology are rapidly changing the face of manufacturing and their costs. Information technology is making production systems more interconnected and intelligent. Cost pressures are increasing the focus on productivity and the ability of companies to respond to customers' needs. The rapid adoption of advanced manufacturing technologies will likely accelerate the implementation of new technologies and their cost-effectiveness. As the industry digitizes, this will likely lead to a rapid adoption of such technologies.
Human error reduction
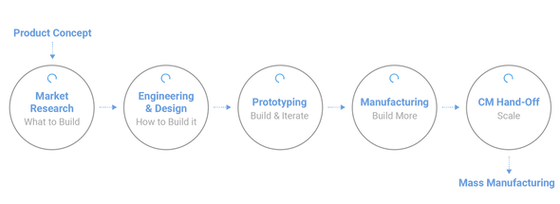
While humans make mistakes, the process they use to produce a product is usually designed to protect it. Employees who fail to follow written instructions or don't understand them can cause human error. For example, pharmaceutical laboratories must follow specific procedures when making drugs. An employee might think they understand the process, and so proceed to make the drug mixture without reading the written instructions.
Human error can also be reduced by effective communication between junior staff and senior managers. Employees who are treated unfairly are more likely to make mistakes. Managers should not punish employees for asking questions. Employees need to feel comfortable asking questions, and if they feel uncomfortable with the way they are treated, they will not be likely to take corrective actions. Respect senior employees' opinions and communicate with them in a friendly and professional manner.
FAQ
What is it like to manage a logistics company?
A successful logistics business requires a lot more than just knowledge. Effective communication skills are necessary to work with suppliers and clients. You should be able analyse data and draw inferences. You will need to be able handle pressure well and work in stressful situations. You must be creative and innovative to develop new ideas to improve efficiency. Strong leadership qualities are essential to motivate your team and help them achieve their organizational goals.
To meet tight deadlines, you must also be efficient and organized.
What kind of jobs are there in logistics?
There are different kinds of jobs available in logistics. Here are some:
-
Warehouse workers - They load and unload trucks and pallets.
-
Transportation drivers – These drivers drive trucks and wagons to transport goods and pick up the goods.
-
Freight handlers are people who sort and pack freight into warehouses.
-
Inventory managers – They manage the inventory in warehouses.
-
Sales reps - They sell products and services to customers.
-
Logistics coordinators - They organize and plan logistics operations.
-
Purchasing agents: They are responsible for purchasing goods and services to support company operations.
-
Customer service representatives - Answer calls and email from customers.
-
Shipping clerks – They process shipping orders, and issue bills.
-
Order fillers - These people fill orders based on what has been ordered.
-
Quality control inspectors are responsible for inspecting incoming and outgoing products looking for defects.
-
Other - Logistics has many other job opportunities, including transportation supervisors, logistics specialists, and cargo specialists.
What is production planning?
Production Planning refers to the development of a plan for every aspect of production. This document aims to ensure that everything is planned and ready when you are ready to shoot. This document should also include information on how to get the best result on set. This includes information on shooting times, locations, cast lists and crew details.
It is important to first outline the type of film you would like to make. You may already know where you want the film to be shot, or perhaps you have specific locations and sets you wish to use. Once you have determined your scenes and locations, it is time to start figuring out the elements that you will need for each scene. For example, you might decide that you need a car but don't know exactly what model you want. In this case, you could start looking up cars online to find out what models are available and then narrow your choices by choosing between different makes and models.
After you've found the perfect car, it's time to start thinking about adding extras. What about additional seating? Maybe you need someone to move around in the back. You might want to change your interior color from black and white. These questions will help guide you in determining the ideal look and feel for your car. The type of shots that you are looking for is another thing to consider. Do you want to film close-ups, or wider angles? Maybe you want to show the engine and the steering wheel. These details will help identify the exact car you wish to film.
Once you have made all the necessary decisions, you can start to create a schedule. A schedule will tell you when you need to start shooting and when you need to finish. A schedule for each day will detail when you should arrive at the location and when you need leave. Everyone knows exactly what they should do and when. You can also make sure to book extra staff in advance if you have to hire them. It's not worth paying someone to show up if you haven't told him.
When creating your schedule, you will also need to consider the number of days you need to film. Some projects only take one or two days, while others may last weeks. While creating your schedule, it is important to remember whether you will require more than one shot per day. Multiplying takes in the same area will result both in increased costs and a longer time. It's better to be safe than sorry and shoot less takes if you're not certain whether you need more takes.
Budgeting is another crucial aspect of production plan. As it will allow you and your team to work within your financial means, setting a realistic budget is crucial. You can always lower the budget if you encounter unexpected problems. It is important to not overestimate how much you will spend. You'll end up with less money after paying for other things if the cost is underestimated.
Production planning is a very detailed process, but once you understand how everything works together, it becomes easier to plan future projects.
What are the logistics products?
Logistics refers to the movement of goods from one place to another.
They include all aspects associated with transport including packaging, loading transporting, unloading storage, warehousing inventory management customer service, distribution returns and recycling.
Logisticians ensure that the product is delivered to the correct place, at the right time, and under safe conditions. Logisticians assist companies in managing their supply chains by providing information such as demand forecasts, stock levels and production schedules.
They can also track shipments in transit and monitor quality standards.
Why automate your warehouse
Automation has become increasingly important in modern warehousing. With the rise of ecommerce, there is a greater demand for faster delivery times as well as more efficient processes.
Warehouses should be able adapt quickly to new needs. To do so, they must invest heavily in technology. Automation of warehouses offers many benefits. Here are some benefits of investing in automation
-
Increases throughput/productivity
-
Reduces errors
-
Improves accuracy
-
Safety is boosted
-
Eliminates bottlenecks
-
Companies can scale up more easily
-
This makes workers more productive
-
Gives you visibility into all that is happening in your warehouse
-
Enhances customer experience
-
Improves employee satisfaction
-
This reduces downtime while increasing uptime
-
This ensures that quality products are delivered promptly
-
Eliminates human error
-
It helps ensure compliance with regulations
What is the job of a production plan?
Production planners make sure that every aspect of the project is delivered on-time, within budget, and within schedule. They make sure that the product and services meet client expectations.
How can excess manufacturing production be reduced?
Better inventory management is key to reducing excess production. This would decrease the time that is spent on inefficient activities like purchasing, storing, or maintaining excess stock. This will allow us to free up resources for more productive tasks.
One way to do this is to adopt a Kanban system. A Kanbanboard is a visual tool that allows you to keep track of the work being done. Kanban systems are where work items travel through a series of states until reaching their final destination. Each state represents an individual priority level.
When work is completed, it can be transferred to the next stage. A task that is still in the initial stages of a process will be considered complete until it moves on to the next stage.
This keeps work moving and ensures no work is lost. Managers can view the Kanban board to see how much work they have done. This allows them the ability to adjust their workflow using real-time data.
Lean manufacturing, another method to control inventory levels, is also an option. Lean manufacturing is about eliminating waste from all stages of the production process. Anything that does not contribute to the product's value is considered waste. The following are examples of common waste types:
-
Overproduction
-
Inventory
-
Unnecessary packaging
-
Materials in excess
By implementing these ideas, manufacturers can improve efficiency and cut costs.
Statistics
- Many factories witnessed a 30% increase in output due to the shift to electric motors. (en.wikipedia.org)
- In 2021, an estimated 12.1 million Americans work in the manufacturing sector.6 (investopedia.com)
- Job #1 is delivering the ordered product according to specifications: color, size, brand, and quantity. (netsuite.com)
- In the United States, for example, manufacturing makes up 15% of the economic output. (twi-global.com)
- According to the United Nations Industrial Development Organization (UNIDO), China is the top manufacturer worldwide by 2019 output, producing 28.7% of the total global manufacturing output, followed by the United States, Japan, Germany, and India.[52][53] (en.wikipedia.org)
External Links
How To
How to Use Lean Manufacturing for the Production of Goods
Lean manufacturing is a management style that aims to increase efficiency and reduce waste through continuous improvement. It was developed in Japan between 1970 and 1980 by Taiichi Ohno. TPS founder Kanji Tyoda gave him the Toyota Production System, or TPS award. The first book published on lean manufacturing was titled "The Machine That Changed the World" written by Michael L. Watkins and published in 1990.
Lean manufacturing is often defined as a set of principles used to improve the quality, speed, and cost of products and services. It emphasizes eliminating waste and defects throughout the value stream. Lean manufacturing can be described as just-in–time (JIT), total productive maintenance, zero defect (TPM), or even 5S. Lean manufacturing focuses on eliminating non-value-added activities such as rework, inspection, and waiting.
Lean manufacturing improves product quality and costs. It also helps companies reach their goals quicker and decreases employee turnover. Lean manufacturing is considered one of the most effective ways to manage the entire value chain, including suppliers, customers, distributors, retailers, and employees. Many industries worldwide use lean manufacturing. Toyota's philosophy is the foundation of its success in automotives, electronics and appliances, healthcare, chemical engineers, aerospace, paper and food, among other industries.
Five basic principles of Lean Manufacturing are included in lean manufacturing
-
Define Value - Determine the value that your business brings to society. Also, identify what sets you apart from your competitors.
-
Reduce waste - Stop any activity that isn't adding value to the supply chains.
-
Create Flow - Ensure work moves smoothly through the process without interruption.
-
Standardize & simplify - Make processes consistent and repeatable.
-
Build Relationships- Develop personal relationships with both internal as well as external stakeholders.
Lean manufacturing, although not new, has seen renewed interest in the economic sector since 2008. Many businesses have adopted lean production techniques to make them more competitive. Economists think that lean manufacturing is a crucial factor in economic recovery.
With many benefits, lean manufacturing is becoming more common in the automotive industry. These include higher customer satisfaction, lower inventory levels, lower operating expenses, greater productivity, and improved overall safety.
Any aspect of an enterprise can benefit from Lean manufacturing. It is especially useful for the production aspect of an organization, as it ensures that every step in the value chain is efficient and effective.
There are three types of lean manufacturing.
-
Just-in-Time Manufacturing (JIT): This type of lean manufacturing is commonly referred to as "pull systems." JIT is a process in which components can be assembled at the point they are needed, instead of being made ahead of time. This approach reduces lead time, increases availability and reduces inventory.
-
Zero Defects Manufacturing (ZDM): ZDM focuses on ensuring that no defective units leave the manufacturing facility. Repairing a part that is damaged during assembly should be done, not scrapping. This applies to finished goods that may require minor repairs before shipment.
-
Continuous Improvement (CI: Continuous improvement aims to increase the efficiency of operations by constantly identifying and making improvements to reduce or eliminate waste. Continuous Improvement involves continuous improvement of processes.