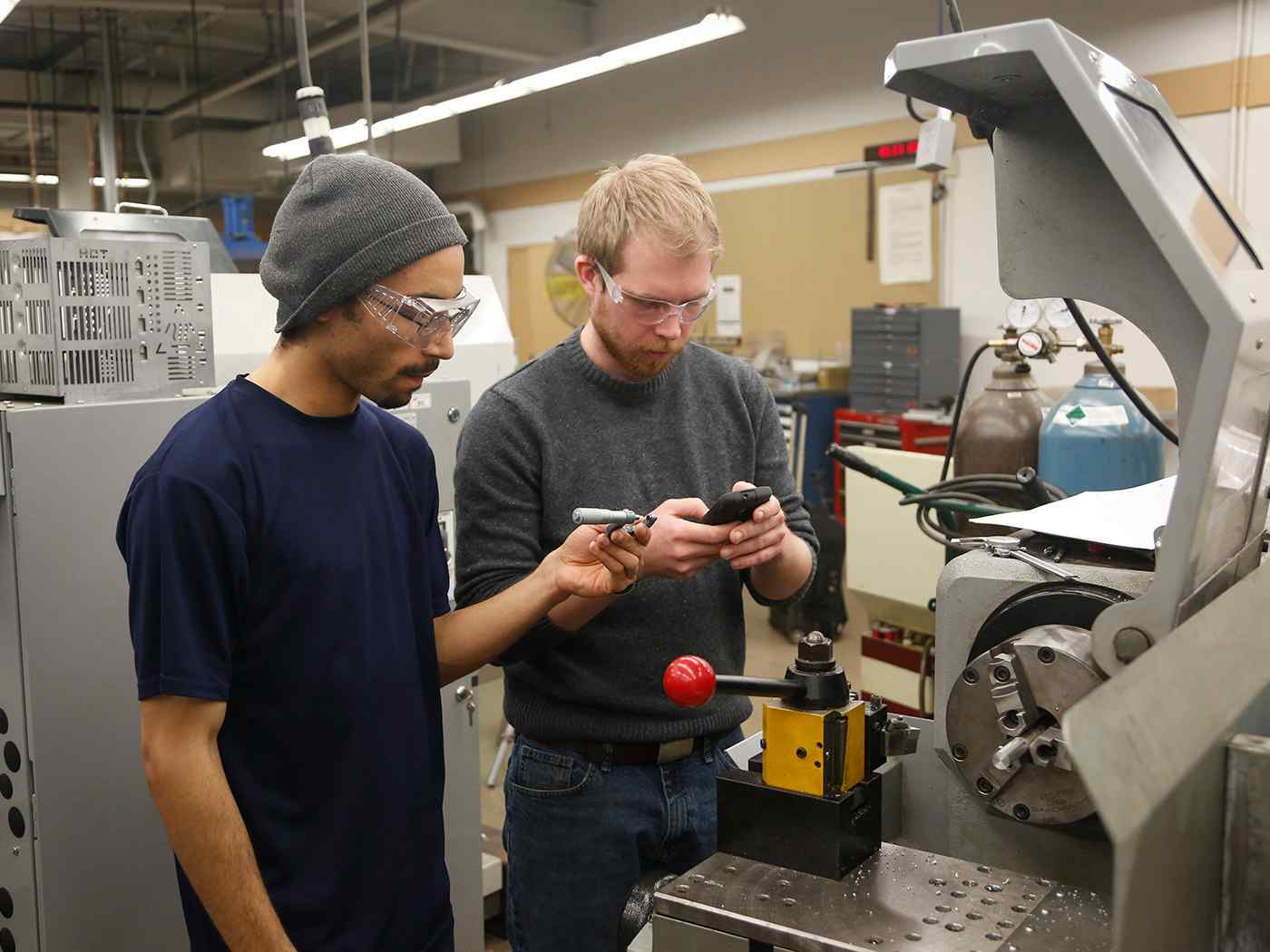
You can check out a supply chain entry-level salary if you are interested in a career as a supply chain professional. Dispatchers is one example. CPSM certification is an additional credential which goes beyond the ASCM standards. CPSM certification might be an option if you want to earn a better starting salary.
CPSM certification is a credential which exceeds the ASCM standard
The CPSM certification is a global credential that provides supply chain professionals with the tools necessary to meet the complex challenges of a modern supply chain. It is administered by the Institute for Supply Management and requires three tests and five years of full-time supply chain employment. For your CPSM certification to be maintained, you will need 60 credits of continuing educational.
Many employers are seeking a CPSM certificate. This credential has a higher pass rate than those who don't have it. The CSCP exam usually takes three to six months. It's a great way of demonstrating your knowledge in supply-chain management and to showcase your abilities during interviews. On your LinkedIn profile, it is important to include your certifications.
Obtaining a CPSM Certification can help you secure a career that pays as much as a ASCM entry-level position. CPSM certification allows you to prove that you have a deep understanding of supply chain operations and are able to support the organization's goals.
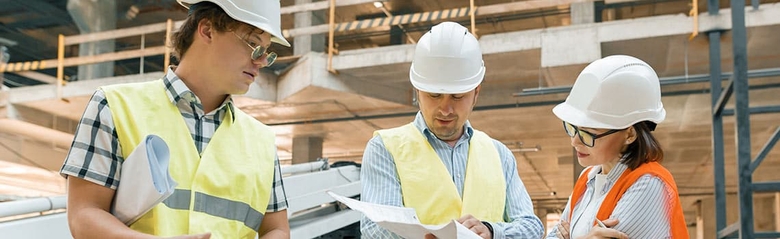
FAQ
How does manufacturing avoid bottlenecks in production?
To avoid production bottlenecks, ensure that all processes run smoothly from the moment you receive your order to the time the product ships.
This includes planning to meet capacity requirements and quality control.
Continuous improvement techniques such Six Sigma can help you achieve this.
Six Sigma is a management method that helps to improve quality and reduce waste.
It's all about eliminating variation and creating consistency in work.
Is automation necessary in manufacturing?
Not only are service providers and manufacturers important, but so is automation. Automation allows them to deliver services quicker and more efficiently. They can also reduce their costs by reducing human error and improving productivity.
What does warehouse refer to?
A warehouse or storage facility is where goods are stored before they are sold. It can be an indoor space or an outdoor area. In some cases, it may be a combination of both.
What does it take for a logistics enterprise to succeed?
To be a successful businessman in logistics, you will need many skills and knowledge. You must have good communication skills to interact effectively with your clients and suppliers. You will need to know how to interpret data and draw conclusions. You need to be able work under pressure and manage stressful situations. You must be creative and innovative to develop new ideas to improve efficiency. You must be a strong leader to motivate others and direct them to achieve organizational goals.
It is also important to be efficient and well organized in order meet deadlines.
What makes a production planner different from a project manger?
The difference between a product planner and project manager is that a planer is typically the one who organizes and plans the entire project. A production planner, however, is mostly involved in the planning stages.
Statistics
- It's estimated that 10.8% of the U.S. GDP in 2020 was contributed to manufacturing. (investopedia.com)
- Many factories witnessed a 30% increase in output due to the shift to electric motors. (en.wikipedia.org)
- Job #1 is delivering the ordered product according to specifications: color, size, brand, and quantity. (netsuite.com)
- [54][55] These are the top 50 countries by the total value of manufacturing output in US dollars for its noted year according to World Bank.[56] (en.wikipedia.org)
- According to a Statista study, U.S. businesses spent $1.63 trillion on logistics in 2019, moving goods from origin to end user through various supply chain network segments. (netsuite.com)
External Links
How To
Six Sigma in Manufacturing
Six Sigma refers to "the application and control of statistical processes (SPC) techniques in order to achieve continuous improvement." Motorola's Quality Improvement Department developed it at their Tokyo plant in Japan in 1986. Six Sigma's core idea is to improve the quality of processes by standardizing and eliminating defects. In recent years, many companies have adopted this method because they believe there is no such thing as perfect products or services. Six Sigma seeks to reduce variation between the mean production value. This means that if you take a sample of your product, then measure its performance against the average, you can find out what percentage of the time the process deviates from the norm. If you notice a large deviation, then it is time to fix it.
The first step toward implementing Six Sigma is understanding how variability works in your business. Once you have a good understanding of the basics, you can identify potential sources of variation. These variations can also be classified as random or systematic. Random variations are caused when people make mistakes. While systematic variations are caused outside of the process, they can occur. Random variations would include, for example, the failure of some widgets to fall from the assembly line. However, if you notice that every time you assemble a widget, it always falls apart at exactly the same place, then that would be a systematic problem.
After identifying the problem areas, you will need to devise solutions. That solution might involve changing the way you do things or redesigning the process altogether. Test them again once you've implemented the changes. If they didn't work, then you'll need to go back to the drawing board and come up with another plan.