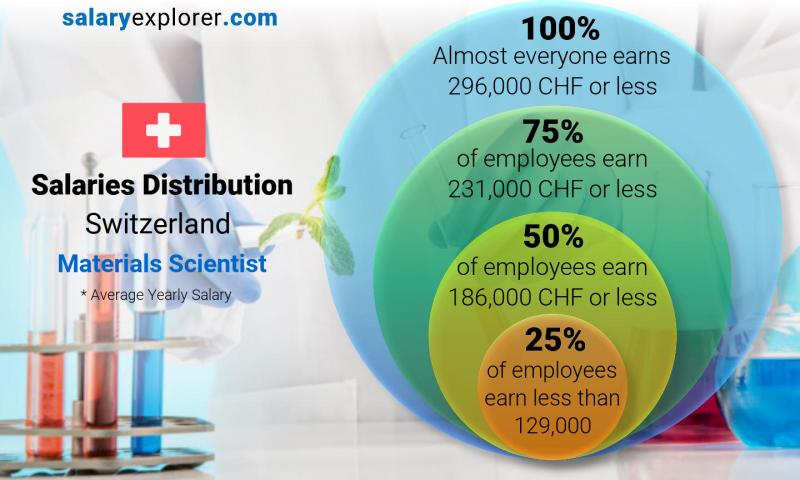
There are several good reasons to be an engineer. These include the satisfaction of solving problems in the real world and the chance to help people. In addition, engineering is a growing field that offers good career growth and high-paying jobs.
The average salary for an engineering technologist is $52,171 per year. This is about 1% higher than national average $51,860. That's equal to $2,174 for each hour of work. This pay is based off an estimated federal income tax rate of 22 percent.
They assist the engineers in the design, development, and testing of machinery, appliances and equipment. They can help with the production process in factories and during the research and design phase before production. They may be involved in the analysis of product designs and preparing layouts for components that will have to be made. They may also test the equipment for quality or calibrate new devices.
Other engineering technology specialists use CAD to convert the designs of engineers and architects into technical drawing. These technicians may also be in charge of entering job specifications, making changes to existing drawings, and completing reports.
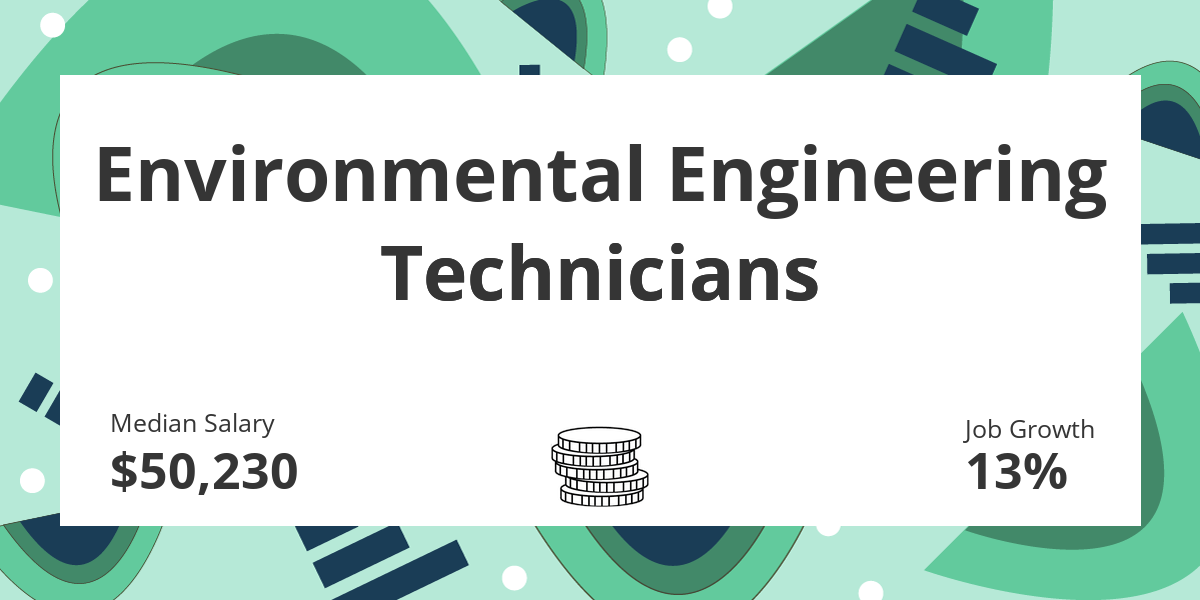
A bachelor's or a master's degree is usually required to become an engineering technician. However, if you have a degree in electrical engineering or electronics engineering, it can improve your chances of landing a job. Most employers prefer to hire individuals who have earned these degrees because they have more experience and training in the field of engineering technology than those with less education.
The salaries of manufacturing engineering technicians range from $22,295 to $94100. A median salary is $61,260. The majority of these employees are between 26 and 31 years old, with about one-third falling in the age group of 31 to 36 years.
They are employed primarily in the manufacturing industry, helping engineers to solve problems that may affect the production process or the layout of the plant. You can find them at companies that manufacture consumer goods, industrial machinery, food products and more.
They are generally employed full time, and they are expected to work over 40 hours a weekly. Their duties also vary according to the organization they work for.
Under the supervision of a chemist engineer, chemical engineering technologists carry out experiments and develop chemical processes. They also perform inventories. Also, they may be required to estimate manufacturing costs.
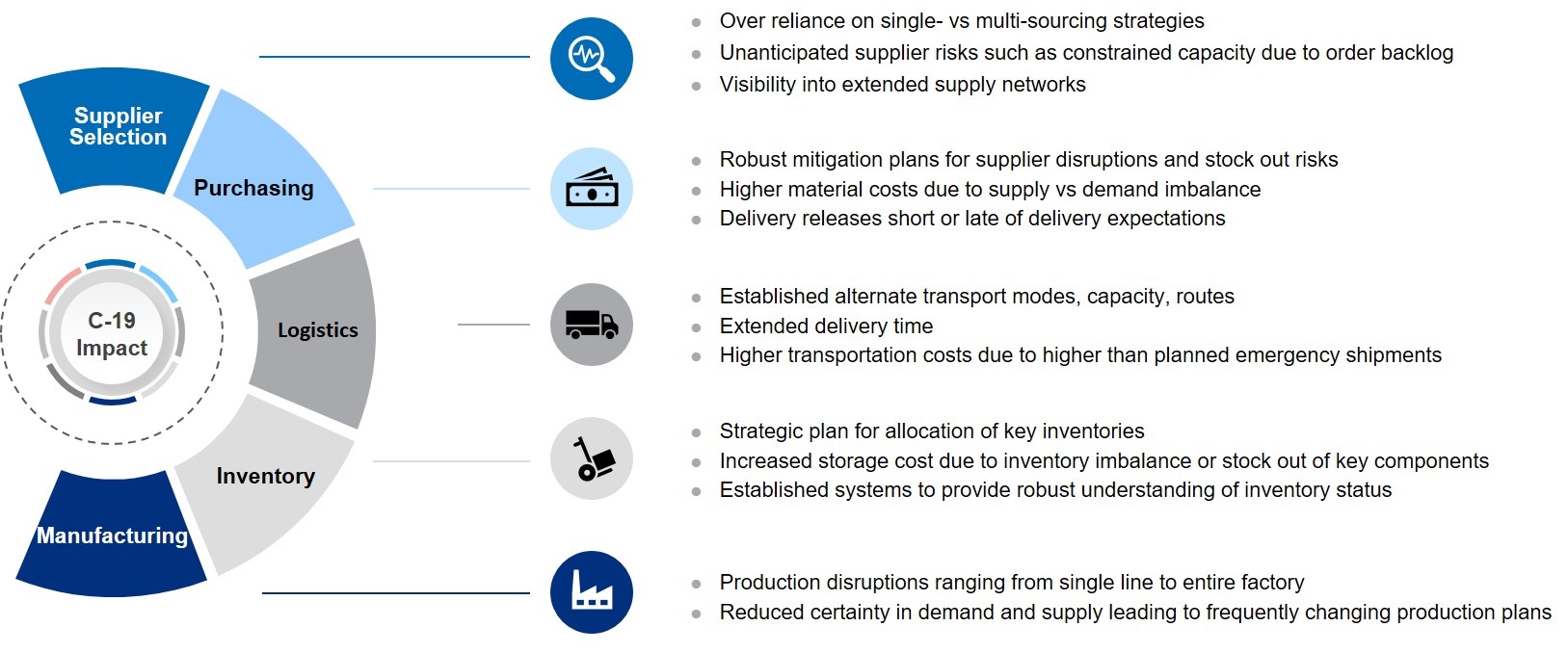
This group is dominated by a young workforce and has a lower employment rate than the overall labor force, but jobs are projected to grow slightly through 2031. This occupation was reported to have a salary median of $60,220 by the BLS in May 2021.
Jobs in electronics engineering technology are an excellent way to get hands-on training with electronic technology and components. These positions are very popular with recent graduates. You can find them in manufacturing, research laboratories or engineering services.
It's important to take into account the potential salary before accepting any job offers. Increasing your salary is possible in a few ways, including changing to a different employer that will pay more, gaining advanced education, and managing your experience.
FAQ
How can manufacturing efficiency improved?
First, identify the factors that affect production time. We must then find ways that we can improve these factors. If you don’t know where to begin, consider which factors have the largest impact on production times. Once you identify them, look for solutions.
What are the products and services of logistics?
Logistics refers to the movement of goods from one place to another.
They include all aspects of transport, including packaging, loading, transporting, unloading, storing, warehousing, inventory management, customer service, distribution, returns, and recycling.
Logisticians ensure that the right product reaches the right place at the right time and under safe conditions. Logisticians assist companies in managing their supply chains by providing information such as demand forecasts, stock levels and production schedules.
They keep track and monitor the transit of shipments, maintain quality standards, order replenishment and inventories, coordinate with suppliers, vendors, and provide support for sales and marketing.
What makes a production planner different from a project manger?
The primary difference between a producer planner and a manager of a project is that the manager usually plans and organizes the whole project, while a production planner is only involved in the planning stage.
What are the 7 Rs of logistics.
The acronym "7R's" of Logistics stands for seven principles that underpin logistics management. It was created by the International Association of Business Logisticians and published in 2004 under its "Seven Principles of Logistics Management".
The following letters form the acronym:
-
Responsible - to ensure that all actions are within the legal requirements and are not detrimental to others.
-
Reliable - You can have confidence that you will fulfill your promises.
-
It is reasonable to use resources efficiently and not waste them.
-
Realistic – consider all aspects of operations, from cost-effectiveness to environmental impact.
-
Respectful - show respect and treat others fairly and fairly
-
Reliable - Find ways to save money and increase your productivity.
-
Recognizable: Provide customers with value-added service
What is the difference between manufacturing and logistics
Manufacturing is the process of creating goods from raw materials by using machines and processes. Logistics includes all aspects related to supply chain management, such as procurement, distribution planning, inventory control and transportation. Logistics and manufacturing are often referred to as one thing. It encompasses both the creation of products and their delivery to customers.
Statistics
- In 2021, an estimated 12.1 million Americans work in the manufacturing sector.6 (investopedia.com)
- Job #1 is delivering the ordered product according to specifications: color, size, brand, and quantity. (netsuite.com)
- You can multiply the result by 100 to get the total percent of monthly overhead. (investopedia.com)
- [54][55] These are the top 50 countries by the total value of manufacturing output in US dollars for its noted year according to World Bank.[56] (en.wikipedia.org)
- According to a Statista study, U.S. businesses spent $1.63 trillion on logistics in 2019, moving goods from origin to end user through various supply chain network segments. (netsuite.com)
External Links
How To
How to use lean manufacturing in the production of goods
Lean manufacturing is a management system that aims at increasing efficiency and reducing waste. It was developed by Taiichi Okono in Japan, during the 1970s & 1980s. TPS founder Kanji Takoda awarded him the Toyota Production System Award (TPS). The first book published on lean manufacturing was titled "The Machine That Changed the World" written by Michael L. Watkins and published in 1990.
Lean manufacturing is often defined as a set of principles used to improve the quality, speed, and cost of products and services. It is about eliminating defects and waste from all stages of the value stream. Just-in-time (JIT), zero defect (TPM), and 5S are all examples of lean manufacturing. Lean manufacturing is about eliminating activities that do not add value, such as inspection, rework, and waiting.
Lean manufacturing can help companies improve their product quality and reduce costs. Additionally, it helps them achieve their goals more quickly and reduces employee turnover. Lean manufacturing has been deemed one of the best ways to manage the entire value-chain, including customers, distributors as well retailers and employees. Lean manufacturing is widely practiced in many industries around the world. Toyota's philosophy, for example, is what has enabled it to be successful in electronics, automobiles, medical devices, healthcare and chemical engineering as well as paper and food.
Lean manufacturing includes five basic principles:
-
Define Value - Identify the value your business adds to society and what makes you different from competitors.
-
Reduce Waste – Eliminate all activities that don't add value throughout the supply chain.
-
Create Flow: Ensure that the work process flows without interruptions.
-
Standardize and simplify - Make your processes as consistent as possible.
-
Build relationships - Develop and maintain personal relationships with both your internal and external stakeholders.
Lean manufacturing is not a new concept, but it has been gaining popularity over the last few years due to a renewed interest in the economy following the global financial crisis of 2008. Many businesses have adopted lean production techniques to make them more competitive. According to some economists, lean manufacturing could be a significant factor in the economic recovery.
Lean manufacturing has many benefits in the automotive sector. These include improved customer satisfaction, reduced inventory levels, lower operating costs, increased productivity, and better overall safety.
Any aspect of an enterprise can benefit from Lean manufacturing. It is especially useful for the production aspect of an organization, as it ensures that every step in the value chain is efficient and effective.
There are three main types in lean manufacturing
-
Just-in Time Manufacturing: This lean manufacturing method is commonly called "pull systems." JIT is a method in which components are assembled right at the moment of use, rather than being manufactured ahead of time. This approach is designed to reduce lead times and increase the availability of components. It also reduces inventory.
-
Zero Defects Manufacturing (ZDM): ZDM focuses on ensuring that no defective units leave the manufacturing facility. It is better to repair a part than have it removed from the production line if it needs to be fixed. This applies to finished products, which may need minor repairs before they are shipped.
-
Continuous Improvement (CI),: Continuous improvement aims improve the efficiency and effectiveness of operations by continuously identifying issues and making changes to reduce waste. Continuous improvement involves continuous improvement of processes and people as well as tools.