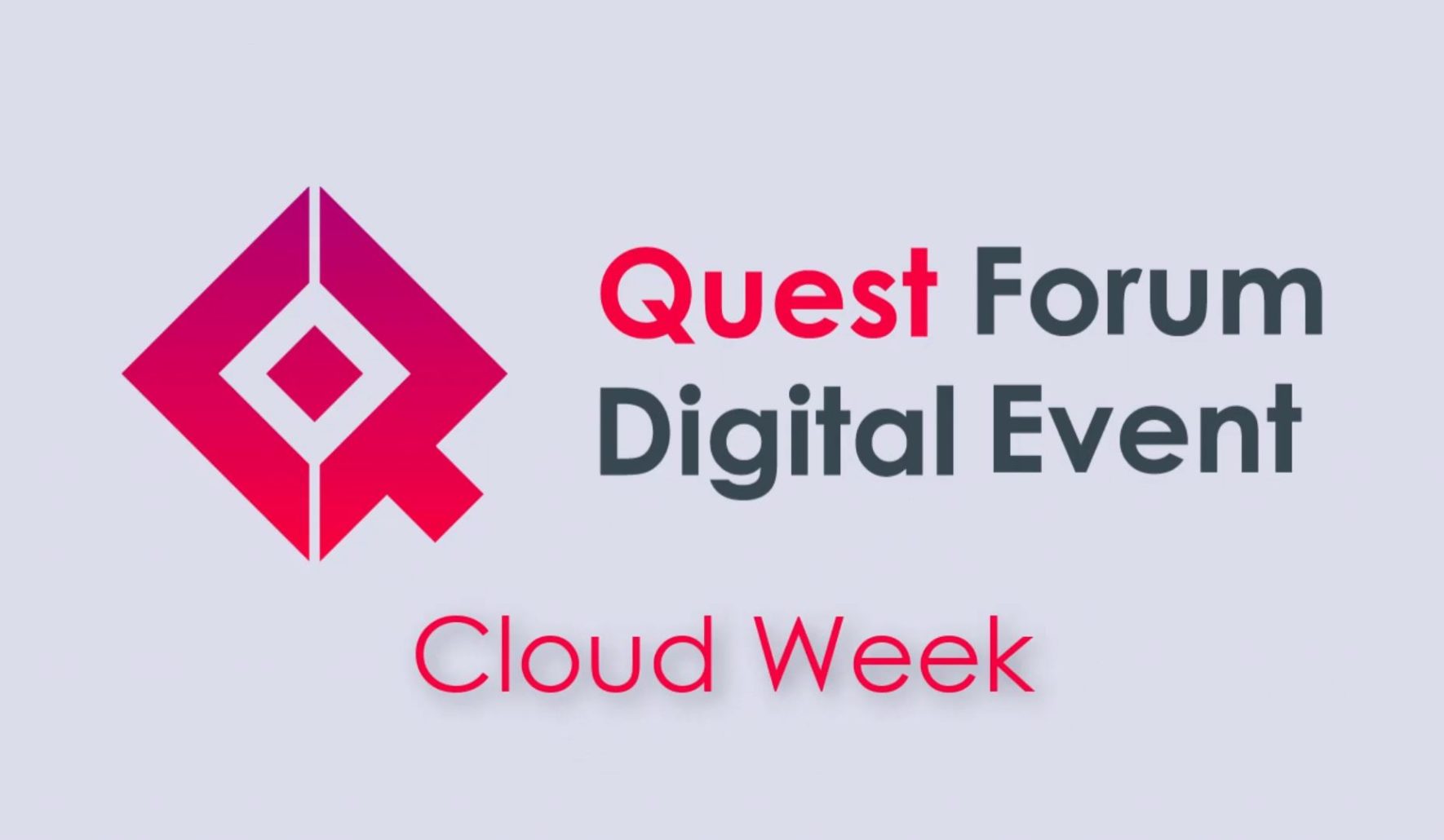
Consumers expect more holistic experiences from products. To meet this expectation, companies need a supply chain capable of delivering personalized products quickly and customized. The modern supply network is more flexible, responsive and adaptable than its older counterpart. Companies can make better decisions and monitor disruptions to ensure reliable and timely deliveries by using data and analytics.
Accenture Strategy, an Accenture service, helps companies transform their supply chain capabilities. This includes creating innovative solutions, accelerating the skills and capabilities of the supply chain workforce, and aligning operating models with business strategies. It also includes a commitment to sustainability and governance. The company's ultimate goal is to create long-term value and satisfaction for its clients.
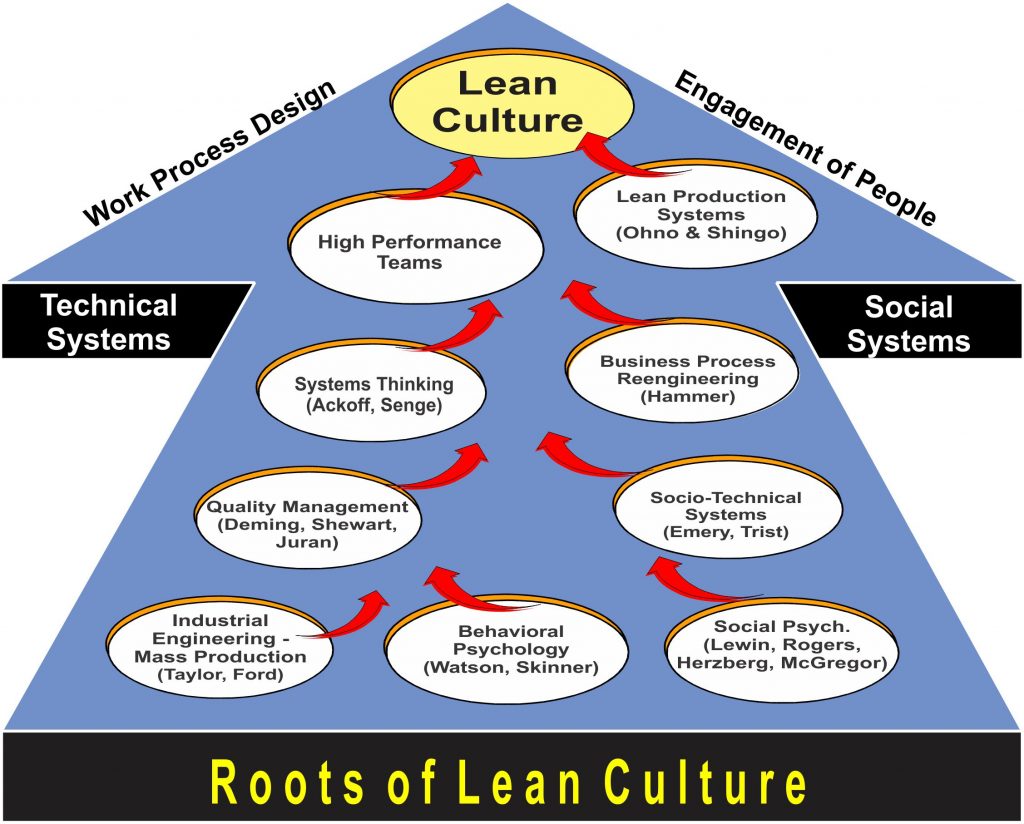
Accenture focuses on improving supply chains on a global scale. This is achieved through the use of both industry knowledge and digital services. They can assist companies in building intelligent supply chains that result in profitable growth and positive social impact. Accenture supply chain experts can work with many industries, from energy to consumer packaged goods. Accenture's supply-chain experts collaborate with clients to create, operate, and transform their supply systems.
Accenture also works closely with clients to implement sustainability initiatives. They also have a global supplier integration program, which helps more companies make better business decisions while helping to create a sustainable, inclusive and ethical supply chain. The company just released a report that gives advice on creating a sustainable and data-driven supply chain, as well as leveraging data and governance. The report contains suggestions for building resilient supply networks and supplier scoring data.
Accenture's supply chain analytics team works with clients to improve their sustainability practices and to help them become more responsible. They are able identify clients' strengths, weaknesses and opportunities for improvement. Blue Yonder technology was used by the team in order to assist companies with optimizing their supply chain.
Accenture is well-known for its supply chain expertise. The company also has considerable purchasing power. In 2007 Accenture introduced an enterprise business system that provides businesses with the capabilities to implement and manage supply chains more effectively. Before Accenture, companies were unable to see beyond a few suppliers and had little knowledge about their supply chains. Companies could not respond quickly to changing demand. The company introduced myConcerto, an enterprise-wide solution that provides companies with comprehensive information on how to monitor their supply chain.
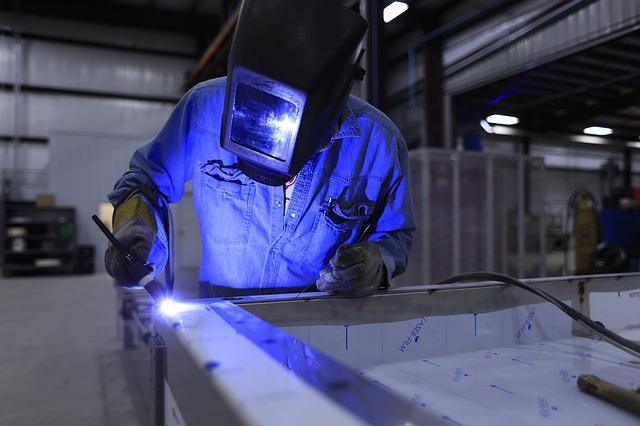
Accenture has a team of supply chain experts who work with Defense Logistics Agency (DLA). This helps them to improve efficiency and reliability in the military supply chain. The DLA manages 520,000 shipping shipments per year and averages 8,000 contracts each day. Accenture collaborates closely with the DLA for product availability and faster delivery times. Accenture works with Coles Supermarkets, to improve the customer experience. The company also developed a Splunk technology control tower monitoring solution.
FAQ
What is the difference between Production Planning and Scheduling?
Production Planning (PP), also known as forecasting and identifying production capacities, is the process that determines what product needs to be produced at any particular time. This can be done by forecasting demand and identifying production capabilities.
Scheduling is the process of assigning specific dates to tasks so they can be completed within the specified timeframe.
What is production planning?
Production Planning is the creation of a plan to cover all aspects, such as scheduling, budgeting. Location, crew, equipment, props and other details. This document aims to ensure that everything is planned and ready when you are ready to shoot. This document should include information about how to achieve the best results on-set. This includes shooting schedules, locations, cast lists, crew details, and equipment requirements.
The first step in filming is to define what you want. You may already know where you want the film to be shot, or perhaps you have specific locations and sets you wish to use. Once you have determined your scenes and locations, it is time to start figuring out the elements that you will need for each scene. Perhaps you have decided that you need to buy a car but aren't sure which model. To narrow your options, you can search online for available models.
After you have selected the car you want, you can begin to think about additional features. What about additional seating? Maybe you need someone to move around in the back. Maybe you'd like to change the interior from black to a white color. These questions can help you decide the right look for your car. Another thing you can do is think about what type of shots are desired. Do you want to film close-ups, or wider angles? Maybe you want the engine or the steering wheels to be shown. This will allow you to determine the type of car you want.
Once you've determined the above, it is time to start creating a calendar. The schedule will show you when to begin shooting and when to stop. A schedule for each day will detail when you should arrive at the location and when you need leave. Everyone knows exactly what they should do and when. Book extra staff ahead of time if you need them. There is no point in hiring someone who won't turn up because you didn't let him know.
Also, consider how many days you will be filming your schedule. Some projects only take one or two days, while others may last weeks. When creating your schedule, be aware of whether you need more shots per day. Multiple takes of the same location will lead to higher costs and take more time. You can't be certain if you will need multiple takes so it is better not to shoot too many.
Another important aspect of production planning is setting budgets. You will be able to manage your resources if you have a realistic budget. Keep in mind that you can always reduce your budget if you face unexpected difficulties. However, you shouldn't overestimate the amount of money you will spend. Underestimating the cost will result in less money after you have paid for other items.
Production planning is a very detailed process, but once you understand how everything works together, it becomes easier to plan future projects.
What are the 4 types manufacturing?
Manufacturing is the process by which raw materials are transformed into useful products through machines and processes. Manufacturing involves many activities, including designing, building, testing and packaging, shipping, selling, service, and so on.
Statistics
- According to a Statista study, U.S. businesses spent $1.63 trillion on logistics in 2019, moving goods from origin to end user through various supply chain network segments. (netsuite.com)
- Job #1 is delivering the ordered product according to specifications: color, size, brand, and quantity. (netsuite.com)
- [54][55] These are the top 50 countries by the total value of manufacturing output in US dollars for its noted year according to World Bank.[56] (en.wikipedia.org)
- In the United States, for example, manufacturing makes up 15% of the economic output. (twi-global.com)
- In 2021, an estimated 12.1 million Americans work in the manufacturing sector.6 (investopedia.com)
External Links
How To
Six Sigma in Manufacturing:
Six Sigma refers to "the application and control of statistical processes (SPC) techniques in order to achieve continuous improvement." It was developed by Motorola's Quality Improvement Department at their plant in Tokyo, Japan, in 1986. Six Sigma's main goal is to improve process quality by standardizing processes and eliminating defects. In recent years, many companies have adopted this method because they believe there is no such thing as perfect products or services. Six Sigma seeks to reduce variation between the mean production value. This means that if you take a sample of your product, then measure its performance against the average, you can find out what percentage of the time the process deviates from the norm. If you notice a large deviation, then it is time to fix it.
Understanding how your business' variability is a key step towards Six Sigma implementation is the first. Once you have this understanding, you will need to identify sources and causes of variation. Also, you will need to identify the sources of variation. Random variations are caused when people make mistakes. While systematic variations are caused outside of the process, they can occur. Random variations would include, for example, the failure of some widgets to fall from the assembly line. If however, you notice that each time you assemble a widget it falls apart in exactly the same spot, that is a problem.
After identifying the problem areas, you will need to devise solutions. That solution might involve changing the way you do things or redesigning the process altogether. Test them again once you've implemented the changes. If they fail, you can go back to the drawing board to come up with a different plan.