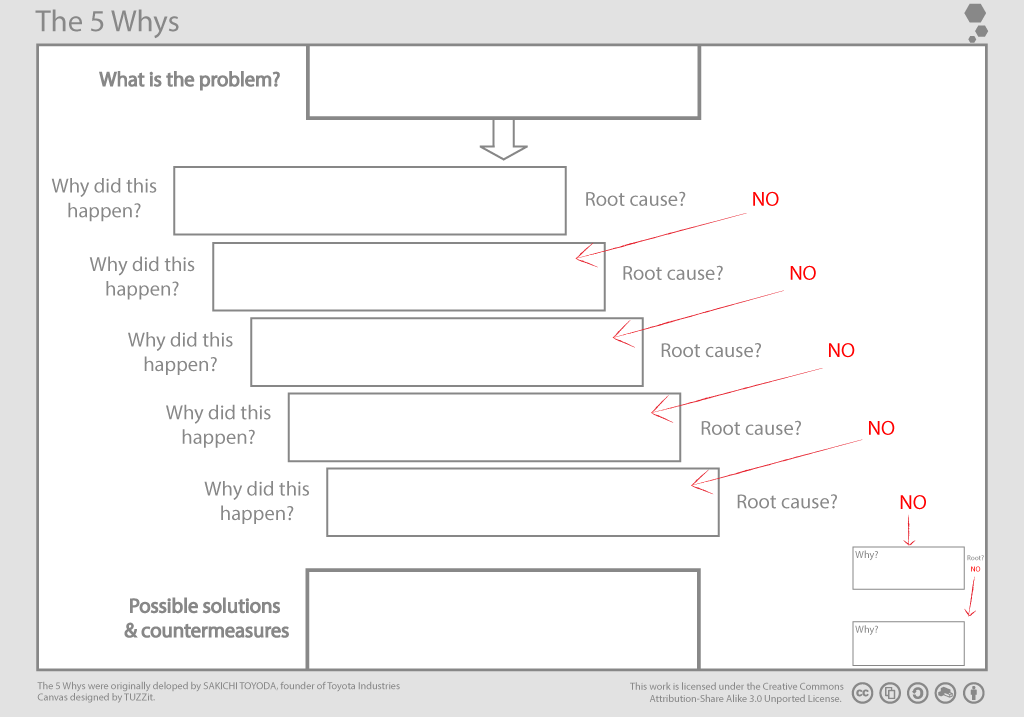
Lean, an acronym used in the manufacturing sector to describe principles and methods is called Lean. It is also a motivating word that encourages improvements in the process.
The Definition Of Lean
If a company wants to become more efficient, they may need to eliminate activities that do not add value to their product or service. This can include idle resources, unused equipment, or other resources that have not been used to the fullest extent.
Lean management is a system designed to eliminate waste in production. This is because the process will never stop, it's always changing and improving.
Lean is the concept that says businesses should be focused on what customers really want and prioritize delivering this value over what they think they require. So, businesses will not waste time or money on products that their customers do not want.
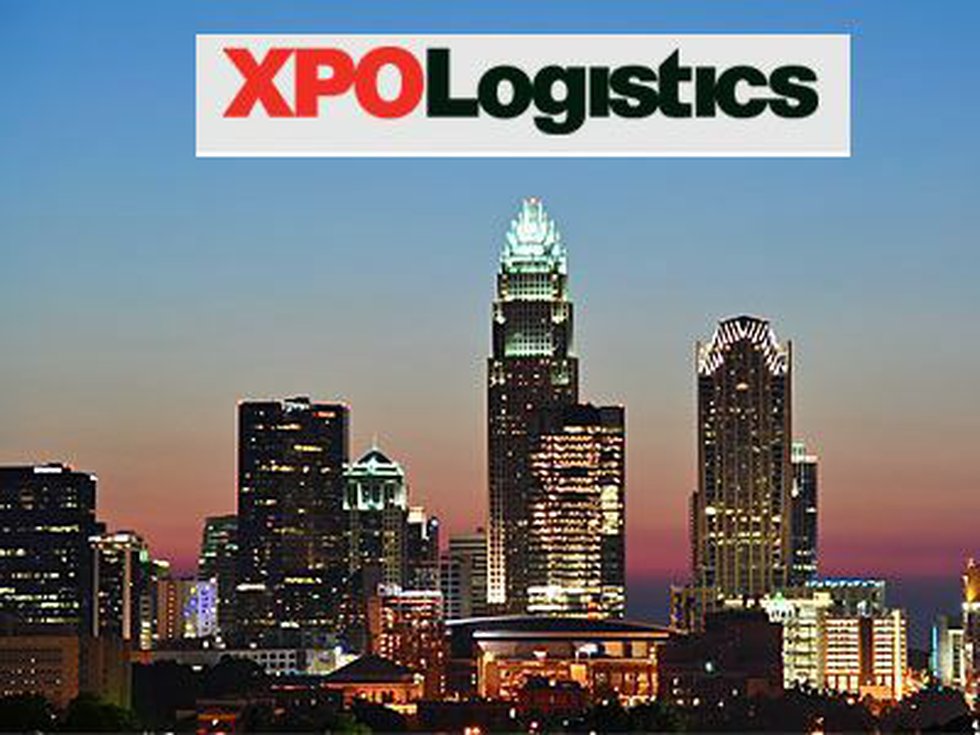
Note that lean principles can be applied to any industry or production method. This is the reason it has become popular in so many different industries.
Lean production, which has existed for quite some time, is a way of focusing on delivering quality products in the right quantities and at the right times. It is an excellent tool for improving efficiency in the manufacturing process.
Toyoda's definition of lean is based on the elimination of waste in production. This includes things like waste in the form of defects, which would not be acceptable to the customer.
Toyoda came up with a solution that involved a flow-process, where workers would stop the production line and inspect an item. If necessary, they would remove it. The company was able to optimize each stage of production to reduce defects and increase productivity.
Jidoka can be defined as a system which automatically stops when an abnormality is detected in a production process. Kaizen is a vital part of lean production.
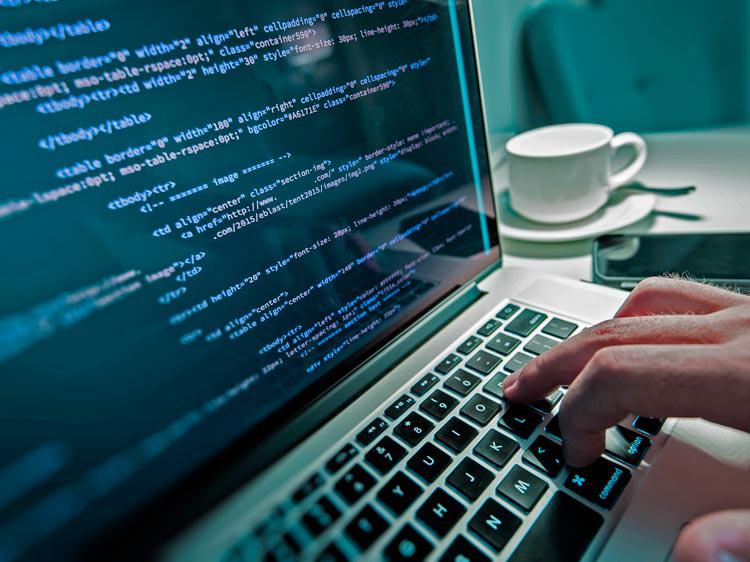
Kaizen is the process of continuous improvement in any process. This process can be applied in any area of business, whether it is the production of products.
A lot of people don't really understand what lean means, but it is a great concept that helps improve the way businesses run. Lean helps companies save time and resources by improving their business processes. They can also build a good reputation among customers.
Remember that lean is a process, not a practice. It's something that needs to be improved at all levels in a business to be successful. All employees should be involved in the lean process so they can all contribute ideas and ensure everything runs smoothly.
FAQ
Are there any Manufacturing Processes that we should know before we can learn about Logistics?
No. No. But, being familiar with manufacturing processes will give you a better understanding about how logistics works.
Why automate your warehouse
Automation has become increasingly important in modern warehousing. The rise of e-commerce has led to increased demand for faster delivery times and more efficient processes.
Warehouses must be able to quickly adapt to changing demands. In order to do this, they need to invest in technology. Automating warehouses is a great way to save money. Here are some of the reasons automation is worth your investment:
-
Increases throughput/productivity
-
Reduces errors
-
Improves accuracy
-
Safety increases
-
Eliminates bottlenecks
-
Allows companies scale more easily
-
It makes workers more efficient
-
This gives you visibility into what happens in the warehouse
-
Enhances customer experience
-
Improves employee satisfaction
-
This reduces downtime while increasing uptime
-
This ensures that quality products are delivered promptly
-
Removes human error
-
It helps ensure compliance with regulations
What does warehouse refer to?
A warehouse is an area where goods are stored before being sold. It can be an indoor space or an outdoor area. In some cases, it may be a combination of both.
Statistics
- [54][55] These are the top 50 countries by the total value of manufacturing output in US dollars for its noted year according to World Bank.[56] (en.wikipedia.org)
- You can multiply the result by 100 to get the total percent of monthly overhead. (investopedia.com)
- In 2021, an estimated 12.1 million Americans work in the manufacturing sector.6 (investopedia.com)
- According to a Statista study, U.S. businesses spent $1.63 trillion on logistics in 2019, moving goods from origin to end user through various supply chain network segments. (netsuite.com)
- Many factories witnessed a 30% increase in output due to the shift to electric motors. (en.wikipedia.org)
External Links
How To
How to Use Lean Manufacturing for the Production of Goods
Lean manufacturing is an approach to management that aims for efficiency and waste reduction. It was created in Japan by Taiichi Ohno during the 1970s and 80s. He received the Toyota Production System award (TPS), from Kanji Toyoda, founder of TPS. Michael L. Watkins published the original book on lean manufacturing, "The Machine That Changed the World," in 1990.
Lean manufacturing is often defined as a set of principles used to improve the quality, speed, and cost of products and services. It emphasizes reducing defects and eliminating waste throughout the value chain. Just-in-time (JIT), zero defect (TPM), and 5S are all examples of lean manufacturing. Lean manufacturing seeks to eliminate non-value added activities, such as inspection, work, waiting, and rework.
Lean manufacturing is a way for companies to achieve their goals faster, improve product quality, and lower costs. Lean Manufacturing is one of the most efficient ways to manage the entire value chains, including suppliers and customers as well distributors and retailers. Many industries worldwide use lean manufacturing. For example, Toyota's philosophy underpins its success in automobiles, electronics, appliances, healthcare, chemical engineering, aerospace, paper, food, etc.
Five fundamental principles underlie lean manufacturing.
-
Define Value- Identify the added value your company brings to society. What makes you stand out from your competitors?
-
Reduce Waste - Eliminate any activity that doesn't add value along the supply chain.
-
Create Flow: Ensure that the work process flows without interruptions.
-
Standardize and simplify – Make processes as repeatable and consistent as possible.
-
Build Relationships- Develop personal relationships with both internal as well as external stakeholders.
Lean manufacturing, although not new, has seen renewed interest in the economic sector since 2008. To increase their competitiveness, many businesses have turned to lean manufacturing. In fact, some economists believe that lean manufacturing will be an important factor in economic recovery.
Lean manufacturing is becoming a popular practice in automotive. It has many advantages. These include improved customer satisfaction, reduced inventory levels, lower operating costs, increased productivity, and better overall safety.
Lean manufacturing can be applied to almost every aspect of an organization. It is especially useful for the production aspect of an organization, as it ensures that every step in the value chain is efficient and effective.
There are three main types of lean manufacturing:
-
Just-in-Time Manufacturing: Also known as "pull systems", this type of lean manufacturing uses just-in-time manufacturing (JIT). JIT means that components are assembled at the time of use and not manufactured in advance. This approach aims to reduce lead times, increase the availability of parts, and reduce inventory.
-
Zero Defects Manufacturing: ZDM ensures that no defective units leave the manufacturing plant. You should repair any part that needs to be repaired during an assembly line. This is also true for finished products that require minor repairs before shipping.
-
Continuous Improvement (CI: Continuous improvement aims to increase the efficiency of operations by constantly identifying and making improvements to reduce or eliminate waste. It involves continuous improvement of processes, people, and tools.