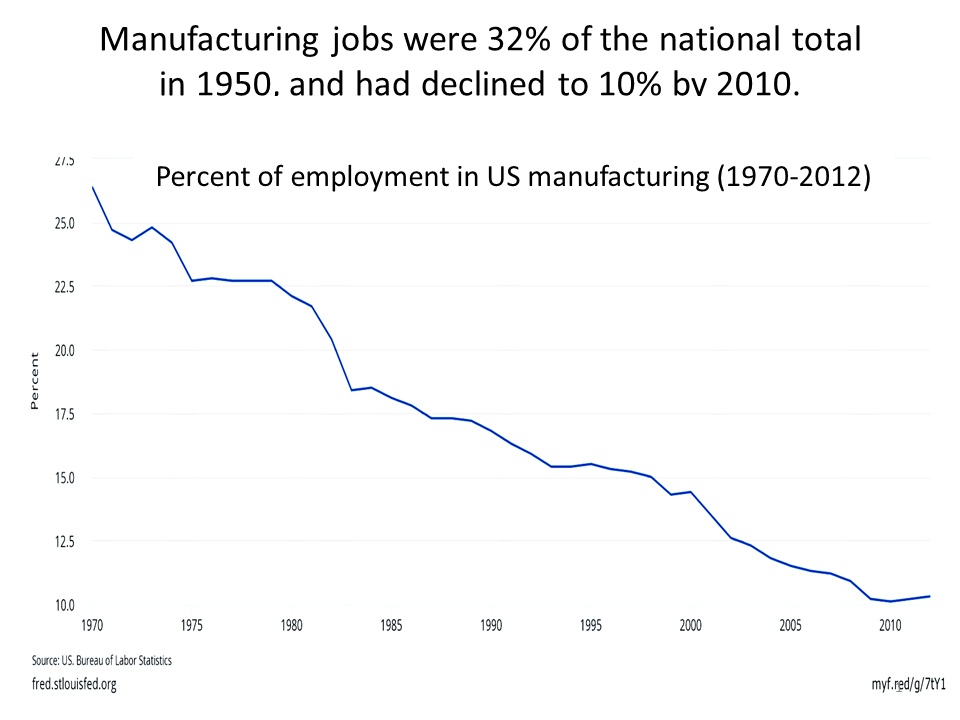
You will be an industrial designer and create innovative products for your home, office, or industry. This article will explain your job duties, what education and training you need, and what salary you can expect. In addition, you'll discover how to get started in this field, and explore the various career paths available. You will also learn about the potential benefits of this job and how to advance. Once you've completed your education, you'll be well on your way to a lucrative career in the design field.
Doing job
The Industrial designer is responsible for generating new products and services through the integration of art, business, and engineering skills. They have to balance functionality and aesthetics, and align with brand strategies. To be a successful Industrial Designer, one must have experience in the field, and a strong portfolio of design concepts and designs brought to reality. Industrial Designers must have strong computer-aided design software skills and be creative in incorporating new technology into products.
Industrial Designers are responsible for developing design regulations and concepts as part of their job. They must have excellent analytical and problem-solving skills and must be able to effectively communicate design concepts to cross-functional teams. They should be able work with engineers and create CAD models. Industrial Designers must also be familiar with Microsoft Office, Solidworks, Keyshot, and other computer-aided design software.
Education necessary
A background in industrial design programs is beneficial for job seekers looking for a career in this area. Students can create an electronic portfolio to showcase their design skills through such programs. Many industrial designers also have a Master of Business Administration degree. This allows them to increase their business acumen while understanding the limitations of products. Industrial designers apply their analytical skills to understand customer needs and reason to invent new products and services.
The kind of work you are interested in is a factor in the education that an industrial designer needs. As a general rule, industrial designers need at least a bachelor's degree. Some schools offer degrees in industrial design, while others do not. Candidats should not only take business and design courses. They also need to take courses that include mathematics, computer science engineering, art, and computer sciences. Prospective employers will also appreciate a portfolio. Like all design jobs, there is a lot of career growth and advancement.
Chances for advancement
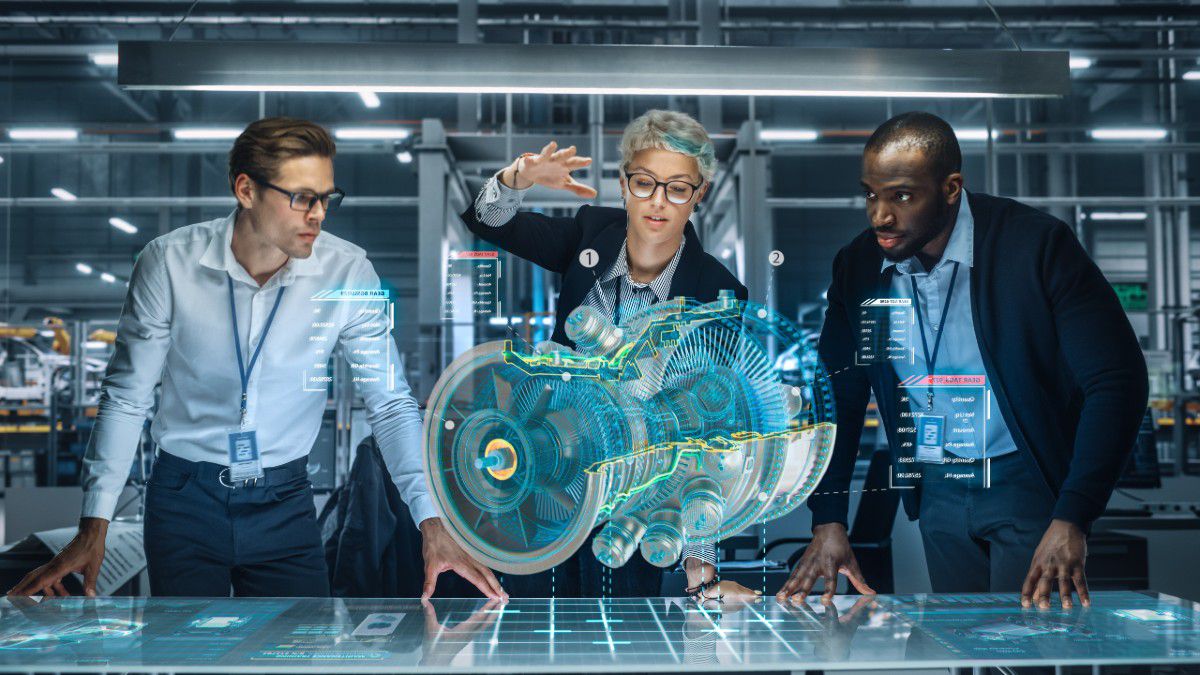
You may be interested in a career as an industrial designer. There are various entry-level roles available at design companies, manufacturing companies, and in-house department heads. Then, you can progress to more senior roles by applying for jobs as a chief designer or design department head. Whatever job you choose to pursue, any chance to develop your design skills will prove beneficial. Listed below are a few of the most common entry-level positions available to industrial designers.
An industrial designer typically has a bachelor's or similar qualification. Many employers are looking for candidates with backgrounds in sketching or graphics, which can help them stand out when applying for jobs. Employers may prefer candidates with 3D modelling and CADD skills. For example, if you're an architect or a civil engineer, an industrial designer will be required to be highly proficient in drafting, rendering, and presenting their work to decision-makers.
Salary
The educational background and experience of industrial designers will impact the annual salary. An industrial designer who holds a Masters or Doctorate degree is likely to earn more than $75,000. A Bachelor's or Master's degree will earn you less. Many industrial designers go on to become managers. Here are some suggestions to help increase your salary. To begin, make sure to read the job description carefully and know your exact salary expectations.
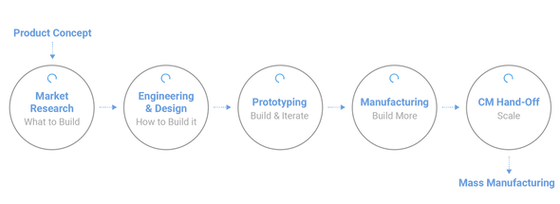
Industrial Designers are paid an average of $62,315, but actual salaries may be higher or less. According to the U.S. Bureau of Labor Statistics (USBoLS), the highest earners in this profession make $106,000 a YEAR. It is important to remember that this is only a guideline. Your salary will ultimately depend on your experience, the industry you're in, and where you're working. Once you have established the skills and whereabouts of your work, it's time to consider the compensation you receive in your area.
FAQ
What are the 7 Rs of logistics?
The 7R's of Logistics is an acronym for the seven basic principles of logistics management. It was published in 2004 by the International Association of Business Logisticians as part of their "Seven Principles of Logistics Management" series.
The acronym consists of the following letters:
-
Responsible – ensure that all actions are legal and don't cause harm to anyone else.
-
Reliable - Have confidence in your ability to fulfill all of your commitments.
-
Be responsible - Use resources efficiently and avoid wasting them.
-
Realistic – consider all aspects of operations, from cost-effectiveness to environmental impact.
-
Respectful – Treat others fairly and equitably.
-
You are resourceful and look for ways to save money while increasing productivity.
-
Recognizable is a company that provides customers with value-added solutions.
Can we automate some parts of manufacturing?
Yes! Since ancient times, automation has been in existence. The Egyptians invented the wheel thousands of years ago. Nowadays, we use robots for assembly lines.
Actually, robotics can be used in manufacturing for many purposes. These include:
-
Line robots
-
Robot welding
-
Robot painting
-
Robotics inspection
-
Robots create products
Manufacturing can also be automated in many other ways. For example, 3D printing allows us to make custom products without having to wait for weeks or months to get them manufactured.
How can overproduction in manufacturing be reduced?
It is essential to find better ways to manage inventory to reduce overproduction. This would decrease the time that is spent on inefficient activities like purchasing, storing, or maintaining excess stock. This would allow us to use our resources for more productive tasks.
Kanban systems are one way to achieve this. A Kanban Board is a visual display that tracks work progress. Kanban systems allow work items to move through different states until they reach their final destination. Each state represents a different priority level.
To illustrate, work can move from one stage or another when it is complete enough for it to be moved to a new stage. If a task is still in its beginning stages, it will continue to be so until it reaches the end.
This keeps work moving and ensures no work is lost. A Kanban board allows managers to monitor how much work is being completed at any given moment. This information allows them to adjust their workflow based on real-time data.
Lean manufacturing is another option to control inventory levels. Lean manufacturing is about eliminating waste from all stages of the production process. Anything that doesn't add value to the product is considered waste. Some common types of waste include:
-
Overproduction
-
Inventory
-
Unnecessary packaging
-
Overstock materials
These ideas can help manufacturers improve efficiency and reduce costs.
Statistics
- In the United States, for example, manufacturing makes up 15% of the economic output. (twi-global.com)
- It's estimated that 10.8% of the U.S. GDP in 2020 was contributed to manufacturing. (investopedia.com)
- [54][55] These are the top 50 countries by the total value of manufacturing output in US dollars for its noted year according to World Bank.[56] (en.wikipedia.org)
- In 2021, an estimated 12.1 million Americans work in the manufacturing sector.6 (investopedia.com)
- (2:04) MTO is a production technique wherein products are customized according to customer specifications, and production only starts after an order is received. (oracle.com)
External Links
How To
How to Use 5S for Increasing Productivity in Manufacturing
5S stands as "Sort", Set In Order", Standardize", Separate" and "Store". Toyota Motor Corporation developed the 5S method in 1954. It helps companies achieve higher levels of efficiency by improving their work environment.
The idea behind standardizing production processes is to make them repeatable and measurable. It means tasks like cleaning, sorting or packing, labeling, and storing are done every day. Workers can be more productive by knowing what to expect.
There are five steps that you need to follow in order to implement 5S. Each step requires a different action to increase efficiency. If you sort items, it makes them easier to find later. You arrange items by placing them in an order. After you have divided your inventory into groups you can store them in easy-to-reach containers. You can also label your containers to ensure everything is properly labeled.
Employees need to reflect on how they do their jobs. Employees should understand why they do the tasks they do, and then decide if there are better ways to accomplish them. To implement the 5S system, employees must acquire new skills and techniques.
The 5S method increases efficiency and morale among employees. They feel more motivated to work towards achieving greater efficiency as they see the results.