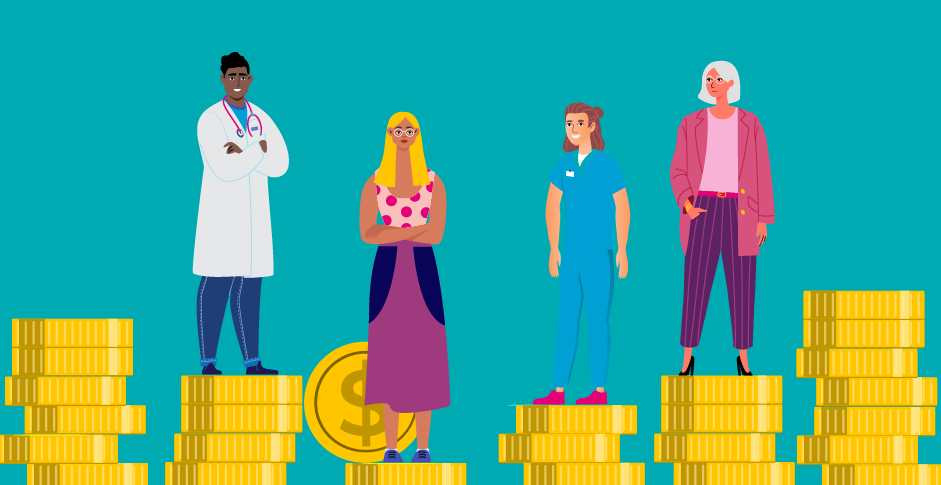
The state-by-state list shows a surprising trend. The top states are the ones you would expect to be there, like the southeastern. This trend is changing, and many states are showing that it's possible to trade off labor quality and cost in order to get the best deals. This trend shows that many factors affect a state's ability attract manufacturing jobs. How can you choose the best location for your company?
Group Five
You've found the right place if you are looking for a state-by-state list of Group Five companies. Group Five's portfolio includes steel pipes, structural components, and industrial engineering products. The company offers pipe design services, offering the best price-to-quality ratio of steel thickness and grade, and stiffening of thin-walled pipes. The company uses the latest CAD systems and computer finite analysis programs to ensure that the pipe design meets all of your needs.
Group Three
According to the United States Census Bureau, there are approximately 50,000 manufacturers in Group Three. This group has low unemployment rates, high economic growth and has a low rate of GDP growth. This is because the majority of manufacturers in this group have small businesses. These limitations aside, data can still be useful. Below are the top-rated manufacturers in each state. Continue reading for more information.
The three largest European manufacturers are Audi, Mercedes-Benz and BMW. Honda and Toyota are now in fourth and fifth, respectively. But, the Big Three has been reclaimed from Honda and Toyota by the Detroit Three. The following table lists these carmakers and their sales in each state. The link below will take you to the list of top-selling cars in each state. There are many models from these manufacturers to choose from, such as SUVs, sedans of medium size, and minivans.
FAQ
What are the differences between these four types?
Manufacturing is the process of transforming raw materials into useful products using machines and processes. It involves many different activities such as designing, building, testing, packaging, shipping, selling, servicing, etc.
What are the 7 Rs of logistics?
The 7R's of Logistics is an acronym for the seven basic principles of logistics management. It was developed by International Association of Business Logisticians (IABL), and published as part of their "Seven Principles of Logistics Management Series" in 2004.
The following letters form the acronym:
-
Responsible - ensure that actions are in compliance with legal requirements and do not cause harm to others.
-
Reliable - Have confidence in your ability to fulfill all of your commitments.
-
Use resources effectively and sparingly.
-
Realistic – Consider all aspects, including cost-effectiveness as well as environmental impact.
-
Respectful - Treat people fairly and equitably
-
You are resourceful and look for ways to save money while increasing productivity.
-
Recognizable - provide customers with value-added services.
Is it necessary to be familiar with Manufacturing Processes before we learn about Logistics.
No. You don't have to know about manufacturing processes before learning about logistics. Knowing about manufacturing processes will help you understand how logistics works.
Statistics
- [54][55] These are the top 50 countries by the total value of manufacturing output in US dollars for its noted year according to World Bank.[56] (en.wikipedia.org)
- You can multiply the result by 100 to get the total percent of monthly overhead. (investopedia.com)
- According to a Statista study, U.S. businesses spent $1.63 trillion on logistics in 2019, moving goods from origin to end user through various supply chain network segments. (netsuite.com)
- It's estimated that 10.8% of the U.S. GDP in 2020 was contributed to manufacturing. (investopedia.com)
- Job #1 is delivering the ordered product according to specifications: color, size, brand, and quantity. (netsuite.com)
External Links
How To
How to use the Just In-Time Production Method
Just-in-time is a way to cut costs and increase efficiency in business processes. It is a process where you get the right amount of resources at the right moment when they are needed. This means that you only pay for what you actually use. Frederick Taylor was the first to coin this term. He developed it while working as a foreman during the early 1900s. He noticed that workers were often paid overtime when they had to work late. He decided that workers would be more productive if they had enough time to complete their work before they started to work.
The idea behind JIT is that you should plan ahead and have everything ready so you don't waste money. The entire project should be looked at from start to finish. You need to ensure you have enough resources to tackle any issues that might arise. You'll be prepared to handle any potential problems if you know in advance. This will prevent you from spending extra money on unnecessary things.
There are different types of JIT methods:
-
Demand-driven: This JIT is where you place regular orders for the parts/materials that are needed for your project. This will enable you to keep track of how much material is left after you use it. It will also allow you to predict how long it takes to produce more.
-
Inventory-based : You can stock the materials you need in advance. This allows you predict the amount you can expect to sell.
-
Project-driven: This approach involves setting aside sufficient funds to cover your project's costs. Once you have an idea of how much material you will need, you can purchase the necessary materials.
-
Resource-based JIT: This is the most popular form of JIT. Here, you allocate certain resources based on demand. You might assign more people to help with orders if there are many. You'll have fewer orders if you have fewer.
-
Cost-based : This is similar in concept to resource-based. But here, you aren't concerned about how many people your company has but how much each individual costs.
-
Price-based pricing: This is similar in concept to cost-based but instead you look at how much each worker costs, it looks at the overall company's price.
-
Material-based: This approach is similar to cost-based. However, instead of looking at the total cost for the company, you look at how much you spend on average on raw materials.
-
Time-based: This is another variation of resource-based JIT. Instead of focusing on how much each employee costs, you focus on how long it takes to complete the project.
-
Quality-based: This is yet another variation of resource-based JIT. Instead of focusing on the cost of each worker or how long it takes, think about how high quality your product is.
-
Value-based JIT: One of the most recent forms of JIT. In this instance, you are not concerned about the product's performance or meeting customer expectations. Instead, you are focused on adding value to the marketplace.
-
Stock-based: This stock-based method focuses on the actual quantity of products being made at any given time. It's used when you want to maximize production while minimizing inventory.
-
Just-intime planning (JIT), is a combination JIT/sales chain management. This refers to the scheduling of the delivery of components as soon after they are ordered. It's important as it reduces leadtimes and increases throughput.