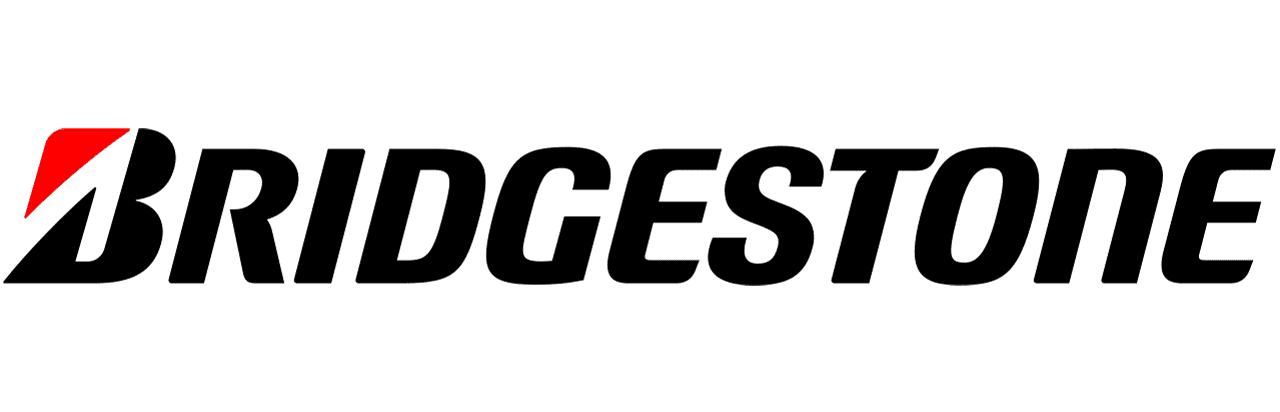
Ohio's Great Recession saw the loss of 166,000 manufacturing jobs. Ohio's manufacturing sector has shown some signs of recovery, but it has not been as fast as other states. Ohio's manufacturing jobs are still below the level they were before the recession.
Ohio's manufacturing jobs have declined due to increased competition from Europe and Japan. Manufacturers have been forced to become technologically more advanced and shed labor costs. The global economic climate has been very lukewarm, which has resulted in job losses.
Ohio's workforce shortfall is one of the greatest challenges that manufacturers have to face. However, there are several initiatives in the state to address the skilled labor shortage. These initiatives are siloed and fragmented, and do not address all of the workforce challenges manufacturers face. The Ohio Governor's Office of Workforce Transformation issued a special report on the workforce shortage, which recommended better collaboration between educators and businesses. However, the report showed a disconnect in the school curriculum and the business needs.
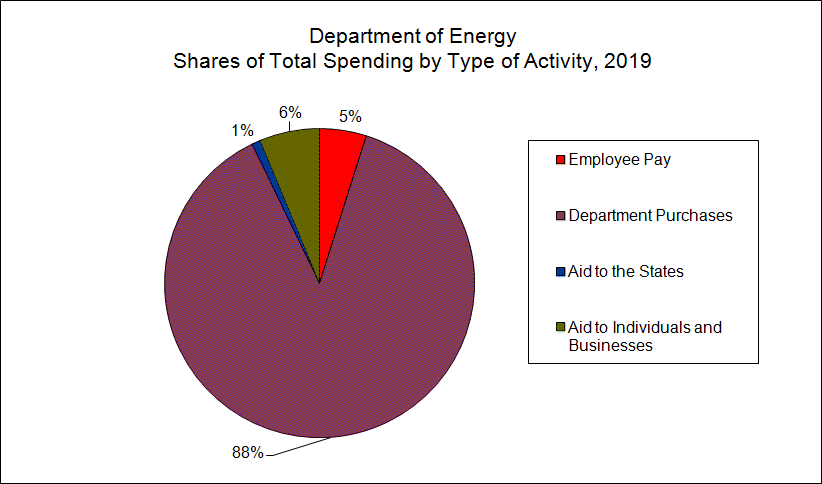
Ohio's workforce is multifaceted, complex and diverse. Workers in manufacturing are less likely than those in other industries to be represented in a union. However, unionized manufacturing jobs offer solid benefits and livable wages.
Ohio's manufacturing industry is a significant contributor to the state's economy. Interstate highways, rails, and inland waterways make it possible for manufacturers to sell their goods efficiently. In addition, the state is a top exporter of goods. Private investors also love the fact that natural gas is produced in the state.
Despite the fact that the state has been able to recover over 50,000 manufacturing jobs within the last four year, Kasich's term as president saw little improvement in job growth. In Kasich's first three terms, the average manufacturing job gain was 7 percent. Manufacturing jobs have dropped by 1,771 jobs in the last two years. These losses are due primarily to the slowing economic growth, the auto industry and lukewarm global market demand.
Ohio is a top exporter of goods, with top export markets including the U.S., Canada, Mexico, and the U.K. Exports have declined by $1.4 billion over the past year. Ohio manufacturers still face major challenges in trade policy. While trade policy changes may be helpful to certain workers, they will not address the whole range of problems.
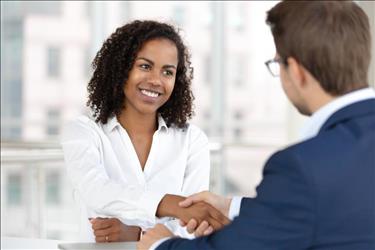
Ohio's primary industry is still manufacturing. Manufacturing jobs are among the most lucrative for semi-skilled workers who have not completed post-secondary education. But wages in Ohio have not kept pace with the production. While manufacturing jobs are more lucrative than those in other industries, they are not sufficient to provide a middle-class lifestyle.
Ohio's workforce in manufacturing is diverse. To keep pace with the rest of the country, Ohio's manufacturing industry has been diversifying. The economy has become more service-oriented, and manufacturing is no longer the primary employer in Ohio. Manufacturers are increasingly focusing on international exposure and future-generation skills.
FAQ
What is production planning?
Production Planning involves developing a plan for all aspects of the production, including scheduling, budgeting, casting, crew, location, equipment, props, etc. This document is designed to make sure everything is ready for when you're ready to shoot. This document should include information about how to achieve the best results on-set. This includes information on shooting times, locations, cast lists and crew details.
The first step in filming is to define what you want. You might have an idea of where you want to film, or you may have specific locations or sets in mind. Once you have determined your scenes and locations, it is time to start figuring out the elements that you will need for each scene. If you decide you need a car and don't know what model to choose, this could be an example. To narrow your options, you can search online for available models.
Once you have found the right car, you can start thinking about extras. Do you need people sitting in the front seats? Maybe you need someone to move around in the back. You might want to change your interior color from black and white. These questions can help you decide the right look for your car. It is also worth considering the types of shots that you wish to take. You will be filming close-ups and wide angles. Maybe you want to show the engine and the steering wheel. These details will help identify the exact car you wish to film.
Once you have established all the details, you can create a schedule. You will know when you should start and when you should finish shooting. You will need to know when you have to be there, what time you have to leave and when your return home. So everyone is clear about what they need to do. Hire extra staff by booking them ahead of time. There is no point in hiring someone who won't turn up because you didn't let him know.
Also, consider how many days you will be filming your schedule. Some projects can be completed in a matter of days or weeks. Others may take several days. When creating your schedule, be aware of whether you need more shots per day. Multiple takes of the same location will lead to higher costs and take more time. It's better to be safe than sorry and shoot less takes if you're not certain whether you need more takes.
Budgeting is another important aspect of production planning. You will be able to manage your resources if you have a realistic budget. If you have to reduce your budget due to unexpected circumstances, you can always lower it later. You shouldn't underestimate the amount you'll spend. Underestimating the cost will result in less money after you have paid for other items.
Planning production is a tedious process. Once you have a good understanding of how everything works together, planning future projects becomes easy.
Is automation important for manufacturing?
Not only is automation important for manufacturers, but it's also vital for service providers. It allows them to offer services faster and more efficiently. It also helps to reduce costs and improve productivity.
What are the main products of logistics?
Logistics is the process of moving goods from one point to another.
These include all aspects related to transport such as packaging, loading and transporting, storing, transporting, unloading and warehousing inventory management, customer service. Distribution, returns, recycling are some of the options.
Logisticians ensure that products reach the right destination at the right moment and under safe conditions. They provide information on demand forecasts as well stock levels, production schedules and availability of raw material.
They can also track shipments in transit and monitor quality standards.
What are the four types in manufacturing?
Manufacturing refers to the transformation of raw materials into useful products by using machines and processes. It involves many different activities such as designing, building, testing, packaging, shipping, selling, servicing, etc.
What makes a production planner different from a project manger?
The major difference between a Production Planner and a Project Manager is that a Project Manager is often the person responsible for organizing and planning the entire project. While a Production Planner is involved mainly in the planning stage,
What are manufacturing and logistic?
Manufacturing refers to the process of making goods using raw materials and machines. Logistics is the management of all aspects of supply chain activities, including procurement, production planning, distribution, warehousing, inventory control, transportation, and customer service. As a broad term, manufacturing and logistics often refer to both the creation and delivery of products.
Why is logistics important in manufacturing?
Logistics are an essential component of any business. They enable you to achieve outstanding results by helping manage product flow from raw materials through to finished goods.
Logistics play an important role in reducing costs as well as increasing efficiency.
Statistics
- [54][55] These are the top 50 countries by the total value of manufacturing output in US dollars for its noted year according to World Bank.[56] (en.wikipedia.org)
- In the United States, for example, manufacturing makes up 15% of the economic output. (twi-global.com)
- Job #1 is delivering the ordered product according to specifications: color, size, brand, and quantity. (netsuite.com)
- You can multiply the result by 100 to get the total percent of monthly overhead. (investopedia.com)
- According to the United Nations Industrial Development Organization (UNIDO), China is the top manufacturer worldwide by 2019 output, producing 28.7% of the total global manufacturing output, followed by the United States, Japan, Germany, and India.[52][53] (en.wikipedia.org)
External Links
How To
How to Use 5S to Increase Productivity in Manufacturing
5S stands to stand for "Sort", “Set In Order", “Standardize", and "Store". Toyota Motor Corporation was the first to develop the 5S approach in 1954. It assists companies in improving their work environments and achieving higher efficiency.
This approach aims to standardize production procedures, making them predictable, repeatable, and easily measurable. It means tasks like cleaning, sorting or packing, labeling, and storing are done every day. Because workers know what they can expect, this helps them perform their jobs more efficiently.
There are five steps to implementing 5S, including Sort, Set In Order, Standardize, Separate and Store. Each step requires a different action to increase efficiency. For example, when you sort things, you make them easy to find later. When items are ordered, they are put together. Once you have separated your inventory into groups and organized them, you will store these groups in easily accessible containers. Make sure everything is correctly labeled when you label your containers.
Employees must be able to critically examine their work practices. Employees must be able to see why they do what they do and find a way to achieve them without having to rely on their old methods. To implement the 5S system, employees must acquire new skills and techniques.
The 5S method not only increases efficiency but also boosts morale and teamwork. They are more motivated to achieve higher efficiency levels as they start to see improvement.