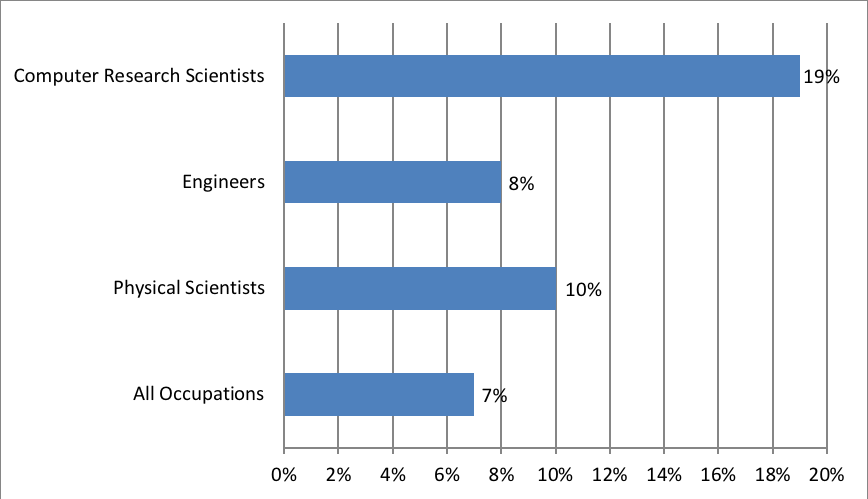
The company's manufacturing director is responsible for overseeing the entire production process. As they are responsible for managing the entire production process, their role is critical. For this job, you must have a great deal of manufacturing experience and be familiar with all new technologies. Some examples of such technologies include robotics and 3D printing. The director who is up-to-date with these technologies will be a valuable asset to the company. As the manufacturing sector continues to develop, the director will find his or her role more complicated as he/she must coordinate with both engineering and operations. Quality control will also be a key focus.
Salary for a Director of Manufacturing
The compensation for a Director in Manufacturing will vary depending on the location they work. Many directors get a salary in the low six figures, but some earn more than others. Based on years of education and experience, the salary of a Director in Manufacturing can also vary. In order to determine how much you'll earn in your area, consider a few factors that may influence your salary:
The salary for a Director Of Manufacturing varies, but in general, the more experience you have, the higher your salary will be. Pay can be affected by your location and cost of living. While you may earn more if your location is a major city, it's possible to make a living in that area. It is important that you are always willing to negotiate a higher salary when the opportunity arises.
The salary for a Director of Manufacturing Operations ranges from $181,500 to $66,000 per annum. The salary of a Director Manufacturing Operations is highly variable. It can vary by up 8% among different cities. A director of manufacturing operations in Fremont, CA can earn between $128,493 and $164,500, which is considerably more than the national average. The salary for a Director, Manufacturing Operations is dependent on where the job is located, what experience the person has, and the company.
Education necessary
The director manufacturing is responsible for overseeing and managing a factory. This job includes managing new employees, quality assurance, working with designers and meeting production standards. A director in manufacturing typically reports directly to the senior management team. This person executes policies and sales initiatives. Candidates should have some experience in manufacturing and be good communicators. Different companies have different requirements for directors of manufacturing.
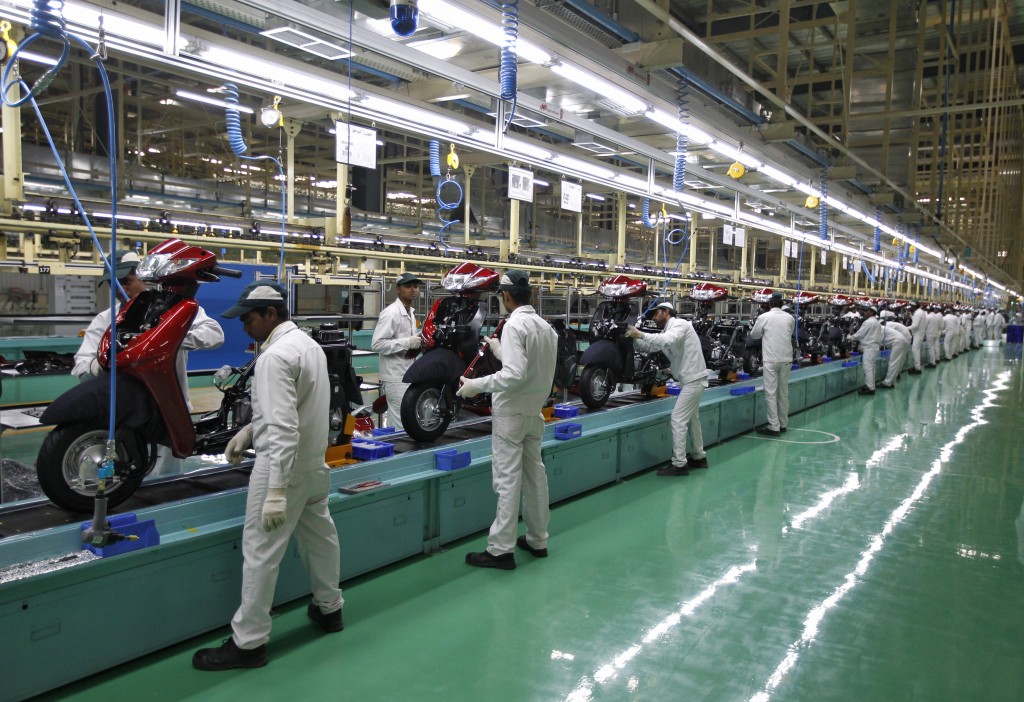
Although a master's degree in engineering does not necessarily make you a director in manufacturing, having a post-secondary education is a great way to increase your knowledge and skill set. A MBA program in business administration or industrial management is a great choice as it helps candidates learn about management, economics and organization. You will eventually be responsible to manage a diverse group.
As a director in manufacturing you will work closely alongside engineers and designers during the product design phase. This stage will see you actively evaluate the feasibility of new processes, and ensure quality standards before committing resources for larger productions. Successful directors not only oversee the production process but also act as coaches for employees. They mentor their employees in risk mitigation and best practices. Manufacturing directors must have strong problem-solving abilities in addition to supervising production.
Experience required
A bachelor's degree in a relevant field and five to 10 years of progressive work experience are often necessary for this position. In general, manufacturing companies prefer to hire employees for this job. The ideal candidate must have a deep understanding of the manufacturing industry and its business goals. Employers may want to see a graduate level. Employers may require candidates to complete additional training in their chosen fields or industries.
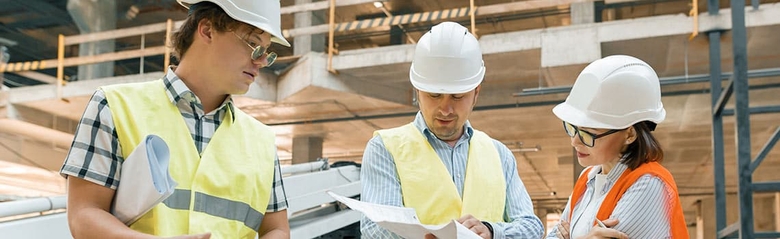
The manufacturing director oversees all aspects of the production process including workers, supervisors and engineers. They may be responsible for solving problems and developing a solution for them. They could also be responsible, in addition to supervising production, for creating and implementing quality-control programmes. A director of manufacturing reports directly to the top executive of the manufacturing organization. Experience in manufacturing is a must. If you are looking to succeed in the manufacturing management position, it is important that you have some experience.
Experience as a manufacturing director will be an asset. Directors must have at least 10 years of relevant experience in a manufacturing environment. These people might have been employed as technicians or supervisors in manufacturing. They should also possess strong communication skills. A director of manufacturing should also have a thorough understanding of business strategy. A director of Manufacturing must also be able to communicate effectively with other departments. As such, the director is responsible for overseeing the production process and ensuring that it meets all quality standards.
FAQ
Can we automate some parts of manufacturing?
Yes! Since ancient times, automation has been in existence. The Egyptians created the wheel thousands years ago. Robots are now used to assist us in assembly lines.
In fact, there are several applications of robotics in manufacturing today. They include:
-
Automation line robots
-
Robot welding
-
Robot painting
-
Robotics inspection
-
Robots that produce products
Automation could also be used to improve manufacturing. 3D printing, for example, allows us to create custom products without waiting for them to be made.
What does manufacturing mean?
Manufacturing Industries are companies that manufacture products. Consumers are people who purchase these goods. To accomplish this goal, these companies employ a range of processes including distribution, sales, management, and production. They manufacture goods from raw materials using machines and other equipment. This includes all types of manufactured goods, including food items, clothing, building supplies, furniture, toys, electronics, tools, machinery, vehicles, pharmaceuticals, medical devices, chemicals, and many others.
What is the role of a logistics manager
Logistics managers make sure all goods are delivered on schedule and without damage. This is accomplished by using the experience and knowledge gained from working with company products. He/she should ensure that sufficient stock is available in order to meet customer demand.
What is production management?
Production Planning refers to the development of a plan for every aspect of production. This document aims to ensure that everything is planned and ready when you are ready to shoot. This document should also include information on how to get the best result on set. This information includes locations, crew details and equipment requirements.
The first step in filming is to define what you want. You may have decided where to shoot or even specific locations you want to use. Once you have identified your locations and scenes it's time to begin figuring out what elements you will need for each one. For example, you might decide that you need a car but don't know exactly what model you want. To narrow your options, you can search online for available models.
After you have chosen the right car, you will be able to begin thinking about accessories. What about additional seating? Maybe you need someone to move around in the back. You may want to change the interior's color from black or white. These questions will help you determine the exact look and feel of your car. The type of shots that you are looking for is another thing to consider. Do you want to film close-ups, or wider angles? Maybe you want the engine or the steering wheels to be shown. These details will help identify the exact car you wish to film.
Once you have all the information, you are ready to create a plan. A schedule will tell you when you need to start shooting and when you need to finish. A schedule for each day will detail when you should arrive at the location and when you need leave. Everyone knows exactly what they should do and when. You can also make sure to book extra staff in advance if you have to hire them. It's not worth paying someone to show up if you haven't told him.
It is important to calculate the amount of filming days when you are creating your schedule. Some projects only take one or two days, while others may last weeks. When you are creating your schedule, you should always keep in mind whether you need more than one shot per day or not. Multiple takes of the same location will lead to higher costs and take more time. If you aren't sure whether you need multiple shots, it is best to take fewer photos than you would like.
Another important aspect of production planning is setting budgets. Setting a realistic budget is essential as it will allow you to work within your means. If you have to reduce your budget due to unexpected circumstances, you can always lower it later. But, don't underestimate how much money you'll spend. If you underestimate how much something costs, you'll have less money to pay for other items.
Production planning is a detailed process. But, once you understand the workings of everything, it becomes easier for future projects to be planned.
Statistics
- [54][55] These are the top 50 countries by the total value of manufacturing output in US dollars for its noted year according to World Bank.[56] (en.wikipedia.org)
- Many factories witnessed a 30% increase in output due to the shift to electric motors. (en.wikipedia.org)
- Job #1 is delivering the ordered product according to specifications: color, size, brand, and quantity. (netsuite.com)
- In the United States, for example, manufacturing makes up 15% of the economic output. (twi-global.com)
- According to a Statista study, U.S. businesses spent $1.63 trillion on logistics in 2019, moving goods from origin to end user through various supply chain network segments. (netsuite.com)
External Links
How To
How to use lean manufacturing in the production of goods
Lean manufacturing is a management style that aims to increase efficiency and reduce waste through continuous improvement. It was first developed in Japan in the 1970s/80s by Taiichi Ahno, who was awarded the Toyota Production System (TPS), award from KanjiToyoda, the founder of TPS. Michael L. Watkins published the first book on lean manufacturing in 1990.
Lean manufacturing is often described as a set if principles that help improve the quality and speed of products and services. It emphasizes the elimination of defects and waste throughout the value stream. Lean manufacturing is called just-in-time (JIT), zero defect, total productive maintenance (TPM), or 5S. Lean manufacturing focuses on eliminating non-value-added activities such as rework, inspection, and waiting.
Lean manufacturing improves product quality and costs. It also helps companies reach their goals quicker and decreases employee turnover. Lean manufacturing can be used to manage all aspects of the value chain. Customers, suppliers, distributors, retailers and employees are all included. Lean manufacturing can be found in many industries. For example, Toyota's philosophy underpins its success in automobiles, electronics, appliances, healthcare, chemical engineering, aerospace, paper, food, etc.
Lean manufacturing includes five basic principles:
-
Define Value- Identify the added value your company brings to society. What makes you stand out from your competitors?
-
Reduce waste - Get rid of any activity that does not add value to the supply chain.
-
Create Flow - Ensure work moves smoothly through the process without interruption.
-
Standardize and simplify – Make processes as repeatable and consistent as possible.
-
Build relationships - Develop and maintain personal relationships with both your internal and external stakeholders.
Lean manufacturing, although not new, has seen renewed interest in the economic sector since 2008. Many businesses have adopted lean production techniques to make them more competitive. Many economists believe lean manufacturing will play a major role in economic recovery.
Lean manufacturing, which has many benefits, is now a standard practice in the automotive industry. These include higher customer satisfaction levels, reduced inventory levels as well as lower operating costs.
The principles of lean manufacturing can be applied in almost any area of an organization. This is because it ensures efficiency and effectiveness in all stages of the value chain.
There are three types principally of lean manufacturing:
-
Just-in Time Manufacturing (JIT), also known as "pull system": This form of lean manufacturing is often referred to simply as "pull". JIT stands for a system where components are assembled on the spot rather than being made in advance. This approach is designed to reduce lead times and increase the availability of components. It also reduces inventory.
-
Zero Defects Manufacturing (ZDM),: ZDM is a system that ensures no defective units are left the manufacturing facility. Repairing a part that is damaged during assembly should be done, not scrapping. This also applies to finished products that need minor repairs before being shipped.
-
Continuous Improvement (CI),: Continuous improvement aims improve the efficiency and effectiveness of operations by continuously identifying issues and making changes to reduce waste. Continuous Improvement (CI) involves continuous improvement in processes, people, tools, and infrastructure.