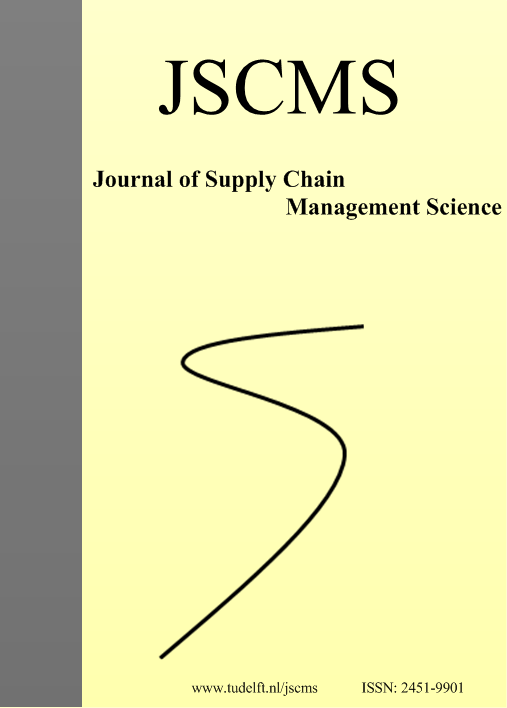
Industrial engineers are responsible for designing and implementing processes that minimize wastefulness and maximize the use of resources. They work in different industries to develop processes that are beneficial for their customers in a variety ways. They look at production schedules, design specifications, as well as workflows to help create more efficient processes. Additionally, industrial engineers help to improve the profitability of production processes. They also aid in improving the quality and quantity of products.
Industrial engineer job requirements
An Industrial Engineer is an essential role in a manufacturing company. He or she uses innovative design systems for efficient operations in the natural and organic food sectors. The Industrial Engineer develops and leads innovative projects that improve the manufacturing process. To qualify for this job, an individual must be qualified and able to perform all essential duties satisfactorily. Industrial engineers must be skilled in AutoCAD and Pro-E.
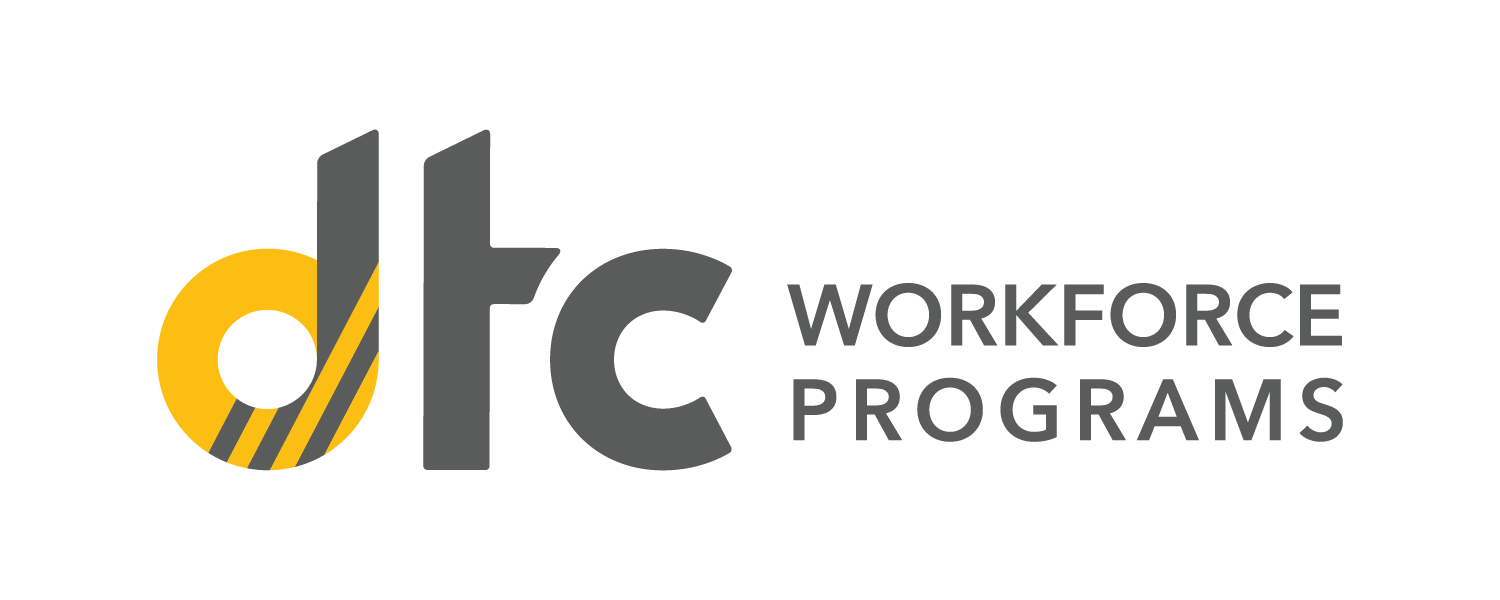
Industrial Engineers work on optimizing efficiency through the design and testing of integrated systems. The job involves not only designing and testing integrated systems, but also studying human factors in order to optimize product quality. Other responsibilities include guest coordination and cost analysis. A person must also have advanced technical skills, such as Microsoft Office. It is necessary to have experience in manufacturing, logistics and systems design. In Orlando, you must have the technical skills necessary to perform your job well.
Industrial engineer salary
You should look at the salaries for Industrial & Manufacturing Engineers here in Orlando, FL if you are considering a career in this field. Orlando is one the best places in America, with an average annual salary of $803,325 This is 6% more than the national median salary and 9% less that the New York, NY median salary. Orlando's average salary is $64,260 to $86,390. The middle 67% make $85,000 per year, while the top ten earn $102,000.
Industrial Engineers can earn salaries ranging from $89,700 to $114,300 USD. Industrial engineers' salaries can vary, as with all careers. The salary figures listed above are based on the average salary for an Industrial Engineer with five to ten years of experience. With more experience, you can expect to make twice as much than those with less. Different industrial engineers may have different pay rates.
Responsibilities of industrial engineer
As a process designer and manager, you will determine the best ways to improve process performance. It is your responsibility to develop and implement flexible, efficient and effective processes that meet customer requirements and goals. The Industrial Engineer may be required to perform many tasks. They could include Cost Analysis, Capacity Planning or Reporting. Capital Project Management is also possible. Discrete event simulation is another example. It is also expected that you will perform time studies, observations, and contribute to cross-functional improvement efforts.
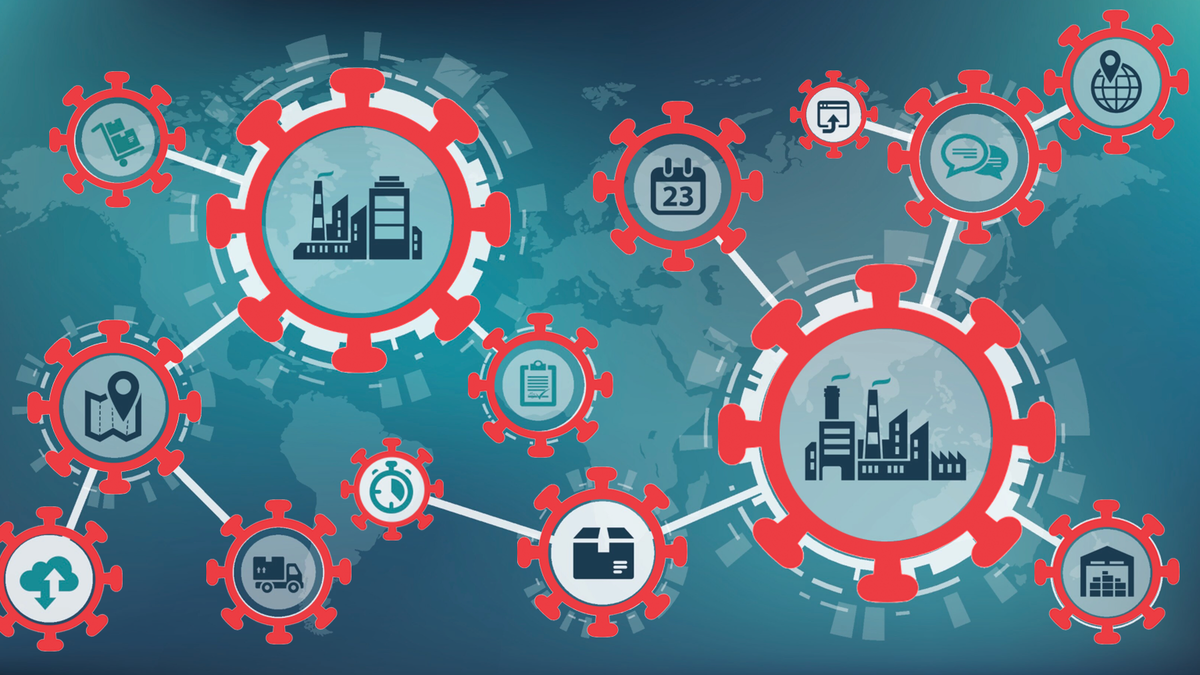
This job requires strong communication skills and engineering experience. Industrial engineers work closely alongside management to develop standards and lead industrial engineering projects that are moderately complex. They will analyze data and generate statistical reports to improve process flow and standard times. They will coordinate and create key metric reports and process documentation.
FAQ
Why is logistics so important in manufacturing?
Logistics is an integral part of every business. They help you achieve great results by helping you manage all aspects of product flow, from raw materials to finished goods.
Logistics play a key role in reducing expenses and increasing efficiency.
How can manufacturing excess production be decreased?
The key to reducing overproduction lies in developing better ways to manage inventory. This would decrease the time that is spent on inefficient activities like purchasing, storing, or maintaining excess stock. We could use these resources to do other productive tasks.
You can do this by adopting a Kanban method. A Kanban board is a visual display used to track work in progress. Kanban systems allow work items to move through different states until they reach their final destination. Each state represents a different priority level.
As an example, if work is progressing from one stage of the process to another, then the current task is complete and can be transferred to the next. A task that is still in the initial stages of a process will be considered complete until it moves on to the next stage.
This allows work to move forward and ensures that no work is missed. A Kanban board allows managers to monitor how much work is being completed at any given moment. This data allows them adjust their workflow based upon real-time data.
Lean manufacturing is another option to control inventory levels. Lean manufacturing emphasizes eliminating waste in all phases of production. Anything that doesn't add value to the product is considered waste. Some common types of waste include:
-
Overproduction
-
Inventory
-
Unnecessary packaging
-
Material surplus
Manufacturers can increase efficiency and decrease costs by implementing these ideas.
What do you mean by warehouse?
Warehouses and storage facilities are where goods are kept before being sold. You can have it indoors or outdoors. It may also be an indoor space or an outdoor area.
What is the responsibility for a logistics manager
A logistics manager makes sure that all goods are delivered on-time and in good condition. This is accomplished by using the experience and knowledge gained from working with company products. He/she should make sure that enough stock is on hand to meet the demands.
Statistics
- It's estimated that 10.8% of the U.S. GDP in 2020 was contributed to manufacturing. (investopedia.com)
- You can multiply the result by 100 to get the total percent of monthly overhead. (investopedia.com)
- [54][55] These are the top 50 countries by the total value of manufacturing output in US dollars for its noted year according to World Bank.[56] (en.wikipedia.org)
- In the United States, for example, manufacturing makes up 15% of the economic output. (twi-global.com)
- According to the United Nations Industrial Development Organization (UNIDO), China is the top manufacturer worldwide by 2019 output, producing 28.7% of the total global manufacturing output, followed by the United States, Japan, Germany, and India.[52][53] (en.wikipedia.org)
External Links
How To
How to Use Just-In-Time Production
Just-in-time is a way to cut costs and increase efficiency in business processes. This is where you have the right resources at the right time. This means that you only pay the amount you actually use. Frederick Taylor developed the concept while working as foreman in early 1900s. He saw how overtime was paid to workers for work that was delayed. He decided that workers would be more productive if they had enough time to complete their work before they started to work.
JIT is an acronym that means you need to plan ahead so you don’t waste your money. The entire project should be looked at from start to finish. You need to ensure you have enough resources to tackle any issues that might arise. You'll be prepared to handle any potential problems if you know in advance. This will prevent you from spending extra money on unnecessary things.
There are different types of JIT methods:
-
Demand-driven: This JIT is where you place regular orders for the parts/materials that are needed for your project. This will allow to track how much material has been used up. You'll also be able to estimate how long it will take to produce more.
-
Inventory-based: This allows you to store the materials necessary for your projects in advance. This allows you predict the amount you can expect to sell.
-
Project-driven: This is an approach where you set aside enough funds to cover the cost of your project. If you know the amount you require, you can buy the materials you need.
-
Resource-based: This is the most common form of JIT. This is where you assign resources based upon demand. If you have many orders, you will assign more people to manage them. If you don’t have many orders you will assign less people to the work.
-
Cost-based : This is similar in concept to resource-based. But here, you aren't concerned about how many people your company has but how much each individual costs.
-
Price-based pricing: This is similar in concept to cost-based but instead you look at how much each worker costs, it looks at the overall company's price.
-
Material-based is an alternative to cost-based. Instead of looking at the total cost in the company, this method focuses on the average amount of raw materials that you consume.
-
Time-based: This is another variation of resource-based JIT. Instead of focusing only on how much each employee is costing, you should focus on how long it takes to complete your project.
-
Quality-based JIT is another variant of resource-based JIT. Instead of thinking about how much each employee costs or how long it takes to manufacture something, you think about how good the quality of your product is.
-
Value-based: This is one of the newest forms of JIT. This is where you don't care about how the products perform or whether they meet customers' expectations. Instead, your goal is to add value to the market.
-
Stock-based: This is an inventory-based method that focuses on the actual number of items being produced at any given time. It is used when production goals are met while inventory is kept to a minimum.
-
Just-in-time planning (JIT): This is a combination JIT and supply-chain management. It is the process of scheduling components' delivery as soon as they have been ordered. It's important as it reduces leadtimes and increases throughput.