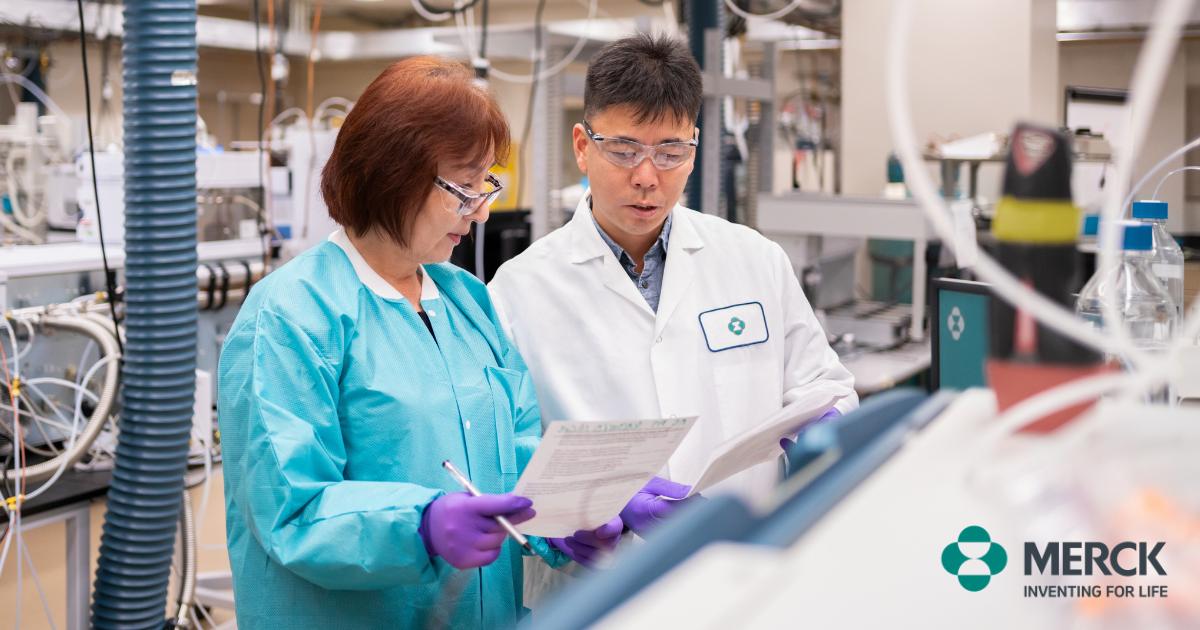
Diverse sources can cause disruptions in supply chains. Natural disasters, product recalls and delays in transportation are just a few examples. These disruptions can cause margin shrinking and price increases. To continue production, some companies may need a change in their sourcing strategies. To prepare for the next disruption, many companies will need a re-evaluate or diversify their supply network.
Diverse industries like transportation, electronics and pharmaceuticals have had to deal with disruptions in supply chains. In some cases the disruption was caused by an internal issue within a company. Other times it was caused by a global problem. One example is a pandemic that caused widespread health disruptions across several countries. It also impacted the retail industry. The pandemic forced governments and other government agencies to take measures to prevent its spread.
A pandemic could affect the workforce, distribution and manufacturing processes of a company. Companies will need to adjust their supply and production chains and reevaluate the impact on production. Depending upon the extent of the disruption, the impact may last for several weeks or even months. Businesses will need a re-evaluation of their inventory in the event of a pandemic. Capital can be reallocated if needed.
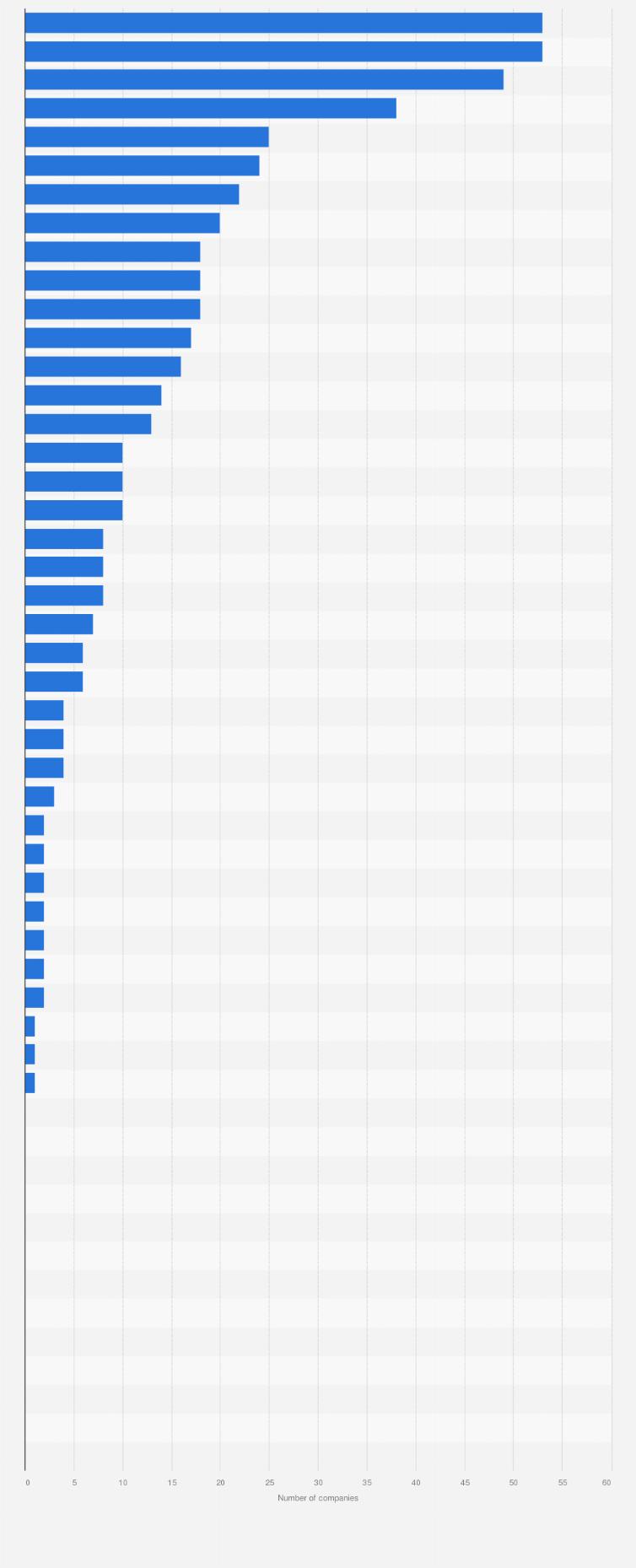
Disruption in any part of the supply chains can occur. In most cases, the supply side will be affected more than that of the demand. If the supply side of an epidemic is disrupted, however, the ripple effect will affect the whole economy.
Supply chain disruptions can have a major impact on a business and are often difficult to predict. Although it is possible to identify seasonal fluctuations, it can be difficult to predict changes in consumer behavior. One of the best ways to mitigate these risks is to rely on a predictive analytics tool to identify potential problems.
A labor shortage is another common reason for supply chain disruption. Companies can lose productivity if they are unable to get parts or equipment from reliable suppliers. Machine failures can also cause chaos in an operation.
Natural disasters, market fluctuations, geopolitical stability, and other factors are all common causes of supply-chain disruptions. Natural disasters can be very costly and disrupt the global supply chains. Supply chain disruption can also be caused by a power cut, telecommunications blackouts, and even border closures. To protect their business, some companies might be forced to store large quantities.
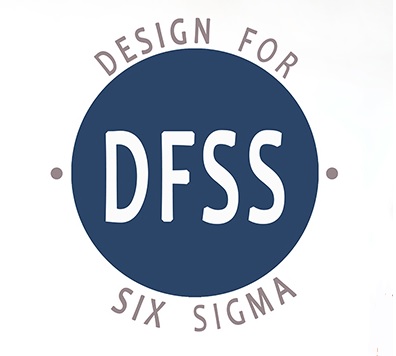
The impact of disruptions in supply chains is generally low. Companies will need take action if they spot a disruption. The majority of companies will need to do so within a reasonable timeframe. It's important to recognize problems early in order to avoid conflict.
Ernest & Young LLP surveyed 72% of respondents to a survey and found that 79% had experienced disruptions at some time. 57% reported negative effects. Some of these issues can easily be solved quickly, while others require a more strategic approach.
FAQ
How can manufacturing avoid production bottlenecks
To avoid production bottlenecks, ensure that all processes run smoothly from the moment you receive your order to the time the product ships.
This includes planning for capacity requirements as well as quality control measures.
This can be done by using continuous improvement techniques, such as Six Sigma.
Six Sigma is a management method that helps to improve quality and reduce waste.
It emphasizes consistency and eliminating variance in your work.
What are the responsibilities of a logistic manager?
A logistics manager ensures that all goods are delivered on time and without damage. This is done using his/her knowledge of the company's products. He/she also needs to ensure adequate stock to meet demand.
How can manufacturing excess production be decreased?
The key to reducing overproduction lies in developing better ways to manage inventory. This would reduce the time needed to manage inventory. This could help us free up our time for other productive tasks.
You can do this by adopting a Kanban method. A Kanban board, a visual display to show the progress of work, is called a Kanban board. Kanban systems allow work items to move through different states until they reach their final destination. Each state represents a different priority.
When work is completed, it can be transferred to the next stage. But if a task remains in the beginning stages it will stay that way until it reaches its end.
This keeps work moving and ensures no work is lost. Managers can monitor the work being done by Kanban boards to see what is happening at any given time. This allows them to adjust their workflows based on real-time information.
Lean manufacturing is another way to manage inventory levels. Lean manufacturing emphasizes eliminating waste in all phases of production. Any product that isn't adding value can be considered waste. Here are some examples of common types.
-
Overproduction
-
Inventory
-
Unnecessary packaging
-
Material surplus
These ideas can help manufacturers improve efficiency and reduce costs.
Statistics
- (2:04) MTO is a production technique wherein products are customized according to customer specifications, and production only starts after an order is received. (oracle.com)
- According to a Statista study, U.S. businesses spent $1.63 trillion on logistics in 2019, moving goods from origin to end user through various supply chain network segments. (netsuite.com)
- [54][55] These are the top 50 countries by the total value of manufacturing output in US dollars for its noted year according to World Bank.[56] (en.wikipedia.org)
- You can multiply the result by 100 to get the total percent of monthly overhead. (investopedia.com)
- In the United States, for example, manufacturing makes up 15% of the economic output. (twi-global.com)
External Links
How To
How to use the Just In-Time Production Method
Just-in-time is a way to cut costs and increase efficiency in business processes. It allows you to get the right amount resources at the right time. This means that you only pay the amount you actually use. Frederick Taylor first coined this term while working in the early 1900s as a foreman. Taylor observed that overtime was paid to workers if they were late in working. He realized that workers should have enough time to complete their jobs before they begin work. This would help increase productivity.
JIT is about planning ahead. You should have all the necessary resources ready to go so that you don’t waste money. The entire project should be looked at from start to finish. You need to ensure you have enough resources to tackle any issues that might arise. You will have the resources and people to solve any problems you anticipate. This will prevent you from spending extra money on unnecessary things.
There are many JIT methods.
-
Demand-driven JIT: You order the parts and materials you need for your project every other day. This will allow you to track how much material you have left over after using it. You'll also be able to estimate how long it will take to produce more.
-
Inventory-based: This allows you to store the materials necessary for your projects in advance. This allows you to predict how much you can expect to sell.
-
Project-driven: This means that you have enough money to pay for your project. Once you have an idea of how much material you will need, you can purchase the necessary materials.
-
Resource-based JIT is the most widespread form. This is where you assign resources based upon demand. For example, if there is a lot of work coming in, you will have more people assigned to them. If you don't receive many orders, then you'll assign fewer employees to handle the load.
-
Cost-based : This is similar in concept to resource-based. But here, you aren't concerned about how many people your company has but how much each individual costs.
-
Price-based: This is very similar to cost-based, except that instead of looking at how much each individual worker costs, you look at the overall price of the company.
-
Material-based: This approach is similar to cost-based. However, instead of looking at the total cost for the company, you look at how much you spend on average on raw materials.
-
Time-based JIT: This is another variant of resource-based JIT. Instead of focusing on how much each employee costs, you focus on how long it takes to complete the project.
-
Quality-based: This is yet another variation of resource-based JIT. Instead of focusing on the cost of each worker or how long it takes, think about how high quality your product is.
-
Value-based JIT : This is the newest type of JIT. In this case, you're not concerned with how well the products perform or whether they meet customer expectations. Instead, your goal is to add value to the market.
-
Stock-based. This method is inventory-based and focuses only on the actual production at any given point. It's used when you want to maximize production while minimizing inventory.
-
Just-in time (JIT), planning: This is a combination JIT/supply chain management. It refers to the process of scheduling the delivery of components as soon as they are ordered. It's important because it reduces lead times and increases throughput.