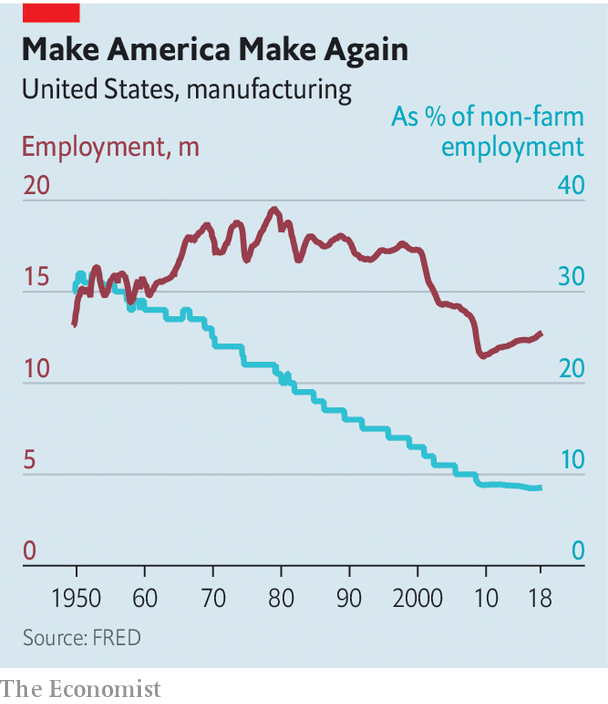
Advanced manufacturing refers specifically to the use innovative technology to improve processes and products. This technology can be classified as either "advanced", "innovative," and "cutting-edge". This is because advanced manufacturing has become more common in the manufacturing industry. Here are some examples for advanced manufacturing. These are the most popular technologies in advanced manufacturing.
Continuous manufacturing
Continuous manufacturing dates back to the early 1700s, when it was first used to produce pig iron using blast furnaces. The concept has since spread across various industries, including the automotive, food, oil and refining, chemicals, and pulp and paper industries. Continuous manufacturing is now gaining significant traction in biopharmaceutical, drawing the attention and support of CMOs as well as big pharma players.
Recent commentary by the FDA and its partner organizations discussed the benefits that continuous manufacturing can bring to the production of therapeutic protein. This legislation would establish national centers to help companies develop standards and advance the field. It is designed to assist the medical industry in improving the process of creating and utilizing medical products. Further, it would also encourage companies to use continuous manufacturing to develop and improve products. It is important to make sure that continuous manufacturing is safe.
Automated processes
Automating advanced manufacturing processes is a great way to increase efficiency and reduce costs. Automating processes in advanced manufacturing is the best way to maximize production efficiency and make the most of your floor space. Manufacturing companies can increase productivity and reduce costs by collecting data and using automation technologies. Automating the process industry saves time as well as money. The initial investment is not cheap, but it will ultimately increase the bottom line for a manufacturing company.
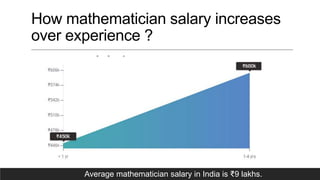
Companies are now combining automated manufacturing processes with advanced manufacturing processes. Audi is one example. They use automated welding and bonding processes to reduce their production time while also saving energy and weight. They also utilize advanced manufacturing systems such as regenerative braking in conveyor systems. 3D printing, which is a major advancement in manufacturing, has only recently been adopted by mainstream companies. What is it that makes 3D printing so appealing?
Internet of Things (IoT).
The IIoT revolution transforms manufacturing by using sensors to monitor machines as well as their processes. These sensors gather data from different parts of the manufacturing process and feed this data into a central base station. This data is then processed and analyzed, which can be used to improve processes and eliminate waste. Advanced manufacturers already utilize IIoT sensors to monitor their processes and optimize production. The IIoT is an industrial version of key fobs.
IIoT deployment requires a comprehensive roadmap and development capabilities to roll out use cases in an effective and scalable manner. The following road map from an automaker shows three waves of deployment:
Cost-effectiveness
Advanced manufacturing is not always cheaper than traditional production. Instead, traditional cost-benefit analyses are not enough to determine economic benefits. A holistic model that includes both the costs and benefits of technology is possible to help identify new benefits and speed up decision-making. Munker, Schroer, and Munker present a cost-benefit calculator that addresses key issues related to AMS implementation.
Information technology advances are changing rapidly the face of manufacturing, as well as their costs. As production systems become more networked and smart, they are also becoming more efficient. Cost pressures are increasing the focus on productivity and the ability of companies to respond to customers' needs. Rapid adoption of advanced manufacturing technology will likely speed up the implementation of these technologies as well as their cost-effectiveness. As the industry continues digitizing, it is likely that such technologies will be adopted more quickly.
Human error reduction
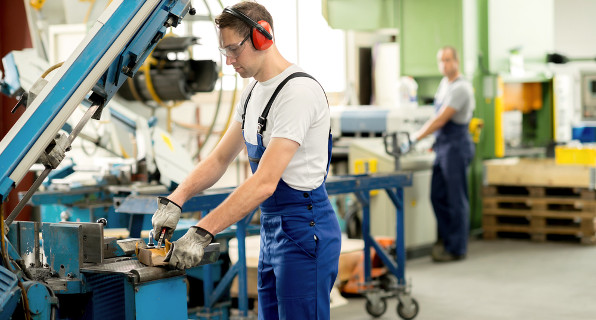
Although human beings can make mistakes sometimes, the production process is often designed to protect them. Human error can occur when employees fail to follow the written process or misunderstand instructions. For example, pharmaceutical laboratories must follow specific procedures when making drugs. Some employees believe they are familiar with a process and know how to use the correct ingredients. They then proceed to make the compound without consulting the written instructions.
Effective communication between senior and junior employees is another way to reduce human error. Employees who are treated unfairly are more likely to make mistakes. Managers should not punish employees for asking questions. Employees need to feel comfortable asking questions, and if they feel uncomfortable with the way they are treated, they will not be likely to take corrective actions. It is important to establish a healthy relationship between senior and junior employees. Also, it is important to address communication issues in a polite and professional manner.
FAQ
Why is logistics important for manufacturing?
Logistics are an essential part of any business. They help you achieve great results by helping you manage all aspects of product flow, from raw materials to finished goods.
Logistics play an important role in reducing costs as well as increasing efficiency.
What are the jobs in logistics?
There are different kinds of jobs available in logistics. These are some of the jobs available in logistics:
-
Warehouse workers - They load trucks and pallets.
-
Transportation drivers – These drivers drive trucks and wagons to transport goods and pick up the goods.
-
Freight handlers: They sort and package freight in warehouses.
-
Inventory managers – These people oversee inventory at warehouses.
-
Sales representatives - They sell products.
-
Logistics coordinators are responsible for organizing and planning logistics operations.
-
Purchasing agents - They buy goods and services that are necessary for company operations.
-
Customer service representatives – They answer emails and phone calls from customers.
-
Ship clerks - They issue bills and process shipping orders.
-
Order fillers - They fill orders based on what is ordered and shipped.
-
Quality control inspectors - They check incoming and outgoing products for defects.
-
Others - There is a variety of other jobs in logistics. These include transportation supervisors and cargo specialists.
What are the four types in manufacturing?
Manufacturing refers the process of turning raw materials into useful products with machines and processes. It includes many different activities like designing, building and testing, packaging, shipping and selling, as well as servicing.
How does a Production Planner differ from a Project Manager?
The primary difference between a producer planner and a manager of a project is that the manager usually plans and organizes the whole project, while a production planner is only involved in the planning stage.
Statistics
- You can multiply the result by 100 to get the total percent of monthly overhead. (investopedia.com)
- According to a Statista study, U.S. businesses spent $1.63 trillion on logistics in 2019, moving goods from origin to end user through various supply chain network segments. (netsuite.com)
- Job #1 is delivering the ordered product according to specifications: color, size, brand, and quantity. (netsuite.com)
- In 2021, an estimated 12.1 million Americans work in the manufacturing sector.6 (investopedia.com)
- According to the United Nations Industrial Development Organization (UNIDO), China is the top manufacturer worldwide by 2019 output, producing 28.7% of the total global manufacturing output, followed by the United States, Japan, Germany, and India.[52][53] (en.wikipedia.org)
External Links
How To
How to Use the 5S to Increase Productivity In Manufacturing
5S stands for "Sort", 'Set In Order", 'Standardize', & Separate>. Toyota Motor Corporation developed the 5S method in 1954. It improves the work environment and helps companies to achieve greater efficiency.
The basic idea behind this method is to standardize production processes, so they become repeatable, measurable, and predictable. Cleaning, sorting and packing are all done daily. These actions allow workers to perform their job more efficiently, knowing what to expect.
There are five steps that you need to follow in order to implement 5S. Each step has a different action and leads to higher efficiency. You can make it easy for people to find things later by sorting them. You arrange items by placing them in an order. Then, after you separate your inventory into groups, you store those groups in containers that are easy to access. Finally, label all containers correctly.
This requires employees to critically evaluate how they work. Employees need to be able understand their motivations and discover alternative ways to do them. They must learn new skills and techniques in order to implement the 5S system.
The 5S method increases efficiency and morale among employees. Once they start to notice improvements, they are motivated to keep working towards their goal of increasing efficiency.