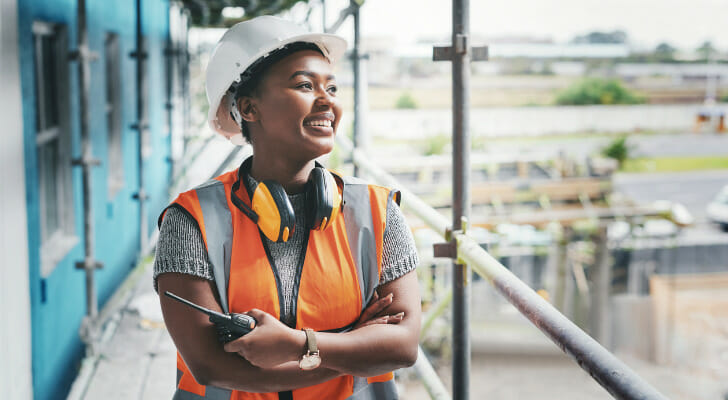
Until recently, "Made in Japan" meant low-quality consumer goods. Japanese products are known for their reliability, precision and durability. Japanese manufacturers are also setting higher standards. This has increased cost pressure and created more competition. Japanese firms are also questioning how quickly they can adapt in changing market conditions.
Japanese factories have a high level of process control. They ensure that the work content, labour, and relationships are all controlled. This is possible by training their employees to make high-quality products. They also encourage feedback from their customers, quality inspectors, and vendors.
Japan's manufacturing tradition is rooted in Japan's culture of discipline and cultural conformity. Modern technology has also influenced it. Artificial intelligence is used by some Japanese companies to enhance their non-manufacturing workforce. Next-generation technology will further enhance non-manufacturing labour. This includes robots that will work in factories, nursing homes, hospitals, temples, and even schools.
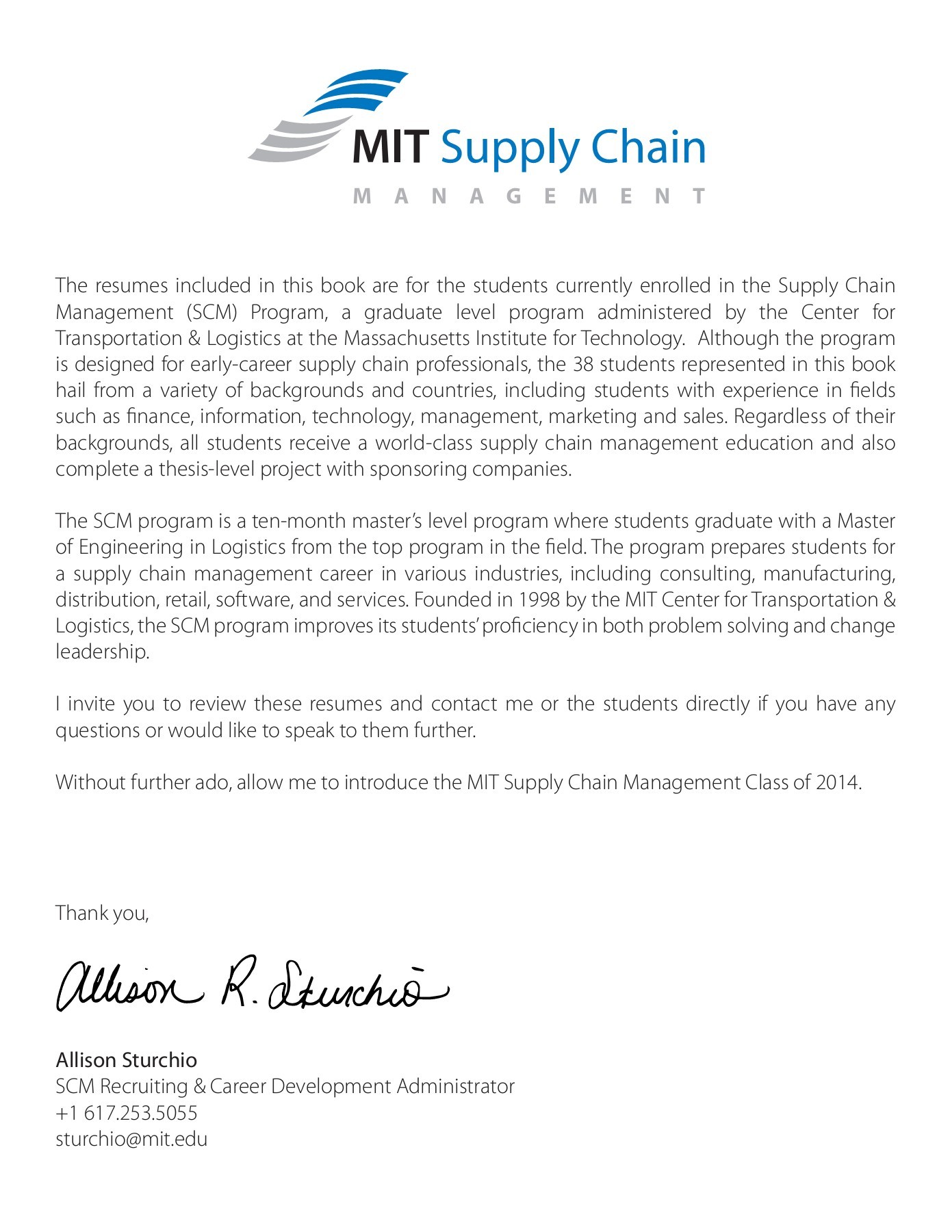
There have been numerous safety issues. One was a 13-year old girl who died from complications from a factory illness. Another concern a company who admitted to infringing vehicle inspection procedures. These scandals have put the Japanese factory floor under scrutiny. The work environment has also been affected by several strikes of workers. To address these problems, government officials have enacted new regulations like closed loop management. This allows workers to be isolated to prevent the spread of viruses.
Another important factor affecting Japan's manufacturing industry is the aging population. The Japanese birth rate is decreasing, which means there is a shortage of labor. But, this is not possible because there aren't enough workers. Japanese manufacturing requires foreign workers to grow. Many factories have difficulty sourcing supplies. This is causing problems in their supply chain.
Japanese manufacturers have a reputation for working closely with suppliers to resolve problems. Japanese companies sometimes hold seminars for their suppliers to teach them how they can better meet customer demands. To ensure that incoming parts meet specifications, they also screen them. Advanced technology such as automatic checkers is also used to detect defects before they occur.
Their products show the best of Japanese production. Japanese automobiles, for example, are known for their fuel economy, durability, and excellent quality. The Japanese auto industry is also one the largest in world. Japan currently houses six of top ten auto manufacturers including Toyota, Honda, Suzuki. They also produce cars with more features for a less expensive price.
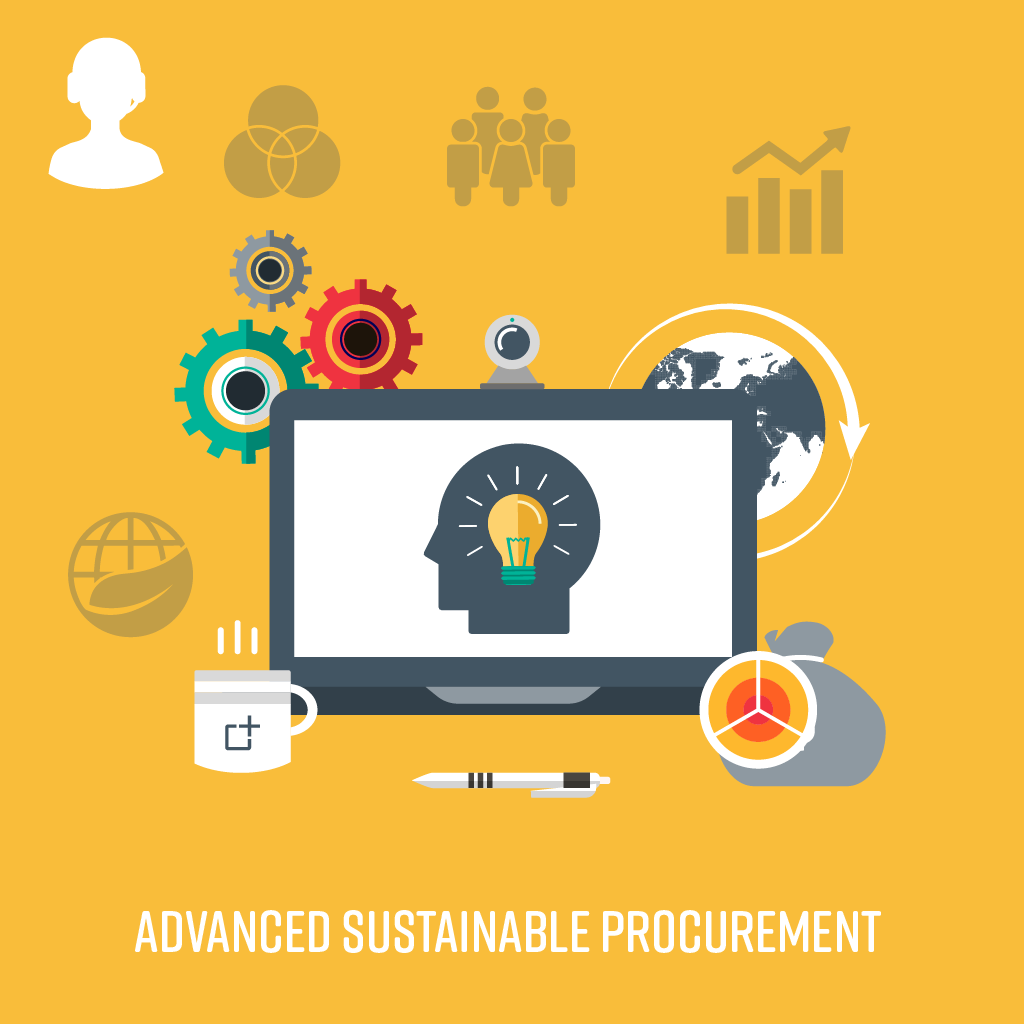
The industry will also be impacted by the next wave of technology, especially in terms wages. Robots are already replacing field workers in service organizations. These workers report directly on to the sales or manufacturing managers. The future of automated manufacturing will be more than just Japanese factories. Robots will also work in train stations, hospitals, and other public places.
Japan faces many problems with its supply chains. This has led to a slowdown in exports as well as clogging of the port. Other problems include the proliferation of non-regular workers, which have lowered standards and shaved off costs.
FAQ
Is automation necessary in manufacturing?
Not only are service providers and manufacturers important, but so is automation. It allows them to offer services faster and more efficiently. In addition, it helps them reduce costs by reducing human errors and improving productivity.
Can some manufacturing processes be automated?
Yes! Yes. Automation has been around since ancient time. The Egyptians invent the wheel thousands of year ago. To help us build assembly lines, we now have robots.
Actually, robotics can be used in manufacturing for many purposes. These include:
-
Robots for assembly line
-
Robot welding
-
Robot painting
-
Robotics inspection
-
Robots that create products
Automation could also be used to improve manufacturing. 3D printing makes it possible to produce custom products in a matter of days or weeks.
How does manufacturing avoid bottlenecks in production?
You can avoid bottlenecks in production by making sure that everything runs smoothly throughout the production cycle, from the moment you receive an order to the moment the product is shipped.
This includes planning for both capacity requirements and quality control measures.
Continuous improvement techniques like Six Sigma are the best way to achieve this.
Six Sigma management is a system that improves quality and reduces waste within your organization.
It's all about eliminating variation and creating consistency in work.
What are the products and services of logistics?
Logistics is the process of moving goods from one point to another.
These include all aspects related to transport such as packaging, loading and transporting, storing, transporting, unloading and warehousing inventory management, customer service. Distribution, returns, recycling are some of the options.
Logisticians ensure that the product is delivered to the correct place, at the right time, and under safe conditions. They help companies manage their supply chain efficiency by providing information on demand forecasts, stock levels, production schedules, and availability of raw materials.
They also keep track of shipments in transit, monitor quality standards, perform inventories and order replenishment, coordinate with suppliers and vendors, and provide support services for sales and marketing.
Statistics
- According to a Statista study, U.S. businesses spent $1.63 trillion on logistics in 2019, moving goods from origin to end user through various supply chain network segments. (netsuite.com)
- In 2021, an estimated 12.1 million Americans work in the manufacturing sector.6 (investopedia.com)
- (2:04) MTO is a production technique wherein products are customized according to customer specifications, and production only starts after an order is received. (oracle.com)
- In the United States, for example, manufacturing makes up 15% of the economic output. (twi-global.com)
- It's estimated that 10.8% of the U.S. GDP in 2020 was contributed to manufacturing. (investopedia.com)
External Links
How To
How to Use Just-In-Time Production
Just-intime (JIT), a method used to lower costs and improve efficiency in business processes, is called just-in-time. It allows you to get the right amount resources at the right time. This means that you only pay the amount you actually use. Frederick Taylor developed the concept while working as foreman in early 1900s. Taylor observed that overtime was paid to workers if they were late in working. He realized that workers should have enough time to complete their jobs before they begin work. This would help increase productivity.
The idea behind JIT is that you should plan ahead and have everything ready so you don't waste money. The entire project should be looked at from start to finish. You need to ensure you have enough resources to tackle any issues that might arise. You will have the resources and people to solve any problems you anticipate. This will ensure that you don't spend more money on things that aren't necessary.
There are many JIT methods.
-
Demand-driven: This JIT is where you place regular orders for the parts/materials that are needed for your project. This will allow you to track how much material you have left over after using it. It will also allow you to predict how long it takes to produce more.
-
Inventory-based : You can stock the materials you need in advance. This allows for you to anticipate how much you can sell.
-
Project-driven : This is a method where you make sure that enough money is set aside to pay the project's cost. Knowing how much money you have available will help you purchase the correct amount of materials.
-
Resource-based JIT: This type of JIT is most commonly used. Here, you allocate certain resources based on demand. If you have many orders, you will assign more people to manage them. If you don't have many orders, you'll assign fewer people to handle the workload.
-
Cost-based: This is similar to resource-based, except that here you're not just concerned about how many people you have but how much each person costs.
-
Price-based: This approach is very similar to the cost-based method except that you don't look at individual workers costs but the total cost of the company.
-
Material-based - This is a variant of cost-based. But instead of looking at the total company cost, you focus on how much raw material you spend per year.
-
Time-based JIT: A variation on resource-based JIT. Instead of focusing on the cost of each employee, you will focus on the time it takes to complete a project.
-
Quality-based JIT: Another variation on resource-based JIT. Instead of thinking about the cost of each employee or the time it takes to produce something, you focus on how good your product quality.
-
Value-based: This is one of the newest forms of JIT. You don't worry about whether the products work or if they meet customer expectations. Instead, your goal is to add value to the market.
-
Stock-based: This inventory-based approach focuses on how many items are being produced at any one time. It's useful when you want maximum production and minimal inventory.
-
Just-intime planning (JIT), is a combination JIT/sales chain management. It is the process that schedules the delivery of components within a short time of their order. It's important as it reduces leadtimes and increases throughput.