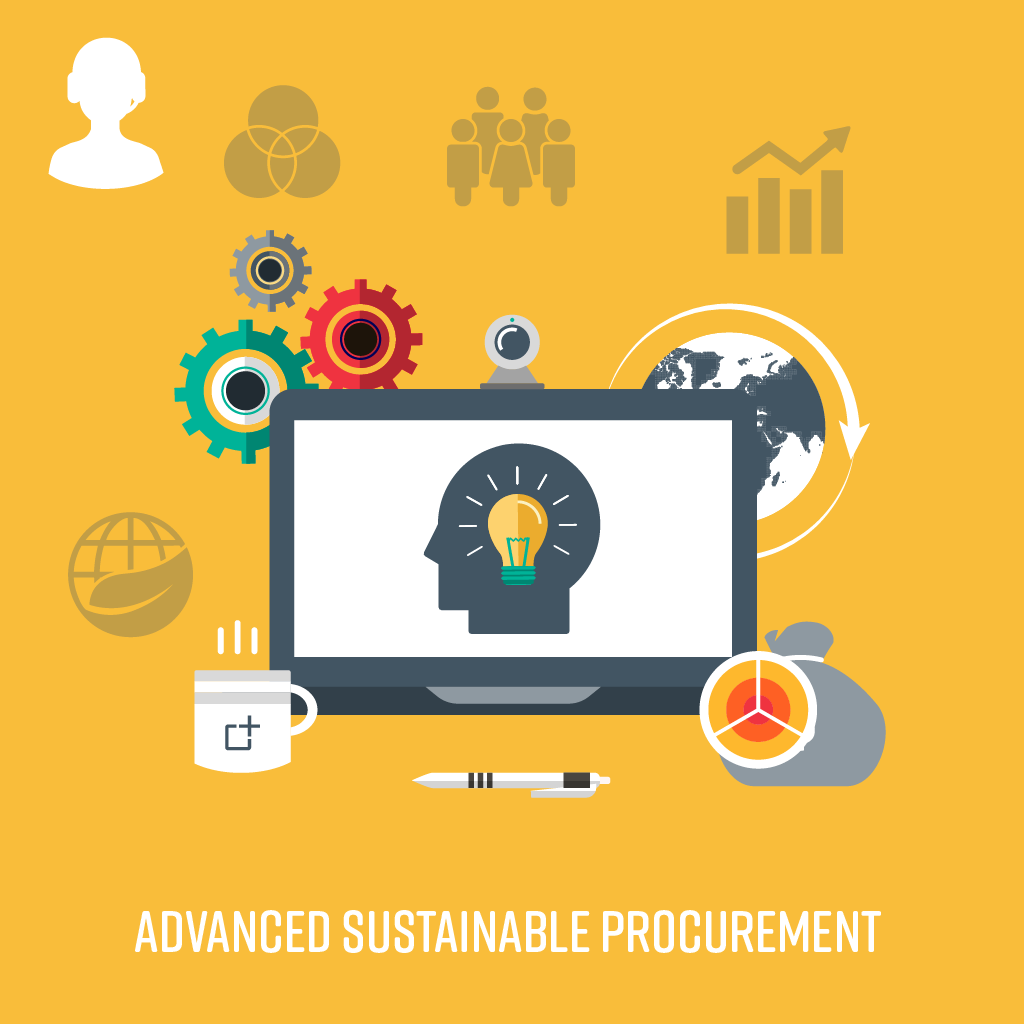
Manufacturing Phoenix in Arizona is a company that offers a range products to the federal Government. It also provides similar products for commercial and individual clients. All production can be done in one location, with all resources located within a few feet of each others. Since its inception, the company offers opportunities for persons with disabilities. It employs approximately 70 people in its manufacturing segment.
Honeywell Aerospace
Honeywell Aerospace, a Phoenix-based aerospace company, develops innovative transportation options. The company's products improve flight safety and fuel efficiency as well as improving runway traffic. Its products can be found in nearly all commercial airliner. Honeywell Aerospace is also responsible for the technology used in 2001: A Space Odyssey. Honeywell Aerospace also makes systems for International Space Station.
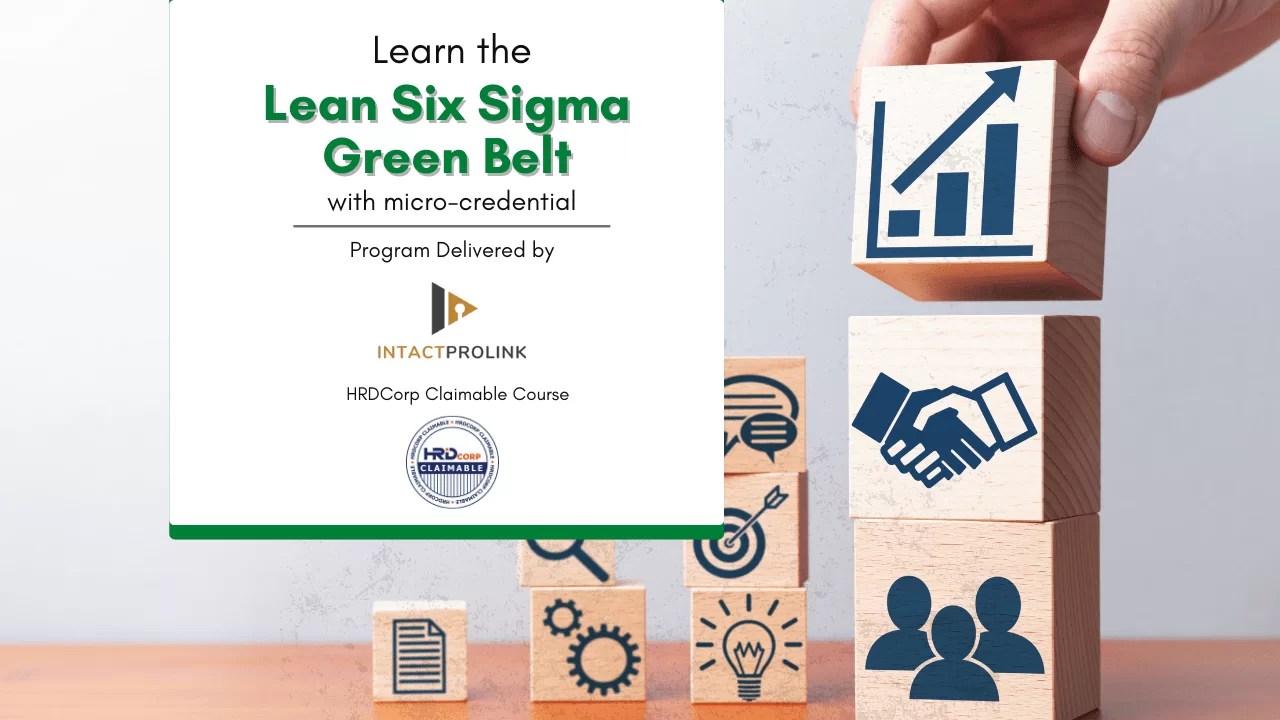
In 2016, Honeywell opened a Phoenix reactive metal alloy manufacturing plant. This facility converted an old flame spray facility to support production of parts made of titanium and aluminium alloys. Honeywell intends to start producing Inconel 718 parts in this facility by 2017. The facility is home to more than $25 million of investment by Honeywell.
Raytheon Technologies Corp.
Raytheon Technologies Corp. is an international aerospace and defense conglomerate headquartered in Arlington, Virginia. This company is one of largest producers of military equipment around the globe. Its products include aircraft, rockets, missiles, and more. Raytheon is an aerospace and defense company that is also a market leader.
Raytheon has a long history in the defense and aerospace sectors. The company's aerial navigation systems division, for example, accounts for 27.4% of the company's net sales. It also makes mechanical and electric systems for airplanes.
Benchmark Electronics
Benchmark Electronics has its headquarters in Tempe, Arizona. It is a contract electronic manufacturing company. With over 13,000 employees, the Phoenix-based ODM is one of the most important in the world. The company operates offices in Tempe Marketplace, Scottsdale, as well as Tempe Marketplace. Gayla Delly was recently promoted to CEO.
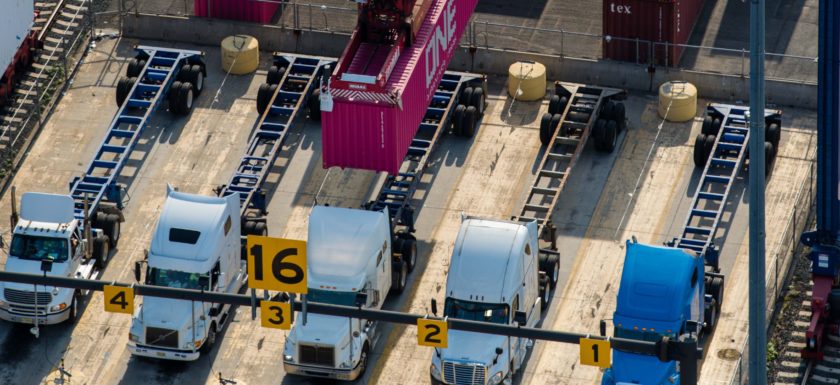
Vertically integrated engineering and manufacturing services are offered by the Phoenix manufacturing facility. Its capabilities include microwave and RF components, embedded electronics design, and high-frequency circuits. The company also offers aftermarket solutions. It has a broad range of customers in the commercial, industrial and defense markets.
FAQ
What is production planning?
Production Planning refers to the development of a plan for every aspect of production. This document will ensure everything is in order and ready to go when you need it. It should also contain information on achieving the best results on set. It should include information about shooting locations, casting lists, crew details, equipment requirements, and shooting schedules.
The first step is to outline what you want to film. You might have an idea of where you want to film, or you may have specific locations or sets in mind. Once you have identified your locations and scenes it's time to begin figuring out what elements you will need for each one. You might decide you need a car, but not sure what make or model. To narrow your options, you can search online for available models.
After you have selected the car you want, you can begin to think about additional features. Do you have people who need to be seated in the front seat? Or perhaps you need someone walking around the back of the car? You may want to change the interior's color from black or white. These questions will help guide you in determining the ideal look and feel for your car. Another thing you can do is think about what type of shots are desired. Are you going to be shooting close-ups? Or wide angles? Maybe you want to show your engine or the steering wheel. These things will help you to identify the car that you are looking for.
Once you have made all the necessary decisions, you can start to create a schedule. You can use a schedule to determine when and where you need it to be shot. You will need to know when you have to be there, what time you have to leave and when your return home. This way, everyone knows what they need to do and when. Hire extra staff by booking them ahead of time. It is not worth hiring someone who won’t show up because you didn’t tell him.
Your schedule will also have to be adjusted to reflect the number of days required to film. Some projects only take one or two days, while others may last weeks. When you are creating your schedule, you should always keep in mind whether you need more than one shot per day or not. Multiple takes at the same place will result in higher costs and longer completion times. You can't be certain if you will need multiple takes so it is better not to shoot too many.
Another important aspect of production planning is setting budgets. A realistic budget will help you work within your means. You can always lower the budget if you encounter unexpected problems. It is important to not overestimate how much you will spend. You will end up spending less money if you underestimate the cost of something.
Production planning is a complicated process. But once you understand how everything works together, it becomes much easier to plan future project.
What is manufacturing and logistics?
Manufacturing is the production of goods using raw materials. Logistics manages all aspects of the supply chain, including procurement, production planning and distribution, inventory control, transportation, customer service, and transport. Manufacturing and logistics are often considered together as a broader term that encompasses both the process of creating products and delivering them to customers.
What is the difference between a production planner and a project manager?
The primary difference between a producer planner and a manager of a project is that the manager usually plans and organizes the whole project, while a production planner is only involved in the planning stage.
How can manufacturing efficiency be improved?
First, determine which factors have the greatest impact on production time. We must then find ways that we can improve these factors. If you don't know where to start, then think about which factor(s) have the biggest impact on production time. Once you've identified them all, find solutions to each one.
Statistics
- Job #1 is delivering the ordered product according to specifications: color, size, brand, and quantity. (netsuite.com)
- According to the United Nations Industrial Development Organization (UNIDO), China is the top manufacturer worldwide by 2019 output, producing 28.7% of the total global manufacturing output, followed by the United States, Japan, Germany, and India.[52][53] (en.wikipedia.org)
- It's estimated that 10.8% of the U.S. GDP in 2020 was contributed to manufacturing. (investopedia.com)
- (2:04) MTO is a production technique wherein products are customized according to customer specifications, and production only starts after an order is received. (oracle.com)
- According to a Statista study, U.S. businesses spent $1.63 trillion on logistics in 2019, moving goods from origin to end user through various supply chain network segments. (netsuite.com)
External Links
How To
How to Use Six Sigma in Manufacturing
Six Sigma is "the application statistical process control (SPC), techniques for continuous improvement." Motorola's Quality Improvement Department created Six Sigma at their Tokyo plant, Japan in 1986. The basic idea behind Six Sigma is to improve quality by improving processes through standardization and eliminating defects. In recent years, many companies have adopted this method because they believe there is no such thing as perfect products or services. Six Sigma aims to reduce variation in the production's mean value. It is possible to measure the performance of your product against an average and find the percentage of time that it differs from the norm. If it is too large, it means that there are problems.
Understanding the dynamics of variability within your business is the first step in Six Sigma. Once you have this understanding, you will need to identify sources and causes of variation. You'll also want to determine whether these variations are random or systematic. Random variations occur when people make mistakes; systematic ones are caused by factors outside the process itself. Random variations would include, for example, the failure of some widgets to fall from the assembly line. It would be considered a systematic problem if every widget that you build falls apart at the same location each time.
Once you identify the problem areas, it is time to create solutions. That solution might involve changing the way you do things or redesigning the process altogether. Once you have implemented the changes, it is important to test them again to ensure they work. If they fail, you can go back to the drawing board to come up with a different plan.