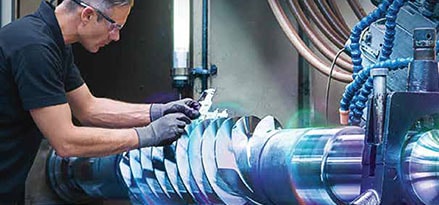
For your company to be able to attract the best and most sought-after talent at the right price and time, it is important that you have a strong talent supply chain. It is also key to achieving competitive advantage in the global market.
It is not an easy task to create a strong talent supply network. It requires constant monitoring of the talent pool and assessment. It requires collaboration from several groups, including operations, IT and HR leaders. To ensure that the talent supply chains are aligned with the company's goals and objectives, it is essential to have a common business strategy.
Diversity is a key challenge for HR leaders. To attract and retain top talent, companies need to review their HR processes. This is possible by adopting new technologies. Modern technology can make it easier to find talent and reduce the time involved in recruitment. Your organization can identify and optimize talent using data. This will also help identify common skills within your supply chain.
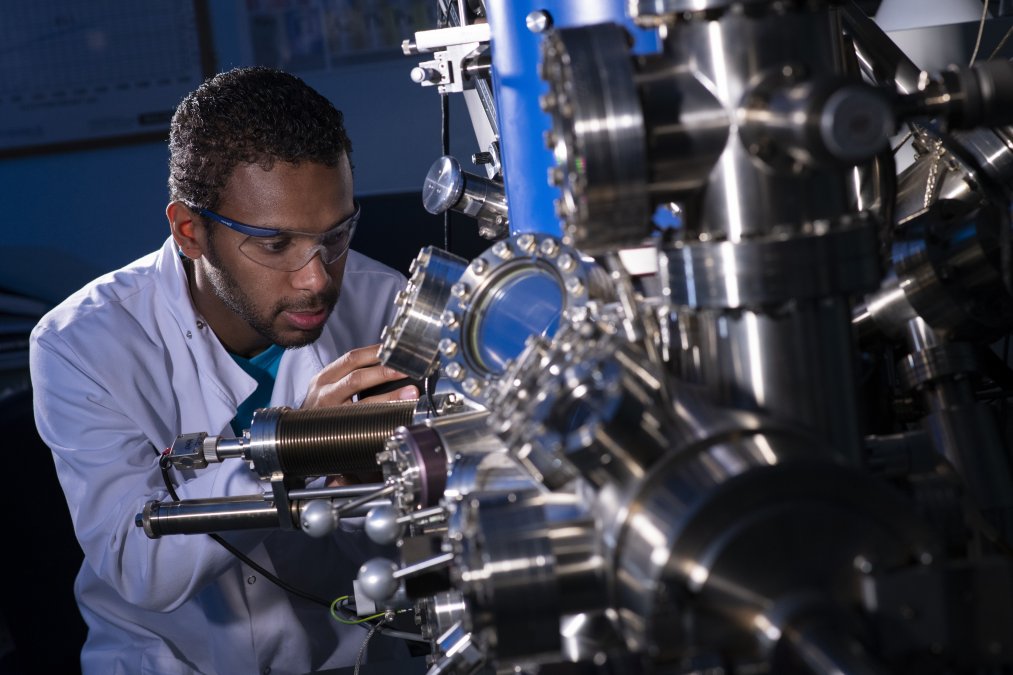
Identifying talent is the first step. Once you have identified your talent pools, you can use the data you have to evaluate your needs. Once you have identified your talent pool, you can use that data to assess where you need to go and how you should be recruiting. You can also upskill your employees to round out your talent pipeline.
Your organization may be able to track changes in political trends and market forecasts by making use of existing data. These data can provide insight and help you to identify talent strategies that align with your business goals. To maintain candidate profiles, you can also use existing data.
A talent supply chain is a way for your company to improve the quality of its workforce and increase its retention. Ultimately, it can also help you streamline your operations. You can cut down on the time and expense required to hire talent while maintaining a stable and productive workforce.
A talent supply channel can be used to address both short-term and long-term demands, such IT projects or recruiting and retaining staff. You can also make use of a talent supply network to aid regions with limited job opportunities. A global talent supply network can offer a greater pool of diverse candidates and cut down on the time required for talent retention and hiring.
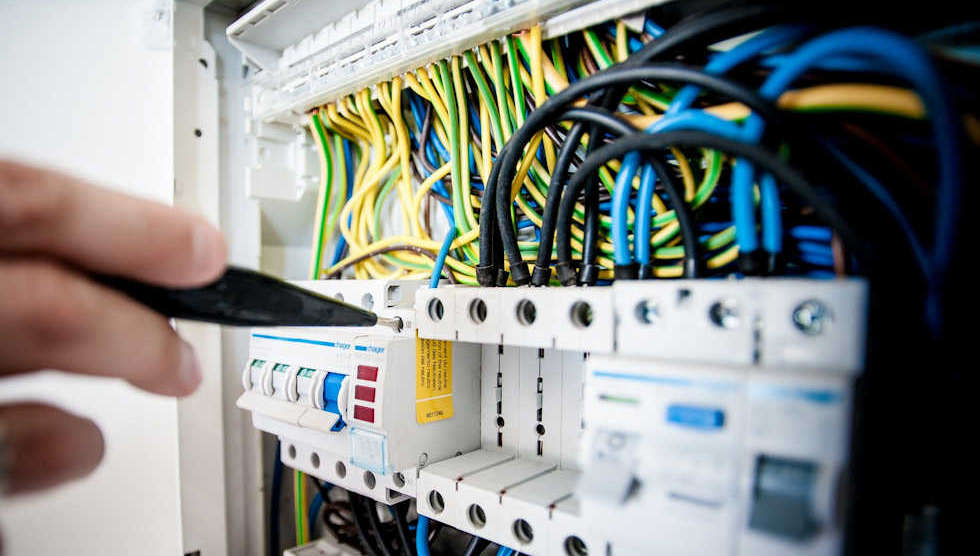
Historically, HR has worked separately to attract talent. Today's companies need to compete in the global market and have access the most in-demand talent from all parts of their workforce. To ensure that the talent supply chain meets the company's goals, it is important to identify the talents and skills required by the company.
Companies face new challenges as technology advances. These changes mean that companies must reassess their talent requirements, develop new skill sets and become more agile. This new talent acquisition strategy is an important part of the future of many companies.
FAQ
What skills is required for a production planner?
You must be flexible and organized to become a productive production planner. Also, you must be able and willing to communicate with clients and coworkers.
How can manufacturing avoid production bottlenecks
To avoid production bottlenecks, ensure that all processes run smoothly from the moment you receive your order to the time the product ships.
This includes both planning for capacity and quality control.
Continuous improvement techniques like Six Sigma are the best way to achieve this.
Six Sigma is a management method that helps to improve quality and reduce waste.
It focuses on eliminating variation and creating consistency in your work.
Is automation important in manufacturing?
Automating is not just important for manufacturers, but also for service providers. It enables them to provide services faster and more efficiently. It helps them to lower costs by reducing human errors, and improving productivity.
How can manufacturing overproduction be reduced?
Improved inventory management is the key to reducing overproduction. This would reduce time spent on activities such as purchasing, stocking, and maintaining excess stock. We could use these resources to do other productive tasks.
One way to do this is to adopt a Kanban system. A Kanban board can be used to monitor work progress. In a Kanban system, work items move through a sequence of states until they reach their final destination. Each state has a different priority level.
If work is moving from one stage to the other, then the current task can be completed and moved on to the next. But if a task remains in the beginning stages it will stay that way until it reaches its end.
This helps to keep work moving forward while ensuring that no work is left behind. Managers can monitor the work being done by Kanban boards to see what is happening at any given time. This information allows them to adjust their workflow based on real-time data.
Lean manufacturing, another method to control inventory levels, is also an option. Lean manufacturing focuses on eliminating waste throughout the entire production chain. Anything that does not contribute to the product's value is considered waste. Some common types of waste include:
-
Overproduction
-
Inventory
-
Unnecessary packaging
-
Exceed materials
By implementing these ideas, manufacturers can improve efficiency and cut costs.
Statistics
- (2:04) MTO is a production technique wherein products are customized according to customer specifications, and production only starts after an order is received. (oracle.com)
- It's estimated that 10.8% of the U.S. GDP in 2020 was contributed to manufacturing. (investopedia.com)
- You can multiply the result by 100 to get the total percent of monthly overhead. (investopedia.com)
- Many factories witnessed a 30% increase in output due to the shift to electric motors. (en.wikipedia.org)
- According to the United Nations Industrial Development Organization (UNIDO), China is the top manufacturer worldwide by 2019 output, producing 28.7% of the total global manufacturing output, followed by the United States, Japan, Germany, and India.[52][53] (en.wikipedia.org)
External Links
How To
How to Use lean manufacturing in the Production of Goods
Lean manufacturing is a management style that aims to increase efficiency and reduce waste through continuous improvement. It was first developed in Japan in the 1970s/80s by Taiichi Ahno, who was awarded the Toyota Production System (TPS), award from KanjiToyoda, the founder of TPS. Michael L. Watkins published the "The Machine That Changed the World", the first book about lean manufacturing. It was published in 1990.
Lean manufacturing is often described as a set if principles that help improve the quality and speed of products and services. It emphasizes eliminating waste and defects throughout the value stream. Lean manufacturing is also known as just in time (JIT), zero defect total productive maintenance(TPM), and five-star (S). Lean manufacturing seeks to eliminate non-value added activities, such as inspection, work, waiting, and rework.
Lean manufacturing improves product quality and costs. It also helps companies reach their goals quicker and decreases employee turnover. Lean manufacturing has been deemed one of the best ways to manage the entire value-chain, including customers, distributors as well retailers and employees. Lean manufacturing practices are widespread in many industries. For example, Toyota's philosophy underpins its success in automobiles, electronics, appliances, healthcare, chemical engineering, aerospace, paper, food, etc.
Lean manufacturing includes five basic principles:
-
Define Value - Determine the value that your business brings to society. Also, identify what sets you apart from your competitors.
-
Reduce Waste - Eliminate any activity that doesn't add value along the supply chain.
-
Create Flow. Ensure that your work is uninterrupted and flows seamlessly.
-
Standardize and Simplify – Make processes as consistent, repeatable, and as simple as possible.
-
Build relationships - Develop and maintain personal relationships with both your internal and external stakeholders.
Lean manufacturing, although not new, has seen renewed interest in the economic sector since 2008. Many businesses have adopted lean production techniques to make them more competitive. In fact, some economists believe that lean manufacturing will be an important factor in economic recovery.
Lean manufacturing is now becoming a common practice in the automotive industry, with many benefits. These include higher customer satisfaction, lower inventory levels, lower operating expenses, greater productivity, and improved overall safety.
It can be applied to any aspect of an organisation. This is because it ensures efficiency and effectiveness in all stages of the value chain.
There are three main types of lean manufacturing:
-
Just-in Time Manufacturing, (JIT): This kind of lean manufacturing is also commonly known as "pull-systems." JIT is a method in which components are assembled right at the moment of use, rather than being manufactured ahead of time. This strategy aims to decrease lead times, increase availability of parts and reduce inventory.
-
Zero Defects Manufacturing: ZDM ensures that no defective units leave the manufacturing plant. Repairing a part that is damaged during assembly should be done, not scrapping. This applies to finished products, which may need minor repairs before they are shipped.
-
Continuous Improvement (CI): CI aims to improve the efficiency of operations by continuously identifying problems and making changes in order to eliminate or minimize waste. Continuous improvement involves continuous improvement of processes and people as well as tools.