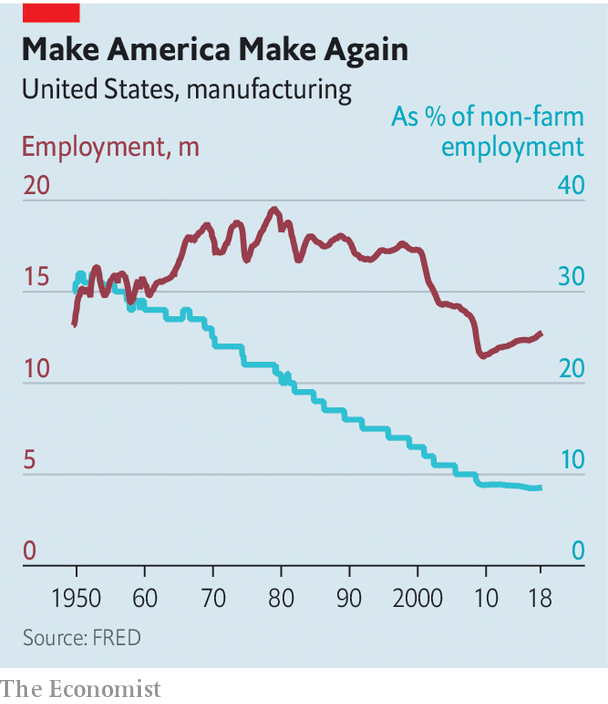
A director of manufacturing manages the company's entire manufacturing process. They are responsible for overseeing all aspects of manufacturing, from design through to production. For this job, you must have a great deal of manufacturing experience and be familiar with all new technologies. Robotics and 3D printing are two examples of these technologies. The director who is up-to-date with these technologies will be a valuable asset to the company. The director's role in the manufacturing industry will change as it evolves. He or she will need to work closely with engineering and operations, as well as placing greater emphasis on quality control in the manufacturing plant.
Salary for a director in manufacturing
The region in which a Director or Manufacturing is located can have a significant impact on their salary. Many directors earn in the six-figures range. Some directors make significantly more than others. The years of experience and education can have an impact on the salary of a director of manufacturing. There are a few things that can influence the amount you earn in your region.
The salary for a director of manufacturing varies but it's generally higher if you have more work experience. Like many other positions, salary can be affected by the cost of living or where you live. If you live in a big city, expect to earn higher salaries, but be aware that your salary may not match the cost of living. When the opportunity presents itself, it is important to be open to negotiations to obtain a higher wage.
The salary for a Director of Manufacturing Operations ranges from $181,500 to $66,000 per annum. The salary of a Director Manufacturing Operations is highly variable. It can vary by up 8% among different cities. A director of manufacturing operations in Fremont, CA can earn between $128,493 and $164,500, which is considerably more than the national average. The salary of a Director in Manufacturing Operations can vary depending on where you live, how experienced you are, and what company you work for.
Education necessary
The director of manufacturing is responsible for managing a production facility and overseeing the production process. This job includes managing new employees, quality assurance, working with designers and meeting production standards. A director of manufacturing usually reports to the top management team. He or she executes sales and policy initiatives. Candidates must have experience in manufacturing and communicate well. Different companies have different requirements for directors of manufacturing.
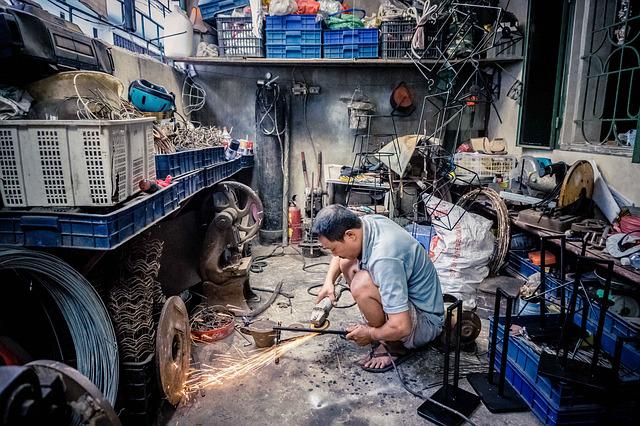
Although a graduate degree in engineering is not always required for director of manufacturing jobs, a post-secondary education in a related field will greatly enhance your skill set and knowledge base. A MBA in industrial management or business administration would be a great option for this job. It teaches candidates about economics, management, and organizational behavior. Ultimately, you will be responsible for managing a diverse group of people.
As a director in manufacturing you will work closely alongside engineers and designers during the product design phase. You will play a key role in this stage by evaluating new processes and making sure quality standards are met before you commit resources to larger productions. Successful directors are also responsible for overseeing the production process and acting as coaches for their employees. They will mentor them on best practices and risk mitigation. Manufacturing directors are responsible for overseeing all aspects of production and must also have problem-solving skills.
Experience required
A bachelor's degree in a relevant field and five to 10 years of progressive work experience are often necessary for this position. For this position, manufacturing companies prefer to recruit internal employees. The ideal candidate must have a deep understanding of the manufacturing industry and its business goals. However, a graduate degree may also be desired by some employers. In addition to these requirements, candidates may have additional training in their chosen field or industry.
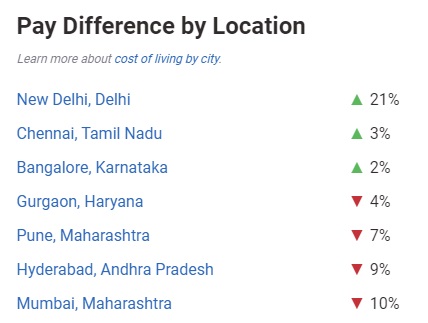
The manufacturing process is managed by the director of production, who oversees engineers, supervisors and workers. They could be responsible to solve problems and develop solutions. They might also be responsible to develop and implement quality control programs. The manufacturing director reports directly to the chief executive of the organization. Experience in manufacturing is an absolute must. If you are looking to succeed in the manufacturing management position, it is important that you have some experience.
Experience as a manufacturing director essential. Directors must have a minimum of 10 years of experience in a manufacturing context. They may have worked as supervisors or technicians in the manufacturing industry. They should have excellent communication skills. Additionally, the director of manufacturing should have a solid understanding of business strategy. A director of Manufacturing must also be able to communicate effectively with other departments. The director of manufacturing oversees production and ensures it meets high quality standards.
FAQ
Can we automate some parts of manufacturing?
Yes! Yes! Automation has existed since ancient times. The Egyptians discovered the wheel thousands and years ago. Today, robots assist in the assembly of lines.
There are many uses of robotics today in manufacturing. These include:
-
Automation line robots
-
Robot welding
-
Robot painting
-
Robotics inspection
-
Robots create products
Automation could also be used to improve manufacturing. For example, 3D printing allows us to make custom products without having to wait for weeks or months to get them manufactured.
What is the responsibility of a logistics manager?
Logistics managers ensure that goods arrive on time and are unharmed. This is done using his/her knowledge of the company's products. He/she should make sure that enough stock is on hand to meet the demands.
What are the four types of manufacturing?
Manufacturing is the process of transforming raw materials into useful products using machines and processes. Manufacturing can include many activities such as designing and building, testing, packaging shipping, selling, servicing, and other related activities.
Statistics
- In 2021, an estimated 12.1 million Americans work in the manufacturing sector.6 (investopedia.com)
- Many factories witnessed a 30% increase in output due to the shift to electric motors. (en.wikipedia.org)
- In the United States, for example, manufacturing makes up 15% of the economic output. (twi-global.com)
- According to a Statista study, U.S. businesses spent $1.63 trillion on logistics in 2019, moving goods from origin to end user through various supply chain network segments. (netsuite.com)
- Job #1 is delivering the ordered product according to specifications: color, size, brand, and quantity. (netsuite.com)
External Links
How To
How to use lean manufacturing in the production of goods
Lean manufacturing is a management system that aims at increasing efficiency and reducing waste. It was developed by Taiichi Okono in Japan, during the 1970s & 1980s. TPS founder Kanji Takoda awarded him the Toyota Production System Award (TPS). Michael L. Watkins published the original book on lean manufacturing, "The Machine That Changed the World," in 1990.
Lean manufacturing is often described as a set if principles that help improve the quality and speed of products and services. It is about eliminating defects and waste from all stages of the value stream. Lean manufacturing is also known as just in time (JIT), zero defect total productive maintenance(TPM), and five-star (S). Lean manufacturing is about eliminating activities that do not add value, such as inspection, rework, and waiting.
Lean manufacturing can help companies improve their product quality and reduce costs. Additionally, it helps them achieve their goals more quickly and reduces employee turnover. Lean manufacturing can be used to manage all aspects of the value chain. Customers, suppliers, distributors, retailers and employees are all included. Lean manufacturing can be found in many industries. Toyota's philosophy, for example, is what has enabled it to be successful in electronics, automobiles, medical devices, healthcare and chemical engineering as well as paper and food.
Five principles are the basis of lean manufacturing:
-
Define Value: Identify the social value of your business and what sets you apart.
-
Reduce waste - Get rid of any activity that does not add value to the supply chain.
-
Create Flow – Ensure that work flows smoothly throughout the process.
-
Standardize & simplify - Make processes consistent and repeatable.
-
Develop Relationships: Establish personal relationships both with internal and external stakeholders.
Lean manufacturing isn’t new, but it has seen a renewed interest since 2008 due to the global financial crisis. Many businesses have adopted lean production techniques to make them more competitive. In fact, some economists believe that lean manufacturing will be an important factor in economic recovery.
Lean manufacturing has many benefits in the automotive sector. These include higher customer satisfaction, lower inventory levels, lower operating expenses, greater productivity, and improved overall safety.
Any aspect of an enterprise can benefit from Lean manufacturing. However, it is particularly useful when applied to the production side of an organization because it ensures that all steps in the value chain are efficient and effective.
There are three types of lean manufacturing.
-
Just-in Time Manufacturing: This lean manufacturing method is commonly called "pull systems." JIT refers to a system in which components are assembled at the point of use instead of being produced ahead of time. This approach aims to reduce lead times, increase the availability of parts, and reduce inventory.
-
Zero Defects Manufacturing (ZDM),: ZDM is a system that ensures no defective units are left the manufacturing facility. If a part is required to be repaired on the assembly line, it should not be scrapped. This also applies to finished products that need minor repairs before being shipped.
-
Continuous Improvement (CI), also known as Continuous Improvement, aims at improving the efficiency of operations through continuous identification and improvement to minimize or eliminate waste. Continuous Improvement involves continuous improvement of processes.