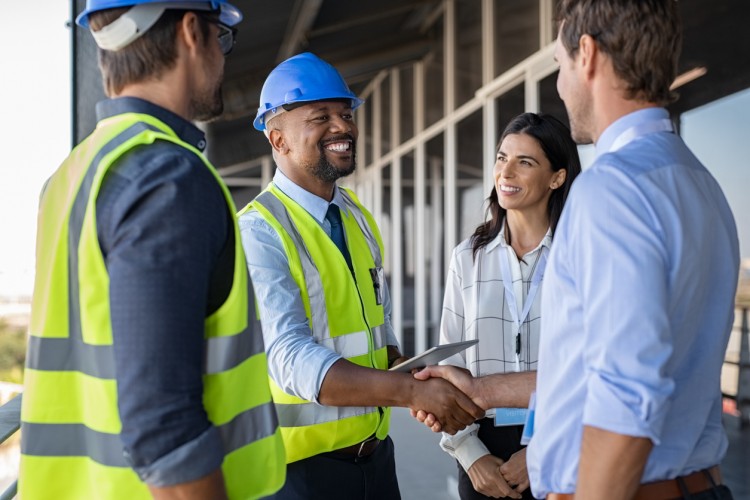
An industrial engineer applies his or her knowledge to improve products and processes by engineering and testing. In product development, industrial engineers use shake tables to test entire products under varying temperatures, humidity, and vibrations. Failure data is collected and used to improve manufacturing processes and engineering. Simple changes such as mold-resistant coatings can make a big difference in the quality and durability of a product. Even the smallest changes, such as a lock-washed placement, can improve a product's service life.
Job description
Your job description is a key component of a career as an engineer. You will attract the best industrial engineers if you can combine technical knowledge with people skills. Monster has many engineering job listings. You can find inspiration for your job description here. Begin with a persuasive introduction that highlights the company's benefits. Your employer should be attractive to you, whether you are looking to join a well-respected brand, an innovative start up, or a young, dynamic company with a creative, open atmosphere.
Along with excellent technical skills and communication skills, industrial engineers should also be able to communicate well. An industrial engineer must be able communicate well with everyone involved in industrial processes. An industrial engineer must be able to convince employees and managers that his or her methods will increase efficiency. The best relationship management results in higher productivity. It isn't just technical skills that are essential in the job of an industrial engineer.
Education requirements
An education in the field of industrial engineering is necessary for a position as this one involves a great deal of math and analytical skills. A strong communication skill is also essential for industrial engineers. They are expected to communicate the results to others. In addition to this, they must be able to design processes and designs that reduce labor and costs. This field can also be achieved through education. Here are some requirements to be successful in this position.
An industrial engineer must have a college diploma. However, they also need to be able to communicate and interact well with others. To communicate effectively with employees and business leaders, industrial engineers need to have strong communication and analytical skills. This profession requires excellent leadership and problem-solving skills. An industrial engineer must have a high degree in technical competence and mechanical aptitude.
You have many options for career choices
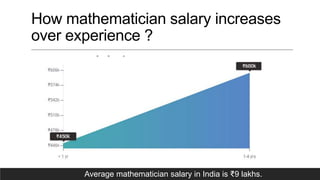
There are many career opportunities for industrial engineers. Although most industrial engineers start in manufacturing, other options include hospitals or government agencies. Other possible careers for industrial engineers include the food industry as well as retail trade, professional trade organizations, education agencies, and computer service centres. The list of possible jobs for industrial engineers is endless, but here are a few of the best. Learn more about what career options are available for industrial engineers to see if they're right for you.
An industrial engineer can be focused on efficiency and effectiveness. Their job requires them to balance several factors such as time, number of workers needed, available technology, and actions workers must take. They must also be aware of safety and environment concerns. Many industrial engineers also engage in quality assurance activities and supply chain management. This is important because many industries are constantly trying to cut costs while increasing their productivity. In addition, they can help to develop new product applications and optimize work flow throughout an organization.
Salary
In 2004, the median industrial engineer salary was $87.513 USD. This number is expected increase to $114.146 by 2020. The industry one works in will have a significant impact on how much you earn. Salaries in thriving industries are likely to receive larger raises. Industrial Engineers' bonus figures change regularly and are often modest. Most bonus recipients work in the revenue generation chain. To get the best pay for this job, you must have a degree in industrial engineering.
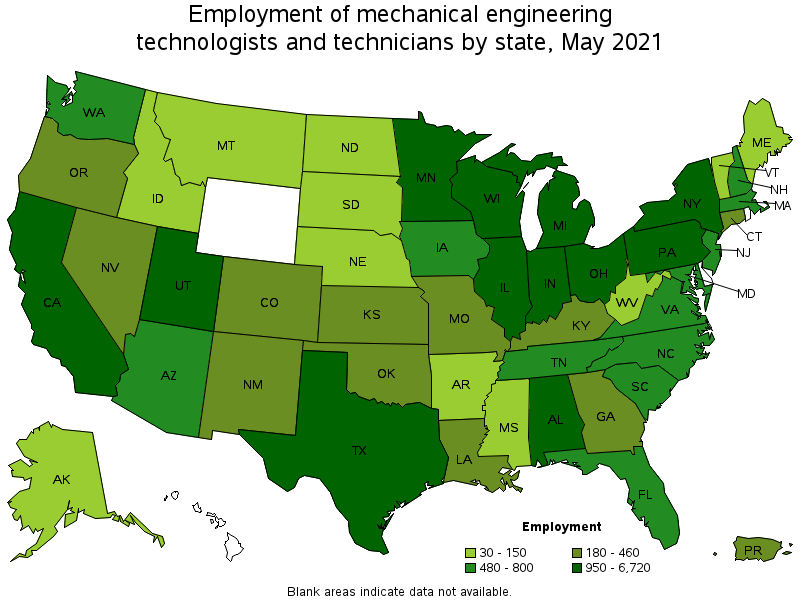
To be a successful industrial engineer, you must hold a bachelor's degree. Some employers, however, prefer PhDs. The average salary for an industrial engineer in the United States is $56,000 to $121,000. However, this number can fluctuate greatly. An industrial engineer can work in an administrative setting but most jobs require overtime and protective gear. Therefore, flexibility is essential.
FAQ
Why should you automate your warehouse?
Modern warehousing has seen automation take center stage. The rise of e-commerce has led to increased demand for faster delivery times and more efficient processes.
Warehouses must adapt quickly to meet changing customer needs. To do so, they must invest heavily in technology. Automating warehouses has many benefits. Here are some of the reasons automation is worth your investment:
-
Increases throughput/productivity
-
Reduces errors
-
Improves accuracy
-
Safety Boosts
-
Eliminates bottlenecks
-
Allows companies to scale more easily
-
Workers are more productive
-
Provides visibility into everything that happens in the warehouse
-
Enhances customer experience
-
Improves employee satisfaction
-
Reduces downtime and improves uptime
-
Ensures quality products are delivered on time
-
Eliminates human error
-
It helps ensure compliance with regulations
What is the role of a manager in manufacturing?
A manufacturing manager has to ensure that all manufacturing processes work efficiently and effectively. They should also be aware and responsive to any company problems.
They must also be able to communicate with sales and marketing departments.
They should also be knowledgeable about the latest trends in the industry so they can use this information for productivity and efficiency improvements.
What are manufacturing and logistics?
Manufacturing is the act of producing goods from raw materials using machines and processes. Logistics encompasses the management of all aspects associated with supply chain activities such as procurement, production planning, distribution and inventory control. It also includes customer service. As a broad term, manufacturing and logistics often refer to both the creation and delivery of products.
What are the jobs in logistics?
There are many jobs available in logistics. These are some of the jobs available in logistics:
-
Warehouse workers: They load and unload trucks, pallets, and other cargo.
-
Transport drivers - These are people who drive trucks and trailers to transport goods or perform pick-ups.
-
Freight handlers: They sort and package freight in warehouses.
-
Inventory managers – These people oversee inventory at warehouses.
-
Sales representatives: They sell products to customers.
-
Logistics coordinators are responsible for organizing and planning logistics operations.
-
Purchasing agents – They buy goods or services necessary to run a company.
-
Customer service representatives - They answer calls and emails from customers.
-
Shippers clerks - They process shipping order and issue bills.
-
Order fillers - These people fill orders based on what has been ordered.
-
Quality control inspectors are responsible for inspecting incoming and outgoing products looking for defects.
-
Other - Logistics has many other job opportunities, including transportation supervisors, logistics specialists, and cargo specialists.
What's the difference between Production Planning & Scheduling?
Production Planning (PP) is the process of determining what needs to be produced at any given point in time. Forecasting and identifying production capacity are two key elements to this process.
Scheduling is the process of assigning specific dates to tasks so they can be completed within the specified timeframe.
Is it possible to automate certain parts of manufacturing
Yes! Yes. Automation has been around since ancient time. The Egyptians invent the wheel thousands of year ago. Nowadays, we use robots for assembly lines.
Actually, robotics can be used in manufacturing for many purposes. These include:
-
Automation line robots
-
Robot welding
-
Robot painting
-
Robotics inspection
-
Robots that make products
Automation could also be used to improve manufacturing. 3D printing, for example, allows us to create custom products without waiting for them to be made.
What does manufacturing mean?
Manufacturing Industries are those businesses that make products for sale. These products are sold to consumers. These companies use various processes such as production, distribution, retailing, management, etc., to fulfill this purpose. They make goods from raw materials with machines and other equipment. This includes all types manufactured goods such as clothing, building materials, furniture, electronics, tools and machinery.
Statistics
- [54][55] These are the top 50 countries by the total value of manufacturing output in US dollars for its noted year according to World Bank.[56] (en.wikipedia.org)
- It's estimated that 10.8% of the U.S. GDP in 2020 was contributed to manufacturing. (investopedia.com)
- Job #1 is delivering the ordered product according to specifications: color, size, brand, and quantity. (netsuite.com)
- According to the United Nations Industrial Development Organization (UNIDO), China is the top manufacturer worldwide by 2019 output, producing 28.7% of the total global manufacturing output, followed by the United States, Japan, Germany, and India.[52][53] (en.wikipedia.org)
- According to a Statista study, U.S. businesses spent $1.63 trillion on logistics in 2019, moving goods from origin to end user through various supply chain network segments. (netsuite.com)
External Links
How To
Six Sigma: How to Use it in Manufacturing
Six Sigma is defined by "the application SPC (statistical process control) techniques to achieve continuous improvements." Motorola's Quality Improvement Department in Tokyo, Japan developed Six Sigma in 1986. Six Sigma is a method to improve quality through standardization and elimination of defects. Many companies have adopted this method in recent years. They believe there is no such thing a perfect product or service. Six Sigma's main objective is to reduce variations from the production average. It is possible to measure the performance of your product against an average and find the percentage of time that it differs from the norm. If it is too large, it means that there are problems.
Understanding the nature of variability in your business is the first step to Six Sigma. Once you have a good understanding of the basics, you can identify potential sources of variation. Also, you will need to identify the sources of variation. Random variations occur when people do mistakes. Symmetrical variations are caused due to factors beyond the process. You could consider random variations if some widgets fall off the assembly lines. It would be considered a systematic problem if every widget that you build falls apart at the same location each time.
Once you've identified where the problems lie, you'll want to design solutions to eliminate those problems. This could mean changing your approach or redesigning the entire process. You should then test the changes again after they have been implemented. If they fail, you can go back to the drawing board to come up with a different plan.