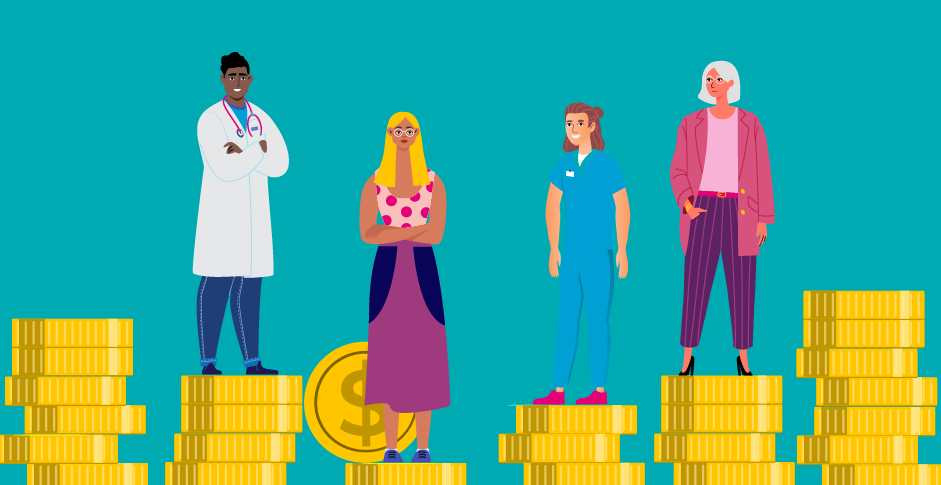
Manufacturers have a significant role to play in the economy. Manufacturing creates jobs and supplies materials for national defense. Manufacturing is actually the largest sector in our economy. It provides goods for almost everyone in our society. Moreover, manufacturing provides a vital source of innovation. While some economists believe that manufacturing is on the decline, others believe it will continue to grow.
Manufacturers produce a variety of products, including furniture, lighting, mattresses, cabinets, and blinds. Each product requires a particular design, a series, of processes, and an investment into tools, labor, equipment, and in machinery. Manufacturing industries are also home to many highly skilled workers in high-productivity jobs. On average, manufacturing workers in America earned $79,000 per annum in 2019.
For manufacturers to compete in the global marketplace, circular processes are essential. These processes are designed to extend beyond the plant, to include the entire supply chain. Manufacturers should also consider the social cost of their processes. There are many processes that involve hazardous substances, which can be harmful to the workers' health. Depending on the degree of safety, hazardous waste cleanup might be more costly than the benefits that the product offers.
The manufacturing sector can play a key role in driving the economic recovery in the United States. The "indirect employment multiplier” of manufacturing is large. Manufacturing's purchasing strength supports more than 14,000 jobs elsewhere in American's economy. Manufacturing's strength can help develop local economies, and communities.
The manufacturing sector plays an important role for economic development. But, the sector is also being under pressure. Many economists believe manufacturing will continue to grow while others believe that it will be eclipsed in the future by the post goods economy. But policymakers will still be able to see the importance of manufacturing's contribution to innovation and economic resilience.
Manufacturing has a diverse workforce and offers jobs for workers of all skill levels. Even for those without college degrees, wages in manufacturing are much higher than the national average. There are many other industries that employ manufacturing workers. These workers are employed in many different industries, including as engineers, technicians, and production managers. There are four main types for manufacturing activities. These include continuous manufacturing and batch process manufacturing. Scale-based and standardized activities and discrete production.
Continuous manufacturing, also known by batch process manufacturing or oil refining, involves a variety of processes that run continuously, 24 hours per day. Continuous manufacturing is used in oil refining, and food production. Batch manufacturing is similar as continuous manufacturing but uses a larger variety of raw materials. Batch process manufacturing also uses clean machinery for the next batch.
The manufacturing sector is a strong driver for inclusive growth and resilience in the U.S. Manufacturing creates jobs for a wide range of skilled workers. Additionally, the sector's purchase of domestic products supports many other jobs. Manufacturing's high wages make it a major driver of economic growth.
FAQ
How can I learn about manufacturing?
Hands-on experience is the best way to learn more about manufacturing. You can also read educational videos or take classes if this isn't possible.
Why is logistics important for manufacturing?
Logistics are an essential component of any business. They enable you to achieve outstanding results by helping manage product flow from raw materials through to finished goods.
Logistics play a key role in reducing expenses and increasing efficiency.
How can excess manufacturing production be reduced?
Improved inventory management is the key to reducing overproduction. This would reduce the time needed to manage inventory. We could use these resources to do other productive tasks.
This can be done by using a Kanban system. A Kanbanboard is a visual tool that allows you to keep track of the work being done. Kanban systems are where work items travel through a series of states until reaching their final destination. Each state is assigned a different priority.
When work is completed, it can be transferred to the next stage. But if a task remains in the beginning stages it will stay that way until it reaches its end.
This allows for work to continue moving forward, while also ensuring that there is no work left behind. With a Kanban board, managers can see exactly how much work is being done at any given moment. This data allows them adjust their workflow based upon real-time data.
Another way to control inventory levels is to implement lean manufacturing. Lean manufacturing is about eliminating waste from all stages of the production process. Waste includes anything that does not add value to the product. The following are examples of common waste types:
-
Overproduction
-
Inventory
-
Unnecessary packaging
-
Excess materials
These ideas will help manufacturers increase efficiency and lower costs.
What is the difference in Production Planning and Scheduling, you ask?
Production Planning (PP), also known as forecasting and identifying production capacities, is the process that determines what product needs to be produced at any particular time. Forecasting demand is one way to do this.
Scheduling refers the process by which tasks are assigned dates so that they can all be completed within the given timeframe.
How can manufacturing efficiency be improved?
First, determine which factors have the greatest impact on production time. The next step is to identify the most important factors that affect production time. If you aren't sure where to begin, think about the factors that have the greatest impact on production time. Once you have identified the factors, then try to find solutions.
Statistics
- Job #1 is delivering the ordered product according to specifications: color, size, brand, and quantity. (netsuite.com)
- (2:04) MTO is a production technique wherein products are customized according to customer specifications, and production only starts after an order is received. (oracle.com)
- In 2021, an estimated 12.1 million Americans work in the manufacturing sector.6 (investopedia.com)
- Many factories witnessed a 30% increase in output due to the shift to electric motors. (en.wikipedia.org)
- According to the United Nations Industrial Development Organization (UNIDO), China is the top manufacturer worldwide by 2019 output, producing 28.7% of the total global manufacturing output, followed by the United States, Japan, Germany, and India.[52][53] (en.wikipedia.org)
External Links
How To
How to Use Lean Manufacturing for the Production of Goods
Lean manufacturing (or lean manufacturing) is a style of management that aims to increase efficiency, reduce waste and improve performance through continuous improvement. It was developed in Japan between 1970 and 1980 by Taiichi Ohno. TPS founder Kanji Tyoda gave him the Toyota Production System, or TPS award. Michael L. Watkins published the "The Machine That Changed the World", the first book about lean manufacturing. It was published in 1990.
Lean manufacturing refers to a set of principles that improve the quality, speed and costs of products and services. It is about eliminating defects and waste from all stages of the value stream. Lean manufacturing can be described as just-in–time (JIT), total productive maintenance, zero defect (TPM), or even 5S. Lean manufacturing emphasizes reducing non-value-added activities like inspection, rework and waiting.
Lean manufacturing is a way for companies to achieve their goals faster, improve product quality, and lower costs. Lean manufacturing has been deemed one of the best ways to manage the entire value-chain, including customers, distributors as well retailers and employees. Lean manufacturing practices are widespread in many industries. For example, Toyota's philosophy underpins its success in automobiles, electronics, appliances, healthcare, chemical engineering, aerospace, paper, food, etc.
Lean manufacturing is based on five principles:
-
Define Value - Identify the value your business adds to society and what makes you different from competitors.
-
Reduce waste - Stop any activity that isn't adding value to the supply chains.
-
Create Flow - Make sure work runs smoothly without interruptions.
-
Standardize & Simplify - Make processes as consistent and repeatable as possible.
-
Build Relationships- Develop personal relationships with both internal as well as external stakeholders.
Lean manufacturing, although not new, has seen renewed interest in the economic sector since 2008. Many businesses have adopted lean production techniques to make them more competitive. Many economists believe lean manufacturing will play a major role in economic recovery.
With many benefits, lean manufacturing is becoming more common in the automotive industry. These include higher customer satisfaction, lower inventory levels, lower operating expenses, greater productivity, and improved overall safety.
You can apply Lean Manufacturing to virtually any aspect of your organization. Because it makes sure that all value chains are efficient and effectively managed, Lean Manufacturing is particularly helpful for organizations.
There are three main types in lean manufacturing
-
Just-in Time Manufacturing, (JIT): This kind of lean manufacturing is also commonly known as "pull-systems." JIT stands for a system where components are assembled on the spot rather than being made in advance. This approach aims to reduce lead times, increase the availability of parts, and reduce inventory.
-
Zero Defects Manufacturing (ZDM),: ZDM is a system that ensures no defective units are left the manufacturing facility. If a part is required to be repaired on the assembly line, it should not be scrapped. This is true even for finished products that only require minor repairs prior to shipping.
-
Continuous Improvement (CI: Continuous improvement aims to increase the efficiency of operations by constantly identifying and making improvements to reduce or eliminate waste. Continuous improvement involves continuous improvement of processes and people as well as tools.