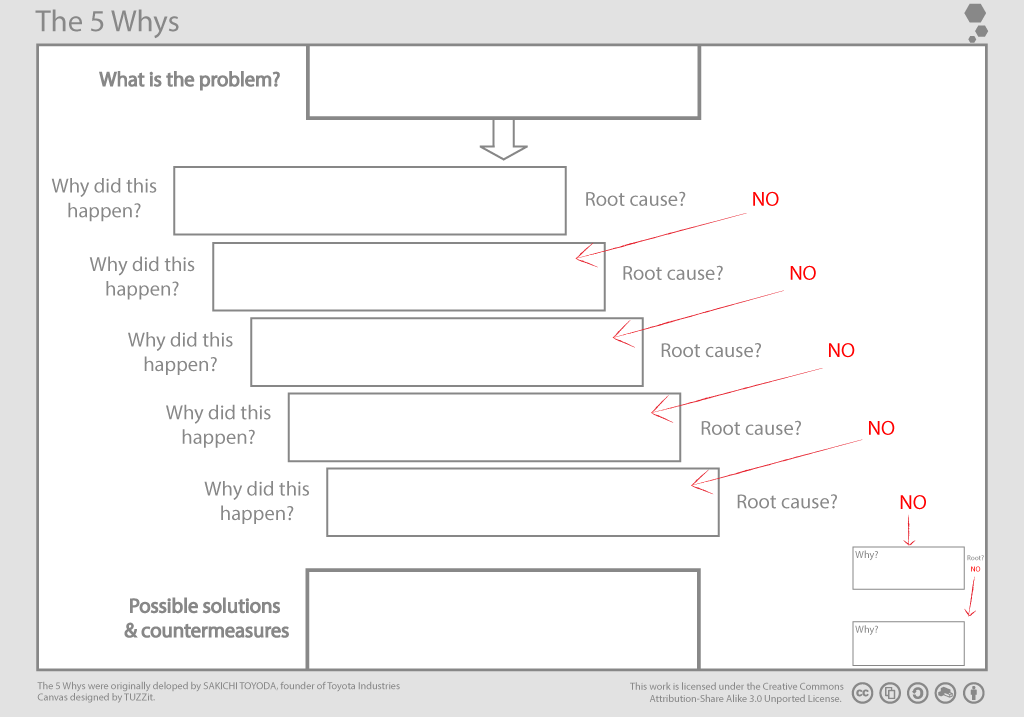
SCOR, a model of process reference developed by Supply Chain Council is widely adopted in industry. It helps companies understand their operational performance, goals and business processes. The software also allows users to compare themselves with their peers and identify areas that need improvement.
The model can be divided into three major sections: process modelling, performance measurements and best practices for the supply chain. The first segment focuses on process modeling. This includes planning, sourcing and making goods. The model also covers market interactions and returns.
This section also includes over 150 key performance indicator (KPI) metrics that you can utilize to measure your success. For example, you can evaluate the delivery performance of your suppliers and determine whether they are providing quality products at a reasonable cost.
You can also analyze customer returns to determine the savings you would achieve if suppliers reduced their return rates by 20%. This helps you identify areas where you might be able to save money by improving your processes.
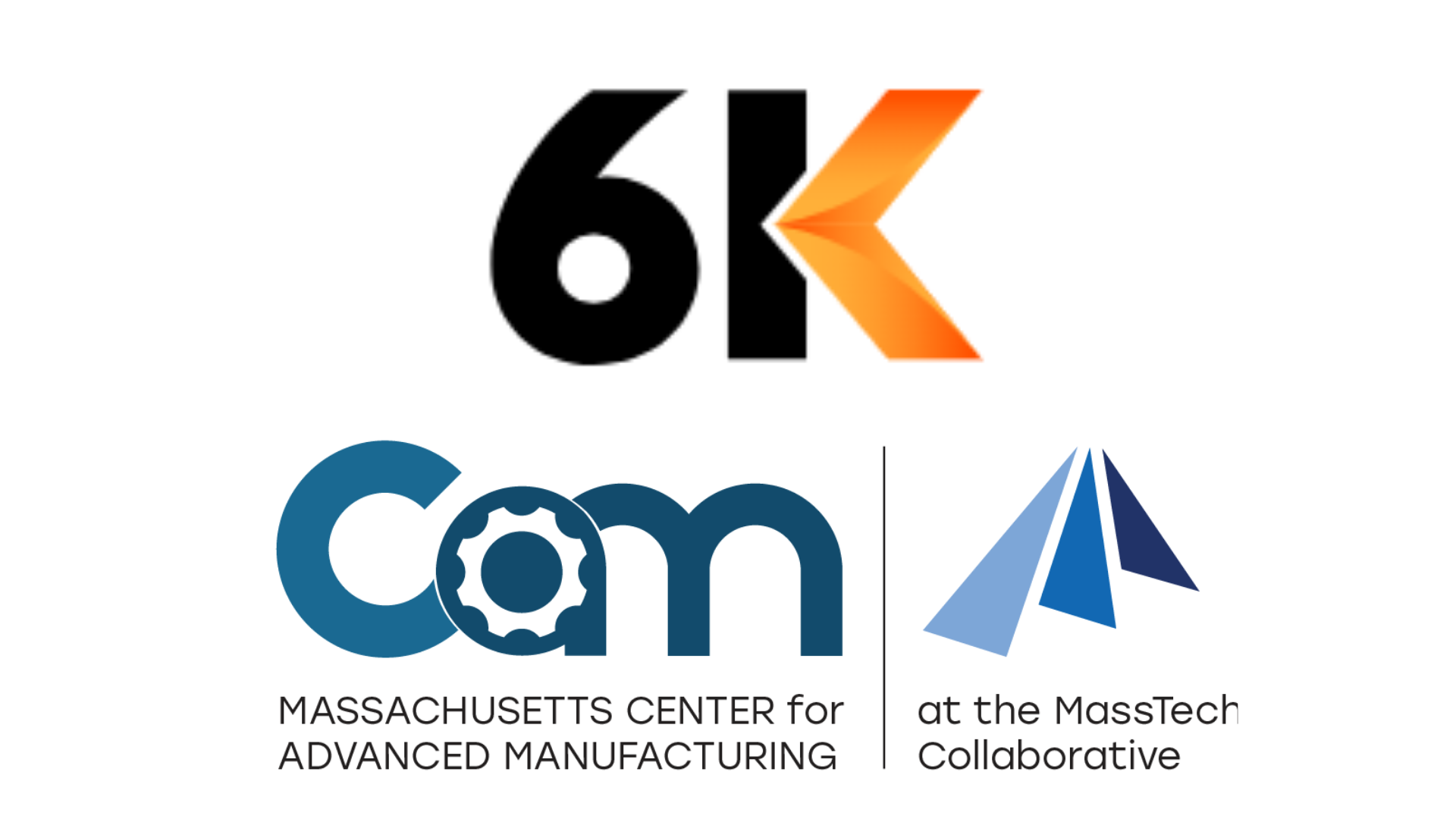
You may be confused by the SCOR model if you are new to it. The SCOR model is designed to help you develop a standardized, efficient system of managing your supply chain.
The system breaks down the supply chain into ideal processes and then categorizes them based on their value to your business. It is easy to compare different supply chain activities in your company as well as across industries.
The second segment of the model is performance measurements, which is made up of metrics that you can use to evaluate the overall success of your supply chain operations. These metrics can be applied to a range of performance aspects, including inventory, transportation, supplier and customer satisfaction.
You can use the performance measurement data to find out how your company is performing in each of these areas and to set action items to improve your operations. These measures will only be useful if you actually take action.
Create a list that includes all the KPIs your company is currently tracking. You can then review these metrics on a monthly basis to determine how well your company is performing in each area.
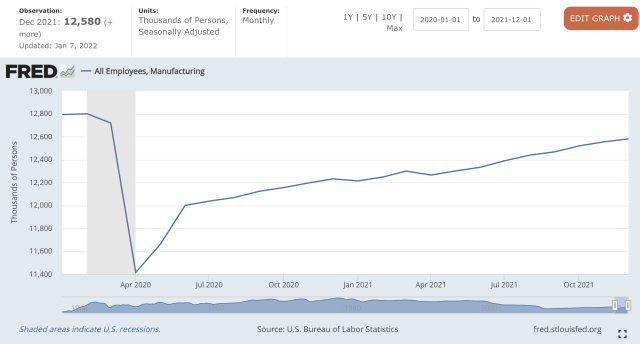
Now is the time to begin thinking about how you can improve your business and increase your profit. Compare the new processes you have implemented with your existing ones to determine if they are effective.
This is the perfect way to get your entire team started on improving your company's operations. SCOR is a great way to get your team started on the path of improving supply chain operations.
FAQ
What are the responsibilities of a logistic manager?
Logistics managers are responsible for ensuring that all goods arrive in perfect condition and on time. This is done through his/her expertise and knowledge about the company's product range. He/she should ensure that sufficient stock is available in order to meet customer demand.
Why is logistics important for manufacturing?
Logistics are an essential part of any business. They enable you to achieve outstanding results by helping manage product flow from raw materials through to finished goods.
Logistics play a key role in reducing expenses and increasing efficiency.
What skills should a production planner have?
You must be flexible and organized to become a productive production planner. Communication skills are essential to ensure that you can communicate effectively with clients, colleagues, and customers.
What is the difference between Production Planning, Scheduling and Production Planning?
Production Planning (PP), also known as forecasting and identifying production capacities, is the process that determines what product needs to be produced at any particular time. This can be done by forecasting demand and identifying production capabilities.
Scheduling refers to the process of allocating specific dates to tasks in order that they can be completed within a specified timeframe.
What are the logistics products?
Logistics refers to the movement of goods from one place to another.
These include all aspects related to transport such as packaging, loading and transporting, storing, transporting, unloading and warehousing inventory management, customer service. Distribution, returns, recycling are some of the options.
Logisticians ensure the product reaches its destination in the most efficient manner. Logisticians help companies improve their supply chain efficiency by providing information about demand forecasts and stock levels, production schedules, as well as availability of raw materials.
They can also track shipments in transit and monitor quality standards.
Statistics
- In the United States, for example, manufacturing makes up 15% of the economic output. (twi-global.com)
- Job #1 is delivering the ordered product according to specifications: color, size, brand, and quantity. (netsuite.com)
- According to the United Nations Industrial Development Organization (UNIDO), China is the top manufacturer worldwide by 2019 output, producing 28.7% of the total global manufacturing output, followed by the United States, Japan, Germany, and India.[52][53] (en.wikipedia.org)
- (2:04) MTO is a production technique wherein products are customized according to customer specifications, and production only starts after an order is received. (oracle.com)
- You can multiply the result by 100 to get the total percent of monthly overhead. (investopedia.com)
External Links
How To
How to use lean manufacturing in the production of goods
Lean manufacturing (or lean manufacturing) is a style of management that aims to increase efficiency, reduce waste and improve performance through continuous improvement. It was first developed in Japan in the 1970s/80s by Taiichi Ahno, who was awarded the Toyota Production System (TPS), award from KanjiToyoda, the founder of TPS. Michael L. Watkins published the "The Machine That Changed the World", the first book about lean manufacturing. It was published in 1990.
Lean manufacturing can be described as a set or principles that are used to improve quality, speed and cost of products or services. It emphasizes the elimination and minimization of waste in the value stream. The five-steps of Lean Manufacturing are just-in time (JIT), zero defect and total productive maintenance (TPM), as well as 5S. Lean manufacturing eliminates non-value-added tasks like inspection, rework, waiting.
Lean manufacturing is a way for companies to achieve their goals faster, improve product quality, and lower costs. Lean manufacturing is a great way to manage the entire value chain including customers, suppliers, distributors and retailers as well as employees. Lean manufacturing can be found in many industries. Toyota's philosophy has been a key driver of success in many industries, including automobiles and electronics.
Five fundamental principles underlie lean manufacturing.
-
Define Value: Identify the social value of your business and what sets you apart.
-
Reduce Waste - Eliminate any activity that doesn't add value along the supply chain.
-
Create Flow: Ensure that the work process flows without interruptions.
-
Standardize and simplify – Make processes as repeatable and consistent as possible.
-
Build Relationships - Establish personal relationships with both internal and external stakeholders.
Although lean manufacturing has always been around, it is gaining popularity in recent years because of a renewed interest for the economy after 2008's global financial crisis. Many businesses have adopted lean manufacturing techniques to help them become more competitive. According to some economists, lean manufacturing could be a significant factor in the economic recovery.
Lean manufacturing, which has many benefits, is now a standard practice in the automotive industry. These include higher customer satisfaction levels, reduced inventory levels as well as lower operating costs.
It can be applied to any aspect of an organisation. However, it is particularly useful when applied to the production side of an organization because it ensures that all steps in the value chain are efficient and effective.
There are three types of lean manufacturing.
-
Just-in-Time Manufacturing: Also known as "pull systems", this type of lean manufacturing uses just-in-time manufacturing (JIT). JIT means that components are assembled at the time of use and not manufactured in advance. This method reduces lead times, increases availability, and decreases inventory.
-
Zero Defects Manufacturing (ZDM): ZDM focuses on ensuring that no defective units leave the manufacturing facility. You should repair any part that needs to be repaired during an assembly line. This is also true for finished products that require minor repairs before shipping.
-
Continuous Improvement (CI), also known as Continuous Improvement, aims at improving the efficiency of operations through continuous identification and improvement to minimize or eliminate waste. Continuous Improvement (CI) involves continuous improvement in processes, people, tools, and infrastructure.