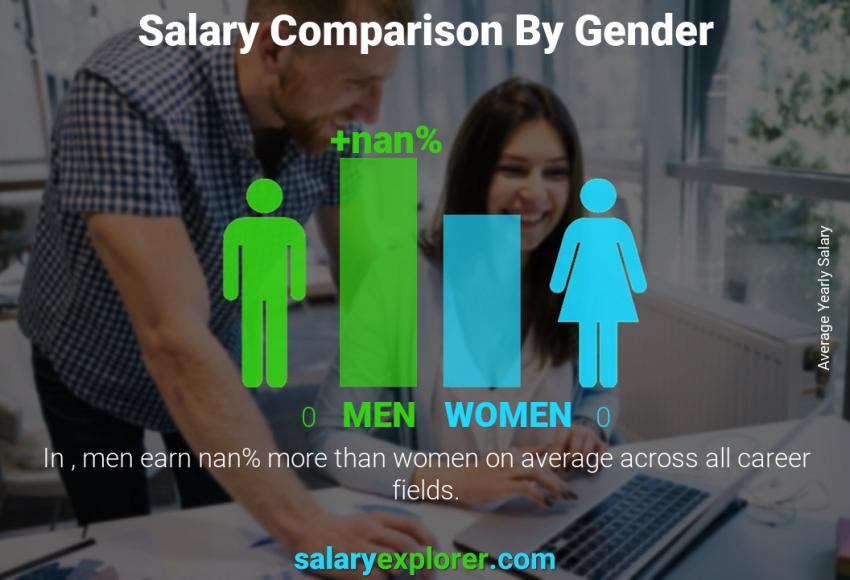
There are many types of manufacturers, but which one is best for your business? Learn more about Continuous manufacturing, Process manufacturing and Job shop manufacturing. Each type comes with its own set of advantages and disadvantages. This article will discuss the differences between these four types. Based on your industry, location and product type, you will be able to choose the right model for your business. Once you have determined which type is best, you need to take into account your sales, production and quality control.
Displacement manufacturing
Discrete Manufacturing is the process of producing distinct products. Some examples of such products include aeroplanes, automobiles, and toys. Companies can focus on specific products and not mass-produce all items with discrete manufacturing. It is possible, for instance, to make unique parts of an aeroplane through the integration of several manufacturing processes. Discrete manufacturing is a popular method for manufacturing high-tech products.
Discrete manufacturing produces distinct items. Instead of producing identical products, discrete Manufacturing produces items that can readily be identified by serial numbers or labels. For example, a smartphone may consist of different parts manufactured in multiple factories in different states, and the individual parts are assembled only once the finished product is ready to be sold. The same applies to the bag that holds your smartphone. It could be made up of different parts, including those from the Missouri plant or headquarters.
Process manufacturing
The process manufacturing branch is one that deals with formulas or recipes. This term contrasts with discrete manufacture, which is concerned only with the production of individual units and bills of materials. The process manufacturing concept also includes the assembly of parts. Because of this, they have very different manufacturing goals. Each method is vital to the manufacturing process. Here are three methods to distinguish between discrete and process manufacturing. Let's examine each one.
Batch process manufacturing works in a similar way to continuous production, but it requires larger batches of raw material and is available around the clock. Batch process manufacturing is used in many industries, including pharmaceuticals, paper production and bookbinding. However, it is not the right choice for every industry. For smaller businesses, it can be too expensive and complex. This method is used by most companies when they need large quantities of the exact same product.
Shop for jobs in manufacturing
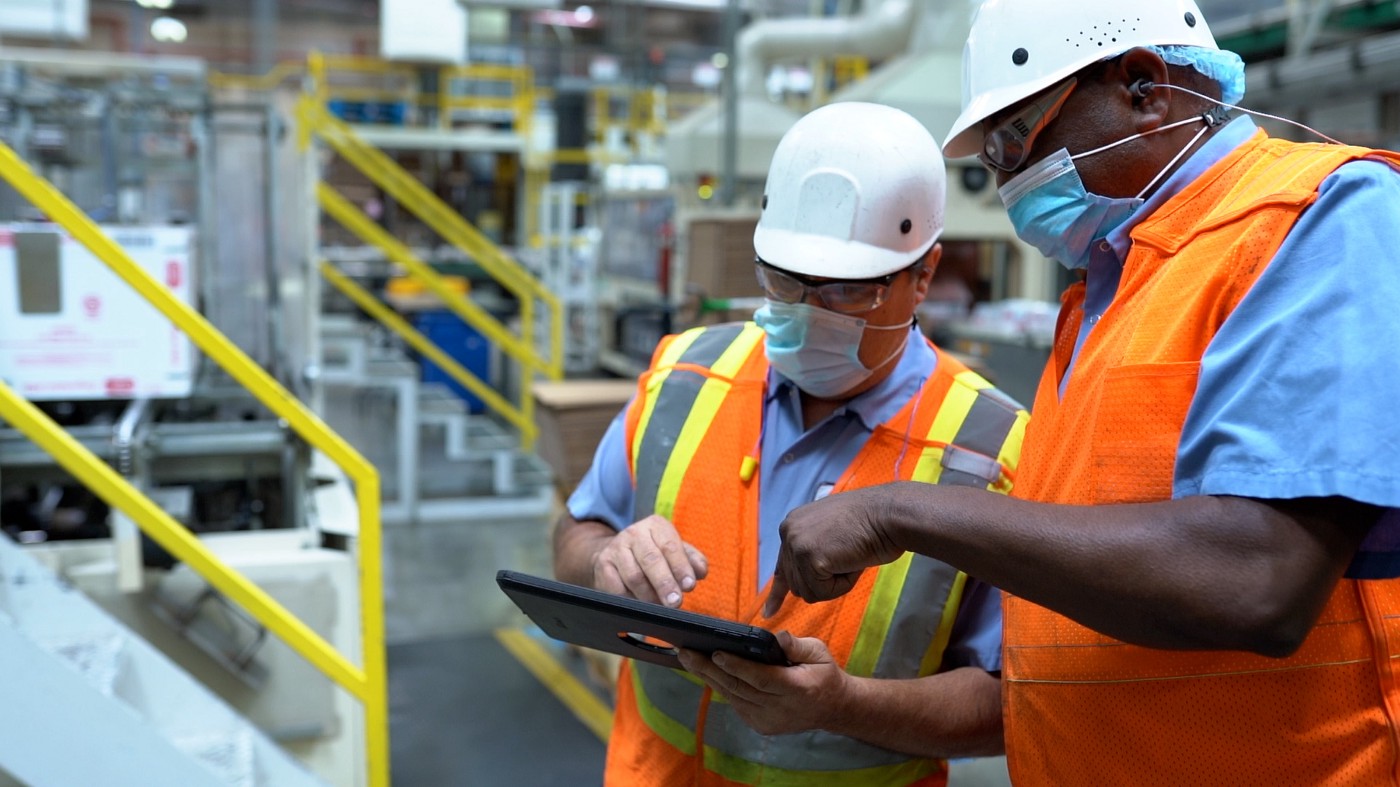
Job shop manufacturing can be described as a small-scale production system that specializes only in custom, batch and semi-custom manufacturing. As each job is completed, job shop systems can move on to the next. This type of production is also known lean manufacturing. It is more efficient to use a single shift than many other methods. These are just a few of the many benefits of job-shop manufacturing. Continue reading to learn more about job shop manufacturing. This method of manufacturing might be beneficial for your business.
First, job shops should be more efficient. A critical factor in achieving a lean manufacturing system is incorporating new manufacturing principles. These principles focus on quality control and justin-time production and are especially relevant for high-volume operations. The job shop can reduce costs and increase productivity by using new manufacturing principles. Each job must be done one at a given time. There should not be any waiting.
Continuous manufacturing
Continuous manufacturing has the advantage of flexible tracking, which is one of its greatest benefits. This is especially beneficial when it concerns product failure. Since the production line's time stamp and the raw material quantity can help identify when a batch has gone wrong, continuous manufacturing allows for more flexible tracking. This increased tracking helps manufacturers reduce waste and decrease the likelihood of product shortages. The pharmaceutical industry is increasingly using continuous manufacturing.
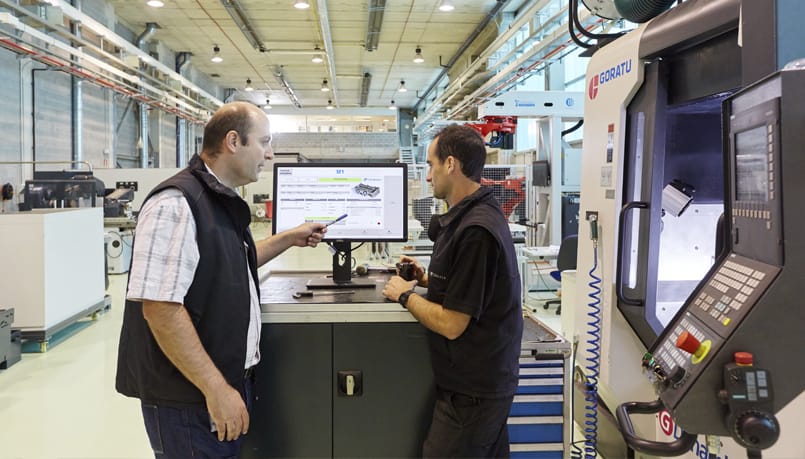
However, while the benefits of continuous manufacturing are clear, implementation is slow. The fact that continuous manufacturing is not fully integrated into the company is often what hinders its implementation. Continuous manufacturing is a great opportunity for the pharmaceutical industry. To be successful, however, the entire process must be integrated with continuous flow as well as end-to–end integration. Although the benefits of continuous production have been recognized by the pharmaceutical industry for many years, implementation has been slow.
FAQ
Can we automate some parts of manufacturing?
Yes! Yes. The wheel was invented by the Egyptians thousands of years ago. We now use robots to help us with assembly lines.
There are many uses of robotics today in manufacturing. These include:
-
Automated assembly line robots
-
Robot welding
-
Robot painting
-
Robotics inspection
-
Robots that make products
Manufacturing can also be automated in many other ways. 3D printing makes it possible to produce custom products in a matter of days or weeks.
What are the essential elements of running a logistics firm?
To be a successful businessman in logistics, you will need many skills and knowledge. You must have good communication skills to interact effectively with your clients and suppliers. You need to understand how to analyze data and draw conclusions from it. You must be able to work well under pressure and handle stressful situations. In order to innovate and create new ways to improve efficiency, creativity is essential. Strong leadership qualities are essential to motivate your team and help them achieve their organizational goals.
It is also important to be efficient and well organized in order meet deadlines.
What are the 7 R's of logistics?
The 7R's of Logistics is an acronym for the seven basic principles of logistics management. It was created by the International Association of Business Logisticians and published in 2004 under its "Seven Principles of Logistics Management".
The acronym consists of the following letters:
-
Responsible - ensure that all actions taken are within legal requirements and are not harmful to others.
-
Reliable - have confidence in the ability to deliver on commitments made.
-
Be responsible - Use resources efficiently and avoid wasting them.
-
Realistic – consider all aspects of operations, from cost-effectiveness to environmental impact.
-
Respectful – Treat others fairly and equitably.
-
You are resourceful and look for ways to save money while increasing productivity.
-
Recognizable - Provide value-added services to customers
What skills do production planners need?
To become a successful production planner, you need to be organized, flexible, and able to multitask. You must also be able to communicate effectively with clients and colleagues.
Why should you automate your warehouse?
Modern warehouses have become more dependent on automation. Increased demand for efficient and faster delivery has resulted in a rise in e-commerce.
Warehouses must be able to quickly adapt to changing demands. They must invest heavily in technology to do this. Automation of warehouses offers many benefits. Here are some of the reasons automation is worth your investment:
-
Increases throughput/productivity
-
Reduces errors
-
Improves accuracy
-
Safety Boosts
-
Eliminates bottlenecks
-
Allows companies to scale more easily
-
It makes workers more efficient
-
Gives you visibility into all that is happening in your warehouse
-
Enhances customer experience
-
Improves employee satisfaction
-
This reduces downtime while increasing uptime
-
Quality products delivered on time
-
Removing human error
-
This helps to ensure compliance with regulations
What do we need to know about Manufacturing Processes in order to learn more about Logistics?
No. No. But, being familiar with manufacturing processes will give you a better understanding about how logistics works.
Statistics
- [54][55] These are the top 50 countries by the total value of manufacturing output in US dollars for its noted year according to World Bank.[56] (en.wikipedia.org)
- Job #1 is delivering the ordered product according to specifications: color, size, brand, and quantity. (netsuite.com)
- According to the United Nations Industrial Development Organization (UNIDO), China is the top manufacturer worldwide by 2019 output, producing 28.7% of the total global manufacturing output, followed by the United States, Japan, Germany, and India.[52][53] (en.wikipedia.org)
- It's estimated that 10.8% of the U.S. GDP in 2020 was contributed to manufacturing. (investopedia.com)
- You can multiply the result by 100 to get the total percent of monthly overhead. (investopedia.com)
External Links
How To
How to Use the Just-In-Time Method in Production
Just-intime (JIT), which is a method to minimize costs and maximize efficiency in business process, is one way. This is where you have the right resources at the right time. This means that you only pay the amount you actually use. Frederick Taylor, a 1900s foreman, first coined the term. He observed how workers were paid overtime if there were delays in their work. He decided to ensure workers have enough time to do their jobs before starting work to improve productivity.
JIT is a way to plan ahead and make sure you don't waste any money. Also, you should look at the whole project from start-to-finish and make sure you have the resources necessary to address any issues. You'll be prepared to handle any potential problems if you know in advance. This way you won't be spending more on things that aren’t really needed.
There are many types of JIT methods.
-
Demand-driven: This JIT is where you place regular orders for the parts/materials that are needed for your project. This will allow to track how much material has been used up. It will also allow you to predict how long it takes to produce more.
-
Inventory-based: This allows you to store the materials necessary for your projects in advance. This allows you to forecast how much you will sell.
-
Project-driven: This means that you have enough money to pay for your project. If you know the amount you require, you can buy the materials you need.
-
Resource-based JIT is the most widespread form. Here, you allocate certain resources based on demand. If you have many orders, you will assign more people to manage them. You'll have fewer orders if you have fewer.
-
Cost-based : This is similar in concept to resource-based. But here, you aren't concerned about how many people your company has but how much each individual costs.
-
Price-based: This is a variant of cost-based. However, instead of focusing on the individual workers' costs, this looks at the total price of the company.
-
Material-based is an alternative to cost-based. Instead of looking at the total cost in the company, this method focuses on the average amount of raw materials that you consume.
-
Time-based: This is another variation of resource-based JIT. Instead of focusing only on how much each employee is costing, you should focus on how long it takes to complete your project.
-
Quality-based: This is yet another variation of resource-based JIT. Instead of looking at the labor costs and time it takes to make a product, think about its quality.
-
Value-based: This is one of the newest forms of JIT. In this scenario, you're not concerned about how products perform or whether customers expect them to meet their expectations. Instead, you're focused on how much value you add to the market.
-
Stock-based. This method is inventory-based and focuses only on the actual production at any given point. It's used when you want to maximize production while minimizing inventory.
-
Just-in time (JIT), planning: This is a combination JIT/supply chain management. It is the process of scheduling components' delivery as soon as they have been ordered. It's important as it reduces leadtimes and increases throughput.