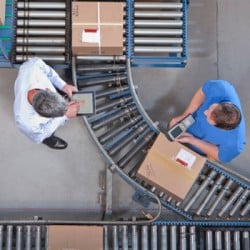
Lean manufacturing, a management method that helps to reduce waste and increase efficiency, is what it stands for. It's based on the principles of Henry Ford and KiichiroToyoda who were the presidents of Toyota Motor Corporation before World War II. Manufacturing is not considered an assembly line in lean manufacturing. The key principles to lean are eliminating waste, streamlining processes, creating knowledge, optimizing whole systems, continuous improvement, and creating value.
To become lean, the first step is to find out what you're doing that doesn't add value. You can do this using either quantitative or qualitative methods. This can be done by looking at the price customers pay for your products. If the price of your product is higher than what you are offering, that's a sign you have a problem.
Kaizen is a method to identify the amount of waste produced by a process. It involves all employees working together to solve small problems in an incremental manner. Kaizen events may be used either alone or in conjunction to other lean tools.
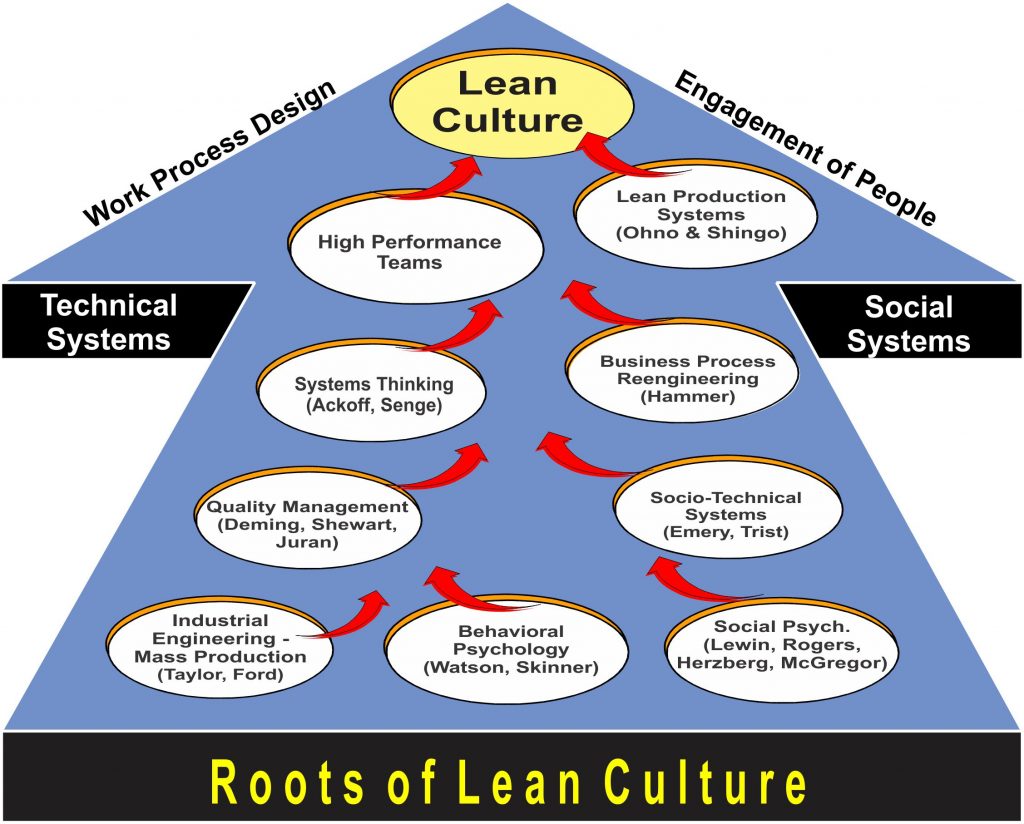
Another way to identify waste in a production facility is to conduct value stream mapping. VSM helps manufacturers see all the steps in a process and identify the ones that are most time-consuming and the least productive.
Waste areas include inventory, waiting, overproduction, motion, and defects. To identify areas where improvement can be made, a lean team will map these areas. They may be in the supply chain, in a production area, or throughout the whole process.
Once you've identified the waste, it is time to begin implementing strategies that will eliminate it. These strategies include creating crossfunctional teams, flattening the workload, and teaching your employees multi-skilled. You might want to implement technologies such just-in-time and cellular manufacturing, depending on your business. You can also utilize other lean tools such total productive maintenance or kanban administration.
You can also incorporate a system of standardized containers that allow workers to know exact quantities without counting. Standardized containers allow workers to easily detect whether food or other items are mixed in the products. Safety mats are also available for machine areas. They can trigger an alarm if someone steps on them.
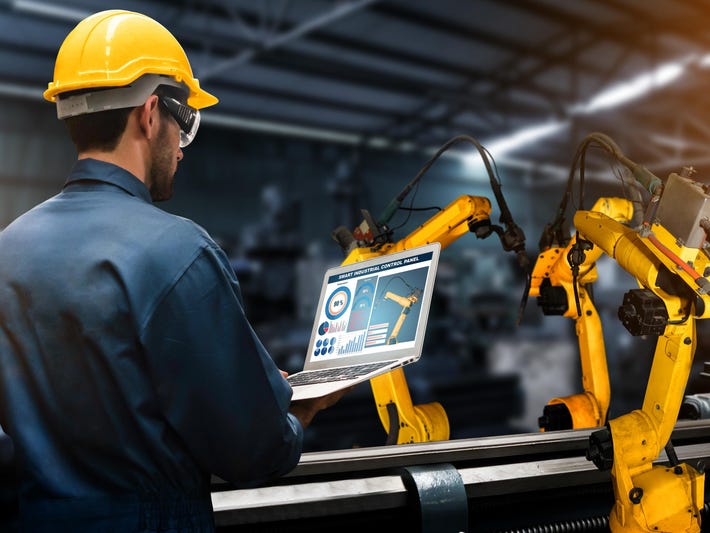
You will need to have a strong organizational culture, as with all lean initiatives. That culture should include an understanding of what the goal of the initiative is, communication skills, and a long-term focus. It is crucial to create a sustainable improvement system in your company for its success.
When you're looking at a new machine, value stream mapping is a great tool. You can create an inventory that includes the future condition of your products, raw materials, and customer needs. You can use this information to better predict when you'll need equipment and supplies. A scheduling system can be created to help you meet your orders on time.
Lean manufacturing is a way to increase efficiency in your business and achieve your goals. There are many lean manufacturing websites that can help you learn more about the available techniques and resources.
FAQ
What is the responsibility of a logistics manager?
Logistics managers are responsible for ensuring that all goods arrive in perfect condition and on time. This is achieved by using their knowledge and experience with the products of the company. He/she should make sure that enough stock is on hand to meet the demands.
What makes a production planner different from a project manger?
The main difference between a production planner and a project manager is that a project manager is usually the person who plans and organizes the entire project, whereas a production planner is mainly involved in the planning stage of the project.
Is automation important for manufacturing?
Automation is essential for both manufacturers and service providers. It allows them provide faster and more efficient services. It reduces human errors and improves productivity, which in turn helps them lower their costs.
What are the four types in manufacturing?
Manufacturing refers the process of turning raw materials into useful products with machines and processes. It includes many different activities like designing, building and testing, packaging, shipping and selling, as well as servicing.
Statistics
- Job #1 is delivering the ordered product according to specifications: color, size, brand, and quantity. (netsuite.com)
- According to the United Nations Industrial Development Organization (UNIDO), China is the top manufacturer worldwide by 2019 output, producing 28.7% of the total global manufacturing output, followed by the United States, Japan, Germany, and India.[52][53] (en.wikipedia.org)
- (2:04) MTO is a production technique wherein products are customized according to customer specifications, and production only starts after an order is received. (oracle.com)
- In the United States, for example, manufacturing makes up 15% of the economic output. (twi-global.com)
- Many factories witnessed a 30% increase in output due to the shift to electric motors. (en.wikipedia.org)
External Links
How To
How to use the Just-In Time Method in Production
Just-in time (JIT), is a process that reduces costs and increases efficiency in business operations. It is a process where you get the right amount of resources at the right moment when they are needed. This means that only what you use is charged to your account. Frederick Taylor first coined this term while working in the early 1900s as a foreman. He saw how overtime was paid to workers for work that was delayed. He then concluded that if he could ensure that workers had enough time to do their job before starting to work, this would improve productivity.
JIT is an acronym that means you need to plan ahead so you don’t waste your money. The entire project should be looked at from start to finish. You need to ensure you have enough resources to tackle any issues that might arise. If you expect problems to arise, you will be able to provide the necessary equipment and personnel to address them. This will prevent you from spending extra money on unnecessary things.
There are several types of JIT techniques:
-
Demand-driven: This type of JIT allows you to order the parts/materials required for your project on a regular basis. This will let you track the amount of material left over after you've used it. This will allow to you estimate the time it will take for more to be produced.
-
Inventory-based : You can stock the materials you need in advance. This allows you to forecast how much you will sell.
-
Project-driven: This method allows you to set aside enough funds for your project. Knowing how much money you have available will help you purchase the correct amount of materials.
-
Resource-based JIT : This is probably the most popular type of JIT. You assign certain resources based off demand. You will, for example, assign more staff to deal with large orders. If you don’t have many orders you will assign less people to the work.
-
Cost-based: This is similar to resource-based, except that here you're not just concerned about how many people you have but how much each person costs.
-
Price-based: This is a variant of cost-based. However, instead of focusing on the individual workers' costs, this looks at the total price of the company.
-
Material-based is an alternative to cost-based. Instead of looking at the total cost in the company, this method focuses on the average amount of raw materials that you consume.
-
Time-based JIT: A variation on resource-based JIT. Instead of focusing only on how much each employee is costing, you should focus on how long it takes to complete your project.
-
Quality-based: This is yet another variation of resource-based JIT. Instead of thinking about how much each employee costs or how long it takes to manufacture something, you think about how good the quality of your product is.
-
Value-based JIT is the newest form of JIT. You don't worry about whether the products work or if they meet customer expectations. Instead, you focus on the added value that you provide to your market.
-
Stock-based is an inventory-based system that measures the number of items produced at any given moment. It is used when production goals are met while inventory is kept to a minimum.
-
Just-in-time planning (JIT): This is a combination JIT and supply-chain management. It refers to the process of scheduling the delivery of components as soon as they are ordered. It's important as it reduces leadtimes and increases throughput.