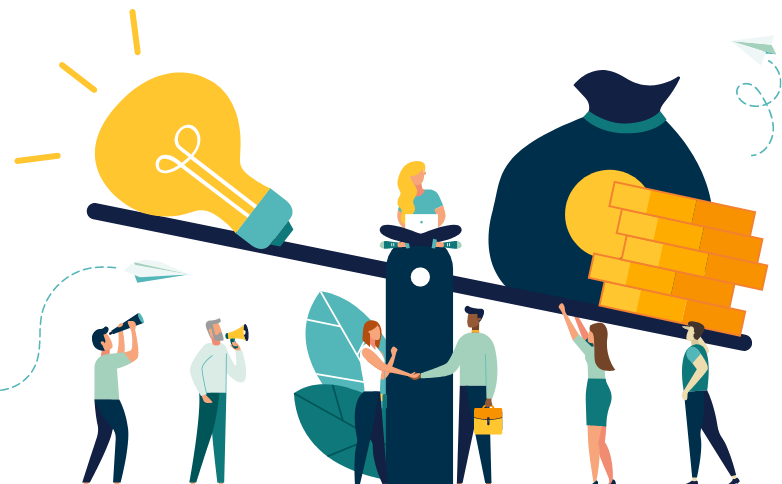
Cost estimates are required for nearly all business activities. This is the job of cost estimators. They are responsible for determining the costs associated with manufacturing and developing new products or services. They also have to determine the cost of building a brand new structure. This includes analysing the labor and materials costs.
Construction companies employ the majority of cost estimators. They are expected to be well-versed in construction processes and methods. They will also need to be familiarized with computer-aided planning (CAD). This software is used for improving the efficiency of design, and manufacturing. The software can also be used to analyze data from databases. They can also utilize other software such as Microsoft Excel.
For accurate cost estimates, cost estimaters work together with other professionals. They assess the project plans, site conditions, and other materials in order to determine the component's cost. Engineers may be involved in determining the dimensions and machining procedures required.

Cost estimators must be detail-oriented, assertive, and dependable. They must be capable of interpreting difficult information. They must be able to communicate clearly and accurately their findings. They must be able communicate effectively with clients or professionals.
Cost estimators usually work in the cost or engineering departments of companies. They should have a solid knowledge of science and math. They should also be comfortable with commercial and CAD software. They might be required to attend a certification program. Certified Cost Estimator/Analysts(CCEA), Professional Estimator/Analysts and Certified Professional Estimators may be required.
Cost estimators could be specialists in specific industries or services. Some individuals specialize in building or construction costs, while others focus on software development costs. Cost estimators could also be employed in other areas like automotive repair and management, building construction, or specialty trade contractors.
These individuals communicate with suppliers, clients, and engineers. They are also proficient in industry terminology. They also develop a large knowledge base before preparing cost estimates. Apart from preparing cost estimates and finding ways to cut costs, many people in this occupation also do studies.
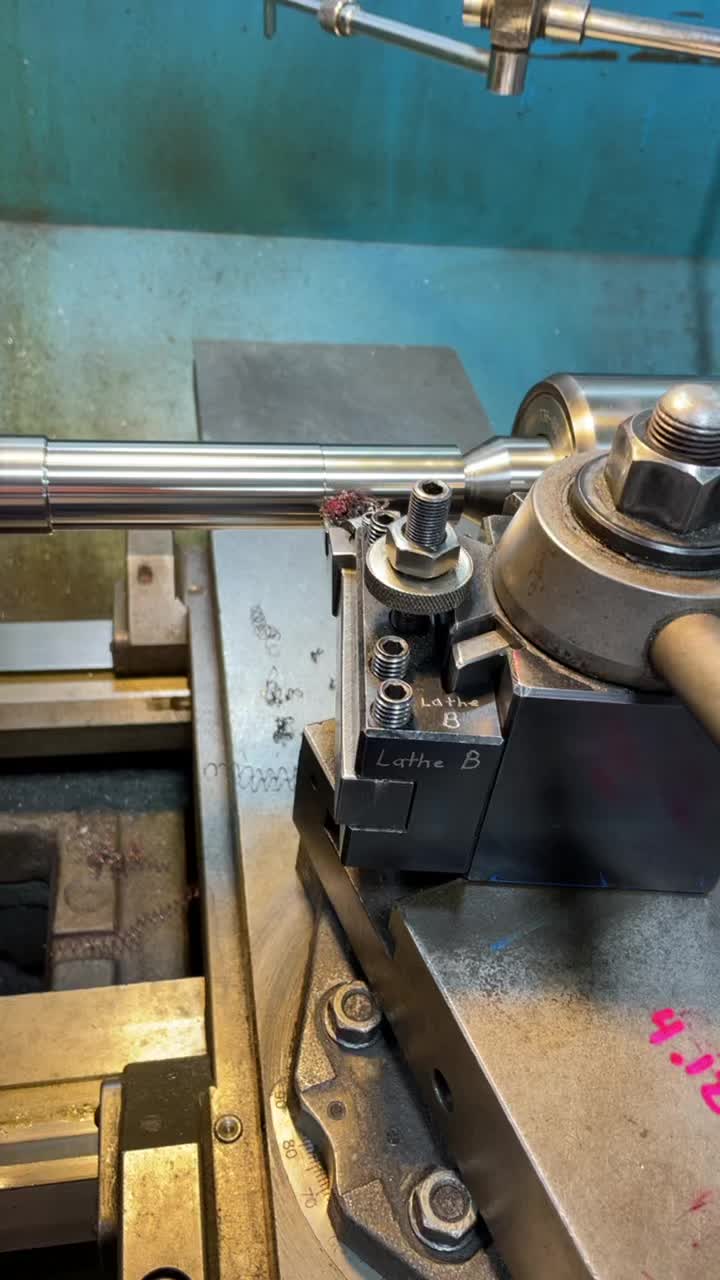
You may need to have a bachelor’s degree depending on your industry. They might also be required to do an internship. They may also be eligible for cooperative education programs. Also, construction companies are more interested in individuals who have a degree that focuses on building construction and/or construction management.
In construction companies and other manufacturing firms, cost estimators are employed. They assist companies in making accurate estimates that will allow them to submit profitable bids. They also analyze data related the supply chain as well as other factors that may affect costs. Government programs can also use cost estimators. They may be asked to design new products or services.
Cost estimators should have a good understanding of computer-aided planning (CAD) software. They can also receive training in automatic cost estimation software.
FAQ
How can I find out more about manufacturing?
The best way to learn about manufacturing is through hands-on experience. You can read books, or watch instructional videos if you don't have the opportunity to do so.
What are the 7 Rs of logistics?
The acronym 7Rs of Logistics refers to the seven core principles of logistics management. It was developed by International Association of Business Logisticians (IABL), and published as part of their "Seven Principles of Logistics Management Series" in 2004.
The acronym consists of the following letters:
-
Responsible – ensure that all actions are legal and don't cause harm to anyone else.
-
Reliable: Have faith in your ability or the ability to honor any promises made.
-
Reasonable - make sure you use your resources well and don't waste them.
-
Realistic - Take into consideration all aspects of operations including cost-effectiveness, environmental impact, and other factors.
-
Respectful: Treat others with fairness and equity
-
Responsive - Look for ways to save time and increase productivity.
-
Recognizable - Provide value-added services to customers
What does the term manufacturing industries mean?
Manufacturing Industries is a group of businesses that produce goods for sale. These products are sold to consumers. These companies use a variety processes such as distribution, retailing and management to accomplish their purpose. They make goods from raw materials with machines and other equipment. This includes all types if manufactured goods.
What skills is required for a production planner?
Being a production planner is not easy. You need to be organized and flexible. It is also important to be able communicate with colleagues and clients.
What is the job of a production plan?
Production planners ensure all aspects of the project are delivered within time and budget. They also ensure the quality of the product and service meets the client's requirements.
What are manufacturing and logistics?
Manufacturing is the process of creating goods from raw materials by using machines and processes. Logistics is the management of all aspects of supply chain activities, including procurement, production planning, distribution, warehousing, inventory control, transportation, and customer service. As a broad term, manufacturing and logistics often refer to both the creation and delivery of products.
Statistics
- [54][55] These are the top 50 countries by the total value of manufacturing output in US dollars for its noted year according to World Bank.[56] (en.wikipedia.org)
- Many factories witnessed a 30% increase in output due to the shift to electric motors. (en.wikipedia.org)
- It's estimated that 10.8% of the U.S. GDP in 2020 was contributed to manufacturing. (investopedia.com)
- In 2021, an estimated 12.1 million Americans work in the manufacturing sector.6 (investopedia.com)
- According to the United Nations Industrial Development Organization (UNIDO), China is the top manufacturer worldwide by 2019 output, producing 28.7% of the total global manufacturing output, followed by the United States, Japan, Germany, and India.[52][53] (en.wikipedia.org)
External Links
How To
How to Use the Just-In-Time Method in Production
Just-in-time (JIT) is a method that is used to reduce costs and maximize efficiency in business processes. It allows you to get the right amount resources at the right time. This means that you only pay for what you actually use. Frederick Taylor, a 1900s foreman, first coined the term. He observed how workers were paid overtime if there were delays in their work. He decided to ensure workers have enough time to do their jobs before starting work to improve productivity.
The idea behind JIT is that you should plan ahead and have everything ready so you don't waste money. Also, you should look at the whole project from start-to-finish and make sure you have the resources necessary to address any issues. You'll be prepared to handle any potential problems if you know in advance. This will ensure that you don't spend more money on things that aren't necessary.
There are many JIT methods.
-
Demand-driven: This JIT is where you place regular orders for the parts/materials that are needed for your project. This will allow to track how much material has been used up. You'll also be able to estimate how long it will take to produce more.
-
Inventory-based: This allows you to store the materials necessary for your projects in advance. This allows you to forecast how much you will sell.
-
Project-driven : This is a method where you make sure that enough money is set aside to pay the project's cost. If you know the amount you require, you can buy the materials you need.
-
Resource-based JIT: This type of JIT is most commonly used. You allocate resources based on the demand. For example, if there is a lot of work coming in, you will have more people assigned to them. If there aren't many orders, you will assign fewer people.
-
Cost-based: This is a similar approach to resource-based but you are not only concerned with how many people you have, but also how much each one costs.
-
Price-based: This approach is very similar to the cost-based method except that you don't look at individual workers costs but the total cost of the company.
-
Material-based - This is a variant of cost-based. But instead of looking at the total company cost, you focus on how much raw material you spend per year.
-
Time-based: This is another variation of resource-based JIT. Instead of focusing solely on the amount each employee costs, focus on how long it takes for the project to be completed.
-
Quality-based JIT: This is another variation of resource based JIT. Instead of worrying about the costs of each employee or how long it takes for something to be made, you should think about how quality your product is.
-
Value-based JIT is the newest form of JIT. In this instance, you are not concerned about the product's performance or meeting customer expectations. Instead, your focus is on the value you bring to the market.
-
Stock-based: This inventory-based approach focuses on how many items are being produced at any one time. This is used to increase production and minimize inventory.
-
Just-intime (JIT), planning is a combination JIT management and supply chain management. It refers to the process of scheduling the delivery of components as soon as they are ordered. This is important as it reduces lead time and increases throughput.