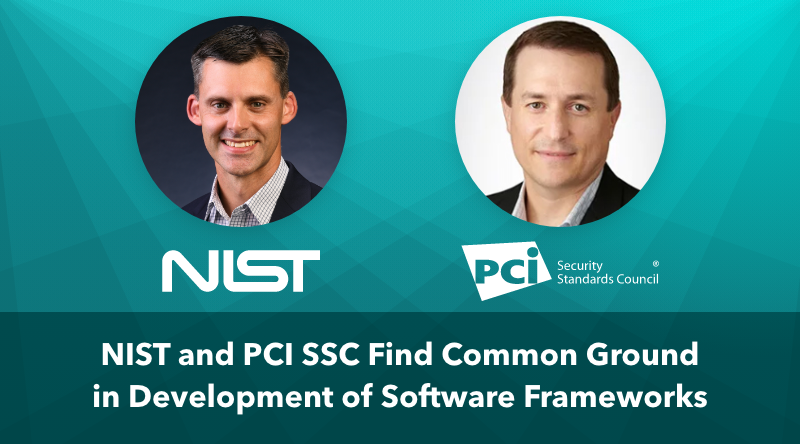
As the Internet of Things transforms manufacturing, cybersecurity is essential for manufacturers. Companies must ensure that their customer information and assets are protected in light of the increasing number of cyberattacks. Companies can stay safe and resilient by utilizing the right technology. You can ensure the safety and security of your industrial equipment with physical security systems that include cameras, locks, access cards, and cameras.
Kaspersky Labs claims that 33% of cybersecurity incidents are directed at manufacturers. These threats are getting more complex and common. These threats can include malware and phishing, as well as ransomware. Protecting intellectual property, designs, products, and formulas is essential for manufacturers. It is also crucial to have a strategy in place that minimizes cyberattacks.
Cybersecurity is vital for protecting confidential data and information such as customer orders and product specifications. A cybersecurity plan should also identify how to respond to a potential cyber attack, which can cost between $3 and $6 million. Companies are more vulnerable to data breaches, theft, and disruption of production. Keeping up with cyberattacks is a challenge for many manufacturers.
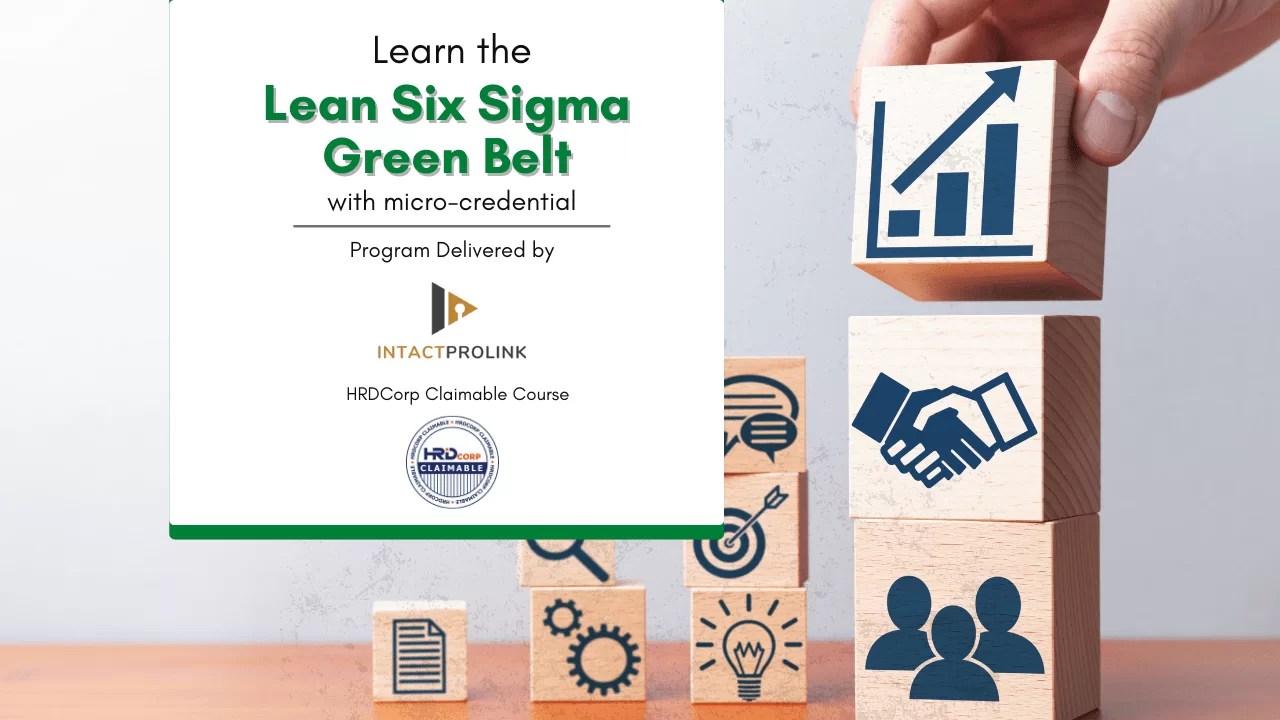
Security for manufacturers is crucial to protect employee and customer data as well the company’s reputation and revenue. It is crucial to perform a thorough audit of all your systems in order to find vulnerabilities and assess your overall readiness.
For help and resources, contact your local Manufacturing Executive Program center. Get expert advice about how to keep your business safe from cyberattacks.
In addition to conducting an audit of your systems, it's critical to set up a back-up plan. Regular testing of your system is essential to make sure it functions as intended. You can lower the chance of an attack by creating hard copies of key documents, and setting up a process to test the effectiveness of your system.
Many manufacturers haven't implemented cybersecurity measures, including data standards. Nearly half of OEMs use outdated or non-compliant software and hardware. However, digital technology is becoming more popular. Information-related technologies, including networked devices, sensors, cloud computing and networked machines are revolutionizing the industry. While the Internet of Things (IoT) and the increased globalization of the industry have sparked new concerns, a cybersecurity strategy can ensure that your organization is protected.
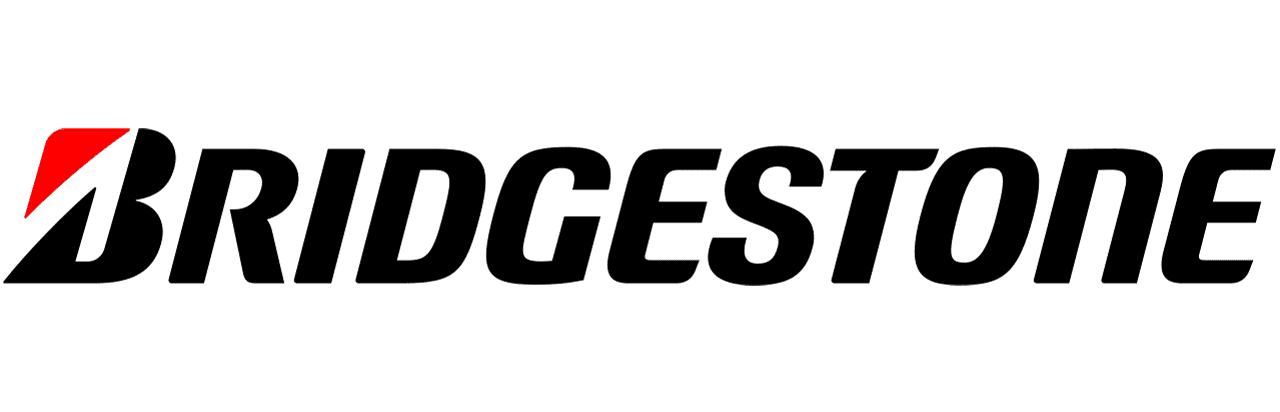
It is essential to understand the specific requirements of each manufacturing industry when designing a cybersecurity plan. For example, global companies with long supply chains have to comply with standards that are specific to their country, region, and partner. However, smaller or medium-sized companies often have more stringent cybersecurity policy. You should have a comprehensive strategy in place to protect your business from cyberattacks, regardless of how big or small you are.
Cybersecurity Framework for Manufacturers is a resource that helps manufacturers to protect their business from cyberattacks. It's available from the National Institute of Standards and Technology. This framework offers a guideline for managing cybersecurity activities across a range of industries, including industrial manufacturing.
FAQ
Can some manufacturing processes be automated?
Yes! Yes. Automation has been around since ancient time. The wheel was invented by the Egyptians thousands of years ago. Today, robots assist in the assembly of lines.
Robotics is used in many manufacturing processes today. These include:
-
Robots for assembly line
-
Robot welding
-
Robot painting
-
Robotics inspection
-
Robots that create products
There are many other examples of how manufacturing could benefit from automation. 3D printing makes it possible to produce custom products in a matter of days or weeks.
What does the term manufacturing industries mean?
Manufacturing Industries refers to businesses that manufacture products. Consumers are those who purchase these products. These companies use various processes such as production, distribution, retailing, management, etc., to fulfill this purpose. They manufacture goods from raw materials using machines and other equipment. This includes all types manufactured goods such as clothing, building materials, furniture, electronics, tools and machinery.
What are the 7 Rs of logistics?
The acronym "7R's" of Logistics stands for seven principles that underpin logistics management. It was published in 2004 by the International Association of Business Logisticians as part of their "Seven Principles of Logistics Management" series.
The acronym is composed of the following letters.
-
Responsible – ensure that all actions are legal and don't cause harm to anyone else.
-
Reliable - You can have confidence that you will fulfill your promises.
-
Reasonable - make sure you use your resources well and don't waste them.
-
Realistic – consider all aspects of operations, from cost-effectiveness to environmental impact.
-
Respectful: Treat others with fairness and equity
-
You are resourceful and look for ways to save money while increasing productivity.
-
Recognizable - provide customers with value-added services.
How does manufacturing avoid bottlenecks in production?
Avoiding production bottlenecks is as simple as keeping all processes running smoothly, from the time an order is received until the product ships.
This includes both quality control and capacity planning.
Continuous improvement techniques like Six Sigma are the best way to achieve this.
Six Sigma is a management method that helps to improve quality and reduce waste.
It emphasizes consistency and eliminating variance in your work.
Statistics
- Job #1 is delivering the ordered product according to specifications: color, size, brand, and quantity. (netsuite.com)
- (2:04) MTO is a production technique wherein products are customized according to customer specifications, and production only starts after an order is received. (oracle.com)
- Many factories witnessed a 30% increase in output due to the shift to electric motors. (en.wikipedia.org)
- In the United States, for example, manufacturing makes up 15% of the economic output. (twi-global.com)
- In 2021, an estimated 12.1 million Americans work in the manufacturing sector.6 (investopedia.com)
External Links
How To
How to Use lean manufacturing in the Production of Goods
Lean manufacturing (or lean manufacturing) is a style of management that aims to increase efficiency, reduce waste and improve performance through continuous improvement. It was developed in Japan between 1970 and 1980 by Taiichi Ohno. TPS founder Kanji Tyoda gave him the Toyota Production System, or TPS award. Michael L. Watkins published the book "The Machine That Changed the World", which was the first to be published about lean manufacturing.
Lean manufacturing refers to a set of principles that improve the quality, speed and costs of products and services. It emphasizes reducing defects and eliminating waste throughout the value chain. Lean manufacturing can be described as just-in–time (JIT), total productive maintenance, zero defect (TPM), or even 5S. Lean manufacturing eliminates non-value-added tasks like inspection, rework, waiting.
Lean manufacturing improves product quality and costs. It also helps companies reach their goals quicker and decreases employee turnover. Lean Manufacturing is one of the most efficient ways to manage the entire value chains, including suppliers and customers as well distributors and retailers. Lean manufacturing practices are widespread in many industries. Toyota's philosophy is the foundation of its success in automotives, electronics and appliances, healthcare, chemical engineers, aerospace, paper and food, among other industries.
Five basic principles of Lean Manufacturing are included in lean manufacturing
-
Define Value- Identify the added value your company brings to society. What makes you stand out from your competitors?
-
Reduce Waste - Remove any activity which doesn't add value to your supply chain.
-
Create Flow - Ensure work moves smoothly through the process without interruption.
-
Standardize & simplify - Make processes consistent and repeatable.
-
Build Relationships- Develop personal relationships with both internal as well as external stakeholders.
Lean manufacturing isn’t new, but it has seen a renewed interest since 2008 due to the global financial crisis. Many companies have adopted lean manufacturing methods to increase their marketability. According to some economists, lean manufacturing could be a significant factor in the economic recovery.
Lean manufacturing has many benefits in the automotive sector. These include better customer satisfaction and lower inventory levels. They also result in lower operating costs.
Lean manufacturing can be applied to almost every aspect of an organization. This is because it ensures efficiency and effectiveness in all stages of the value chain.
There are three main types of lean manufacturing:
-
Just-in Time Manufacturing (JIT), also known as "pull system": This form of lean manufacturing is often referred to simply as "pull". JIT means that components are assembled at the time of use and not manufactured in advance. This approach reduces lead time, increases availability and reduces inventory.
-
Zero Defects Manufacturing (ZDM): ZDM focuses on ensuring that no defective units leave the manufacturing facility. It is better to repair a part than have it removed from the production line if it needs to be fixed. This applies to finished goods that may require minor repairs before shipment.
-
Continuous Improvement (CI): CI aims to improve the efficiency of operations by continuously identifying problems and making changes in order to eliminate or minimize waste. It involves continuous improvement of processes, people, and tools.