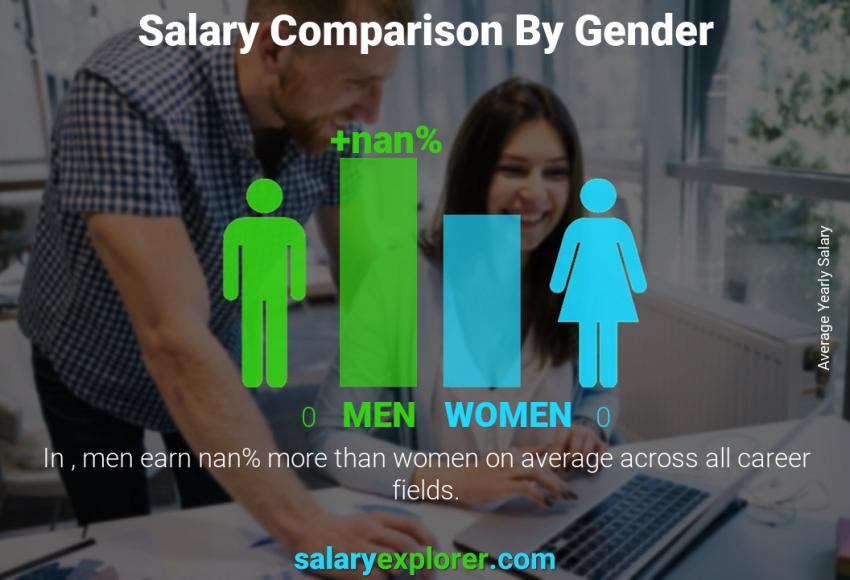
The United States is the third largest country manufacturer in the entire world. Its manufacturing output was almost double that of the Great Recession. Despite the strong domestic economy, the United States' manufacturing industry continues to take a sloppy approach to solving its current problems. We need to be more aggressive when addressing the challenges facing our industry, whether it is because of a lack investment or lack of skilled labor.
In 2000, the number of jobs has fallen by 5,000,000
Five million US manufacturing jobs were lost between 2000 and now. Some believe the increase in trade with China is to blame, but this explains only about a fourth of the decline in manufacturing jobs. Not only was there trade with China, but manufacturing jobs were also lost on local markets that weren't competitive with Chinese imports. But the reasons for the decline in manufacturing jobs are many. The following are some of the reasons:
In the last 20 years, nearly a quarter of the jobs in the US manufacturing industry have been lost. It stood at 17 million in 1965, and fell to just 12 million in 2010. It is not because of trade that manufacturing jobs are declining. Instead, they have been impacted by structural issues - a declines in output, capital investment, productivity and trade deficits. This is not sustainable. While productivity increases played a major part in the decline, these were not enough for the replacement of lost manufacturing jobs. Automation is the problem, not productivity increases.
Strong demand is for manufactured products
The United States has a strong demand for manufactured products despite the fact that consumer spending on these goods has fallen over the past several decades. In 1945, 58% of personal spending on durable goods was made, while it is now only 28%. This is due to the fact that the cost of manufacturing and selling these goods has declined while the content has risen. This has led to a significant drop in the price of computers, TVs, and audio equipment.
The US has seen an increase in manufactured goods production due to the recovery in manufacturing activity. According to the Fifth District Manufacturing Activity Survey (Fifth District Manufacturing Activity Survey), demand is strong for manufactured goods, and production is on the rise. However supply chain bottlenecks are hindering output. The increased production has placed stress on supply chains. Respondents have reported that supply chain disruptions affect their ability maintain adequate inventories. Backlogs of orders and vendor lead times have also increased.
The trade deficit in manufactured products has more than doubled over the past decade
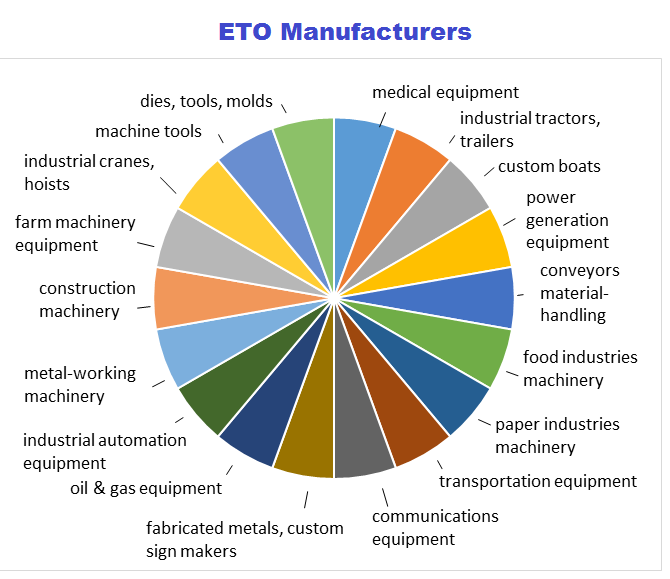
Some economists fear that the U.S.'s trade surplus may lead to lower global economic growth and greater instability among its trading partner. Some argue that the high imports of manufactured goods from the United States are not necessarily bad for its economy. This is essential to maintaining global economic stability. A trade deficit might even be necessary, as the U.S. heavily relies on foreign markets for its economic output. However, high levels of foreign demand could make it more difficult to reach full employment.
Since 2000, the U.S. manufactured goods trade deficit has almost doubled. Partly, this is due to an increase in Chinese imports. But the larger problem is that this imbalance is concentrated in the manufacturing sector, where wages and employment have decreased since the 1990s. US manufacturing jobs have dropped from 26 to 8.5 per cent in 1970, to just 6.5 percent in 2016. Some economists attribute the decline in manufacturing employment to China's increased level of competition. However, most economists attribute the decline primarily to automation, productivity growth, and shifting demand from goods towards services.
Industry adopts a shotgun approach
The US manufacturing industry is well-respected for its advanced manufacturing efforts and has many other initiatives. However, some countries have chosen to bring the internet of everything into manufacturing. The US, on other hand, is focused on different technologies and blends traditional mass media with Internet advertisement. This results in a shotgun approach where companies concentrate on different technologies and seek a wide customer base.
FAQ
What are the differences between these four types?
Manufacturing refers to the transformation of raw materials into useful products by using machines and processes. Manufacturing involves many activities, including designing, building, testing and packaging, shipping, selling, service, and so on.
What skills should a production planner have?
To become a successful production planner, you need to be organized, flexible, and able to multitask. It is also important to be able communicate with colleagues and clients.
How does manufacturing avoid bottlenecks in production?
To avoid production bottlenecks, ensure that all processes run smoothly from the moment you receive your order to the time the product ships.
This includes planning for both capacity requirements and quality control measures.
This can be done by using continuous improvement techniques, such as Six Sigma.
Six Sigma management is a system that improves quality and reduces waste within your organization.
It emphasizes consistency and eliminating variance in your work.
How important is automation in manufacturing?
Not only are service providers and manufacturers important, but so is automation. They can provide services more quickly and efficiently thanks to automation. It reduces human errors and improves productivity, which in turn helps them lower their costs.
Can some manufacturing processes be automated?
Yes! Yes. The Egyptians discovered the wheel thousands and years ago. Robots are now used to assist us in assembly lines.
There are many applications for robotics in manufacturing today. These include:
-
Line robots
-
Robot welding
-
Robot painting
-
Robotics inspection
-
Robots create products
Manufacturing could also benefit from automation in other ways. 3D printing, for example, allows us to create custom products without waiting for them to be made.
Statistics
- In the United States, for example, manufacturing makes up 15% of the economic output. (twi-global.com)
- [54][55] These are the top 50 countries by the total value of manufacturing output in US dollars for its noted year according to World Bank.[56] (en.wikipedia.org)
- In 2021, an estimated 12.1 million Americans work in the manufacturing sector.6 (investopedia.com)
- Job #1 is delivering the ordered product according to specifications: color, size, brand, and quantity. (netsuite.com)
- According to the United Nations Industrial Development Organization (UNIDO), China is the top manufacturer worldwide by 2019 output, producing 28.7% of the total global manufacturing output, followed by the United States, Japan, Germany, and India.[52][53] (en.wikipedia.org)
External Links
How To
How to Use Lean Manufacturing in the Production of Goods
Lean manufacturing is an approach to management that aims for efficiency and waste reduction. It was created in Japan by Taiichi Ohno during the 1970s and 80s. He received the Toyota Production System award (TPS), from Kanji Toyoda, founder of TPS. Michael L. Watkins published the original book on lean manufacturing, "The Machine That Changed the World," in 1990.
Lean manufacturing refers to a set of principles that improve the quality, speed and costs of products and services. It emphasizes the elimination of defects and waste throughout the value stream. Just-in-time (JIT), zero defect (TPM), and 5S are all examples of lean manufacturing. Lean manufacturing emphasizes reducing non-value-added activities like inspection, rework and waiting.
In addition to improving product quality and reducing costs, lean manufacturing helps companies achieve their goals faster and reduces employee turnover. Lean manufacturing is considered one of the most effective ways to manage the entire value chain, including suppliers, customers, distributors, retailers, and employees. Lean manufacturing is widely used in many industries. Toyota's philosophy has been a key driver of success in many industries, including automobiles and electronics.
Five fundamental principles underlie lean manufacturing.
-
Define Value - Identify the value your business adds to society and what makes you different from competitors.
-
Reduce waste - Get rid of any activity that does not add value to the supply chain.
-
Create Flow - Make sure work runs smoothly without interruptions.
-
Standardize & Simplify - Make processes as consistent and repeatable as possible.
-
Build Relationships- Develop personal relationships with both internal as well as external stakeholders.
Although lean manufacturing has always been around, it is gaining popularity in recent years because of a renewed interest for the economy after 2008's global financial crisis. Many businesses have adopted lean production techniques to make them more competitive. Some economists even believe that lean manufacturing can be a key factor in economic recovery.
Lean manufacturing has many benefits in the automotive sector. These include higher customer satisfaction, lower inventory levels, lower operating expenses, greater productivity, and improved overall safety.
It can be applied to any aspect of an organisation. However, it is particularly useful when applied to the production side of an organization because it ensures that all steps in the value chain are efficient and effective.
There are three main types in lean manufacturing
-
Just-in Time Manufacturing, (JIT): This kind of lean manufacturing is also commonly known as "pull-systems." JIT stands for a system where components are assembled on the spot rather than being made in advance. This approach aims to reduce lead times, increase the availability of parts, and reduce inventory.
-
Zero Defects Manufacturing (ZDM),: ZDM is a system that ensures no defective units are left the manufacturing facility. If a part needs to be fixed during the assembly line, it should be repaired rather than scrapped. This applies to finished goods that may require minor repairs before shipment.
-
Continuous Improvement (CI),: Continuous improvement aims improve the efficiency and effectiveness of operations by continuously identifying issues and making changes to reduce waste. It involves continuous improvement of processes, people, and tools.