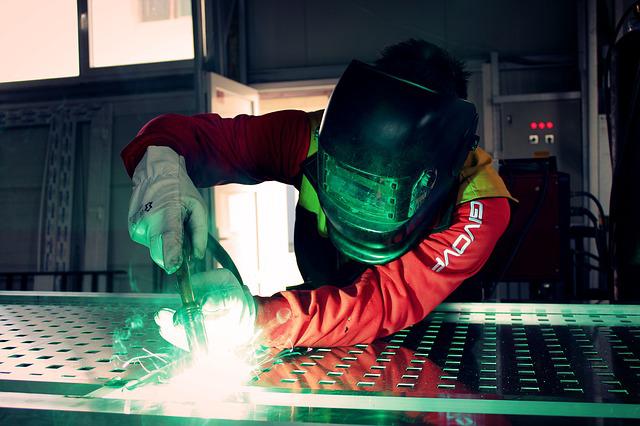
Founded in 2003 in Loveland, Ohio, Supply Dynamics is a multi-enterprise supply chain analytics suite. It offers technology solutions to manufacturers in highly distributed manufacturing environments. Supply Dynamics collaborates closely with the Navy's Defense Logistics Agency. It provides visibility and control of an organization's end-to-end supply chain. It assists manufacturers in planning production and reducing the cost of raw material. Supply Dynamics works with a number of industries including aerospace and defense manufacturing as well as transportation.
Dynamics 365 Supply Chain Management is a Microsoft Cloud solution that enables companies to improve operational efficiency as well as streamline production. It also helps them build strong supply chains. It offers unmatched visibility and flexibility into the supply chain. Its modules enable customers to have complete product lifecycle functionality.
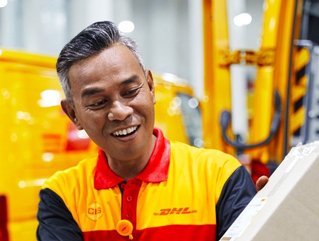
The Dynamics Supply Chain module allows users to create items for discrete or process manufacturing, submit RFQs and test product quality before submitting purchase orders. Gantt charts are also available to give transparency to all operations. The Visual Supply Schedule allows users to see a forecast for inventory levels, anticipated supply, and demand. They can also adjust schedules when supply chain issues arise. It allows managers to monitor the progress of job functions across different areas of a production floor.
Microsoft Dynamics 365 Supply Chain Management allows organizations to use a single, predictive and unified way to manage customer demand. It also ensures that the right materials arrive at the right time. It also helps businesses anticipate customer demands and changes in capacity. It can be used on multiple sites and warehouses, and integrates logistics purchasing and production. It also supports vendor-specific pricing, multiple inventory costing methods, and transportation management. The solution also supports the use of inventory optimization and predictive analytics, as well as AI features.
Dynamics 365 provides self-service to suppliers. Suppliers can accept and decline purchase orders, send invoices for POs, or enter shipment information to existing POs. It supports many inventory costing options, including vendor-specific pricing as well as item-level and item group pricing. You can also create an inventory allocation plan and other inventory optimization features.
Supply Dynamics offers unique benchmarking solutions for metals prices. With this technology, manufacturers are able to respond quicker to fluctuations in marketplace prices. They can also anticipate fluctuations in manufacturing costs and forecast them. This technology is able to reduce raw material costs, which in turn reduces waste. It also provides manufacturers with a blueprint for the bill-of-material data conversion process.
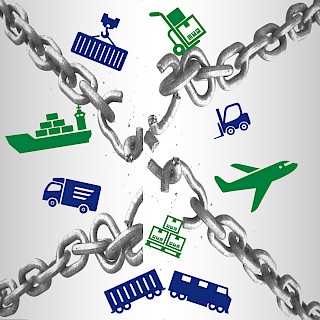
The master planning function automates the creation and processing of Production Orders that are based on open Purchase Orders. It also includes an optimization add-in, which allows users to anticipate changes in customer demand. The AI capabilities of the program can help improve the flow in goods distribution. The Dynamics Supply Chain Management platform is certified by Microsoft, making it a great solution for companies seeking to build a strong supply chain.
FAQ
What does manufacturing industry mean?
Manufacturing Industries refers to businesses that manufacture products. The people who buy these products are called consumers. These companies use a variety processes such as distribution, retailing and management to accomplish their purpose. They manufacture goods from raw materials using machines and other equipment. This includes all types and varieties of manufactured goods, such as food items, clothings, building supplies, furnitures, toys, electronics tools, machinery vehicles, pharmaceuticals medical devices, chemicals, among others.
Why automate your warehouse
Modern warehousing is becoming more automated. E-commerce has increased the demand for quicker delivery times and more efficient processes.
Warehouses should be able adapt quickly to new needs. In order to do this, they need to invest in technology. Automation warehouses can bring many benefits. Here are some of the reasons automation is worth your investment:
-
Increases throughput/productivity
-
Reduces errors
-
Increases accuracy
-
Boosts safety
-
Eliminates bottlenecks
-
This allows companies to scale easily
-
Makes workers more efficient
-
Gives you visibility into all that is happening in your warehouse
-
Enhances customer experience
-
Improves employee satisfaction
-
Reducing downtime and increasing uptime
-
High quality products delivered on-time
-
Removing human error
-
Assure compliance with regulations
What is production plan?
Production planning is the process of creating a plan that covers all aspects of production. This includes scheduling, budgeting and crew, location, equipment, props, and more. This document ensures that everything is prepared and available when you are ready for shooting. This document should include information about how to achieve the best results on-set. This includes location information, crew details, equipment specifications, and casting lists.
The first step is to decide what you want. You may have already decided where you would like to shoot, or maybe there are specific locations or sets that you want to use. Once you have identified your locations and scenes, you can start working out which elements you require for each scene. For example, you might decide that you need a car but don't know exactly what model you want. In this case, you could start looking up cars online to find out what models are available and then narrow your choices by choosing between different makes and models.
After you have selected the car you want, you can begin to think about additional features. Do you have people who need to be seated in the front seat? Or perhaps you need someone walking around the back of the car? Maybe you want to change the interior color from black to white? These questions can help you decide the right look for your car. Also, think about what kind of shots you would like to capture. What type of shots will you choose? Maybe you want to show your engine or the steering wheel. These factors will help you determine which car style you want to film.
Once you have established all the details, you can create a schedule. You will know when you should start and when you should finish shooting. A schedule for each day will detail when you should arrive at the location and when you need leave. This way, everyone knows what they need to do and when. It is possible to make arrangements in advance for additional staff if you are looking to hire. You don't want to hire someone who won't show up because he didn't know.
You will need to factor in the days that you have to film when creating your schedule. Some projects only take one or two days, while others may last weeks. When you are creating your schedule, you should always keep in mind whether you need more than one shot per day or not. Shooting multiple takes over the same location will increase costs and take longer to complete. If you are unsure if you need multiple takes, it is better to err on the side of caution and shoot fewer takes rather than risk wasting money.
Budgeting is another crucial aspect of production plan. It is important to set a realistic budget so you can work within your budget. Keep in mind that you can always reduce your budget if you face unexpected difficulties. However, you shouldn't overestimate the amount of money you will spend. You will end up spending less money if you underestimate the cost of something.
Planning production is a tedious process. Once you have a good understanding of how everything works together, planning future projects becomes easy.
How can excess manufacturing production be reduced?
Improved inventory management is the key to reducing overproduction. This would reduce time spent on activities such as purchasing, stocking, and maintaining excess stock. This would allow us to use our resources for more productive tasks.
A Kanban system is one way to achieve this. A Kanban Board is a visual display that tracks work progress. Kanban systems allow work items to move through different states until they reach their final destination. Each state is assigned a different priority.
For instance, when work moves from one stage to another, the current task is complete enough to be moved to the next stage. A task that is still in the initial stages of a process will be considered complete until it moves on to the next stage.
This helps to keep work moving forward while ensuring that no work is left behind. Managers can see how much work has been done and the status of each task at any time with a Kanban Board. This information allows managers to adjust their workflow based off real-time data.
Lean manufacturing, another method to control inventory levels, is also an option. Lean manufacturing seeks to eliminate waste from every step of the production cycle. Anything that does nothing to add value to a product is waste. The following are examples of common waste types:
-
Overproduction
-
Inventory
-
Unnecessary packaging
-
Overstock materials
By implementing these ideas, manufacturers can improve efficiency and cut costs.
What is the difference between a production planner and a project manager?
The major difference between a Production Planner and a Project Manager is that a Project Manager is often the person responsible for organizing and planning the entire project. While a Production Planner is involved mainly in the planning stage,
Statistics
- It's estimated that 10.8% of the U.S. GDP in 2020 was contributed to manufacturing. (investopedia.com)
- Job #1 is delivering the ordered product according to specifications: color, size, brand, and quantity. (netsuite.com)
- (2:04) MTO is a production technique wherein products are customized according to customer specifications, and production only starts after an order is received. (oracle.com)
- According to a Statista study, U.S. businesses spent $1.63 trillion on logistics in 2019, moving goods from origin to end user through various supply chain network segments. (netsuite.com)
- [54][55] These are the top 50 countries by the total value of manufacturing output in US dollars for its noted year according to World Bank.[56] (en.wikipedia.org)
External Links
How To
How to Use Just-In-Time Production
Just-intime (JIT), which is a method to minimize costs and maximize efficiency in business process, is one way. It allows you to get the right amount resources at the right time. This means that you only pay for what you actually use. Frederick Taylor was the first to coin this term. He developed it while working as a foreman during the early 1900s. He saw how overtime was paid to workers for work that was delayed. He decided that workers would be more productive if they had enough time to complete their work before they started to work.
JIT teaches you to plan ahead and prepare everything so you don’t waste time. Look at your entire project, from start to end. Make sure you have enough resources in place to deal with any unexpected problems. You'll be prepared to handle any potential problems if you know in advance. You won't have to pay more for unnecessary items.
There are many types of JIT methods.
-
Demand-driven: This is a type of JIT where you order the parts/materials needed for your project regularly. This will allow for you to track the material that you have left after using it. You'll also be able to estimate how long it will take to produce more.
-
Inventory-based: This allows you to store the materials necessary for your projects in advance. This allows you to forecast how much you will sell.
-
Project-driven: This means that you have enough money to pay for your project. When you know how much you need, you'll purchase the appropriate amount of materials.
-
Resource-based JIT is the most widespread form. This is where you assign resources based upon demand. If you have many orders, you will assign more people to manage them. You'll have fewer orders if you have fewer.
-
Cost-based: This is the same as resource-based except that you don't care how many people there are but how much each one of them costs.
-
Price-based pricing: This is similar in concept to cost-based but instead you look at how much each worker costs, it looks at the overall company's price.
-
Material-based: This is very similar to cost-based but instead of looking at total costs of the company you are concerned with how many raw materials you use on an average.
-
Time-based: This is another variation of resource-based JIT. Instead of focusing solely on the amount each employee costs, focus on how long it takes for the project to be completed.
-
Quality-based JIT: This is another variation of resource based JIT. Instead of thinking about the cost of each employee or the time it takes to produce something, you focus on how good your product quality.
-
Value-based JIT is the newest form of JIT. In this scenario, you're not concerned about how products perform or whether customers expect them to meet their expectations. Instead, you focus on the added value that you provide to your market.
-
Stock-based is an inventory-based system that measures the number of items produced at any given moment. This method is useful when you want to increase production while decreasing inventory.
-
Just-intime (JIT), planning is a combination JIT management and supply chain management. It is the process that schedules the delivery of components within a short time of their order. It's important as it reduces leadtimes and increases throughput.