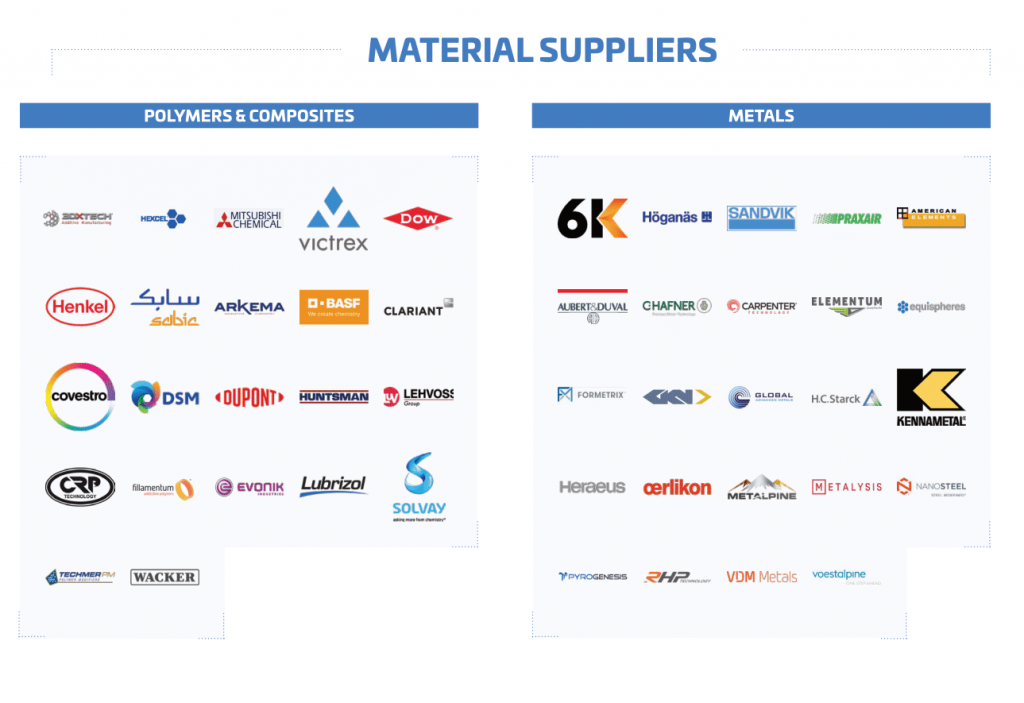
Additive manufacture is a technique for manufacturing which uses digital files. It creates parts, objects, and whole systems. This allows companies to make complex machinery and other devices at a relatively low cost. This process can also be used to reduce production costs and speed up the time to market. This is possible because the process does not require casting or forging or any other traditional methods of production.
The benefits of additive manufacturing extend beyond manufacturers, suppliers, and communities. Customers who can afford innovative products also reap the benefits of additive manufacturing. Several Fortune 500 companies have adopted 3D printing technologies. Biden Administration launched a new initiative to assist small and medium-sized manufacturers in adopting additive production.
AM Forward is a public-private initiative that aims to encourage the use of additive manufacturing by developing standards and common practices, establishing an open-market for additive-manufactured parts, and addressing supply chain issues. The five leading U.S. companies are General Electric Aviation (GEA), Honeywell, Lockheed Martin (Lockheed Martin), Raytheon and Siemens Energy. These firms are partnering with the DOE Manufacturing Demonstration Facility at Oak Ridge National Laboratory, which is a national facility that provides access to a range of additive-manufacturing technologies.
OEMs will use the AM Forward agreement to find technical solutions to industry problems, collaborate with other firms and create standard specifications, as well as offer technical support to U.S.-based suppliers. The initiative is expected to be extended to other large companies in the coming years.
One of the major players involved in AM Forward is the NEO Additive Manufacturing Cluster of Ohio, which works to accelerate the adoption of additive-manufacturing technologies. Ohio has a solid base of skilled engineers and scientists making it an ideal place for additive manufacturing businesses.
America Makes is another important participant. This program partners with academia, industry, economic development resources, and workforce training programs to encourage the adoption of additive-manufacturing by a wide range of sectors. Many university programs now exist for additive-manufacturing.
Additional government programs exist to encourage the adoption or additive manufacturing. These include the Manufacturing Extension Partnership. Small manufacturers can also get technical support and financing from the Department of Labor.
Many of these programs are designed to help overcome common market failures. Many of these programs help overcome common market failures. Similarly, some customers may not be willing to commit to purchasing from companies that invest in additive-manufacturing technologies.
Some of the most innovative additive-manufacturing firms in the country are located in Ohio. Desktop Metal is an industrial additive-manufacturing company that offers metal 3-D printing and machining services to manufacturers and designers. Jonco Industries, Inc. offers a range of fabrication services, such as rapid prototyping, design and prototyping, and high volume surface finishing. PostPro3D specializes in automated surface finishing.
Besides collaborating with the Federal Government, other industry organizations are working to increase the adoption of additive-manufacturing. The Fraunhofer Institute is a leading institution for the development of additive-manufacturing technology.
FAQ
What are the 7 R's of logistics?
The acronym 7R's of Logistic is an acronym that stands for seven fundamental principles of logistics management. It was published in 2004 by the International Association of Business Logisticians as part of their "Seven Principles of Logistics Management" series.
The acronym consists of the following letters:
-
Responsible - to ensure that all actions are within the legal requirements and are not detrimental to others.
-
Reliable: Have faith in your ability or the ability to honor any promises made.
-
It is reasonable to use resources efficiently and not waste them.
-
Realistic - Take into consideration all aspects of operations including cost-effectiveness, environmental impact, and other factors.
-
Respectful - Treat people fairly and equitably
-
Be resourceful: Look for opportunities to save money or increase productivity.
-
Recognizable is a company that provides customers with value-added solutions.
What skills should a production planner have?
You must be flexible and organized to become a productive production planner. Communication skills are essential to ensure that you can communicate effectively with clients, colleagues, and customers.
How is a production manager different from a producer planner?
The major difference between a Production Planner and a Project Manager is that a Project Manager is often the person responsible for organizing and planning the entire project. While a Production Planner is involved mainly in the planning stage,
Why is logistics so important in manufacturing?
Logistics are an essential part of any business. They enable you to achieve outstanding results by helping manage product flow from raw materials through to finished goods.
Logistics also play a major role in reducing costs and increasing efficiency.
Statistics
- Job #1 is delivering the ordered product according to specifications: color, size, brand, and quantity. (netsuite.com)
- According to the United Nations Industrial Development Organization (UNIDO), China is the top manufacturer worldwide by 2019 output, producing 28.7% of the total global manufacturing output, followed by the United States, Japan, Germany, and India.[52][53] (en.wikipedia.org)
- It's estimated that 10.8% of the U.S. GDP in 2020 was contributed to manufacturing. (investopedia.com)
- In 2021, an estimated 12.1 million Americans work in the manufacturing sector.6 (investopedia.com)
- You can multiply the result by 100 to get the total percent of monthly overhead. (investopedia.com)
External Links
How To
Six Sigma and Manufacturing
Six Sigma refers to "the application and control of statistical processes (SPC) techniques in order to achieve continuous improvement." It was developed by Motorola's Quality Improvement Department at their plant in Tokyo, Japan, in 1986. Six Sigma's core idea is to improve the quality of processes by standardizing and eliminating defects. This method has been adopted by many companies in recent years as they believe there are no perfect products or services. Six Sigma's main objective is to reduce variations from the production average. This means that if you take a sample of your product, then measure its performance against the average, you can find out what percentage of the time the process deviates from the norm. If there is a significant deviation from the norm, you will know that something needs to change.
Understanding how variability works in your company is the first step to Six Sigma. Once you have a good understanding of the basics, you can identify potential sources of variation. It is important to identify whether the variations are random or systemic. Random variations occur when people do mistakes. Symmetrical variations are caused due to factors beyond the process. Random variations would include, for example, the failure of some widgets to fall from the assembly line. If however, you notice that each time you assemble a widget it falls apart in exactly the same spot, that is a problem.
Once you have identified the problem, you can design solutions. The solution could involve changing how you do things, or redesigning your entire process. Test them again once you've implemented the changes. If they didn't work, then you'll need to go back to the drawing board and come up with another plan.