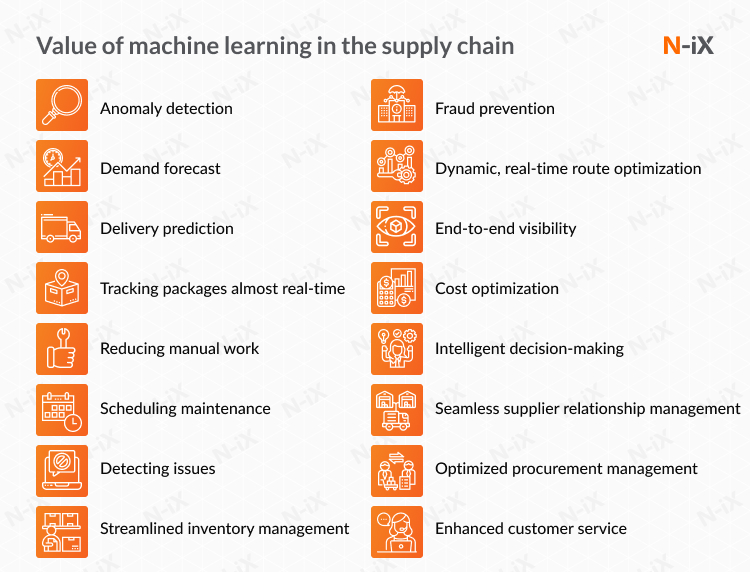
A material manager oversees the purchasing and delivery of materials. They are usually involved in inventory management or raw material management. They are able to identify the different raw materials needed to create a product. They should be resourceful in locating these materials. To get the best price, and delivery rate, they need to have good working relationships with vendors. Materials managers also earn a significant salary. Here are some tips that will help you get the job.
Job description
The materials manager manages stock and purchasing. He or she must have a thorough understanding of stock management and excellent problem-solving skills. A material manager's job involves managing inventory, budgets and efficiencies. Besides managing inventory, this position also has to coordinate the supply chain and supervise subordinates. For this job, an advanced degree is necessary. A materials manager must have had experience in a similar role.
Materials managers typically have a bachelor's in business administration or a related field. A master's degree in the same field is helpful if the position calls for a supervisor. An advanced degree is not always more valuable than on-the-job experience. However, education is a plus. To be eligible for a management position, a materials supervisor must have at most three years of experience in the manufacturing and industrial sectors.
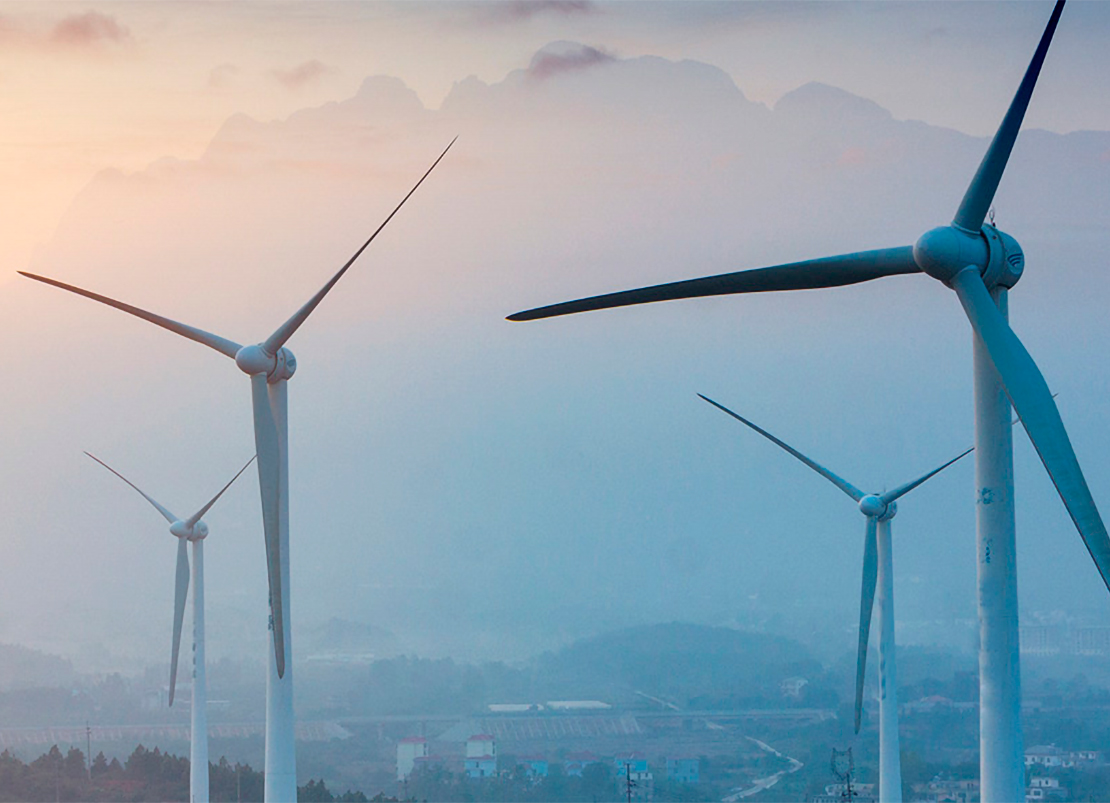
Responsibilities
Materials managers' role is to assess existing projects and decide what materials are needed to make finished products. The materials manager is responsible for keeping track of inventory and stocking spare parts for repairs to faulty products. He or she may also be responsible in training employees about the proper use of inventory management systems. These positions are crucial in many companies but do not require extensive training.
Job Description: A material supervisor oversees the procurement of materials to a company. A material manager oversees the procurement of materials for a company. Experience in logistics, inventory control, supply chain management and logistics are required for this job. Those with experience in these areas will have an advantage. They will also collaborate with the vendors, purchasing and production departments to identify requirements and plan distribution. These positions require a bachelor's degree in business, and a strong analytical mind.
Education required
You should know the education requirements for a career in material management. This position requires excellent management skills as well as a thorough understanding of logistics. As a material manager you will collaborate with QC staff and other managers. Plan functions and delegating to subordinates are some of the job duties. You should be able assess the performance of subordinates and foster harmonious working relationships.
Materials managers typically have a bachelor's degree in a related field. In addition, some companies require two to three years of experience as a material manager before hiring someone with that educational background. Higher-ranking positions may require more education. Many material managers hold certifications, such as those offered by the American Purchasing Society (CPSCP) and the APICS (the Association of Purchasing Professionals).
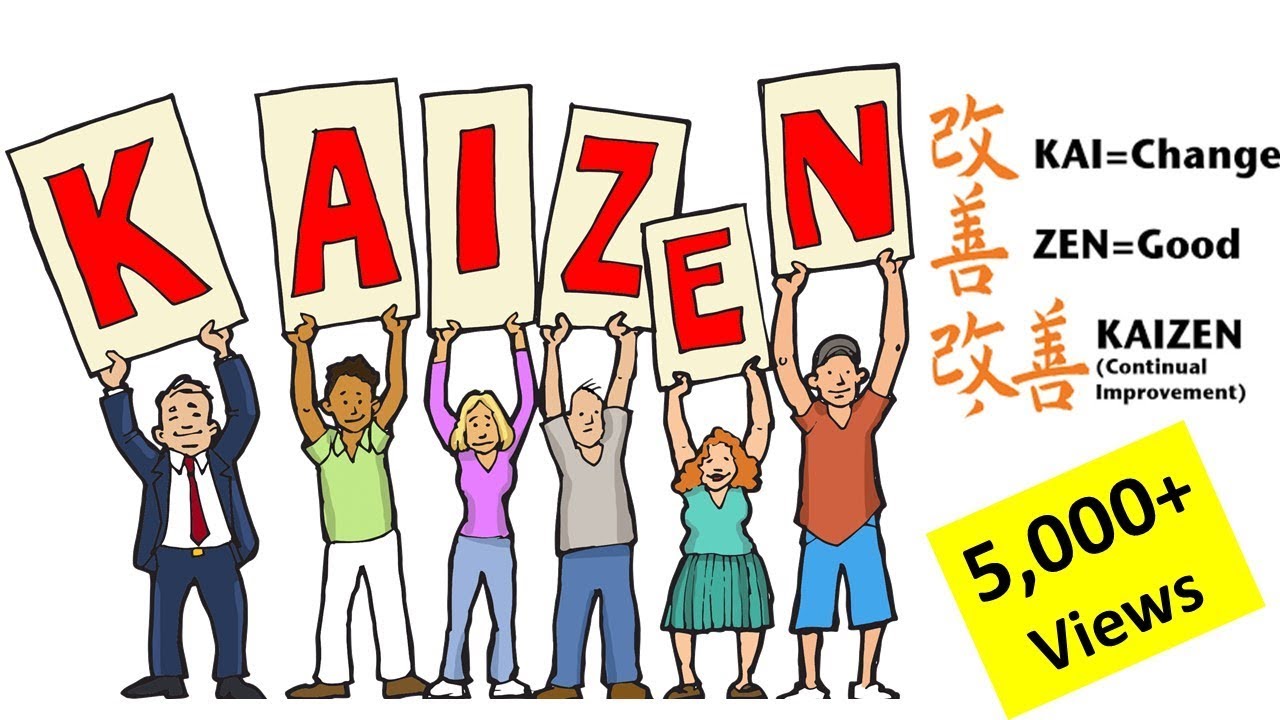
Salary
A Materials Manager's average annual salary is $78,500. This is based upon 106 TurboTax users salaries. It includes taxable wages, tips, and bonuses. The exact salary will vary depending on education and experience. Salary data is adjusted to reflect inflation each year. You can read the following to learn about the average salary for a Materials Manager job.
To become a materials manager, you'll need to have a background in management. A good knowledge of logistics, receiving and shipping is essential. A good understanding of the industry you wish to work in is essential if you work in the manufacturing sector. This will allow you to negotiate the best price with suppliers. A materials manager's salary will likely depend on the type of experience and training they have.
FAQ
How does a Production Planner differ from a Project Manager?
The primary difference between a producer planner and a manager of a project is that the manager usually plans and organizes the whole project, while a production planner is only involved in the planning stage.
What does warehouse refer to?
A warehouse is an area where goods are stored before being sold. It can be indoors or out. It could be one or both.
Why is logistics important for manufacturing?
Logistics are an essential part of any business. They help you achieve great results by helping you manage all aspects of product flow, from raw materials to finished goods.
Logistics also play a major role in reducing costs and increasing efficiency.
What are the 7 R's of logistics?
The acronym 7Rs of Logistics refers to the seven core principles of logistics management. It was published in 2004 by the International Association of Business Logisticians as part of their "Seven Principles of Logistics Management" series.
The acronym is composed of the following letters.
-
Responsible - ensure that all actions taken are within legal requirements and are not harmful to others.
-
Reliable – have faith in your ability and capability to keep promises.
-
Use resources effectively and sparingly.
-
Realistic – consider all aspects of operations, from cost-effectiveness to environmental impact.
-
Respectful - treat people fairly and equitably.
-
Be resourceful: Look for opportunities to save money or increase productivity.
-
Recognizable - provide customers with value-added services.
What is the responsibility of a logistics manager?
Logistics managers are responsible for ensuring that all goods arrive in perfect condition and on time. This is done by using his/her experience and knowledge of the company's products. He/she should ensure that sufficient stock is available in order to meet customer demand.
Statistics
- In the United States, for example, manufacturing makes up 15% of the economic output. (twi-global.com)
- It's estimated that 10.8% of the U.S. GDP in 2020 was contributed to manufacturing. (investopedia.com)
- In 2021, an estimated 12.1 million Americans work in the manufacturing sector.6 (investopedia.com)
- According to the United Nations Industrial Development Organization (UNIDO), China is the top manufacturer worldwide by 2019 output, producing 28.7% of the total global manufacturing output, followed by the United States, Japan, Germany, and India.[52][53] (en.wikipedia.org)
- You can multiply the result by 100 to get the total percent of monthly overhead. (investopedia.com)
External Links
How To
How to Use the Just In Time Method in Production
Just-in time (JIT), is a process that reduces costs and increases efficiency in business operations. It's the process of obtaining the right amount and timing of resources when you need them. This means that you only pay for what you actually use. The term was first coined by Frederick Taylor, who developed his theory while working as a foreman in the early 1900s. Taylor observed that overtime was paid to workers if they were late in working. He decided that workers would be more productive if they had enough time to complete their work before they started to work.
JIT is a way to plan ahead and make sure you don't waste any money. Look at your entire project, from start to end. Make sure you have enough resources in place to deal with any unexpected problems. If you anticipate that there might be problems, you'll have enough people and equipment to fix them. This way you won't be spending more on things that aren’t really needed.
There are several types of JIT techniques:
-
Demand-driven: This type of JIT allows you to order the parts/materials required for your project on a regular basis. This will allow for you to track the material that you have left after using it. It will also allow you to predict how long it takes to produce more.
-
Inventory-based: This type allows you to stock the materials needed for your projects ahead of time. This allows for you to anticipate how much you can sell.
-
Project-driven: This means that you have enough money to pay for your project. If you know the amount you require, you can buy the materials you need.
-
Resource-based JIT: This is the most popular form of JIT. Here you can allocate certain resources based purely on demand. You might assign more people to help with orders if there are many. If there aren't many orders, you will assign fewer people.
-
Cost-based: This is a similar approach to resource-based but you are not only concerned with how many people you have, but also how much each one costs.
-
Price-based: This is very similar to cost-based, except that instead of looking at how much each individual worker costs, you look at the overall price of the company.
-
Material-based: This is very similar to cost-based but instead of looking at total costs of the company you are concerned with how many raw materials you use on an average.
-
Time-based JIT is another form of resource-based JIT. Instead of focusing on the cost of each employee, you will focus on the time it takes to complete a project.
-
Quality-based JIT is another variant of resource-based JIT. Instead of worrying about the costs of each employee or how long it takes for something to be made, you should think about how quality your product is.
-
Value-based JIT is the newest form of JIT. In this instance, you are not concerned about the product's performance or meeting customer expectations. Instead, your goal is to add value to the market.
-
Stock-based is an inventory-based system that measures the number of items produced at any given moment. This is used to increase production and minimize inventory.
-
Just-in-time (JIT) planning: This is a combination of JIT and supply chain management. This refers to the scheduling of the delivery of components as soon after they are ordered. It's important because it reduces lead times and increases throughput.