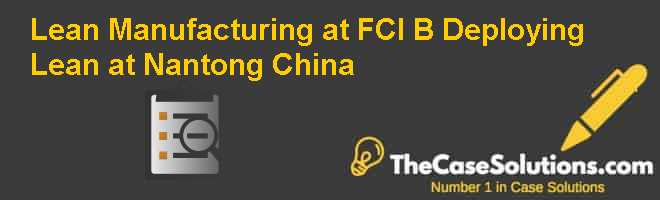
The core qualifications section is essential when writing your environmental engineer job description. This will set out the minimum requirements required for the job in order to attract qualified candidates. These requirements will make it easier to recruit and prevent applicants from being underqualified. It is also beneficial to include a skills section in order to make the hiring process as easy as possible. For more information, please read on. To distinguish the position from others, it is important that this job description be written in a formal, professional tone.
Qualifications
If you're considering changing careers to become an environmental engineer, you should know the details of the job. This position requires you to plan and implement systems to control air, water, and remediate site. This position can often require collaboration with other professionals like environmental specialists or hazardous waste technicians. The role of environmental engineers is to provide technical support in environmental litigation, and for remediation projects. They are also responsible for monitoring progress in environmental improvement programs and contributing to the creation of environmental journals.
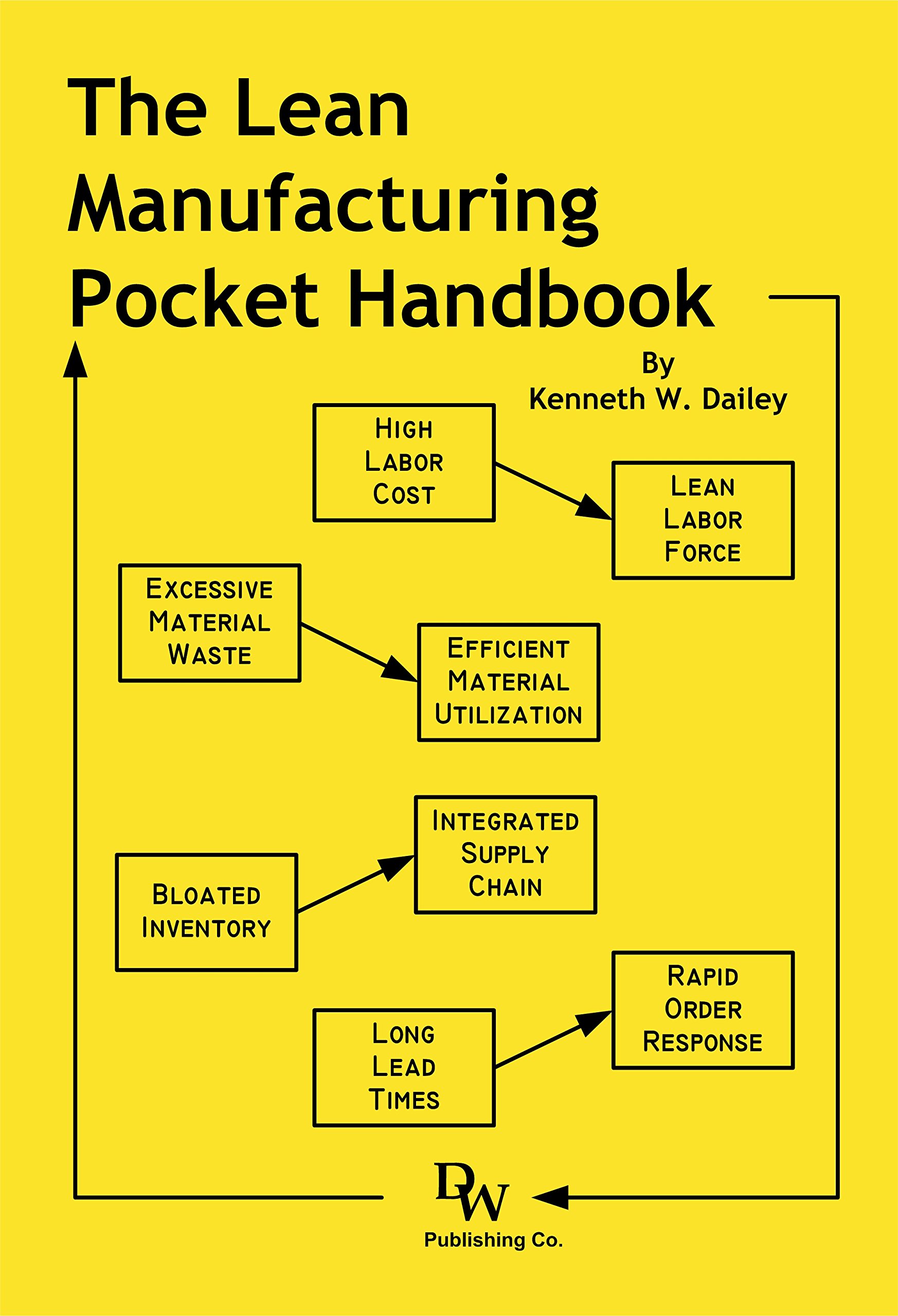
Being an environmental engineer requires extensive office and field work. They may also be responsible for conducting field inspections and evaluating and characterizing materials. They must also be familiar with environmental regulations and practices. They might also have to create and maintain spreadsheets, and other elements of reports. They can be involved in a variety of different projects and can progress from related occupations into their own field.
Responsibilities
The responsibilities of an environmental engineer are varied and diverse. The environmental engineer can design technology to prevent pollution and make recommendations for clean-up efforts. They may also work alongside legal counsel or other experts, such business people and those who specialize in law. Additionally, environmental engineers can also handle administrative tasks such as preparing spreadsheets or other report components. Environmental engineers are responsible for advising federal, state, or local government agencies regarding matters relating to environmental protection, contamination, and other related issues.
Other responsibilities of an environmental engineer include assisting in the development and implementation of plans and programs for the conservation and management of natural resources. They determine the impact of proposed commercial activity on land, water, and other resources. They can also help with general administrative tasks like preparing project documentation, training staff, and budget implementation. An environmental engineer can also provide advice to policymakers about environmental best practices and issues.
The outlook for employment
The employment outlook is favorable for environmental engineers. Engineers can assist companies in complying with environmental regulations, developing alternative methods to reduce pollution and managing the waste they produce. There is a strong demand. Environmental engineers will see a rise in demand due to the growing population and emphasis on prevention. As workers leave and move into other fields or retire, job opportunities will increase. This is a job that will not disappoint. Here are some jobs you can apply for in the future.
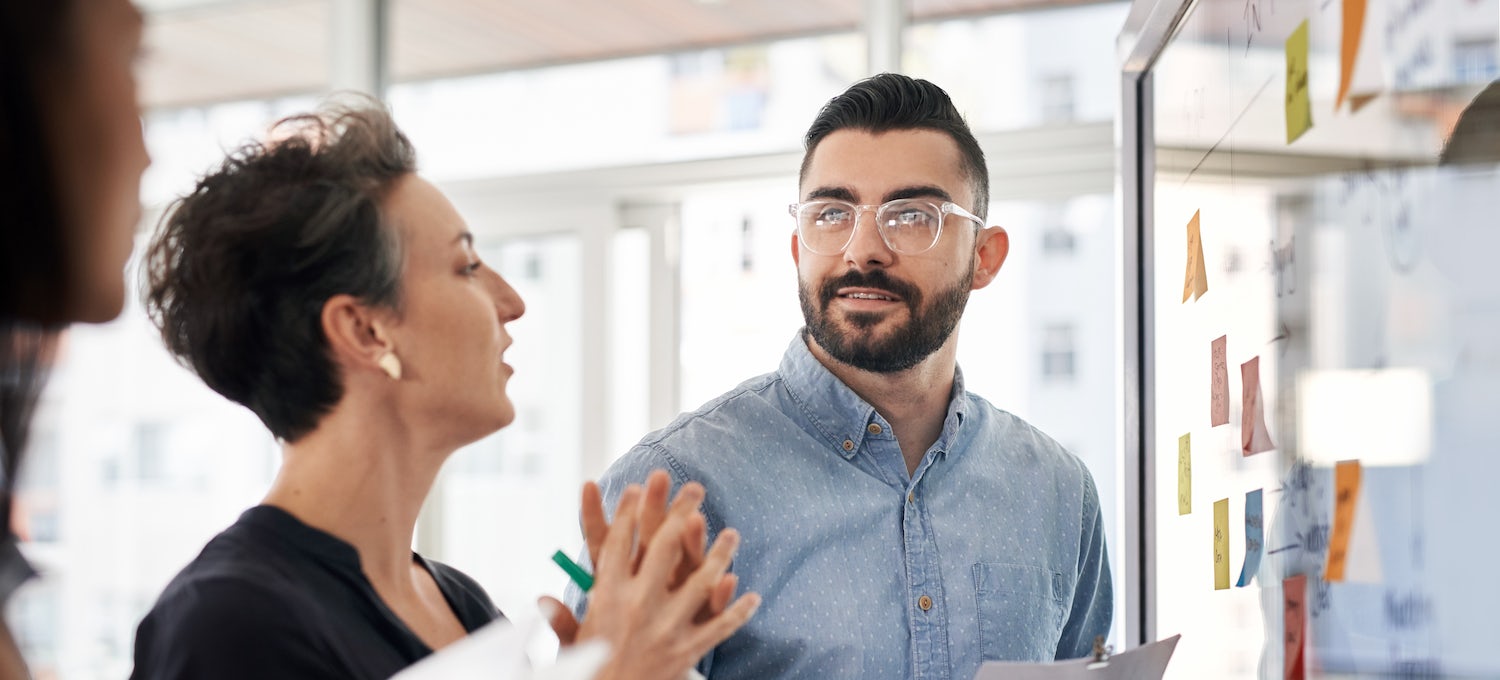
Many environmental engineers work in laboratories or offices. Many work indoors. However, others may spend time outside or travel for work. They work forty hours a week. Your work schedule may change for certain jobs. It can be difficult, especially when deadlines are involved. Because the environment is their main concern, environmental engineers need to be aware of their limitations. This job is highly stressful and can require long hours.
FAQ
How can manufacturing efficiency be improved?
The first step is to identify the most important factors affecting production time. Then we need to find ways to improve these factors. If you don’t know how to start, look at which factors have the greatest impact upon production time. Once you identify them, look for solutions.
What are the goods of logistics?
Logistics refers to all activities that involve moving goods from A to B.
They encompass all aspects transport, including packaging and loading, transporting, storage, unloading.
Logisticians ensure that products reach the right destination at the right moment and under safe conditions. Logisticians help companies improve their supply chain efficiency by providing information about demand forecasts and stock levels, production schedules, as well as availability of raw materials.
They also keep track of shipments in transit, monitor quality standards, perform inventories and order replenishment, coordinate with suppliers and vendors, and provide support services for sales and marketing.
What types of jobs can you find in logistics
Logistics can offer many different jobs. These are some of the jobs available in logistics:
-
Warehouse workers – They load and unload pallets and trucks.
-
Transportation drivers: They drive trucks and trailers and deliver goods and make pick-ups.
-
Freight handlers, - They sort out and pack freight in warehouses.
-
Inventory managers: They are responsible for the inventory and management of warehouses.
-
Sales reps - They sell products and services to customers.
-
Logistics coordinators - They plan and organize logistics operations.
-
Purchasing agents are those who purchase goods and services for the company.
-
Customer service representatives are available to answer customer calls and emails.
-
Shipping clerks – They process shipping orders, and issue bills.
-
Order fillers - These people fill orders based on what has been ordered.
-
Quality control inspectors are responsible for inspecting incoming and outgoing products looking for defects.
-
Others – There are many other types available in logistics. They include transport supervisors, cargo specialists and others.
What is the role of a logistics manager
Logistics managers are responsible for ensuring that all goods arrive in perfect condition and on time. This is achieved by using their knowledge and experience with the products of the company. He/she should make sure that enough stock is on hand to meet the demands.
Statistics
- According to a Statista study, U.S. businesses spent $1.63 trillion on logistics in 2019, moving goods from origin to end user through various supply chain network segments. (netsuite.com)
- In 2021, an estimated 12.1 million Americans work in the manufacturing sector.6 (investopedia.com)
- Job #1 is delivering the ordered product according to specifications: color, size, brand, and quantity. (netsuite.com)
- [54][55] These are the top 50 countries by the total value of manufacturing output in US dollars for its noted year according to World Bank.[56] (en.wikipedia.org)
- Many factories witnessed a 30% increase in output due to the shift to electric motors. (en.wikipedia.org)
External Links
How To
How to Use the Just-In-Time Method in Production
Just-in-time is a way to cut costs and increase efficiency in business processes. It's the process of obtaining the right amount and timing of resources when you need them. This means you only pay what you use. Frederick Taylor was the first to coin this term. He developed it while working as a foreman during the early 1900s. Taylor observed that overtime was paid to workers if they were late in working. He realized that workers should have enough time to complete their jobs before they begin work. This would help increase productivity.
The idea behind JIT is that you should plan ahead and have everything ready so you don't waste money. It is important to look at your entire project from beginning to end and ensure that you have enough resources to handle any issues that may arise. You will have the resources and people to solve any problems you anticipate. This will prevent you from spending extra money on unnecessary things.
There are many JIT methods.
-
Demand-driven: This JIT is where you place regular orders for the parts/materials that are needed for your project. This will allow to track how much material has been used up. This will let you know how long it will be to produce more.
-
Inventory-based: You stock materials in advance to make your projects easier. This allows you to forecast how much you will sell.
-
Project-driven: This means that you have enough money to pay for your project. If you know the amount you require, you can buy the materials you need.
-
Resource-based JIT : This is probably the most popular type of JIT. You allocate resources based on the demand. You will, for example, assign more staff to deal with large orders. If you don’t have many orders you will assign less people to the work.
-
Cost-based: This is a similar approach to resource-based but you are not only concerned with how many people you have, but also how much each one costs.
-
Price-based: This is a variant of cost-based. However, instead of focusing on the individual workers' costs, this looks at the total price of the company.
-
Material-based: This is very similar to cost-based but instead of looking at total costs of the company you are concerned with how many raw materials you use on an average.
-
Time-based: Another variation of resource-based JIT. Instead of worrying about how much each worker costs, you can focus on how long the project takes.
-
Quality-based JIT: This is another variation of resource based JIT. Instead of thinking about the cost of each employee or the time it takes to produce something, you focus on how good your product quality.
-
Value-based JIT: This is the latest form of JIT. In this case, you're not concerned with how well the products perform or whether they meet customer expectations. Instead, you focus on the added value that you provide to your market.
-
Stock-based. This method is inventory-based and focuses only on the actual production at any given point. This is used to increase production and minimize inventory.
-
Just-in-time planning (JIT): This is a combination JIT and supply-chain management. It's the process of scheduling delivery of components immediately after they are ordered. It reduces lead times and improves throughput.