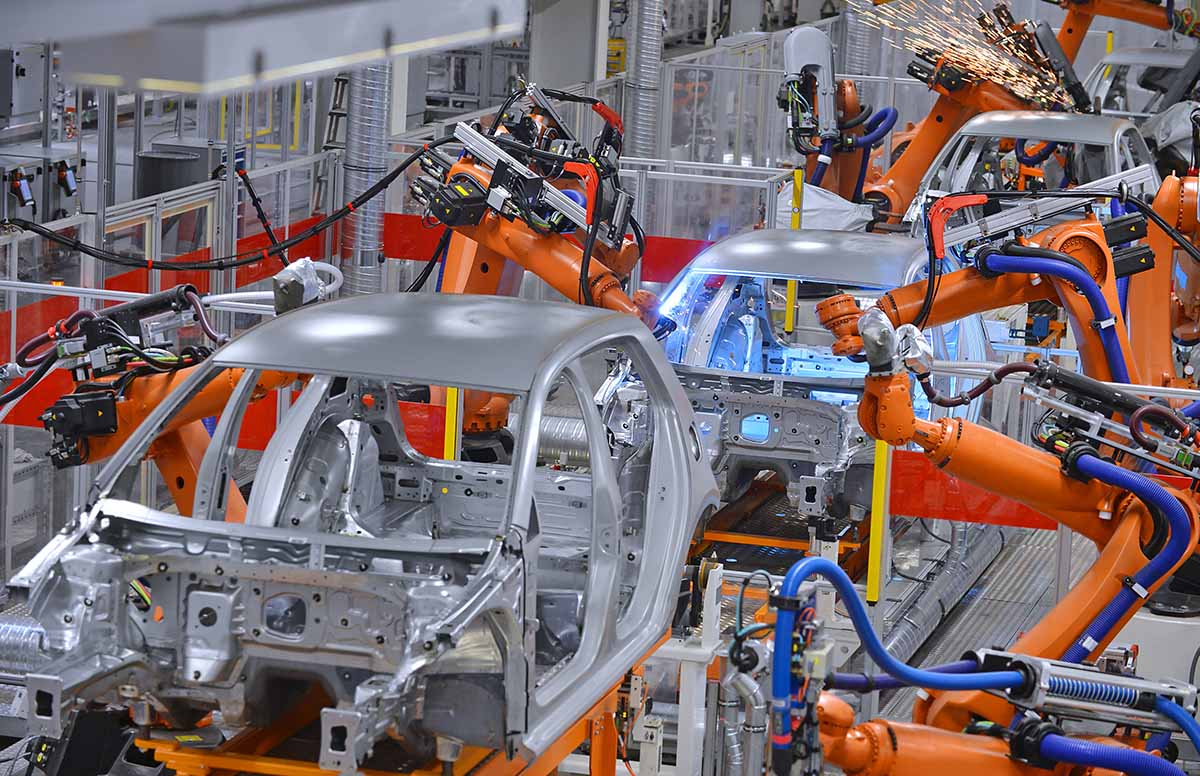
Despite the many benefits of lean manufacturing, there have been some challenges for companies trying to implement this strategy. Companies should develop a comprehensive plan that addresses these issues. Companies who have implemented Lean found three main problems that hamper the success rate of the initiative.
Regardless of the size of a corporation, a commitment to lean manufacturing is critical to its success. Although there are no easy ways to measure how committed a company has been to lean manufacturing implementations, it is crucial that staff are familiarized with the changes and culture.
It is also important to ensure that resources are allocated correctly. Many public organisations have reported that they waste allocated budgets by purchasing unnecessary items. It has been reported that managers sometimes purchase equipment that they do not need to spend their budget. This can cause operational bottlenecks that lead to inefficient lean manufacturing.
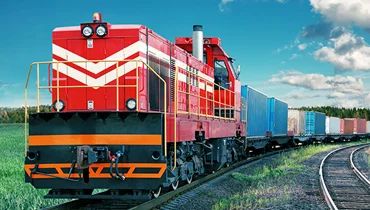
One of the biggest challenges in implementing lean manufacturing is resistance to cultural change. Employees, especially those who have worked for the company for many years, aren’t used to change. These employees might wait for the majority of the workforce to convince them to change. Managers must share the benefits of their program and explain why it is necessary to overcome resistance.
Another significant challenge is the lack of a strategic transformation plan. Even though many companies transform their business operations simultaneously, it is important that you have a long-term plan. This strategy helps companies mentor future leaders, maintain competitiveness and improve operations. It helps to identify and fix operational bottlenecks, and to identify and address growth potential.
It is vital to train workers to overcome resistance. Training is essential to help workers understand their roles and expectations. The training also helps workers to develop multi-skills, which can be used to do more work independently. Training also helps workers develop problem solving skills, which helps them sustain Lean through improvements in performance.
Management should engage with workers regularly to overcome resistance. While managers may use pressure to get workers to comply with instructions, managers also need to take the time to explain why the change is necessary. Ineffective implementation can be caused by managers who gave workers wrong instructions.
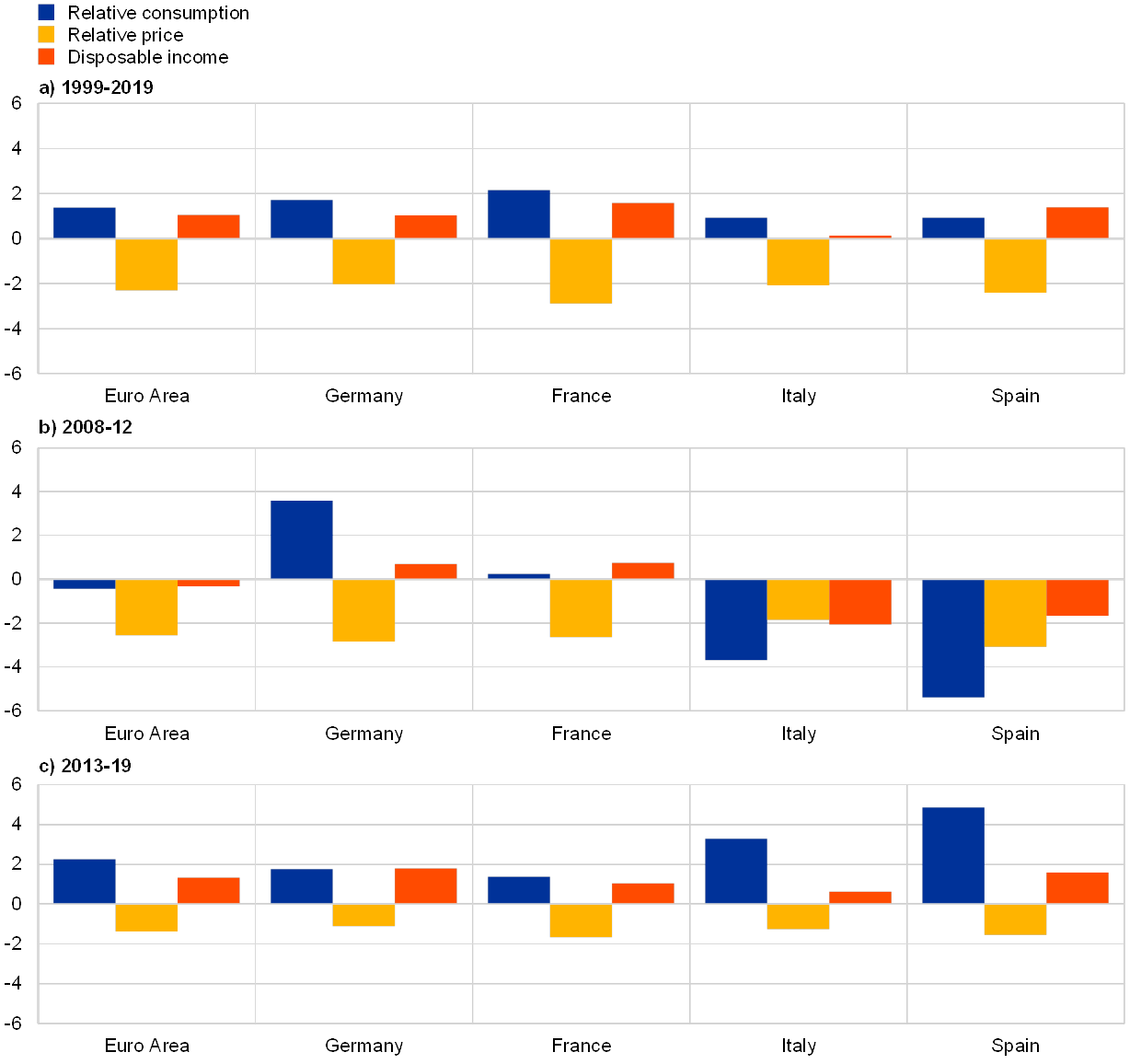
Managers, regardless of company size, must be present at the shop floor to help identify areas for improvement. Managers must also develop training modules and familiarize staff with new digital tools. These tools, including 5S (visual management), improve visual management.
Finally, it is essential to establish and communicate a clear vision for lean manufacturing. This vision should include the responsibilities and schedule of lean manufacturing, as well as a method to measure success.
FAQ
Is automation necessary in manufacturing?
Automating is not just important for manufacturers, but also for service providers. It allows them to offer services faster and more efficiently. In addition, it helps them reduce costs by reducing human errors and improving productivity.
What are the essential elements of running a logistics firm?
To run a successful logistics company, you need a lot knowledge and skills. Effective communication skills are necessary to work with suppliers and clients. You need to understand how to analyze data and draw conclusions from it. You need to be able work under pressure and manage stressful situations. To increase efficiency and creativity, you need to be creative. Strong leadership qualities are essential to motivate your team and help them achieve their organizational goals.
It is important to be organized and efficient in order to meet tight deadlines.
How can manufacturing efficiency be improved?
First, identify the factors that affect production time. Then we need to find ways to improve these factors. If you don’t know where to begin, consider which factors have the largest impact on production times. Once you've identified them, try to find solutions for each of those factors.
What is production planning?
Production planning is the process of creating a plan that covers all aspects of production. This includes scheduling, budgeting and crew, location, equipment, props, and more. This document will ensure everything is in order and ready to go when you need it. It should also contain information on achieving the best results on set. This includes location information, crew details, equipment specifications, and casting lists.
The first step in filming is to define what you want. You may have decided where to shoot or even specific locations you want to use. Once you've identified the locations and scenes you want to use, you can begin to plan what elements you need for each scene. You might decide you need a car, but not sure what make or model. This is where you can look up car models online and narrow down your options by choosing from different makes and models.
After you've found the perfect car, it's time to start thinking about adding extras. Are you looking for people to sit in the front seats? Maybe you need someone to move around in the back. Perhaps you would like to change the interior colour from black to white. These questions will help to determine the style and feel of your car. It is also worth considering the types of shots that you wish to take. Are you going to be shooting close-ups? Or wide angles? Maybe you want the engine or the steering wheels to be shown. These things will help you to identify the car that you are looking for.
Once you've determined the above, it is time to start creating a calendar. You can create a schedule that will outline when you must start and finish your shoots. Every day will have a time for you to arrive at the location, leave when you are leaving and return home when you are done. Everyone knows exactly what they should do and when. Hire extra staff by booking them ahead of time. It is not worth hiring someone who won’t show up because you didn’t tell him.
You will need to factor in the days that you have to film when creating your schedule. Some projects may only take a couple of days, while others could last for weeks. When you are creating your schedule, you should always keep in mind whether you need more than one shot per day or not. Multiple takes at the same place will result in higher costs and longer completion times. You can't be certain if you will need multiple takes so it is better not to shoot too many.
Budgeting is another crucial aspect of production plan. You will be able to manage your resources if you have a realistic budget. You can always lower the budget if you encounter unexpected problems. You shouldn't underestimate the amount you'll spend. If you underestimate how much something costs, you'll have less money to pay for other items.
Production planning can be a complex process. However, once you know how everything works together it will become easier to plan future projects.
Statistics
- In the United States, for example, manufacturing makes up 15% of the economic output. (twi-global.com)
- According to a Statista study, U.S. businesses spent $1.63 trillion on logistics in 2019, moving goods from origin to end user through various supply chain network segments. (netsuite.com)
- Job #1 is delivering the ordered product according to specifications: color, size, brand, and quantity. (netsuite.com)
- It's estimated that 10.8% of the U.S. GDP in 2020 was contributed to manufacturing. (investopedia.com)
- According to the United Nations Industrial Development Organization (UNIDO), China is the top manufacturer worldwide by 2019 output, producing 28.7% of the total global manufacturing output, followed by the United States, Japan, Germany, and India.[52][53] (en.wikipedia.org)
External Links
How To
How to Use the Just In Time Method in Production
Just-intime (JIT), which is a method to minimize costs and maximize efficiency in business process, is one way. It's the process of obtaining the right amount and timing of resources when you need them. This means you only pay what you use. Frederick Taylor developed the concept while working as foreman in early 1900s. He noticed that workers were often paid overtime when they had to work late. He decided that workers would be more productive if they had enough time to complete their work before they started to work.
JIT teaches you to plan ahead and prepare everything so you don’t waste time. The entire project should be looked at from start to finish. You need to ensure you have enough resources to tackle any issues that might arise. If you expect problems to arise, you will be able to provide the necessary equipment and personnel to address them. This way, you won't end up paying extra money for things that weren't really necessary.
There are many JIT methods.
-
Demand-driven JIT: You order the parts and materials you need for your project every other day. This will allow for you to track the material that you have left after using it. This will allow to you estimate the time it will take for more to be produced.
-
Inventory-based: This type allows you to stock the materials needed for your projects ahead of time. This allows you to forecast how much you will sell.
-
Project-driven: This means that you have enough money to pay for your project. Knowing how much money you have available will help you purchase the correct amount of materials.
-
Resource-based JIT : This is probably the most popular type of JIT. Here you can allocate certain resources based purely on demand. For example, if there is a lot of work coming in, you will have more people assigned to them. If there aren't many orders, you will assign fewer people.
-
Cost-based: This is similar to resource-based, except that here you're not just concerned about how many people you have but how much each person costs.
-
Price-based: This approach is very similar to the cost-based method except that you don't look at individual workers costs but the total cost of the company.
-
Material-based is an alternative to cost-based. Instead of looking at the total cost in the company, this method focuses on the average amount of raw materials that you consume.
-
Time-based JIT: This is another variant of resource-based JIT. Instead of worrying about how much each worker costs, you can focus on how long the project takes.
-
Quality-based: This is yet another variation of resource-based JIT. Instead of focusing on the cost of each worker or how long it takes, think about how high quality your product is.
-
Value-based JIT: This is the latest form of JIT. In this scenario, you're not concerned about how products perform or whether customers expect them to meet their expectations. Instead, you're focused on how much value you add to the market.
-
Stock-based is an inventory-based system that measures the number of items produced at any given moment. It is used when production goals are met while inventory is kept to a minimum.
-
Just-intime planning (JIT), is a combination JIT/sales chain management. It is the process that schedules the delivery of components within a short time of their order. This is important as it reduces lead time and increases throughput.