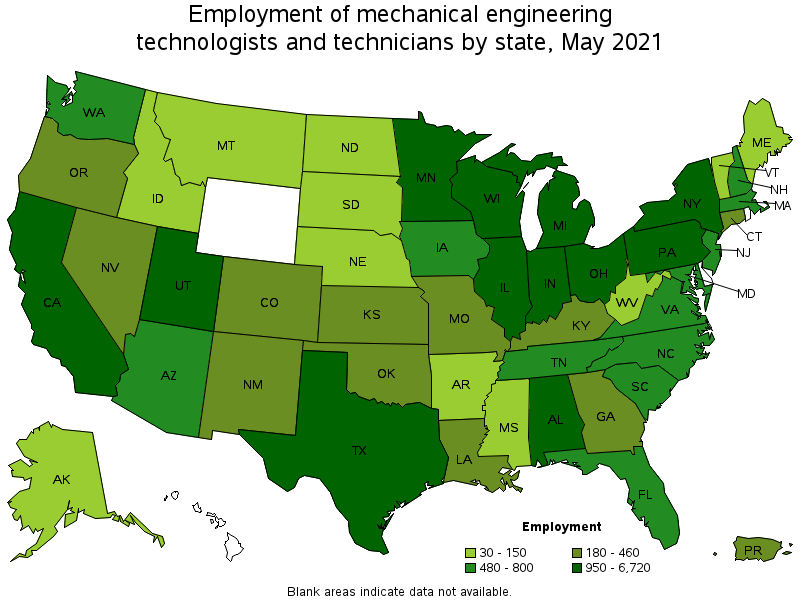
Mechatronics is a multidisciplinary engineering field that combines mechanical engineering with electrical engineering. This combination is critical to creating advanced machines that work efficiently. A typical mechatronics system is made up of actuators and sensors as well as electronics. It collects signals from the environment, processes them, and generates an output signal. It is used in many different products. Mechatronic systems can be found in household appliances such as computers and televisions. Mechatronic systems that are simpler and smarter will be the future of electromechanical technology.
The first use of electromechanical devices was in early telegraphy. A Strowger switch was one of the first types of electromechanical devices used to send electrical signals. These devices were widespread in automated telephone exchanges in America in the middle of 20th century. Today, more equipment is designed with automated features and the use of solid-state electronics has replaced electromechanical devices in many applications.
An Electro-mechanical Technician is a person who uses both mechanical technology and electronic circuits to maintain and operate automated equipment. They might be involved in energy projects or maintenance of equipment used for deep-ocean exploration. They may also be responsible for repairs to machines. The Electro-Mechanical Technician needs to have strong mechanical, troubleshooting, and logical-thinking skills. They should also be able work under pressure. They also need to be able to use tools safely. Employers will find it a huge benefit to have them proficient in electrical and mechanical systems.
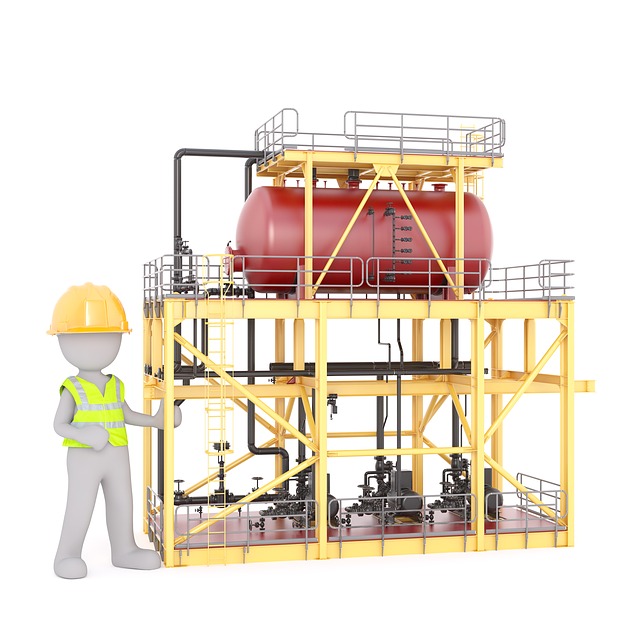
A diploma or certificate may be awarded to Electro-mechanical Technicians by a technical or vocational school. They may also earn an associate's degree or a bachelor's degree in Electrical Engineering or Mechatronics. Certified Control Systems Certification is another certification that Electro-mechanical Technicians can use to prove their professional competence.
Assemblers may also be known as Electro-Mechanical Techs. To assemble electronic and mechanical equipment, they follow instructions and assembly drawings. They may also be able to work with production drawings. These types are more likely to need transistors.
Mechatronics is expected to increase in popularity in the coming years. The societal demand for highly functional and efficient products is what has led to its popularity. The field of Mechatronics has many untapped areas. These include the creation of new technology, like particle electromechanics. Mechatronics combines computer science and electrical engineering to solve new problems. In addition, many large manufacturing companies are looking to develop new electronic-mechanical engineering technologies.
Mechatronics, which is a dynamic field, is constantly evolving. An Electro-mechanical Technician is able to specialize in the area of Mechatronics. This requires specialized information in electrical circuits as well as sensing engineering and computer software. They are expected to use their special knowledge to create value-added products.
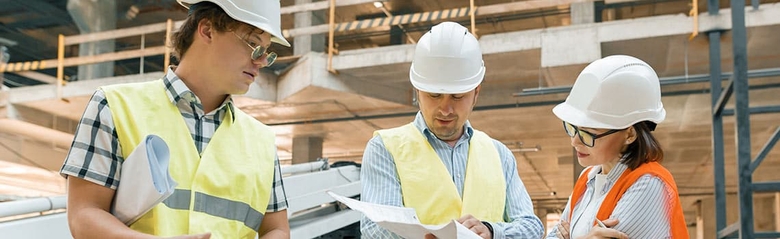
Also, electromechanical technicians have the option to specialize in industrial maintenance, Mechatronics or industrial maintenance and/or maintenance. The rise in computer-controlled systems will likely keep these technicians in demand. Compensation can vary depending on geographic location, industry, and experience.
FAQ
What can I do to learn more about manufacturing?
Experience is the best way for you to learn about manufacturing. If that is not possible, you could always read books or view educational videos.
What is the role and responsibility of a Production Planner?
A production planner ensures all aspects of the project are delivered on time, within budget, and within scope. They make sure that the product and services meet client expectations.
Why is logistics so important in manufacturing?
Logistics is an integral part of every business. They enable you to achieve outstanding results by helping manage product flow from raw materials through to finished goods.
Logistics plays a significant role in reducing cost and increasing efficiency.
Statistics
- (2:04) MTO is a production technique wherein products are customized according to customer specifications, and production only starts after an order is received. (oracle.com)
- Job #1 is delivering the ordered product according to specifications: color, size, brand, and quantity. (netsuite.com)
- According to a Statista study, U.S. businesses spent $1.63 trillion on logistics in 2019, moving goods from origin to end user through various supply chain network segments. (netsuite.com)
- You can multiply the result by 100 to get the total percent of monthly overhead. (investopedia.com)
- It's estimated that 10.8% of the U.S. GDP in 2020 was contributed to manufacturing. (investopedia.com)
External Links
How To
How to use Lean Manufacturing in the production of goods
Lean manufacturing refers to a method of managing that seeks to improve efficiency and decrease waste. It was developed in Japan during the 1970s and 1980s by Taiichi Ohno, who received the Toyota Production System (TPS) award from TPS founder Kanji Toyoda. Michael L. Watkins published the original book on lean manufacturing, "The Machine That Changed the World," in 1990.
Lean manufacturing can be described as a set or principles that are used to improve quality, speed and cost of products or services. It emphasizes reducing defects and eliminating waste throughout the value chain. Lean manufacturing is called just-in-time (JIT), zero defect, total productive maintenance (TPM), or 5S. Lean manufacturing eliminates non-value-added tasks like inspection, rework, waiting.
In addition to improving product quality and reducing costs, lean manufacturing helps companies achieve their goals faster and reduces employee turnover. Lean manufacturing is considered one of the most effective ways to manage the entire value chain, including suppliers, customers, distributors, retailers, and employees. Lean manufacturing is widely practiced in many industries around the world. Toyota's philosophy, for example, is what has enabled it to be successful in electronics, automobiles, medical devices, healthcare and chemical engineering as well as paper and food.
Lean manufacturing includes five basic principles:
-
Define Value - Identify the value your business adds to society and what makes you different from competitors.
-
Reduce Waste - Remove any activity which doesn't add value to your supply chain.
-
Create Flow. Ensure that your work is uninterrupted and flows seamlessly.
-
Standardize & Simplify - Make processes as consistent and repeatable as possible.
-
Building Relationships – Establish personal relationships with both external and internal stakeholders.
Lean manufacturing is not a new concept, but it has been gaining popularity over the last few years due to a renewed interest in the economy following the global financial crisis of 2008. Many businesses are now using lean manufacturing to improve their competitiveness. In fact, some economists believe that lean manufacturing will be an important factor in economic recovery.
Lean manufacturing is now becoming a common practice in the automotive industry, with many benefits. These include better customer satisfaction and lower inventory levels. They also result in lower operating costs.
It can be applied to any aspect of an organisation. It is especially useful for the production aspect of an organization, as it ensures that every step in the value chain is efficient and effective.
There are three types principally of lean manufacturing:
-
Just-in Time Manufacturing, (JIT): This kind of lean manufacturing is also commonly known as "pull-systems." JIT refers to a system in which components are assembled at the point of use instead of being produced ahead of time. This approach is designed to reduce lead times and increase the availability of components. It also reduces inventory.
-
Zero Defects Manufacturing: ZDM ensures that no defective units leave the manufacturing plant. It is better to repair a part than have it removed from the production line if it needs to be fixed. This applies to finished goods that may require minor repairs before shipment.
-
Continuous Improvement (CI): CI aims to improve the efficiency of operations by continuously identifying problems and making changes in order to eliminate or minimize waste. Continuous improvement involves continuous improvement of processes and people as well as tools.