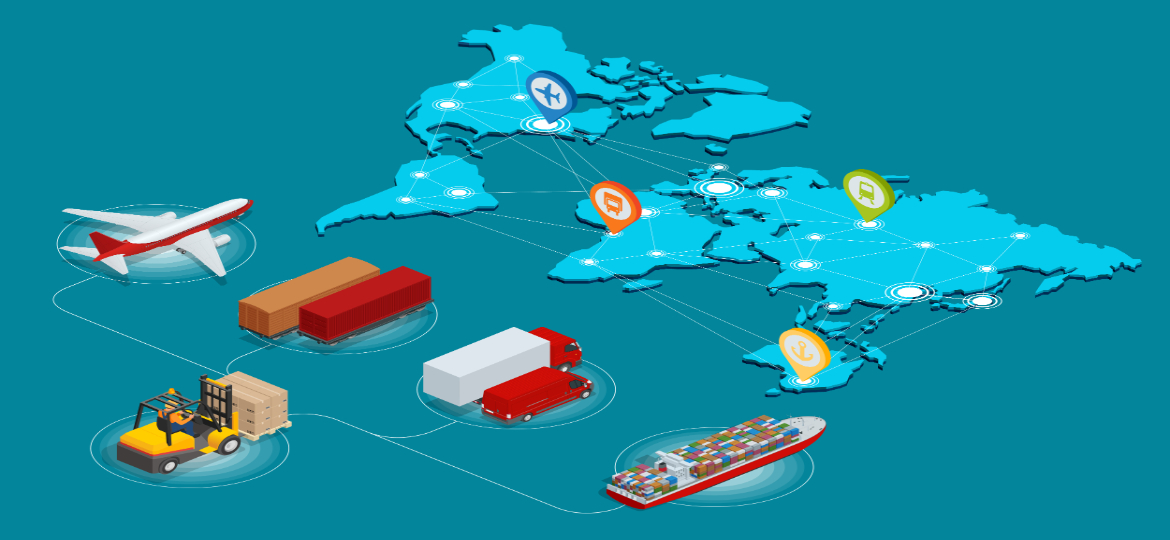
There are a wide variety of logistics jobs in Tampa. There are many logistics jobs in Tampa. Some of them can be found in manufacturing, construction and healthcare. Others may work for wholesalers or consulting firms who help businesses streamline their supply chain.
A degree can provide a wide range of career options. An associate degree can help you find entry-level roles such as shipping clerks. However, bachelor's level jobs are reserved for those with a higher education. Depending on your specific interests and goals, you may choose to specialize in a specific area of logistics, such as warehousing or supply chain management.
BLS statistics predict that jobs for logistics professionals will increase by 5 percent between 2018-2028. The projected job growth is even higher for professionals who specialize in business operations.
You can get a logistics degree either at a 4-year university or a community-college. These programs will offer you a number of concentrations in logistics, allowing you to build up specialized knowledge and increase your employability as you climb the career ladder.
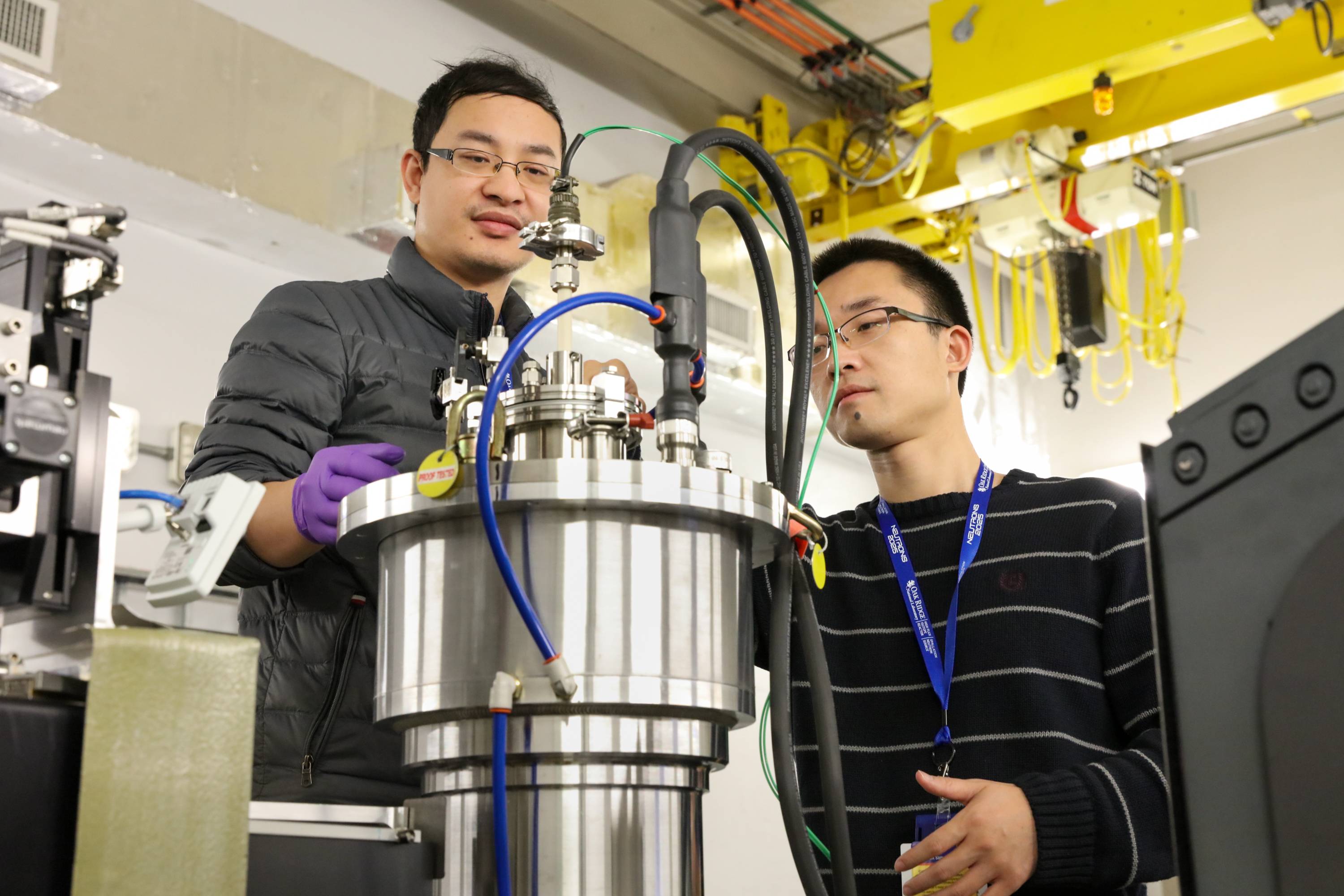
In addition to pursuing a bachelor's degree, students should consider taking part in internships and networking opportunities. These experiences give you valuable hands-on experience in the field, and they can help you find your first logistics job.
The logistics industry is a very diverse field, with good job prospects. You can find logistics jobs throughout the country, particularly in states that are large and growing, like California and Texas. You can also find careers in a number of specific sectors, such as aerospace and oil and gas.
You should take into account the size and capabilities of a logistics provider when choosing one. The ideal 3PL is one that can customize a solution to fit your specific business needs. You can reduce your costs and improve your efficiency.
Your business's supply chain plays a vital role in the success of its operations. To ensure that your product arrives at the correct time in perfect condition, you must have the appropriate people and tools. You can improve the efficiency of your supply chain by selecting a third-party logistics provider that has expertise in your industry and can deliver the goods on time, every time.
Sheer, an integrated 3PL with a Tampa base, can reduce costs and improve supply chain efficiency. We offer our clients a variety services, including transportation management, inventory control, and shipping.
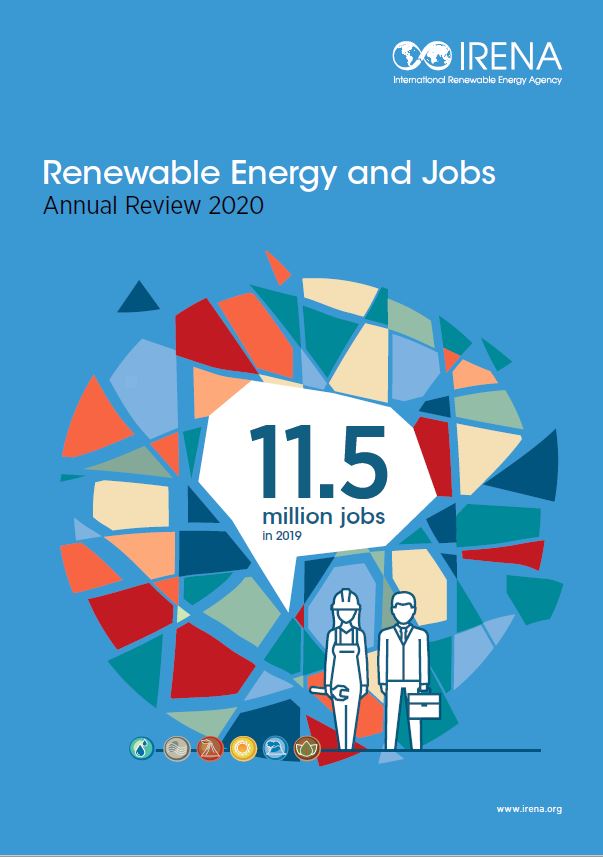
We also provide a suite of technology tools to help you track and manage your supply chain. Cloud-based systems are available that can be integrated with your current ERP system to make it easier for you to control and monitor all aspects of your company.
Sheer's multimodal network can transform your supply chains from liabilities to assets. We will always deliver your products safely and on time.
FAQ
What are the 4 types manufacturing?
Manufacturing is the process of transforming raw materials into useful products using machines and processes. It can involve many activities like designing, manufacturing, testing packaging, shipping, selling and servicing.
What are manufacturing and logistics?
Manufacturing refers the process of producing goods from raw materials through machines and processes. Logistics manages all aspects of the supply chain, including procurement, production planning and distribution, inventory control, transportation, customer service, and transport. Sometimes manufacturing and logistics are combined to refer to a wider term that includes both the process of creating products as well as their delivery to customers.
What are the products of logistics?
Logistics involves the transportation of goods from point A and point B.
They cover all aspects of transportation, such as packing, loading, transporting and unloading.
Logisticians ensure that the right product reaches the right place at the right time and under safe conditions. They provide information on demand forecasts as well stock levels, production schedules and availability of raw material.
They can also track shipments in transit and monitor quality standards.
What is it like to manage a logistics company?
You need to have a lot of knowledge and skills to manage a successful logistic business. Effective communication skills are necessary to work with suppliers and clients. You should be able analyse data and draw inferences. You will need to be able handle pressure well and work in stressful situations. You must be creative and innovative to develop new ideas to improve efficiency. You need to have strong leadership qualities to motivate team members and direct them towards achieving organizational goals.
You should also be organized and efficient to meet tight deadlines.
Statistics
- According to the United Nations Industrial Development Organization (UNIDO), China is the top manufacturer worldwide by 2019 output, producing 28.7% of the total global manufacturing output, followed by the United States, Japan, Germany, and India.[52][53] (en.wikipedia.org)
- In the United States, for example, manufacturing makes up 15% of the economic output. (twi-global.com)
- In 2021, an estimated 12.1 million Americans work in the manufacturing sector.6 (investopedia.com)
- (2:04) MTO is a production technique wherein products are customized according to customer specifications, and production only starts after an order is received. (oracle.com)
- It's estimated that 10.8% of the U.S. GDP in 2020 was contributed to manufacturing. (investopedia.com)
External Links
How To
How to Use 5S to Increase Productivity in Manufacturing
5S stands for "Sort", "Set In Order", "Standardize", "Separate" and "Store". The 5S methodology was developed at Toyota Motor Corporation in 1954. This methodology helps companies improve their work environment to increase efficiency.
This method has the basic goal of standardizing production processes to make them repeatable. Cleaning, sorting and packing are all done daily. Workers can be more productive by knowing what to expect.
There are five steps to implementing 5S, including Sort, Set In Order, Standardize, Separate and Store. Each step has a different action and leads to higher efficiency. Sorting things makes it easier to find them later. You arrange items by placing them in an order. Next, organize your inventory into categories and store them in containers that are easily accessible. Labeling your containers will ensure that everything is correctly labeled.
This requires employees to critically evaluate how they work. Employees need to understand the reasons they do certain jobs and determine if there is a better way. To be successful in the 5S system, employees will need to acquire new skills and techniques.
The 5S method increases efficiency and morale among employees. They are more motivated to achieve higher efficiency levels as they start to see improvement.