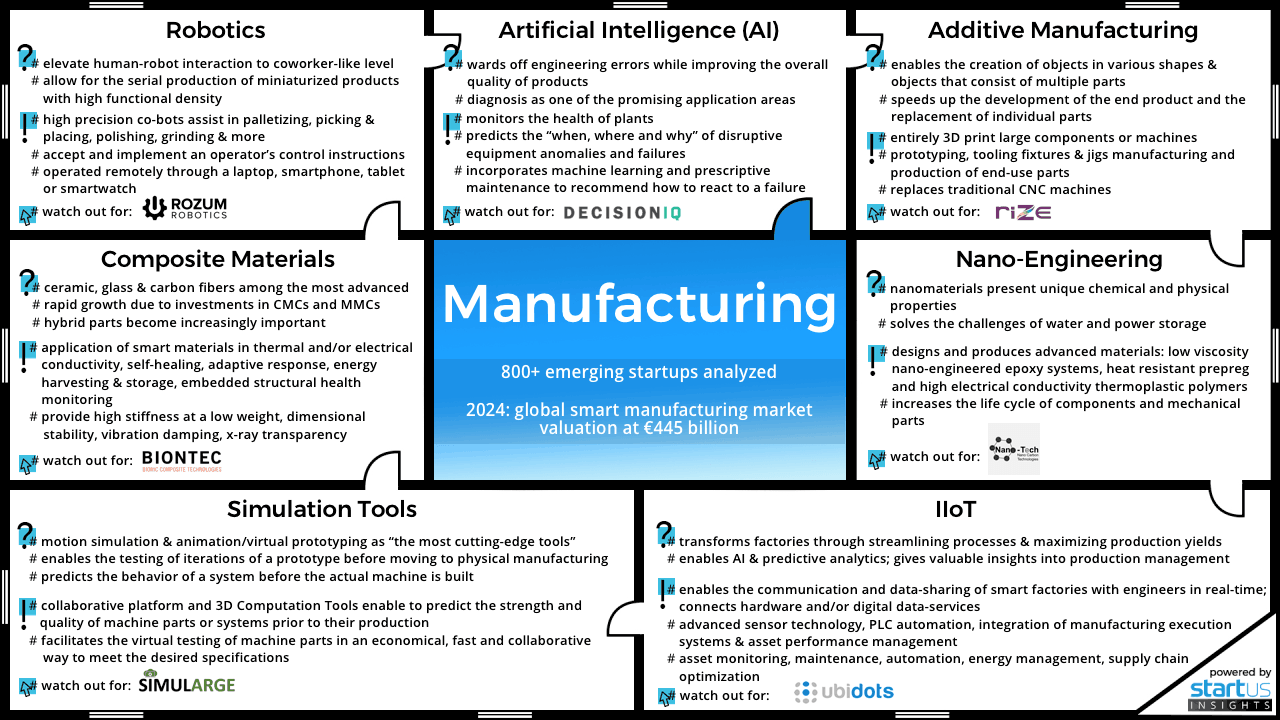
The Defense Industrial Base is a network of more that 200,000 companies who supply goods and service to the Department of Defense. It includes startups, big corporations, small businesses. The Government Accountability Office has released a new report that highlights the risks and challenges facing the DIB, as well its efforts to address these.
The defense industrial base has fallen by almost 40% in the last ten years. Accordingly, the Department of Defense is having difficulty recruiting new members to the sector. The Defense Department tried many different approaches to encouraging new businesses to get involved to solve this problem. Despite all of these efforts, smaller companies are still being left behind. This has resulted in a growing threat to national security.
Numerous DOD departments are currently working together to reduce risks in the DIB. However, the department lacks a comprehensive strategy for managing and assessing these risks. GAO examined several reports from DOD and interviewed DOD officials to help identify areas where improvement could be made. GAO identified five key elements that could aid the department in reaching its goals.
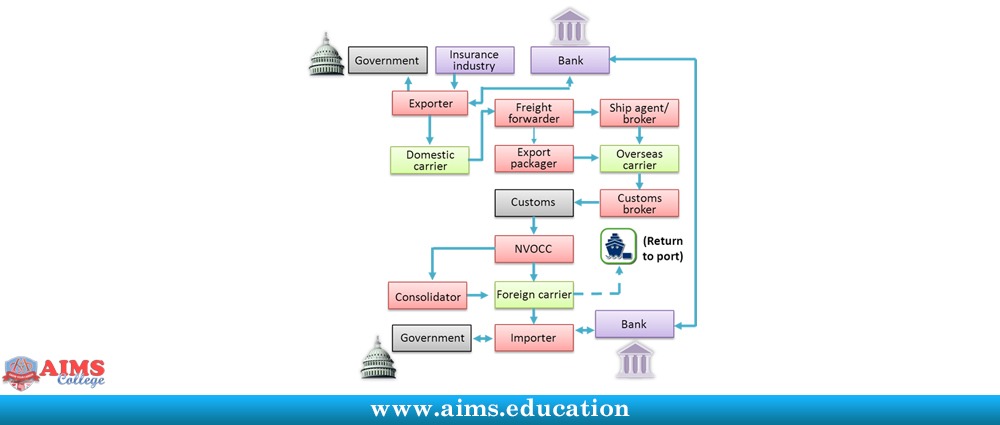
One of the biggest concerns is the loss of commercial suppliers. Many of these companies supply parts for weapons systems used by the Pentagon. There aren't many metrics available to determine how many new companies enter the market. The industry has seen a decline in small-businesses over the past decade.
Material shortages and dependence on foreign suppliers are two other issues. The acquisition process of the military is often slowed down by intellectual property restrictions. There is also no standard definition of "new entrant" in the defense industrial bases.
GAO recommended to the Department of Defense that it update its policy for mitigating risks in DIB. Additionally, the GAO recommends that the Department of Defence continue to engage traditional defence contractors and create tools that make it easier to allow commercial technology providers to enter DoD's marketplace. These recommendations should form part of an overall strategy to address industrial base concerns.
The Defense Department should examine how its OTAs, CSOs, and other resources can be used to accelerate acquisition strategy development. The supply chain can be restructured to produce dynamic outcomes by using the right people and processes.
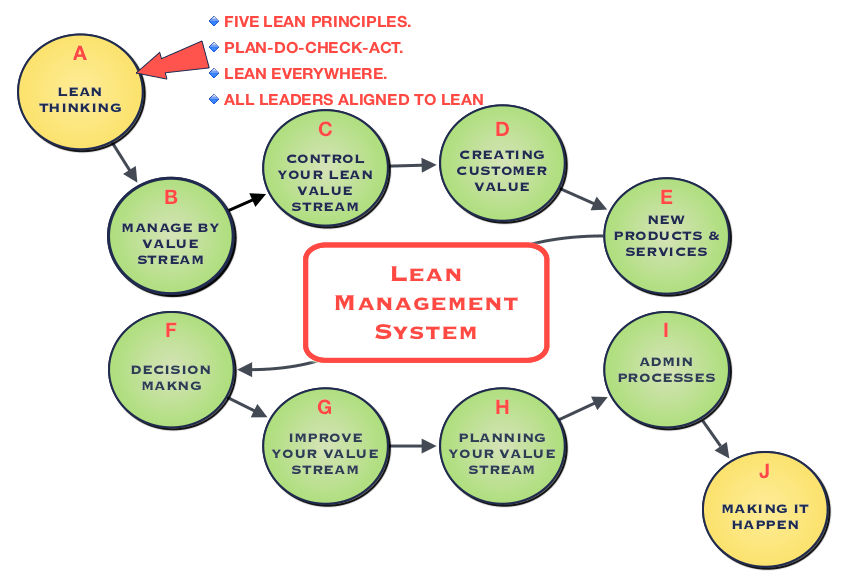
The number of new entrants to the defense industrial base has declined over the past decade, but the industry is still in development. For example, many companies are not comfortable with the traditional Federal Acquisition Regulation (FAR) process. Additionally, small businesses might not have as many opportunities to compete with the larger companies in the current market.
Small businesses and startups are crucial for innovation in the defense industrial base. Companies that make up the resilient DIB are able to support National Security requirements and enable the Department of Defense (DoD) to develop better military equipment.
The defense industrial sector is complex. It requires a comprehensive strategy to ensure resources are aligned with military needs. The Department of Defense should continue to learn about the best practices for integrating technology in its business processes. This will enable it to create more innovative products and services.
FAQ
What does it mean to be a manufacturer?
Manufacturing Industries refers to businesses that manufacture products. The people who buy these products are called consumers. These companies use various processes such as production, distribution, retailing, management, etc., to fulfill this purpose. They produce goods from raw materials by using machines and other machinery. This includes all types if manufactured goods.
How does a Production Planner differ from a Project Manager?
The major difference between a Production Planner and a Project Manager is that a Project Manager is often the person responsible for organizing and planning the entire project. While a Production Planner is involved mainly in the planning stage,
What does it take to run a logistics business?
You need to have a lot of knowledge and skills to manage a successful logistic business. You must have good communication skills to interact effectively with your clients and suppliers. It is important to be able to analyse data and draw conclusions. You must be able and able to handle stress situations and work under pressure. You need to be innovative and creative to come up with new ways to increase efficiency. You will need strong leadership skills to motivate and direct your team members towards achieving their organizational goals.
It is important to be organized and efficient in order to meet tight deadlines.
What are the logistics products?
Logistics refers to the movement of goods from one place to another.
They encompass all aspects transport, including packaging and loading, transporting, storage, unloading.
Logisticians make sure that the right product arrives at the right place at the correct time and in safe conditions. Logisticians help companies improve their supply chain efficiency by providing information about demand forecasts and stock levels, production schedules, as well as availability of raw materials.
They also keep track of shipments in transit, monitor quality standards, perform inventories and order replenishment, coordinate with suppliers and vendors, and provide support services for sales and marketing.
Why automate your warehouse?
Modern warehousing has seen automation take center stage. E-commerce has increased the demand for quicker delivery times and more efficient processes.
Warehouses have to be flexible to meet changing requirements. In order to do this, they need to invest in technology. The benefits of automating warehouses are numerous. These are just a few reasons to invest in automation.
-
Increases throughput/productivity
-
Reduces errors
-
Accuracy is improved
-
Safety enhancements
-
Eliminates bottlenecks
-
Allows companies scale more easily
-
Makes workers more efficient
-
The warehouse can be viewed from all angles.
-
Enhances customer experience
-
Improves employee satisfaction
-
This reduces downtime while increasing uptime
-
Ensures quality products are delivered on time
-
Human error can be eliminated
-
Assure compliance with regulations
Statistics
- Job #1 is delivering the ordered product according to specifications: color, size, brand, and quantity. (netsuite.com)
- [54][55] These are the top 50 countries by the total value of manufacturing output in US dollars for its noted year according to World Bank.[56] (en.wikipedia.org)
- (2:04) MTO is a production technique wherein products are customized according to customer specifications, and production only starts after an order is received. (oracle.com)
- In 2021, an estimated 12.1 million Americans work in the manufacturing sector.6 (investopedia.com)
- According to a Statista study, U.S. businesses spent $1.63 trillion on logistics in 2019, moving goods from origin to end user through various supply chain network segments. (netsuite.com)
External Links
How To
How to Use the Just In Time Method in Production
Just-intime (JIT), which is a method to minimize costs and maximize efficiency in business process, is one way. It's a way to ensure that you get the right resources at just the right time. This means you only pay what you use. Frederick Taylor, a 1900s foreman, first coined the term. After observing how workers were paid overtime for late work, he realized that overtime was a common practice. He decided to ensure workers have enough time to do their jobs before starting work to improve productivity.
JIT is a way to plan ahead and make sure you don't waste any money. The entire project should be looked at from start to finish. You need to ensure you have enough resources to tackle any issues that might arise. You'll be prepared to handle any potential problems if you know in advance. You won't have to pay more for unnecessary items.
There are many JIT methods.
-
Demand-driven: This JIT is where you place regular orders for the parts/materials that are needed for your project. This will let you track the amount of material left over after you've used it. This will let you know how long it will be to produce more.
-
Inventory-based: This allows you to store the materials necessary for your projects in advance. This allows you to predict how much you can expect to sell.
-
Project-driven: This approach involves setting aside sufficient funds to cover your project's costs. Once you have an idea of how much material you will need, you can purchase the necessary materials.
-
Resource-based JIT is the most widespread form. You assign certain resources based off demand. For example, if there is a lot of work coming in, you will have more people assigned to them. If you don't receive many orders, then you'll assign fewer employees to handle the load.
-
Cost-based: This approach is very similar to resource-based. However, you don't just care about the number of people you have; you also need to consider how much each person will cost.
-
Price-based: This is similar to cost-based but instead of looking at individual workers' salaries, you look at the total company price.
-
Material-based: This approach is similar to cost-based. However, instead of looking at the total cost for the company, you look at how much you spend on average on raw materials.
-
Time-based JIT: This is another variant of resource-based JIT. Instead of focusing on the cost of each employee, you will focus on the time it takes to complete a project.
-
Quality-based JIT - This is another form of resource-based JIT. Instead of thinking about how much each employee costs or how long it takes to manufacture something, you think about how good the quality of your product is.
-
Value-based JIT: This is the latest form of JIT. You don't worry about whether the products work or if they meet customer expectations. Instead, you focus on the added value that you provide to your market.
-
Stock-based: This stock-based method focuses on the actual quantity of products being made at any given time. It is used when production goals are met while inventory is kept to a minimum.
-
Just-in-time planning (JIT): This is a combination JIT and supply-chain management. It's the process of scheduling delivery of components immediately after they are ordered. It's important because it reduces lead times and increases throughput.