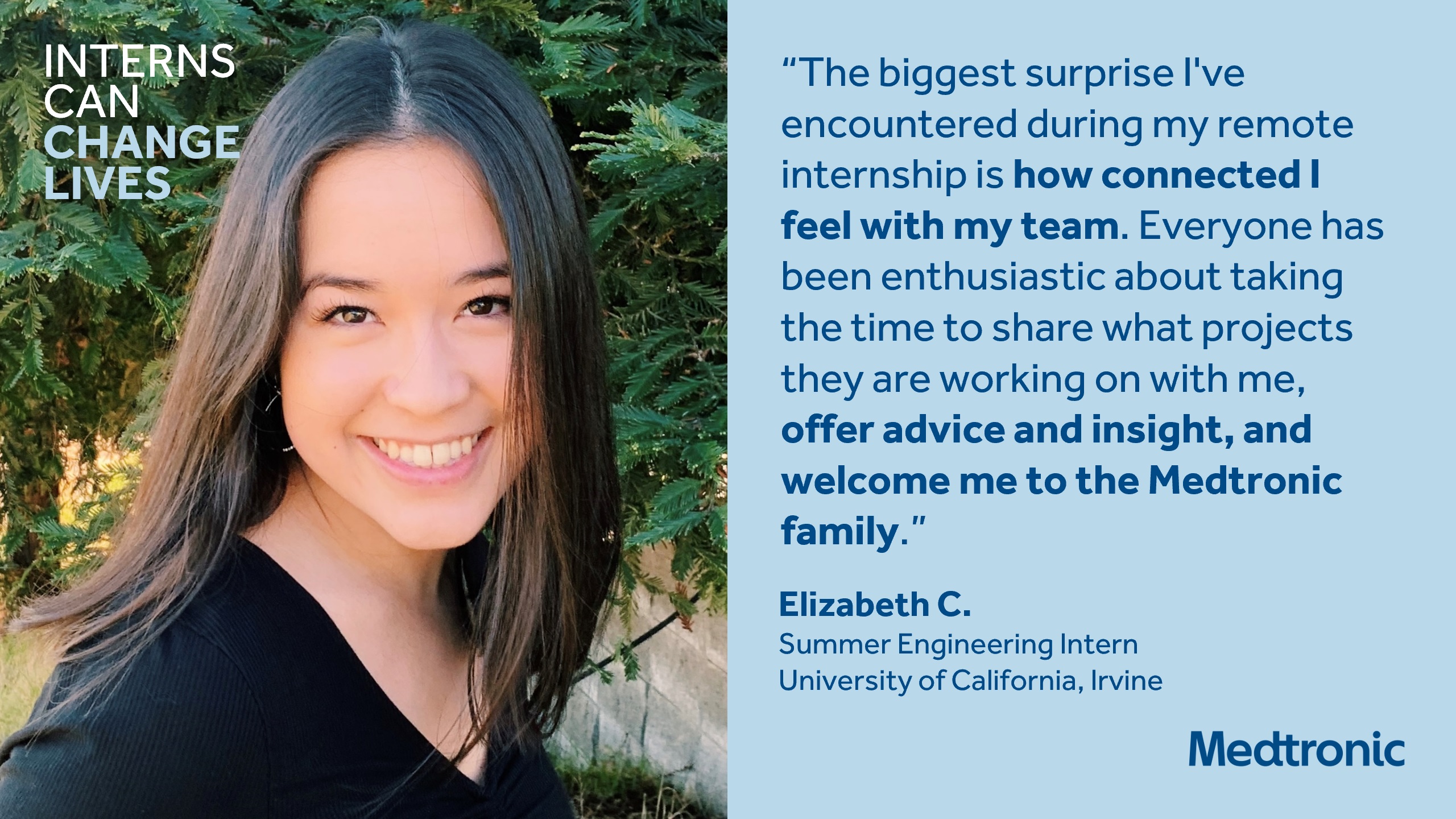
Train engineers not only have a decent income, but they also enjoy many other perks. The average train engineer salary is greater than the average person's lifetime earnings. About one percent of the demand for railroad transport occupations will increase. The train engineer salary can fluctuate depending on your experience and location. Some train engineers make over $100,000 each year after many years of working in the industry.
A train engineer's job isn’t easy. First, you need to obtain federal licensing. After you receive your license you will need to acquire some work experience before you can begin your own business. You will need to pass an exam in order to receive your certification. This typically includes a vision test and an eye test. If you pass, then you are eligible to work with federal railroads as well as other transportation agencies.
You may work long hours as a train engineer. Many train engineers work weekends and nights. Additionally, your schedule may be irregular, such that you work on holidays or in mornings. You will also be exposed to various types of weather. Some cases may require you to drive electric trains. This can be challenging.
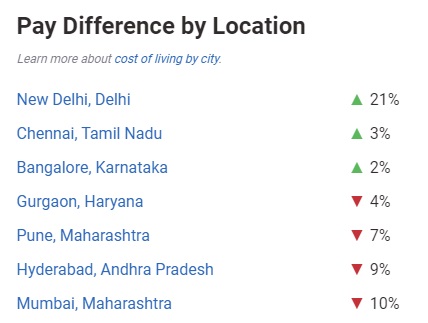
An aptitude test will be taken to determine your mechanical abilities. You will need to be able see clearly and have good hand-eye coordination. Sometimes you may have to drive freight trains.
You may need to work in darkness depending on where you live. Or you might be required to be available 24 hours a days. It's a great job that can bring in a lot of money, as long as your ability to do the job. Large rail companies have the best salaries for train engineers. Although they offer their own training programs for engineers, you can still get certified through a school of trades if your goal is to work for smaller railroads.
Additionally, you'll need to have a solid high school diploma as well as a clean criminal record. A degree in train engineering is not necessary, but it can help you stand out to employers. You can also attend a trade school or community college and earn certification that will allow you to take a job as a train engineer.
Average train engineer salaries are $5,254 per month. The salary of train engineers can vary depending on where you live, how much experience you have, and what your employer offers. For train engineers, most companies pay $75,000 to $80,000 per year. The top earners make up to $186,000 each year. You might even be able to get a higher salary than the average if you know where to look. It's also a good idea to look out for job opportunities.
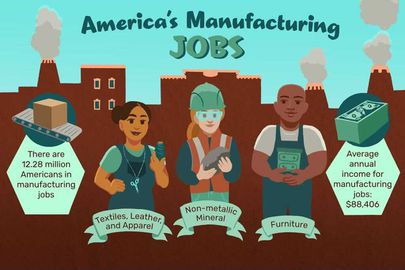
An advanced degree can also help increase your earnings. Some locomotive engineers become railroad schedulers and train trainers. Train engineers are often happy with their job and will work for years.
FAQ
Is it possible to automate certain parts of manufacturing
Yes! Since ancient times, automation has been in existence. The Egyptians discovered the wheel thousands and years ago. Robots are now used to assist us in assembly lines.
There are many applications for robotics in manufacturing today. These include:
-
Robots for assembly line
-
Robot welding
-
Robot painting
-
Robotics inspection
-
Robots that create products
Manufacturing can also be automated in many other ways. 3D printing is a way to make custom products quickly and without waiting weeks or months for them to be manufactured.
What is the role of a production manager?
Production planners make sure that every aspect of the project is delivered on-time, within budget, and within schedule. They also ensure the quality of the product and service meets the client's requirements.
What are the 4 types of manufacturing?
Manufacturing is the process that transforms raw materials into useful products. Manufacturing can include many activities such as designing and building, testing, packaging shipping, selling, servicing, and other related activities.
Is there anything we should know about Manufacturing Processes prior to learning about Logistics.
No. No. Knowing about manufacturing processes will help you understand how logistics works.
Statistics
- According to a Statista study, U.S. businesses spent $1.63 trillion on logistics in 2019, moving goods from origin to end user through various supply chain network segments. (netsuite.com)
- According to the United Nations Industrial Development Organization (UNIDO), China is the top manufacturer worldwide by 2019 output, producing 28.7% of the total global manufacturing output, followed by the United States, Japan, Germany, and India.[52][53] (en.wikipedia.org)
- (2:04) MTO is a production technique wherein products are customized according to customer specifications, and production only starts after an order is received. (oracle.com)
- Many factories witnessed a 30% increase in output due to the shift to electric motors. (en.wikipedia.org)
- Job #1 is delivering the ordered product according to specifications: color, size, brand, and quantity. (netsuite.com)
External Links
How To
How to Use Lean Manufacturing in the Production of Goods
Lean manufacturing is an approach to management that aims for efficiency and waste reduction. It was first developed in Japan in the 1970s/80s by Taiichi Ahno, who was awarded the Toyota Production System (TPS), award from KanjiToyoda, the founder of TPS. Michael L. Watkins published the first book on lean manufacturing in 1990.
Lean manufacturing is often defined as a set of principles used to improve the quality, speed, and cost of products and services. It emphasizes eliminating waste and defects throughout the value stream. Lean manufacturing is also known as just in time (JIT), zero defect total productive maintenance(TPM), and five-star (S). Lean manufacturing is about eliminating activities that do not add value, such as inspection, rework, and waiting.
In addition to improving product quality and reducing costs, lean manufacturing helps companies achieve their goals faster and reduces employee turnover. Lean manufacturing has been deemed one of the best ways to manage the entire value-chain, including customers, distributors as well retailers and employees. Lean manufacturing practices are widespread in many industries. Toyota's philosophy is a great example of this. It has helped to create success in automobiles as well electronics, appliances and healthcare.
Five basic principles of Lean Manufacturing are included in lean manufacturing
-
Define value - Find out what your business contributes to society, and what makes it different from other competitors.
-
Reduce Waste - Eliminate any activity that doesn't add value along the supply chain.
-
Create Flow: Ensure that the work process flows without interruptions.
-
Standardize and simplify – Make processes as repeatable and consistent as possible.
-
Develop Relationships: Establish personal relationships both with internal and external stakeholders.
Lean manufacturing isn’t new, but it has seen a renewed interest since 2008 due to the global financial crisis. Many businesses have adopted lean manufacturing techniques to help them become more competitive. In fact, some economists believe that lean manufacturing will be an important factor in economic recovery.
Lean manufacturing is now becoming a common practice in the automotive industry, with many benefits. These include higher customer satisfaction levels, reduced inventory levels as well as lower operating costs.
It can be applied to any aspect of an organisation. However, it is particularly useful when applied to the production side of an organization because it ensures that all steps in the value chain are efficient and effective.
There are three main types in lean manufacturing
-
Just-in Time Manufacturing, (JIT): This kind of lean manufacturing is also commonly known as "pull-systems." JIT is a method in which components are assembled right at the moment of use, rather than being manufactured ahead of time. This method reduces lead times, increases availability, and decreases inventory.
-
Zero Defects Manufacturing (ZDM),: ZDM is a system that ensures no defective units are left the manufacturing facility. It is better to repair a part than have it removed from the production line if it needs to be fixed. This applies to finished products, which may need minor repairs before they are shipped.
-
Continuous Improvement (CI), also known as Continuous Improvement, aims at improving the efficiency of operations through continuous identification and improvement to minimize or eliminate waste. Continuous improvement involves continuous improvement of processes and people as well as tools.