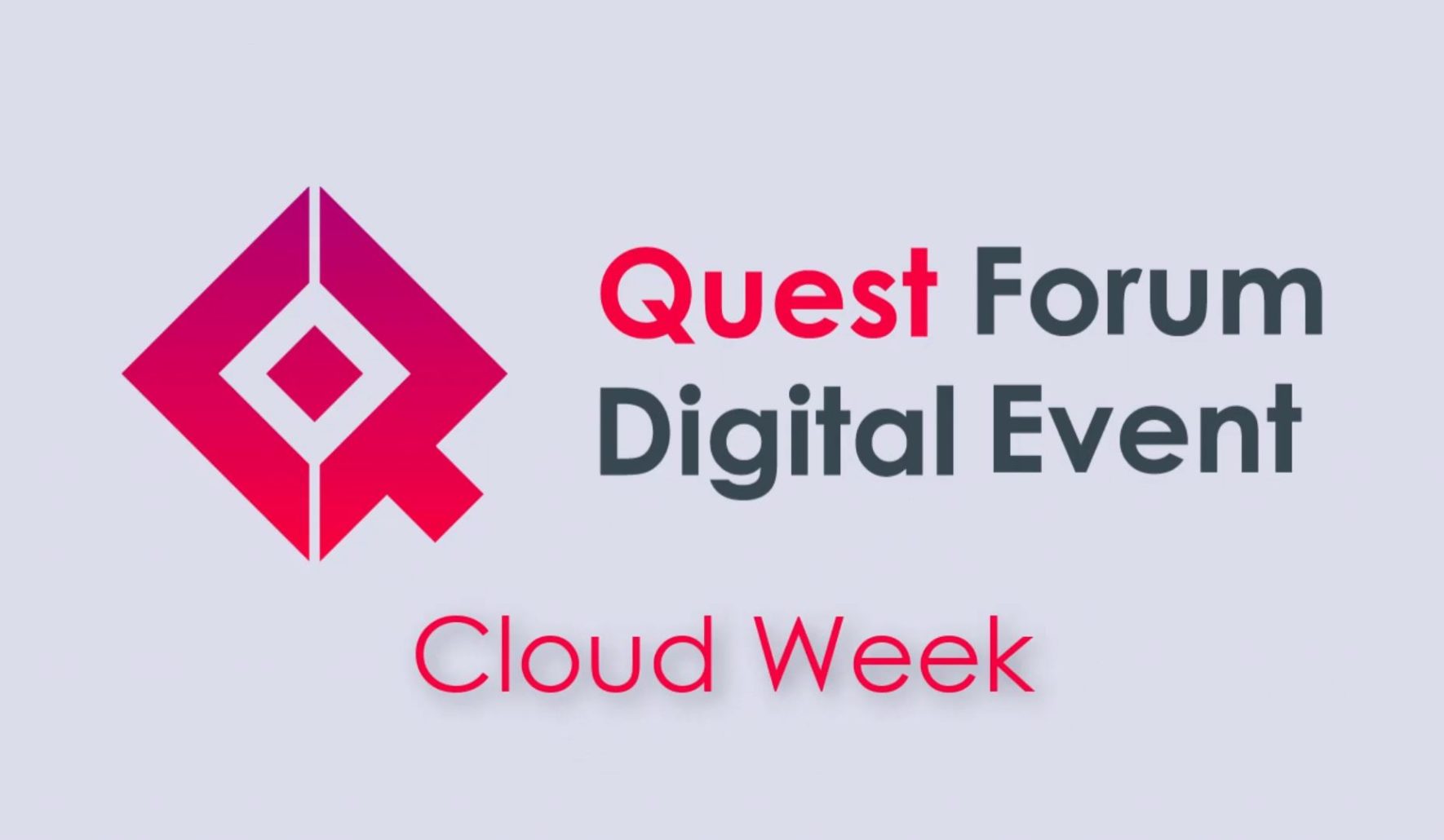
Toyota Motor Manufacturing Indiana Inc. was established in Gibson County, Indiana. It is the first Toyota factory to be 100% owned in the United States. It produces Toyota's full-size pickup trucks including the Avalon, Corolla and Corolla as well as the Sienna minivan. The Toyota RAV4 Hybrid is also produced here, making it the most popular hybrid Toyota has ever made.
The original plan was to produce the Toyota Highlander. However, the plant was moved to Gibson County in Indiana. The Lexus ES 350 and RAV4 Hybrid compact SUVs have been manufactured at the plant by Toyota since 2011. In 2017, Toyota spent more than $1.33 billion at the plant.
Toyota Safety Sense 2.5+ features automatic emergency braking and is also produced at this plant. The plant is currently in the process of preparing all 2018 Camry models. The new model features a new transmission, more power, and a more stylish design. It will cost $25,900.
The largest American manufacturer of the Toyota Camry, Toyota. It's the top-selling midsize sedan in America at present, and has been for 15 consecutive years. In Kentucky, Toyota has made 10 million Camry cars. This plant is the first to produce the hybrid model in North America.
The Toyota Production System is a collection of practices and techniques that improve quality and efficiency. This system also includes the Toyota Production Engineering and Manufacturing Center. It will house 600 Toyota employees. The center will also be the first to assemble hydrogen fuel cell modules for heavy duty commercial trucks. This facility can manufacture up to 100,000 vehicles each year.
In the last five years, Toyota has invested $1.5 billion in the plant. It has also hired 700 additional workers. The investment will result in 470,100 new jobs in the United States by 2020. Toyota has invested more than $147million in Kentucky-based nonprofit partners since 1986.
The Toyota Camry has a reputation for being dependable and fashionable. It has the GA-K platform, and a new transmission. It also has a fun driving experience. In July of this year, Consumer Reports highlighted the Toyota Camry as one of the best-selling cars in America.
The Toyota production system includes a number of elements, including continuous improvement, just-in-time parts delivery, and a sophisticated robotic welding system. Toyota has made good use of its Kentucky investment by building the Toyota Production Engineering and Manufacturing Center.
Toyota can save money on air conditioning and construction costs with a new production hall design. The Visitor Center features interactive video displays and exhibits related to hybrid technology. Toyota will make up to 2,000,000 cars in North America within the next 10 years. This is the largest Toyota factory outside Japan.
Toyota's New Global Architecture (or New Global Architecture) is a huge step forward in improving Toyota's production process. This strategy includes a new engine and production organization, as well as a module that unifies vehicle components. The new design keeps Toyota's innovative spirit alive while still preserving its traditional values.
FAQ
What is production planning?
Production Planning includes planning for all aspects related to production. This document ensures that everything is prepared and available when you are ready for shooting. This document should include information about how to achieve the best results on-set. This includes shooting schedules, locations, cast lists, crew details, and equipment requirements.
The first step is to outline what you want to film. You might have an idea of where you want to film, or you may have specific locations or sets in mind. Once you have identified the scenes and locations, you can start to determine which elements are required for each scene. If you decide you need a car and don't know what model to choose, this could be an example. If this is the case, you might start searching online for car models and then narrow your options by selecting from different makes.
Once you have found the right vehicle, you can think about adding accessories. Do you need people sitting in the front seats? Maybe you need someone to move around in the back. Maybe you want to change the interior color from black to white? These questions will help guide you in determining the ideal look and feel for your car. The type of shots that you are looking for is another thing to consider. Are you going to be shooting close-ups? Or wide angles? Maybe the engine or steering wheel is what you are looking to film. All of these things will help you identify the exact style of car you want to film.
Once you have made all the necessary decisions, you can start to create a schedule. A schedule will tell you when you need to start shooting and when you need to finish. The schedule will show you when to get there, what time to leave, and when to return home. So everyone is clear about what they need to do. It is possible to make arrangements in advance for additional staff if you are looking to hire. You should not hire anyone who doesn't show up because of your inaction.
Your schedule will also have to be adjusted to reflect the number of days required to film. Some projects only take one or two days, while others may last weeks. When creating your schedule, be aware of whether you need more shots per day. Multiplying takes in the same area will result both in increased costs and a longer time. You can't be certain if you will need multiple takes so it is better not to shoot too many.
Budget setting is another important aspect in production planning. You will be able to manage your resources if you have a realistic budget. You can always lower the budget if you encounter unexpected problems. You shouldn't underestimate the amount you'll spend. Underestimating the cost will result in less money after you have paid for other items.
Production planning is a complicated process. But once you understand how everything works together, it becomes much easier to plan future project.
What types of jobs can you find in logistics
There are many types of jobs in logistics. Here are some examples:
-
Warehouse workers - They load and unload trucks and pallets.
-
Transportation drivers: They drive trucks and trailers and deliver goods and make pick-ups.
-
Freight handlers – They sort and package freight at warehouses.
-
Inventory managers: They are responsible for the inventory and management of warehouses.
-
Sales representatives - They sell products.
-
Logistics coordinators - They organize and plan logistics operations.
-
Purchasing agents - They buy goods and services that are necessary for company operations.
-
Customer service representatives - They answer calls and emails from customers.
-
Shipping clerks – They process shipping orders, and issue bills.
-
Order fillers: They fill orders based off what has been ordered and shipped.
-
Quality control inspectors - They check incoming and outgoing products for defects.
-
Others - There are many types of jobs in logistics such as transport supervisors and cargo specialists.
What are the 7 Rs of logistics?
The acronym 7R's of Logistic is an acronym that stands for seven fundamental principles of logistics management. It was developed by International Association of Business Logisticians (IABL), and published as part of their "Seven Principles of Logistics Management Series" in 2004.
The following letters form the acronym:
-
Responsible - ensure that all actions taken are within legal requirements and are not harmful to others.
-
Reliable – have faith in your ability and capability to keep promises.
-
Be responsible - Use resources efficiently and avoid wasting them.
-
Realistic – Consider all aspects, including cost-effectiveness as well as environmental impact.
-
Respectful - Treat people fairly and equitably
-
Reliable - Find ways to save money and increase your productivity.
-
Recognizable - Provide value-added services to customers
What does it take for a logistics enterprise to succeed?
It takes a lot of skills and knowledge to run a successful logistics business. Effective communication skills are necessary to work with suppliers and clients. You need to understand how to analyze data and draw conclusions from it. You must be able and able to handle stress situations and work under pressure. You must be creative and innovative to develop new ideas to improve efficiency. Strong leadership qualities are essential to motivate your team and help them achieve their organizational goals.
It is important to be organized and efficient in order to meet tight deadlines.
Statistics
- Job #1 is delivering the ordered product according to specifications: color, size, brand, and quantity. (netsuite.com)
- You can multiply the result by 100 to get the total percent of monthly overhead. (investopedia.com)
- It's estimated that 10.8% of the U.S. GDP in 2020 was contributed to manufacturing. (investopedia.com)
- In the United States, for example, manufacturing makes up 15% of the economic output. (twi-global.com)
- According to the United Nations Industrial Development Organization (UNIDO), China is the top manufacturer worldwide by 2019 output, producing 28.7% of the total global manufacturing output, followed by the United States, Japan, Germany, and India.[52][53] (en.wikipedia.org)
External Links
How To
How to use the Just-In Time Method in Production
Just-in-time (JIT) is a method that is used to reduce costs and maximize efficiency in business processes. It's a way to ensure that you get the right resources at just the right time. This means that you only pay the amount you actually use. Frederick Taylor was the first to coin this term. He developed it while working as a foreman during the early 1900s. He saw how overtime was paid to workers for work that was delayed. He decided to ensure workers have enough time to do their jobs before starting work to improve productivity.
The idea behind JIT is that you should plan ahead and have everything ready so you don't waste money. Also, you should look at the whole project from start-to-finish and make sure you have the resources necessary to address any issues. You can anticipate problems and have enough equipment and people available to fix them. This will ensure that you don't spend more money on things that aren't necessary.
There are many types of JIT methods.
-
Demand-driven: This type of JIT allows you to order the parts/materials required for your project on a regular basis. This will allow to track how much material has been used up. This will allow you to calculate how long it will take to make more.
-
Inventory-based: This is a type where you stock the materials required for your projects in advance. This allows for you to anticipate how much you can sell.
-
Project-driven: This approach involves setting aside sufficient funds to cover your project's costs. When you know how much you need, you'll purchase the appropriate amount of materials.
-
Resource-based JIT: This is the most popular form of JIT. You assign certain resources based off demand. For instance, if you have a lot of orders coming in, you'll assign more people to handle them. You'll have fewer orders if you have fewer.
-
Cost-based: This approach is very similar to resource-based. However, you don't just care about the number of people you have; you also need to consider how much each person will cost.
-
Price-based pricing: This is similar in concept to cost-based but instead you look at how much each worker costs, it looks at the overall company's price.
-
Material-based is an alternative to cost-based. Instead of looking at the total cost in the company, this method focuses on the average amount of raw materials that you consume.
-
Time-based JIT is another form of resource-based JIT. Instead of focusing solely on the amount each employee costs, focus on how long it takes for the project to be completed.
-
Quality-based JIT - This is another form of resource-based JIT. Instead of thinking about the cost of each employee or the time it takes to produce something, you focus on how good your product quality.
-
Value-based JIT : This is the newest type of JIT. In this scenario, you're not concerned about how products perform or whether customers expect them to meet their expectations. Instead, you're focused on how much value you add to the market.
-
Stock-based is an inventory-based system that measures the number of items produced at any given moment. It's useful when you want maximum production and minimal inventory.
-
Just-in-time planning (JIT): This is a combination JIT and supply-chain management. It's the process of scheduling delivery of components immediately after they are ordered. This is important as it reduces lead time and increases throughput.