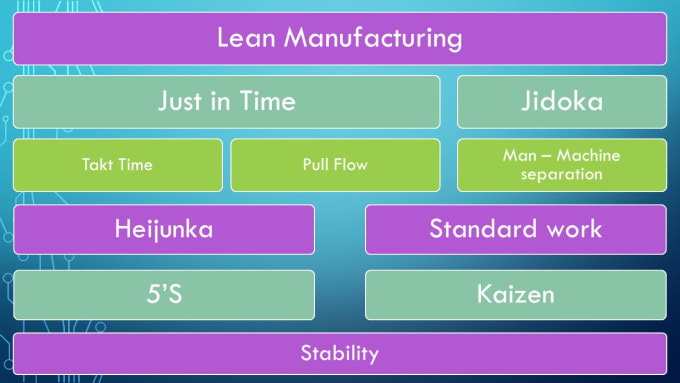
It is crucial to get the best value for money when selecting a course for your company. This course will educate you about the importance of procurement and the role that procurement management plays in business. These are some factors that you need to consider when making a decision. Learn more about Cost-based pricing, Contracting, and Negotiating to make the best possible deal for your business. Here are some of the key points to consider when selecting a course provider:
Cost-based pricing
Future Procurement teaches Cost-Based Pricing to production and purchasing professionals. This course is designed to help both novice and experienced procurement professionals understand and apply Cost-Based Pricing in their daily work. It's available online and can be downloaded free of charge. The course teaches you about CBP and how it works with different types and courses. You should consider a few things when you implement CBP in your course acquisition strategy.
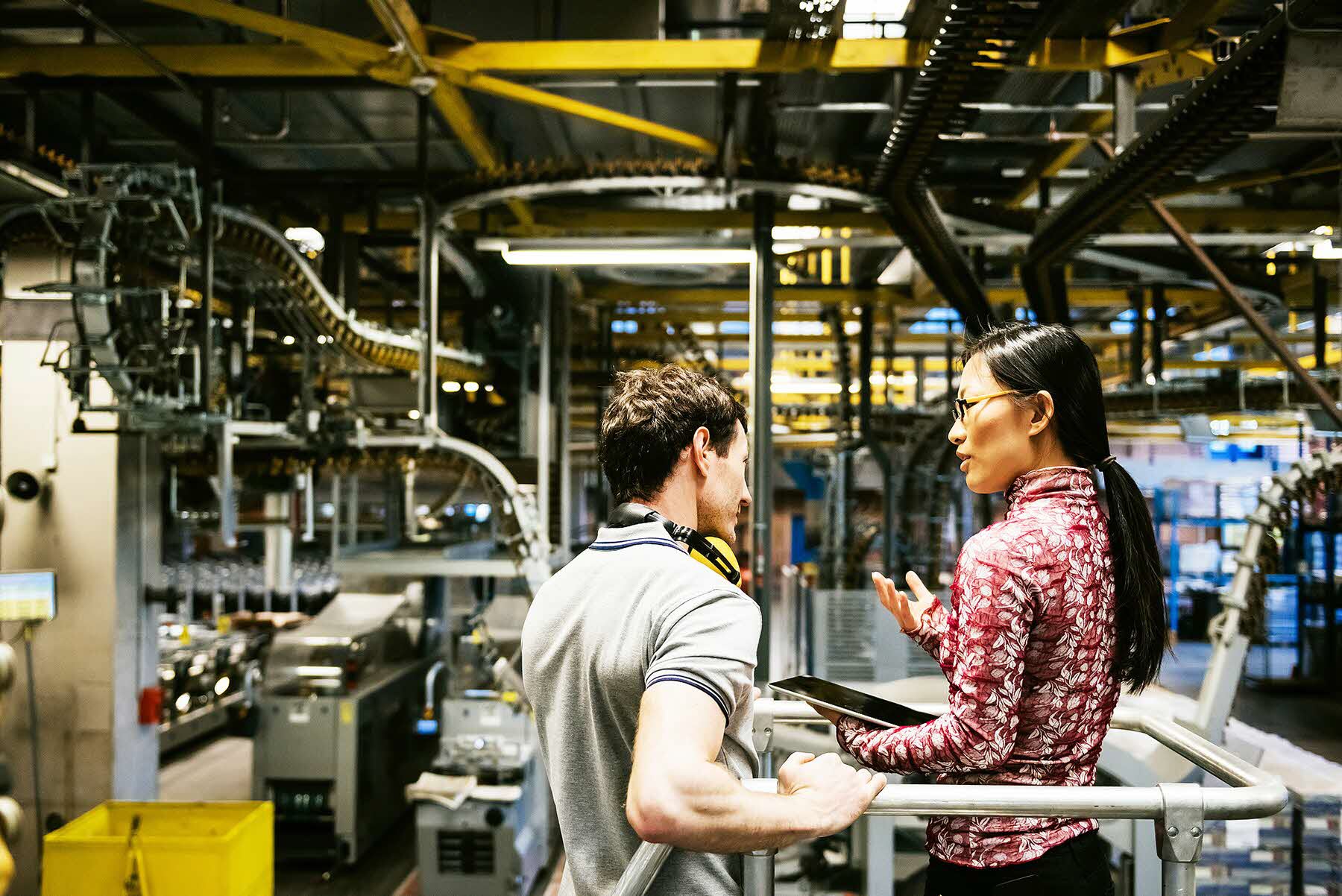
Negotiating
A negotiation course is a great way to improve your negotiation skills. A variety of negotiation courses are offered, including online and classroom versions. The course helps you understand the fundamentals of how to communicate effectively and establish mutually beneficial relationships. This course can also help you get a job in the negotiation field. Read on for more information. Below are some tips for getting the most out this course.
Contracting
This workshop is beneficial for students interested in contracting careers. This workshop will cover the various activities involved in the sourcing process. This workshop will be useful to anyone involved in the procurement process, whether new to the field or in need of a refresher. These are the purposes of the workshop.
Collaboration with external partners
The course is taught in a facilitated classroom environment and includes six sessions that use case studies, workbooks, real-world experience procurement, and each uses workbooks. Participants will engage in role-playing exercises to learn and test their understanding of the course. This course is intended to increase awareness about sales techniques and behaviors. We will be discussing some of the advantages of this workshop and what to expect from it.
Certifications
The Certificate in Course Procurement, (CPP), will allow you to learn about the basics of supply chain management. Additionally, you will be able to learn about the latest trends and current issues in this field. You will be able to improve your negotiation and result skills which will help you stand out from your competitors. A 2.5 grade point average is recommended and the program must be completed within three years. This course will teach about legal and regulatory considerations which affect the procurement procedure.
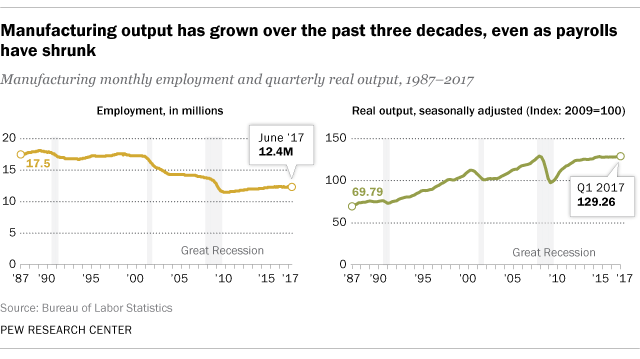
Course platforms
There are many courses platforms to choose from, each with its strengths and limitations. Some are premium, offering social learning tools and high interactivity. Others offer a simpler interface, with fewer features, and are simpler. Teachable, which was one of the first online course platforms, remains one of the strongest options. However, you may consider looking elsewhere if you want to market your course to the public.
FAQ
What are the products and services of logistics?
Logistics are the activities involved in moving goods from point A to point B.
They include all aspects associated with transport including packaging, loading transporting, unloading storage, warehousing inventory management customer service, distribution returns and recycling.
Logisticians ensure that the product is delivered to the correct place, at the right time, and under safe conditions. Logisticians help companies improve their supply chain efficiency by providing information about demand forecasts and stock levels, production schedules, as well as availability of raw materials.
They also keep track of shipments in transit, monitor quality standards, perform inventories and order replenishment, coordinate with suppliers and vendors, and provide support services for sales and marketing.
How can we increase manufacturing efficiency?
The first step is to determine the key factors that impact production time. The next step is to identify the most important factors that affect production time. If you don’t know where to begin, consider which factors have the largest impact on production times. Once you have identified the factors, then try to find solutions.
What is the job of a production plan?
A production planner makes sure all project elements are delivered on schedule, within budget, as well as within the agreed scope. They make sure that the product and services meet client expectations.
Statistics
- According to a Statista study, U.S. businesses spent $1.63 trillion on logistics in 2019, moving goods from origin to end user through various supply chain network segments. (netsuite.com)
- In 2021, an estimated 12.1 million Americans work in the manufacturing sector.6 (investopedia.com)
- [54][55] These are the top 50 countries by the total value of manufacturing output in US dollars for its noted year according to World Bank.[56] (en.wikipedia.org)
- You can multiply the result by 100 to get the total percent of monthly overhead. (investopedia.com)
- (2:04) MTO is a production technique wherein products are customized according to customer specifications, and production only starts after an order is received. (oracle.com)
External Links
How To
Six Sigma in Manufacturing
Six Sigma refers to "the application and control of statistical processes (SPC) techniques in order to achieve continuous improvement." Motorola's Quality Improvement Department created Six Sigma at their Tokyo plant, Japan in 1986. The basic idea behind Six Sigma is to improve quality by improving processes through standardization and eliminating defects. Since there are no perfect products, or services, this approach has been adopted by many companies over the years. Six Sigma aims to reduce variation in the production's mean value. It is possible to measure the performance of your product against an average and find the percentage of time that it differs from the norm. If it is too large, it means that there are problems.
Understanding the nature of variability in your business is the first step to Six Sigma. Once you've understood that, you'll want to identify sources of variation. You'll also want to determine whether these variations are random or systematic. Random variations happen when people make errors; systematic variations are caused externally. If you make widgets and some of them end up on the assembly line, then those are considered random variations. But if you notice that every widget you make falls apart at the exact same place each time, this would indicate that there is a problem.
After identifying the problem areas, you will need to devise solutions. That solution might involve changing the way you do things or redesigning the process altogether. Once you have implemented the changes, it is important to test them again to ensure they work. If they fail, you can go back to the drawing board to come up with a different plan.