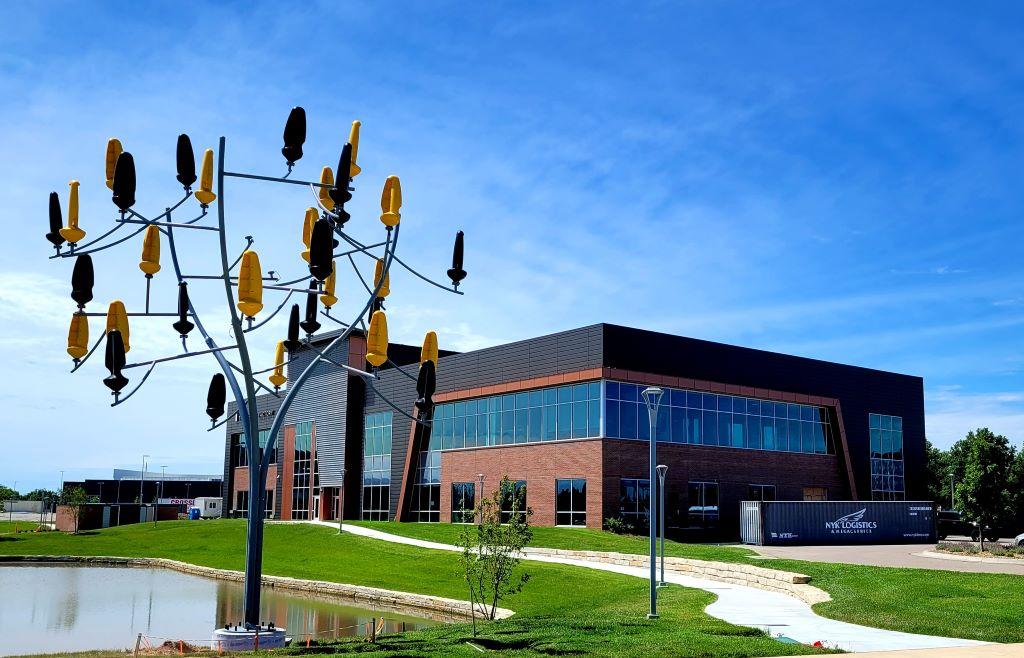
Ohio's Great Recession saw the loss of 166,000 manufacturing jobs. Although Ohio's manufacturing sector has seen some improvement, it is still slower than other states. Ohio's manufacturing employment is still below its pre-recession levels.
The decline of manufacturing jobs in Ohio is a result of the resurgence of manufacturing competition from Japan and Europe. Manufacturers have had to improve their technology and cut labor costs. The global economic climate has been very lukewarm, which has resulted in job losses.
The current workforce shortage is one of the most significant challenges Ohio manufacturers face. However, there are several initiatives in the state to address the skilled labor shortage. These initiatives are siloed and fragmented, and do not address all of the workforce challenges manufacturers face. The Ohio Governor's Office of Workforce Transformation released a special report about the workforce shortage. It recommended greater collaboration between businesses and educators. The report revealed a disconnect between school curriculum and business requirements.
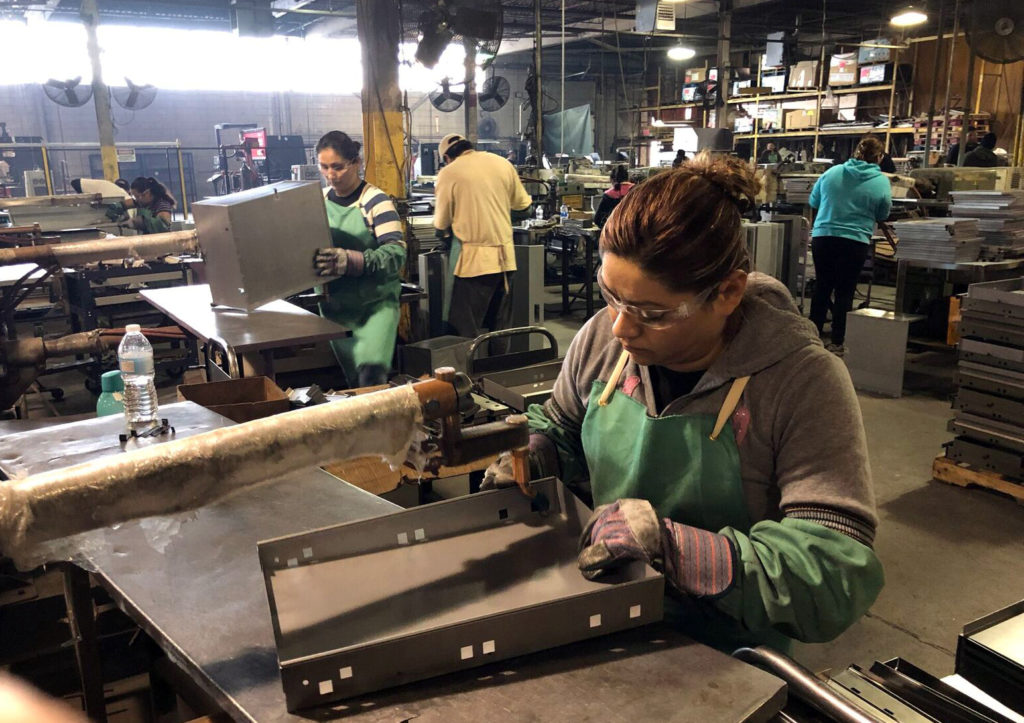
Ohio's workforce has many faces and is diverse. The likelihood of manufacturing workers being represented by a union is lower than that of workers in other sectors in Ohio. However, unionized jobs in manufacturing still offer livable salaries and solid benefits.
Ohio's manufacturing industries are a major contributor of the state's economy. Interstate highways, railways and inland waterways allow manufacturers to efficiently distribute goods. Additionally, the state is a top exporter. The state also produces natural gaz, which is a big draw for private investors.
Despite the fact that the state has been able to recover over 50,000 manufacturing jobs within the last four year, Kasich's term as president saw little improvement in job growth. In Kasich's first three terms, the average manufacturing job gain was 7 percent. Manufacturing jobs have declined by 1,771 jobs between the first and second years of his administration. These losses are due primarily to the slowing economic growth, the auto industry and lukewarm global market demand.
Ohio is a top exporter for goods. The top export markets are the U.S.A., Canada, Mexico and the U.K. In the past year, exports decreased by $1.4 Billion. Ohio manufacturers still face major challenges in trade policy. While changes in trade policy can help workers in specific industries, the full range of challenges will be addressed only by policymakers.
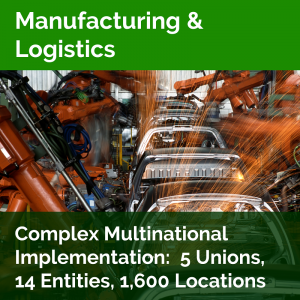
Ohio's main industry, manufacturing, is still very important. Manufacturing jobs offer semi-skilled workers the best opportunities for high-paying jobs without requiring post-secondary education. But wages in Ohio have not kept pace with the production. Manufacturing jobs pay better than other sectors in Ohio but aren't enough to support middle-class lifestyles.
Ohio's diverse workforce of manufacturing workers includes many different workers. Manufacturing industries in Ohio have been diversifying to meet the needs of the rest. The economy has become more service-oriented, and manufacturing is no longer the primary employer in Ohio. Manufacturers are now focusing on developing future skills and international exposure.
FAQ
What types of jobs can you find in logistics
There are many types of jobs in logistics. These are some of the jobs available in logistics:
-
Warehouse workers: They load and unload trucks, pallets, and other cargo.
-
Transportation drivers: They drive trucks and trailers and deliver goods and make pick-ups.
-
Freight handlers – They sort and package freight at warehouses.
-
Inventory managers - They oversee the inventory of goods in warehouses.
-
Sales representatives - They sell products.
-
Logistics coordinators - They organize and plan logistics operations.
-
Purchasing agents - They buy goods and services that are necessary for company operations.
-
Customer service agents - They answer phone calls and respond to emails.
-
Shipping clerks - They process shipping orders and issue bills.
-
Order fillers: They fill orders based off what has been ordered and shipped.
-
Quality control inspectors - They check incoming and outgoing products for defects.
-
Others - There are many types of jobs in logistics such as transport supervisors and cargo specialists.
What does it take to run a logistics business?
To be a successful businessman in logistics, you will need many skills and knowledge. To communicate effectively with clients and suppliers, you must be able to communicate well. You should be able analyse data and draw inferences. You must be able to work well under pressure and handle stressful situations. To increase efficiency and creativity, you need to be creative. You must be a strong leader to motivate others and direct them to achieve organizational goals.
You should also be organized and efficient to meet tight deadlines.
How can manufacturing efficiency be improved?
First, we need to identify which factors are most critical in affecting production times. The next step is to identify the most important factors that affect production time. If you don't know where to start, then think about which factor(s) have the biggest impact on production time. Once you've identified them all, find solutions to each one.
Are there any Manufacturing Processes that we should know before we can learn about Logistics?
No. No. But, being familiar with manufacturing processes will give you a better understanding about how logistics works.
Why automate your factory?
Modern warehouses are increasingly dependent on automation. With the rise of ecommerce, there is a greater demand for faster delivery times as well as more efficient processes.
Warehouses should be able adapt quickly to new needs. They must invest heavily in technology to do this. Automation warehouses can bring many benefits. Here are some reasons why it's worth investing in automation:
-
Increases throughput/productivity
-
Reduces errors
-
Increases accuracy
-
Safety enhancements
-
Eliminates bottlenecks
-
Companies can scale more easily
-
Workers are more productive
-
This gives you visibility into what happens in the warehouse
-
Enhances customer experience
-
Improves employee satisfaction
-
It reduces downtime, and increases uptime
-
Ensures quality products are delivered on time
-
Removes human error
-
Assure compliance with regulations
Statistics
- According to the United Nations Industrial Development Organization (UNIDO), China is the top manufacturer worldwide by 2019 output, producing 28.7% of the total global manufacturing output, followed by the United States, Japan, Germany, and India.[52][53] (en.wikipedia.org)
- Many factories witnessed a 30% increase in output due to the shift to electric motors. (en.wikipedia.org)
- Job #1 is delivering the ordered product according to specifications: color, size, brand, and quantity. (netsuite.com)
- In 2021, an estimated 12.1 million Americans work in the manufacturing sector.6 (investopedia.com)
- According to a Statista study, U.S. businesses spent $1.63 trillion on logistics in 2019, moving goods from origin to end user through various supply chain network segments. (netsuite.com)
External Links
How To
How to use the Just In-Time Production Method
Just-in-time (JIT) is a method that is used to reduce costs and maximize efficiency in business processes. It's the process of obtaining the right amount and timing of resources when you need them. This means that you only pay for what you actually use. Frederick Taylor first coined this term while working in the early 1900s as a foreman. Taylor observed that overtime was paid to workers if they were late in working. He concluded that if workers were given enough time before they start work, productivity would increase.
JIT is a way to plan ahead and make sure you don't waste any money. Look at your entire project, from start to end. Make sure you have enough resources in place to deal with any unexpected problems. You'll be prepared to handle any potential problems if you know in advance. This will prevent you from spending extra money on unnecessary things.
There are many types of JIT methods.
-
Demand-driven JIT: You order the parts and materials you need for your project every other day. This will allow you to track how much material you have left over after using it. This will let you know how long it will be to produce more.
-
Inventory-based: This allows you to store the materials necessary for your projects in advance. This allows one to predict how much they will sell.
-
Project-driven: This approach involves setting aside sufficient funds to cover your project's costs. Knowing how much money you have available will help you purchase the correct amount of materials.
-
Resource-based JIT is the most widespread form. You assign certain resources based off demand. You will, for example, assign more staff to deal with large orders. You'll have fewer orders if you have fewer.
-
Cost-based: This is the same as resource-based except that you don't care how many people there are but how much each one of them costs.
-
Price-based: This is very similar to cost-based, except that instead of looking at how much each individual worker costs, you look at the overall price of the company.
-
Material-based is an alternative to cost-based. Instead of looking at the total cost in the company, this method focuses on the average amount of raw materials that you consume.
-
Time-based JIT is another form of resource-based JIT. Instead of focusing solely on the amount each employee costs, focus on how long it takes for the project to be completed.
-
Quality-based JIT is another variant of resource-based JIT. Instead of worrying about the costs of each employee or how long it takes for something to be made, you should think about how quality your product is.
-
Value-based JIT: One of the most recent forms of JIT. This is where you don't care about how the products perform or whether they meet customers' expectations. Instead, you focus on the added value that you provide to your market.
-
Stock-based. This method is inventory-based and focuses only on the actual production at any given point. It's useful when you want maximum production and minimal inventory.
-
Just-intime planning (JIT), is a combination JIT/sales chain management. It is the process of scheduling components' delivery as soon as they have been ordered. It is essential because it reduces lead-times and increases throughput.