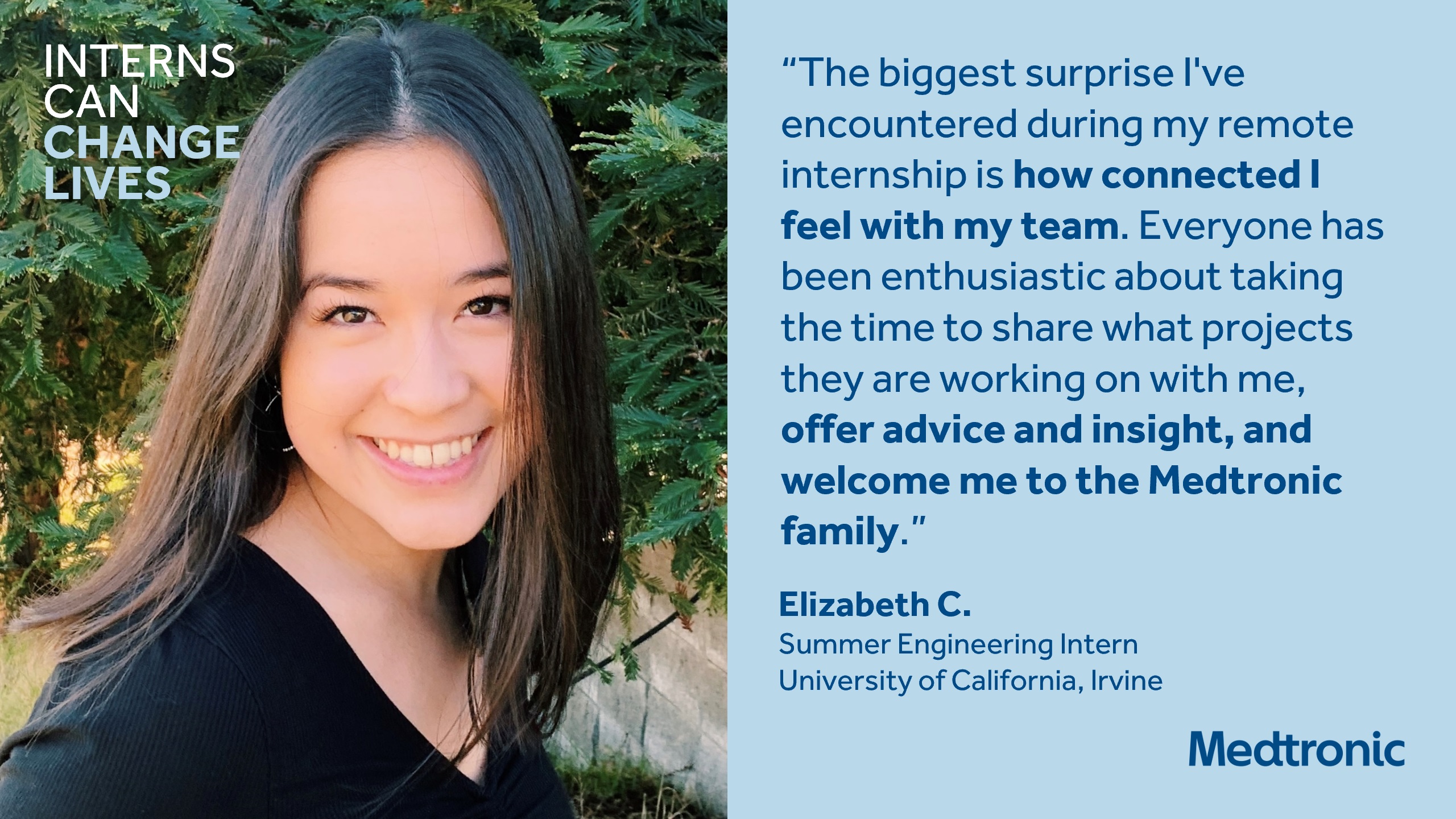
A validation engineer salary is a person's pay for working as a validity engineer. This salary is usually determined by their education, experience and skills. However, it can also be influenced by the type of job they hold and the company they work for.
What Is a Validation Engineer?
A Validation Engineer uses processes, equipment, and procedures to ensure the quality of products. Validation engineers work in the manufacturing, testing and R&D environments to make sure that all systems perform as expected.
What Is the Job of a Validation Engineering?
Validation engineers monitor the performance of the equipment and systems that are used to produce pharmaceutical products. They do this by analyzing, inspecting, testing and calibrating equipment and machinery. They also investigate any malfunctions or anomalies in equipment which could lead to product failure.
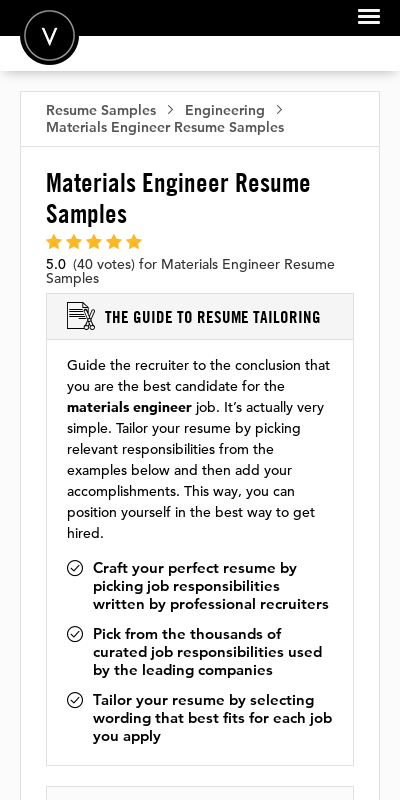
What does a Validation Engineer Salary look like?
The salary of a Validation engineer is high in general, but depends on what type of company you are employed by. The highest salaries are often found in the technology industry, such as Apple and Google. In the pharmaceutical industry, these engineers can expect to make an average of $89,130 per year.
What are some of the most important skills for this profession?
Qualifications for validation engineers include writing, executing and coordinating commissioning/qualification protocols. A validation engineer should have solid technical knowledge in manufacturing, process, and software engineering.
How to become a Validation Engineer
There are a few different routes into a validation engineer role, either by gaining a degree or through an apprenticeship scheme. Employers require that candidates hold a bachelor's in a relevant discipline of engineering, such electrical, mechanical or computer software.
Then, you can gain experience through an internship or placement in a graduate program for engineers. Find jobs online, through newspapers and recruitment agencies.
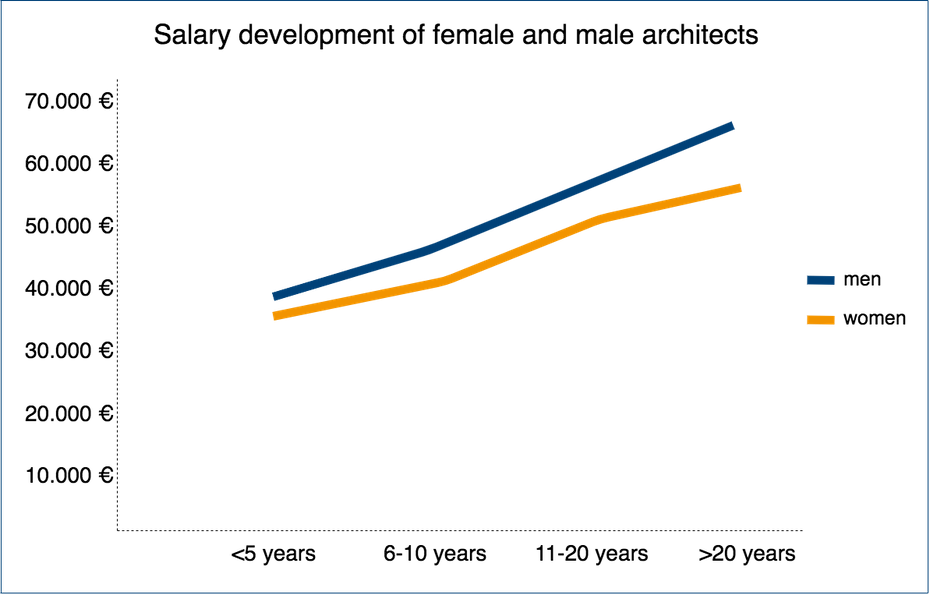
How to Become A Pharmaceutical Validation Engineer
To be a validator engineer, you need to have the right combination between academic credentials and practical experience. You must have a relevant engineering or science degree, and you should also be familiar with the pharmaceutical industry. It can be challenging, but perseverance is key to developing your skills and finding a job that matches your qualifications and aspirations.
How to Become a Pharma Validation Engineer
There is a clear career path for validation engineers, with positions available at varying levels of responsibility. As a senior engineering, you may have managerial responsibilities as well as the opportunity to travel overseas. You can also take on roles that will allow you to specialize in a certain field, like CSV or drugs delivery technologies.
Salary can vary for a validation engineer in pharmaceuticals depending on what industry they are working in and which products they deal with. While the national average for a pharmaceutical validation engineer is $98,150, some cities are more lucrative than others. Hayward, CA for instance, is $18,034 higher than the national average, while San Jose, CA comes in at number one with $21,856.
FAQ
Is automation necessary in manufacturing?
Automation is important not only for manufacturers but also for service providers. Automation allows them to deliver services quicker and more efficiently. They can also reduce their costs by reducing human error and improving productivity.
What types of jobs can you find in logistics
Logistics can offer many different jobs. Some examples are:
-
Warehouse workers: They load and unload trucks, pallets, and other cargo.
-
Transport drivers - These are people who drive trucks and trailers to transport goods or perform pick-ups.
-
Freight handlers - They sort and pack freight in warehouses.
-
Inventory managers - These are responsible for overseeing the stock of goods in warehouses.
-
Sales representatives - They sell products to customers.
-
Logistics coordinators – They plan and coordinate logistics operations.
-
Purchasing agents: They are responsible for purchasing goods and services to support company operations.
-
Customer service representatives are available to answer customer calls and emails.
-
Shipping clerks: They process shipping requests and issue bills.
-
Order fillers: They fill orders based off what has been ordered and shipped.
-
Quality control inspectors - They check incoming and outgoing products for defects.
-
Others - There is a variety of other jobs in logistics. These include transportation supervisors and cargo specialists.
What is the job of a manufacturer manager?
A manufacturing manager must make sure that all manufacturing processes run smoothly and effectively. They should also be aware and responsive to any company problems.
They should also know how to communicate with other departments such as sales and marketing.
They should also be knowledgeable about the latest trends in the industry so they can use this information for productivity and efficiency improvements.
Statistics
- Many factories witnessed a 30% increase in output due to the shift to electric motors. (en.wikipedia.org)
- Job #1 is delivering the ordered product according to specifications: color, size, brand, and quantity. (netsuite.com)
- In 2021, an estimated 12.1 million Americans work in the manufacturing sector.6 (investopedia.com)
- According to a Statista study, U.S. businesses spent $1.63 trillion on logistics in 2019, moving goods from origin to end user through various supply chain network segments. (netsuite.com)
- You can multiply the result by 100 to get the total percent of monthly overhead. (investopedia.com)
External Links
How To
How to Use Just-In-Time Production
Just-in-time is a way to cut costs and increase efficiency in business processes. It's a way to ensure that you get the right resources at just the right time. This means that you only pay the amount you actually use. Frederick Taylor was the first to coin this term. He developed it while working as a foreman during the early 1900s. After observing how workers were paid overtime for late work, he realized that overtime was a common practice. He realized that workers should have enough time to complete their jobs before they begin work. This would help increase productivity.
JIT is an acronym that means you need to plan ahead so you don’t waste your money. Look at your entire project, from start to end. Make sure you have enough resources in place to deal with any unexpected problems. If you anticipate that there might be problems, you'll have enough people and equipment to fix them. You won't have to pay more for unnecessary items.
There are many types of JIT methods.
-
Demand-driven: This is a type of JIT where you order the parts/materials needed for your project regularly. This will let you track the amount of material left over after you've used it. You'll also be able to estimate how long it will take to produce more.
-
Inventory-based: This allows you to store the materials necessary for your projects in advance. This allows you to predict how much you can expect to sell.
-
Project-driven: This is an approach where you set aside enough funds to cover the cost of your project. Knowing how much money you have available will help you purchase the correct amount of materials.
-
Resource-based JIT is the most widespread form. This is where you assign resources based upon demand. If you have many orders, you will assign more people to manage them. If you don't have many orders, you'll assign fewer people to handle the workload.
-
Cost-based: This is similar to resource-based, except that here you're not just concerned about how many people you have but how much each person costs.
-
Price-based: This is very similar to cost-based, except that instead of looking at how much each individual worker costs, you look at the overall price of the company.
-
Material-based is an alternative to cost-based. Instead of looking at the total cost in the company, this method focuses on the average amount of raw materials that you consume.
-
Time-based JIT: A variation on resource-based JIT. Instead of focusing on the cost of each employee, you will focus on the time it takes to complete a project.
-
Quality-based JIT: Another variation on resource-based JIT. Instead of thinking about the cost of each employee or the time it takes to produce something, you focus on how good your product quality.
-
Value-based: This is one of the newest forms of JIT. In this case, you're not concerned with how well the products perform or whether they meet customer expectations. Instead, you focus on the added value that you provide to your market.
-
Stock-based: This is an inventory-based method that focuses on the actual number of items being produced at any given time. It's useful when you want maximum production and minimal inventory.
-
Just-intime planning (JIT), is a combination JIT/sales chain management. This refers to the scheduling of the delivery of components as soon after they are ordered. This is important as it reduces lead time and increases throughput.