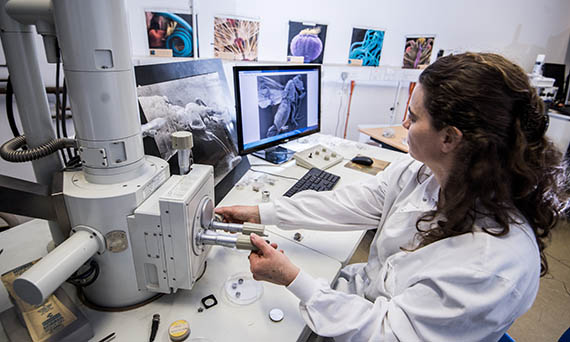
Facilities engineers are also known as maintenance engineers. They provide support in the engineering and construction of buildings and operations. Some of their duties include developing and implementing procedures, recommending repair and upgrades, and coordinating routine and emergency maintenance. They can be involved in a variety of engineering disciplines including plumbing, electrical, and mechanical. Aside from their technical expertise, they have a good understanding of construction law, safety standards and other regulatory requirements.
Facilities engineers are a great career choice. They can easily move up to senior positions from their entry-level position. It is important to have a solid portfolio that includes research, articles, and engineering projects. Facilities engineers need to continue learning about their field. This will enable them to stand out in a job application.
While it is not required for all facilities engineers to have a professional engineer certificate, it can be an advantage when applying for a new job. An engineer must have a good understanding of engineering principles and concepts. They should also be able to make compelling presentations and analyze data. Facilities engineers, for instance, need to have experience in asset reliability-centered strategies and predictive maintenance.

Facility engineers have a variety of jobs. They can be found in manufacturing, construction or office settings. They manage and implement processes that ensure safe, efficient, effective, and reliable operation of utility systems. Facilities engineers work closely with managers and other engineers. This helps to make work more efficient and resolves any problems.
Based on the size or type of facility, the duties of a facilities engineering will vary. The job requires good time management skills and problem-solving skills. It also requires the ability to work well in a team environment. On a typical working day, a facilities manager may be responsible for hundreds of tasks. The engineer is usually responsible for fixing or troubleshooting problems with electrical, mechanical or plumbing equipment.
Several websites, including those of the Association of Facility Engineers (AFE), offer news and information on the profession. You can find a sample resume, salary information, and job-related articles on these websites.
Besides these websites, facilities engineers can read books and articles, attend training courses, and network with other engineers. You will need to have excellent organizational skills and an understanding of different engineering and construction disciplines. Also, you must be familiar with building and safety codes.
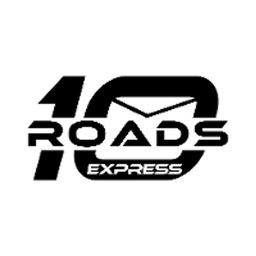
It is important that facilities engineers who are highly skilled can simultaneously analyze data and execute multiple tasks. These engineers need to have a working knowledge of AutoCAD design software and construction techniques like the CAM method. Project management, problem-solving, and critical thinking are all skills that can be beneficial.
One of the biggest advantages of a facilities engineer job is the chance to work with a large array of people. Many of these engineers are trained to work with a variety of different materials and are able to coordinate the work of other engineers.
FAQ
How can overproduction in manufacturing be reduced?
It is essential to find better ways to manage inventory to reduce overproduction. This would reduce the time spent on unproductive activities like purchasing, storing and maintaining excess stock. This will allow us to free up resources for more productive tasks.
You can do this by adopting a Kanban method. A Kanban board is a visual display used to track work in progress. Kanban systems are where work items travel through a series of states until reaching their final destination. Each state has a different priority level.
As an example, if work is progressing from one stage of the process to another, then the current task is complete and can be transferred to the next. But if a task remains in the beginning stages it will stay that way until it reaches its end.
This allows you to keep work moving along while making sure that no work gets neglected. A Kanban board allows managers to monitor how much work is being completed at any given moment. This allows them the ability to adjust their workflow using real-time data.
Lean manufacturing can also be used to reduce inventory levels. Lean manufacturing works to eliminate waste throughout every stage of the production chain. Anything that does not contribute to the product's value is considered waste. Here are some examples of common types.
-
Overproduction
-
Inventory
-
Unnecessary packaging
-
Overstock materials
By implementing these ideas, manufacturers can improve efficiency and cut costs.
How does a Production Planner differ from a Project Manager?
A production planner is more involved in the planning phase of the project than a project manger.
What is the role and responsibility of a Production Planner?
Production planners make sure that every aspect of the project is delivered on-time, within budget, and within schedule. They ensure that the product or service is of high quality and meets client requirements.
What do we need to know about Manufacturing Processes in order to learn more about Logistics?
No. No. However, knowing about manufacturing processes will definitely give you a better understanding of how logistics works.
What does manufacturing industry mean?
Manufacturing Industries are companies that manufacture products. The people who buy these products are called consumers. This is accomplished by using a variety of processes, including production, distribution and retailing. These companies produce goods using raw materials and other equipment. This includes all types manufactured goods such as clothing, building materials, furniture, electronics, tools and machinery.
Statistics
- [54][55] These are the top 50 countries by the total value of manufacturing output in US dollars for its noted year according to World Bank.[56] (en.wikipedia.org)
- (2:04) MTO is a production technique wherein products are customized according to customer specifications, and production only starts after an order is received. (oracle.com)
- In 2021, an estimated 12.1 million Americans work in the manufacturing sector.6 (investopedia.com)
- In the United States, for example, manufacturing makes up 15% of the economic output. (twi-global.com)
- Job #1 is delivering the ordered product according to specifications: color, size, brand, and quantity. (netsuite.com)
External Links
How To
How to Use 5S to Increase Productivity in Manufacturing
5S stands for "Sort", "Set In Order", "Standardize", "Separate" and "Store". Toyota Motor Corporation created the 5S methodology in 1954. It helps companies achieve higher levels of efficiency by improving their work environment.
This approach aims to standardize production procedures, making them predictable, repeatable, and easily measurable. This means that every day tasks such cleaning, sorting/storing, packing, and labeling can be performed. Through these actions, workers can perform their jobs more efficiently because they know what to expect from them.
Five steps are required to implement 5S: Sort, Set In Order, Standardize. Separate. Each step requires a different action to increase efficiency. By sorting, for example, you make it easy to find the items later. Once you have placed items in an ordered fashion, you will put them together. You then organize your inventory in groups. Finally, label all containers correctly.
This process requires employees to think critically about how they do their job. Employees need to understand the reasons they do certain jobs and determine if there is a better way. They will need to develop new skills and techniques in order for the 5S system to be implemented.
The 5S method increases efficiency and morale among employees. As they begin to see improvements, they feel motivated to continue working towards the goal of achieving higher levels of efficiency.