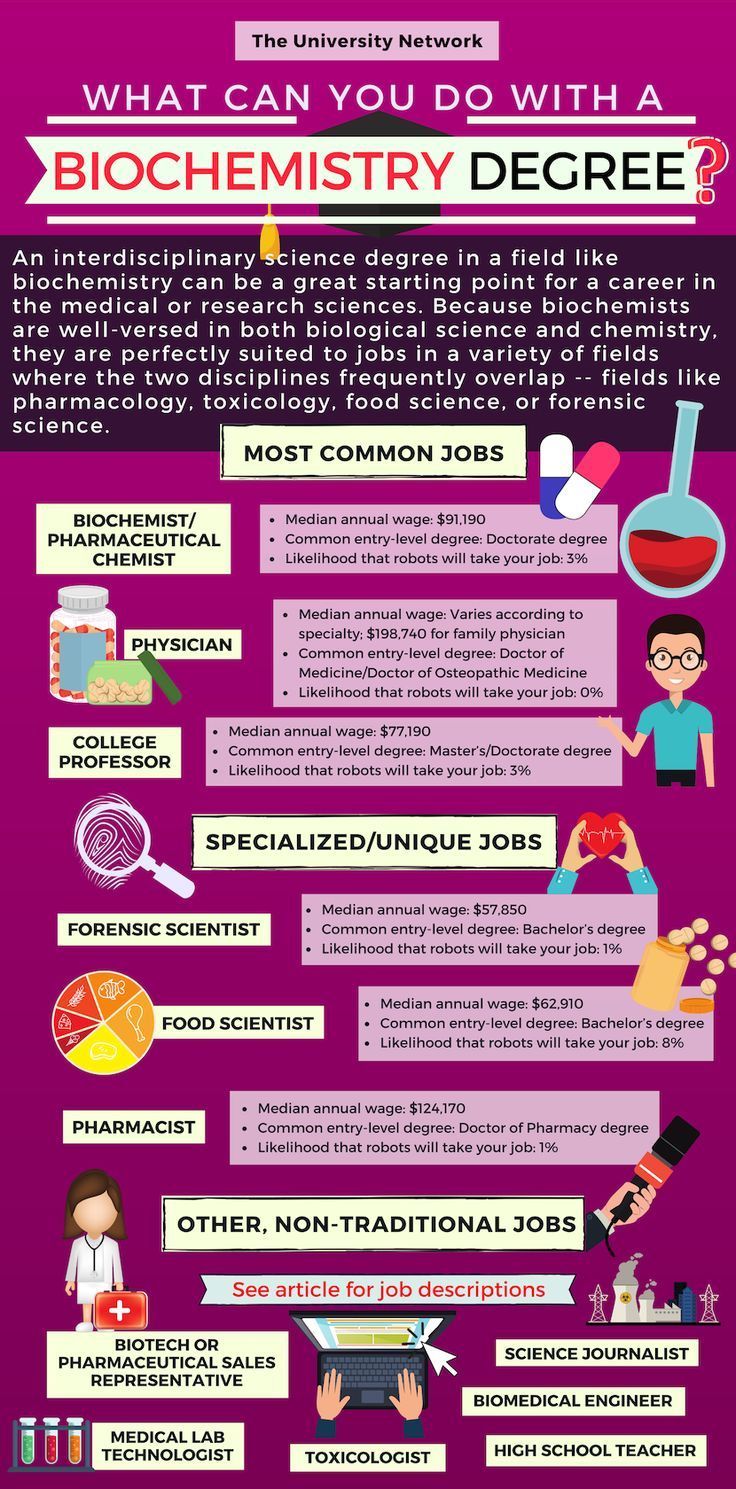
If you're interested in a career in supply chain, you can look into a supply chain entry level salary. One such position is dispatcher. CPSM certification goes beyond ASCM standards. CPSM certification may be an option if your goal is to earn a higher starting income.
CPSM certification, which is a credential that surpasses the ASCM standard, is a credential.
The CPSM certification is a global credential that provides supply chain professionals with the tools necessary to meet the complex challenges of a modern supply chain. The Institute for Supply Management administers it. You must pass three exams and have five years experience in full-time supply chain work. For your CPSM certification to be maintained, you will need 60 credits of continuing educational.
Many employers are seeking a CPSM certificate. Those with this credential have a higher passing rate than those without. The CSCP exam typically takes between three and six months to complete. It's a great tool to demonstrate your knowledge in supply chain management, and also to help you get a job interview. On your LinkedIn profile, it is important to include your certifications.
Obtaining a CPSM Certification can help you secure a career that pays as much as a ASCM entry-level position. Having a CPSM certifies that you have a solid understanding of supply chain operations, and can work with the organization to achieve their goals.
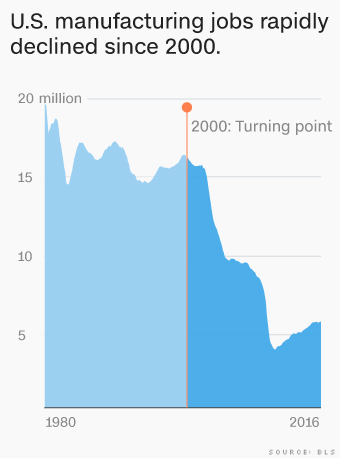
FAQ
How can manufacturing overproduction be reduced?
In order to reduce excess production, you need to develop better inventory management methods. This would reduce the amount of time spent on unnecessary activities such as purchasing, storing, and maintaining excess stock. We could use these resources to do other productive tasks.
This can be done by using a Kanban system. A Kanban board is a visual display used to track work in progress. Kanban systems allow work items to move through different states until they reach their final destination. Each state has a different priority level.
If work is moving from one stage to the other, then the current task can be completed and moved on to the next. If a task is still in its beginning stages, it will continue to be so until it reaches the end.
This allows work to move forward and ensures that no work is missed. With a Kanban board, managers can see exactly how much work is being done at any given moment. This allows them to adjust their workflows based on real-time information.
Lean manufacturing can also be used to reduce inventory levels. Lean manufacturing works to eliminate waste throughout every stage of the production chain. Anything that does nothing to add value to a product is waste. These are some of the most common types.
-
Overproduction
-
Inventory
-
Unnecessary packaging
-
Exceed materials
Manufacturers can increase efficiency and decrease costs by implementing these ideas.
Is automation important in manufacturing?
Not only is automation important for manufacturers, but it's also vital for service providers. They can provide services more quickly and efficiently thanks to automation. It helps them to lower costs by reducing human errors, and improving productivity.
How does a Production Planner differ from a Project Manager?
A production planner is more involved in the planning phase of the project than a project manger.
What are the four types of manufacturing?
Manufacturing is the process by which raw materials are transformed into useful products through machines and processes. It can involve many activities like designing, manufacturing, testing packaging, shipping, selling and servicing.
Why automate your factory?
Automation has become increasingly important in modern warehousing. Increased demand for efficient and faster delivery has resulted in a rise in e-commerce.
Warehouses must be able to quickly adapt to changing demands. To do so, they must invest heavily in technology. The benefits of automating warehouses are numerous. Here are some reasons why it's worth investing in automation:
-
Increases throughput/productivity
-
Reduces errors
-
Accuracy is improved
-
Safety is boosted
-
Eliminates bottlenecks
-
Companies can scale more easily
-
It makes workers more efficient
-
It gives visibility to everything that happens inside the warehouse
-
Enhances customer experience
-
Improves employee satisfaction
-
Reduces downtime and improves uptime
-
Quality products delivered on time
-
Removing human error
-
This helps to ensure compliance with regulations
What are the jobs in logistics?
There are many jobs available in logistics. Here are some examples:
-
Warehouse workers - They load trucks and pallets.
-
Transportation drivers: They drive trucks and trailers and deliver goods and make pick-ups.
-
Freight handlers are people who sort and pack freight into warehouses.
-
Inventory managers - These are responsible for overseeing the stock of goods in warehouses.
-
Sales representatives - They sell products.
-
Logistics coordinators - They plan and organize logistics operations.
-
Purchasing agents: They are responsible for purchasing goods and services to support company operations.
-
Customer service representatives – They answer emails and phone calls from customers.
-
Shippers clerks - They process shipping order and issue bills.
-
Order fillers - These people fill orders based on what has been ordered.
-
Quality control inspectors (QCI) - They inspect all incoming and departing products for potential defects.
-
Others - There is a variety of other jobs in logistics. These include transportation supervisors and cargo specialists.
What are the main products of logistics?
Logistics refers to all activities that involve moving goods from A to B.
They cover all aspects of transportation, such as packing, loading, transporting and unloading.
Logisticians make sure that the right product arrives at the right place at the correct time and in safe conditions. They provide information on demand forecasts as well stock levels, production schedules and availability of raw material.
They also keep track of shipments in transit, monitor quality standards, perform inventories and order replenishment, coordinate with suppliers and vendors, and provide support services for sales and marketing.
Statistics
- Many factories witnessed a 30% increase in output due to the shift to electric motors. (en.wikipedia.org)
- According to the United Nations Industrial Development Organization (UNIDO), China is the top manufacturer worldwide by 2019 output, producing 28.7% of the total global manufacturing output, followed by the United States, Japan, Germany, and India.[52][53] (en.wikipedia.org)
- In 2021, an estimated 12.1 million Americans work in the manufacturing sector.6 (investopedia.com)
- In the United States, for example, manufacturing makes up 15% of the economic output. (twi-global.com)
- It's estimated that 10.8% of the U.S. GDP in 2020 was contributed to manufacturing. (investopedia.com)
External Links
How To
Six Sigma: How to Use it in Manufacturing
Six Sigma refers to "the application and control of statistical processes (SPC) techniques in order to achieve continuous improvement." Motorola's Quality Improvement Department, Tokyo, Japan, developed it in 1986. Six Sigma's core idea is to improve the quality of processes by standardizing and eliminating defects. This method has been adopted by many companies in recent years as they believe there are no perfect products or services. The main goal of Six Sigma is to reduce variation from the mean value of production. This means that you can take a sample from your product and then compare its performance to the average to find out how often the process differs from the norm. If there is a significant deviation from the norm, you will know that something needs to change.
Understanding the nature of variability in your business is the first step to Six Sigma. Once you understand this, you can then identify the causes of variation. It is important to identify whether the variations are random or systemic. Random variations occur when people make mistakes; systematic ones are caused by factors outside the process itself. Random variations would include, for example, the failure of some widgets to fall from the assembly line. However, if you notice that every time you assemble a widget, it always falls apart at exactly the same place, then that would be a systematic problem.
Once you identify the problem areas, it is time to create solutions. That solution might involve changing the way you do things or redesigning the process altogether. Test them again once you've implemented the changes. If they didn't work, then you'll need to go back to the drawing board and come up with another plan.