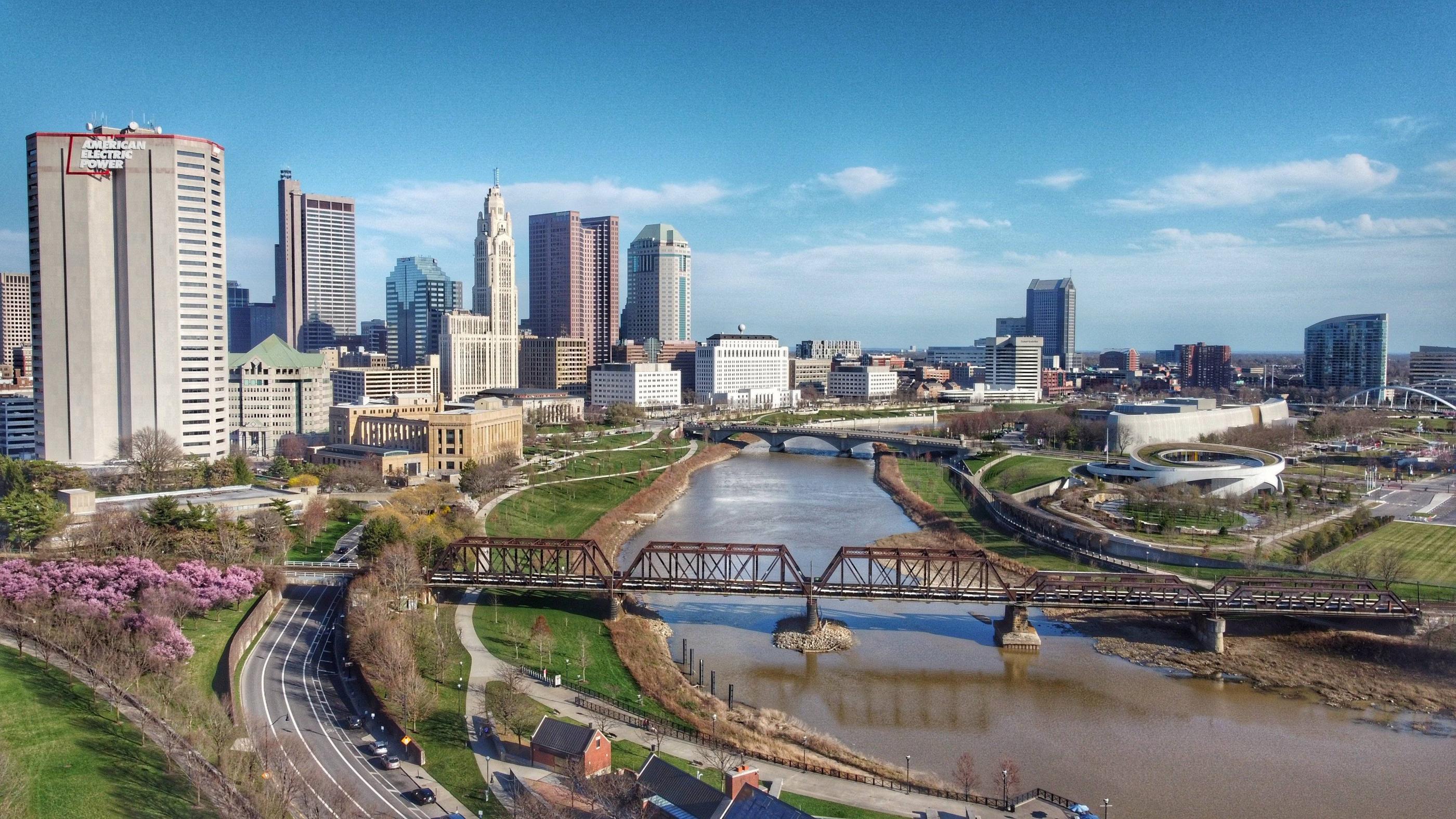
Mexico was one the major actors in DVA's trade network for global manufacturing exports, during the period under analysis. Compared to the textiles industry, which is a more important export sector, the automotive industry has not followed the same path. Both industries are still important for Mexico's job generation and are therefore considered to be key players in Mexico’s export market.
The Mexican auto industry is one the largest suppliers of American parts. It is also one of the fastest growing industries in Mexico. It has not been capable of bringing the rest on a rapid expansion trajectory. In fact, the automotive industry is undergoing a transition from a domestic-oriented industry to a regional auto parts/automobile chain. This transition is driven by a combination foreign direct investment and regional processes.
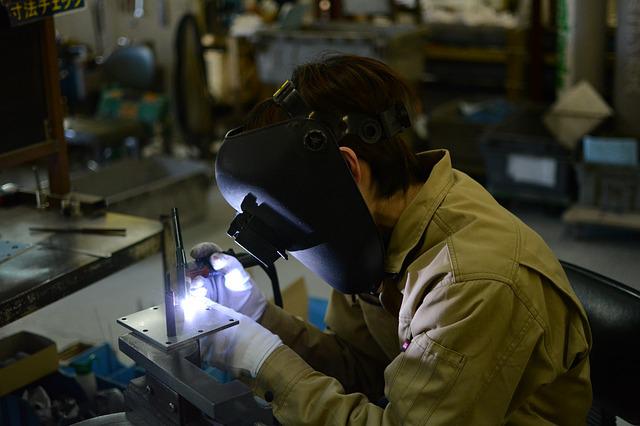
Mexico's special programs for development have been a boon to the automotive industry. It has been the top supplier of auto parts in the U.S. and has seen remarkable growth on international markets. It has also benefited from foreign investment, which has been a key factor in its rise in global value chains.
The Mexican automobile industry is also a key participant in the GVCs Europe and America. Mexico's automotive industry was a major part of its economy in the 1970s and 1980s. But it has not had the same penetration into the world market as textiles. It has also not seen significant growth in its output but has been able to penetrate the global market.
The framework of decent work indicators created by the International Labour Organization is used to analyze the relationship between Mexican international trade and labor in the country's manufacturing sector. The indicators are based upon official data and take into account the connections between Mexican labour regulations and trade agreements. The indicators include an input-output analysis on international trade. This shows that Mexico is a minor player in the value-added domestic manufacturing exports.
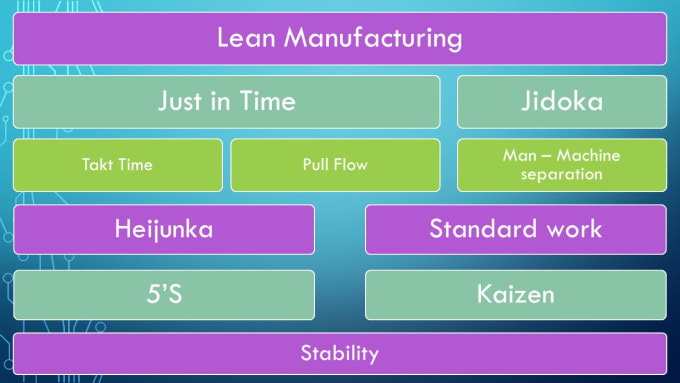
The study also examines how trade liberalization affects employment in Mexico's manufacturing industry. The System of National Accounts (SNA), framework is used to create a set of indicators that indicate decent work for two Mexican industrial activities: textiles and transport equipment. These indicators are compiled into a time series and used to analyze the Mexican evolution of decent employment. The study found that the level D V A V C in Mexico's manufacturing sector is much lower than the textile sector. In the same way, the study found that the level for employment in automobile industry is lower then in the textile. The study also indicates that real wages have decreased in the past year. Also, the nominal wage adjustment wasn't enough to compensate the decline in real earnings. The study finds that the level of DVA in transport equipment exports has increased in the past decade, while the level of DVA in textile exports has decreased.
FAQ
How can I find out more about manufacturing?
You can learn the most about manufacturing by getting involved in it. You can also read educational videos or take classes if this isn't possible.
How can manufacturing overproduction be reduced?
It is essential to find better ways to manage inventory to reduce overproduction. This would decrease the time that is spent on inefficient activities like purchasing, storing, or maintaining excess stock. By doing this, we could free up resources for other productive tasks.
Kanban systems are one way to achieve this. A Kanban board, a visual display to show the progress of work, is called a Kanban board. A Kanban system allows work items to move through several states before reaching their final destination. Each state represents an individual priority level.
To illustrate, work can move from one stage or another when it is complete enough for it to be moved to a new stage. If a task is still in its beginning stages, it will continue to be so until it reaches the end.
This allows you to keep work moving along while making sure that no work gets neglected. With a Kanban board, managers can see exactly how much work is being done at any given moment. This allows them the ability to adjust their workflow using real-time data.
Another way to control inventory levels is to implement lean manufacturing. Lean manufacturing seeks to eliminate waste from every step of the production cycle. Anything that does nothing to add value to a product is waste. There are several types of waste that you might encounter:
-
Overproduction
-
Inventory
-
Packaging that is not necessary
-
Material surplus
Manufacturers can reduce their costs and improve their efficiency by using these ideas.
What makes a production planner different from a project manger?
A production planner is more involved in the planning phase of the project than a project manger.
What is the distinction between Production Planning or Scheduling?
Production Planning (PP), also known as forecasting and identifying production capacities, is the process that determines what product needs to be produced at any particular time. This is done through forecasting demand and identifying production capacities.
Scheduling is the process of assigning specific dates to tasks so they can be completed within the specified timeframe.
What are the 7 Rs of logistics?
The 7R's of Logistics is an acronym for the seven basic principles of logistics management. It was developed by International Association of Business Logisticians (IABL), and published as part of their "Seven Principles of Logistics Management Series" in 2004.
The acronym consists of the following letters:
-
Responsible - to ensure that all actions are within the legal requirements and are not detrimental to others.
-
Reliable - have confidence in the ability to deliver on commitments made.
-
Reasonable - make sure you use your resources well and don't waste them.
-
Realistic - Take into consideration all aspects of operations including cost-effectiveness, environmental impact, and other factors.
-
Respectful - show respect and treat others fairly and fairly
-
Responsive - Look for ways to save time and increase productivity.
-
Recognizable - Provide value-added services to customers
What does manufacturing mean?
Manufacturing Industries refers to businesses that manufacture products. The people who buy these products are called consumers. These companies use a variety processes such as distribution, retailing and management to accomplish their purpose. They produce goods from raw materials by using machines and other machinery. This includes all types manufactured goods such as clothing, building materials, furniture, electronics, tools and machinery.
Statistics
- In 2021, an estimated 12.1 million Americans work in the manufacturing sector.6 (investopedia.com)
- [54][55] These are the top 50 countries by the total value of manufacturing output in US dollars for its noted year according to World Bank.[56] (en.wikipedia.org)
- According to the United Nations Industrial Development Organization (UNIDO), China is the top manufacturer worldwide by 2019 output, producing 28.7% of the total global manufacturing output, followed by the United States, Japan, Germany, and India.[52][53] (en.wikipedia.org)
- It's estimated that 10.8% of the U.S. GDP in 2020 was contributed to manufacturing. (investopedia.com)
- (2:04) MTO is a production technique wherein products are customized according to customer specifications, and production only starts after an order is received. (oracle.com)
External Links
How To
Six Sigma in Manufacturing
Six Sigma is defined by "the application SPC (statistical process control) techniques to achieve continuous improvements." Motorola's Quality Improvement Department created Six Sigma at their Tokyo plant, Japan in 1986. Six Sigma's core idea is to improve the quality of processes by standardizing and eliminating defects. Many companies have adopted Six Sigma in recent years because they believe that there are no perfect products and services. The main goal of Six Sigma is to reduce variation from the mean value of production. This means that if you take a sample of your product, then measure its performance against the average, you can find out what percentage of the time the process deviates from the norm. If you notice a large deviation, then it is time to fix it.
The first step toward implementing Six Sigma is understanding how variability works in your business. Once you have a good understanding of the basics, you can identify potential sources of variation. These variations can also be classified as random or systematic. Random variations occur when people make mistakes; systematic ones are caused by factors outside the process itself. These are, for instance, random variations that occur when widgets are made and some fall off the production line. But if you notice that every widget you make falls apart at the exact same place each time, this would indicate that there is a problem.
Once you've identified where the problems lie, you'll want to design solutions to eliminate those problems. It might mean changing the way you do business or redesigning it entirely. You should then test the changes again after they have been implemented. If they don't work, you will need to go back to the drawing boards and create a new plan.