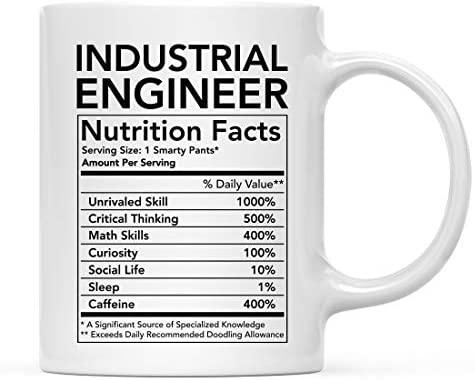
If you're interested in a supply chain management career, you can start by researching industries that offer good opportunities. It is important to research the industry to see how many people are employed in it, what skills they have, and what jobs are available. If you're looking for a job, recruiters or human resource specialists can help. You can join a professional organization to learn more about certifications, depending on your goals.
Supply chain management is an exciting field that requires a variety of skills. It can be a difficult and complicated career but it is extremely rewarding. There is a lot to do and lots of opportunity. You can also use all of your skills in different industries.
Logistics and supply-chain managers need skills in critical thinking and project management as well as interpersonal communication and sustainability. In addition, they must be able to effectively communicate with stakeholders at all levels of an organization. They must be able understand and implement international regulations as well as new technologies.
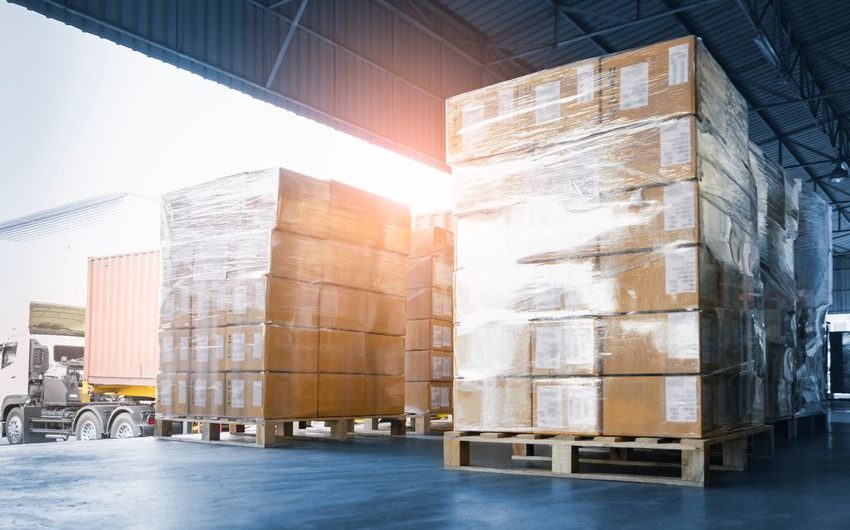
Many companies today take a broader view of their supply chains. This means that not every supply chain model is right for you. Large companies might offer multiple product lines for you to work on. Smaller, family-owned businesses might offer fewer career opportunities. Your satisfaction may also depend on the size of the company.
You'll need to establish a strong networking network to get started. Get to know HR and supply chain management professionals, and read up on the industries that interest you. Once you've established a solid network, you can look for a supply chain job. Most supply chain jobs are competitive, and you'll have to show that you have the requisite expertise and experience.
Supply chain management is a fast-paced, unpredictable field. It is important to be flexible, and to be able to solve problems quickly. By working through problems as quickly as possible, you can prevent disruptions to your supply chain and safeguard the goals of your organization.
As part of a supply chain career, you will also be responsible for collecting and organizing data. This is an essential asset for making effective decisions and allocating team resources. For all processes involved in serving customers, data collection and management must be done well.
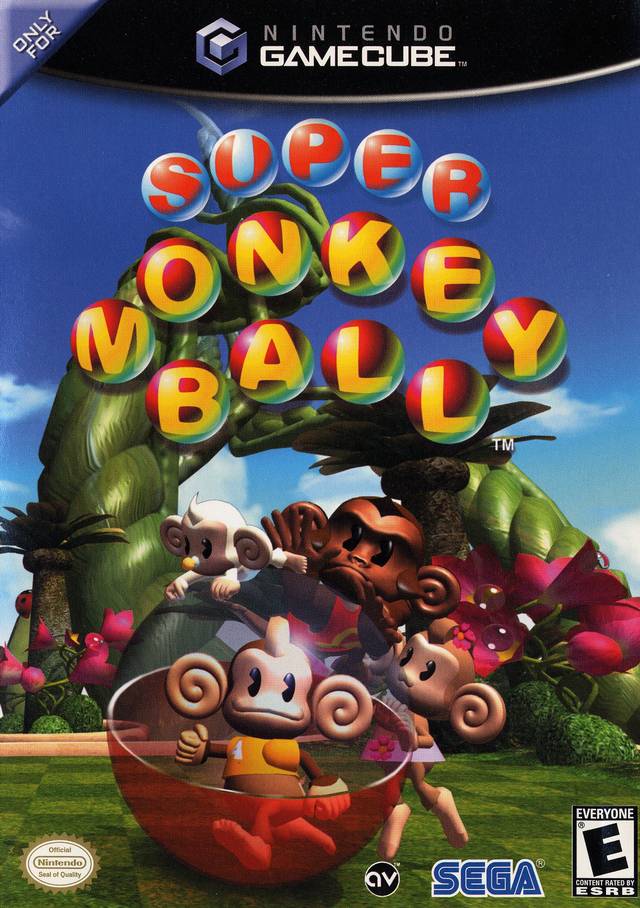
Supply chain managers should also be able to manage projects and oversee finances. While they might be tasked with managing multiple projects at once, they should be able to prioritize them and decide which ones are most important. They'll need the ability to weigh both the benefits and disadvantages of each decision.
If you are interested in a career as a supply chain manager, there are positions available in healthcare, transport, manufacturing, food service, and retail. These positions can vary in salary and employment. However, each industry requires a certain amount of professional experience.
You can consider many different jobs in supply chain management. It is a fast-growing field. Consider what you enjoy about working with people, and how you can leverage that into a career in this fast-paced field.
FAQ
What jobs are available in logistics?
There are many kinds of jobs available within logistics. Some of them are:
-
Warehouse workers: They load and unload trucks, pallets, and other cargo.
-
Transportation drivers: They drive trucks and trailers and deliver goods and make pick-ups.
-
Freight handlers are people who sort and pack freight into warehouses.
-
Inventory managers - They oversee the inventory of goods in warehouses.
-
Sales representatives - They sell products.
-
Logistics coordinators: They plan and manage logistics operations.
-
Purchasing agents – They buy goods or services necessary to run a company.
-
Customer service representatives - They answer calls and emails from customers.
-
Shipping clerks - They process shipping orders and issue bills.
-
Order fillers – They fill orders based upon what was ordered and shipped.
-
Quality control inspectors: They inspect outgoing and incoming products for any defects.
-
Others - There are many types of jobs in logistics such as transport supervisors and cargo specialists.
What are the responsibilities for a manufacturing manager
A manufacturing manager has to ensure that all manufacturing processes work efficiently and effectively. They should also be aware and responsive to any company problems.
They should also learn how to communicate effectively with other departments, including sales and marketing.
They must also keep up-to-date with the latest trends in their field and be able use this information to improve productivity and efficiency.
What is the role of a logistics manager
A logistics manager ensures that all goods are delivered on time and without damage. This is done using his/her knowledge of the company's products. He/she must also ensure sufficient stock to meet the demand.
What are the 7 Rs of logistics.
The acronym 7Rs of Logistics refers to the seven core principles of logistics management. It was developed and published by the International Association of Business Logisticians in 2004 as part of the "Seven Principles of Logistics Management".
The acronym is composed of the following letters.
-
Responsible - ensure that actions are in compliance with legal requirements and do not cause harm to others.
-
Reliable: Have faith in your ability or the ability to honor any promises made.
-
Be responsible - Use resources efficiently and avoid wasting them.
-
Realistic – Consider all aspects, including cost-effectiveness as well as environmental impact.
-
Respectful – Treat others fairly and equitably.
-
Responsive - Look for ways to save time and increase productivity.
-
Recognizable - provide customers with value-added services.
How important is automation in manufacturing?
Automating is not just important for manufacturers, but also for service providers. It allows them to offer services faster and more efficiently. It also helps to reduce costs and improve productivity.
How does a Production Planner differ from a Project Manager?
A production planner is more involved in the planning phase of the project than a project manger.
How can manufacturing reduce production bottlenecks?
Production bottlenecks can be avoided by ensuring that processes are running smoothly during the entire production process, starting with the receipt of an order and ending when the product ships.
This includes planning to meet capacity requirements and quality control.
This can be done by using continuous improvement techniques, such as Six Sigma.
Six Sigma is a management method that helps to improve quality and reduce waste.
It emphasizes consistency and eliminating variance in your work.
Statistics
- In 2021, an estimated 12.1 million Americans work in the manufacturing sector.6 (investopedia.com)
- [54][55] These are the top 50 countries by the total value of manufacturing output in US dollars for its noted year according to World Bank.[56] (en.wikipedia.org)
- According to the United Nations Industrial Development Organization (UNIDO), China is the top manufacturer worldwide by 2019 output, producing 28.7% of the total global manufacturing output, followed by the United States, Japan, Germany, and India.[52][53] (en.wikipedia.org)
- Job #1 is delivering the ordered product according to specifications: color, size, brand, and quantity. (netsuite.com)
- (2:04) MTO is a production technique wherein products are customized according to customer specifications, and production only starts after an order is received. (oracle.com)
External Links
How To
Six Sigma and Manufacturing
Six Sigma refers to "the application and control of statistical processes (SPC) techniques in order to achieve continuous improvement." Motorola's Quality Improvement Department, Tokyo, Japan, developed it in 1986. Six Sigma's main goal is to improve process quality by standardizing processes and eliminating defects. This method has been adopted by many companies in recent years as they believe there are no perfect products or services. The main goal of Six Sigma is to reduce variation from the mean value of production. This means that you can take a sample from your product and then compare its performance to the average to find out how often the process differs from the norm. If there is a significant deviation from the norm, you will know that something needs to change.
Understanding the dynamics of variability within your business is the first step in Six Sigma. Once you understand that, it is time to identify the sources of variation. You'll also want to determine whether these variations are random or systematic. Random variations occur when people do mistakes. Symmetrical variations are caused due to factors beyond the process. These are, for instance, random variations that occur when widgets are made and some fall off the production line. But if you notice that every widget you make falls apart at the exact same place each time, this would indicate that there is a problem.
After identifying the problem areas, you will need to devise solutions. The solution could involve changing how you do things, or redesigning your entire process. Test them again once you've implemented the changes. If they don't work, you will need to go back to the drawing boards and create a new plan.