
A bachelor's degree is required to get a job in safety engineering. In addition to the education, you need to be able to work well with others. Additional certifications may be required.
You will learn about the different regulations and procedures that safety engineers must follow during training. Additionally, you will learn how to identify hazards and investigate accidents. You will be able to evaluate and test machinery, buildings and consumer products. You will also develop safety protocols and prepare reports. You will learn how to conduct routine compliance inspections and prepare health and safety programs for workers.
A safety engineer usually works under the supervision and guidance of a more experienced engineer. You might also consider joining professional safety engineering networks, such as American Society of Safety Professionals. This is a good way to build contacts in your field. This can be a great opportunity to learn from and meet safety engineers. Keep your resume current with your qualifications if you plan to become a safety engineer.
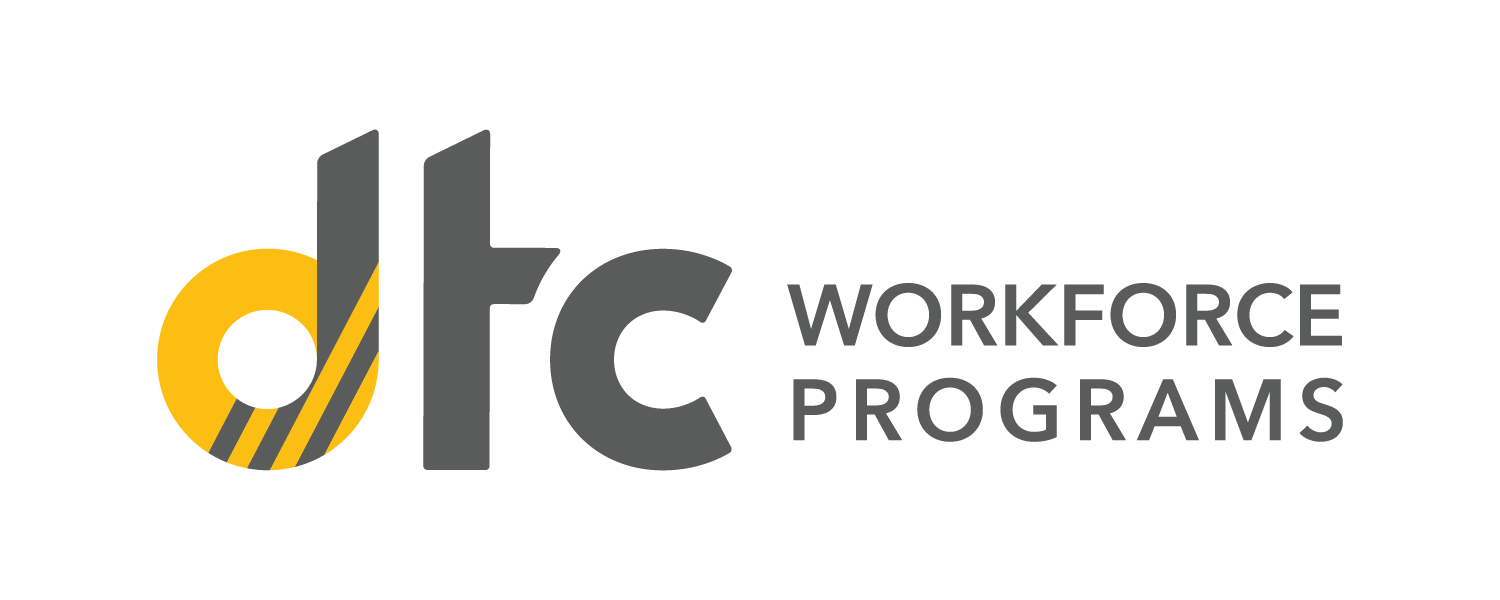
Once you have completed your bachelor's degree, you may want to consider getting a master's degree in health and safety. This will make you more competitive in the job market. Your master's degree can be used to advance in your field.
Your master's program will teach you how to create safety systems and implement organizational-wide procedures. You will also learn advanced planning and analytical skills. This will equip you with the skills to manage more complicated projects and help you move up the ladder. To apply for managerial positions in safety or health, you can use your master's.
Cooperative education is offered by many colleges and universities. These programs give you the chance to earn a bachelor’s degree and get practical experience. This allows you to apply for jobs that are more difficult to get without the degree. Many of these programs allow students to take part-time classes, while others allow them to work full time while they earn their degree.
A bachelor's degree is not enough. You will also need a license to work as safety engineer in your state. A license can be obtained from most states. To obtain a license, you will need to pass the state examination and four years of relevant work experience. You might also need to complete a course on workplace health.
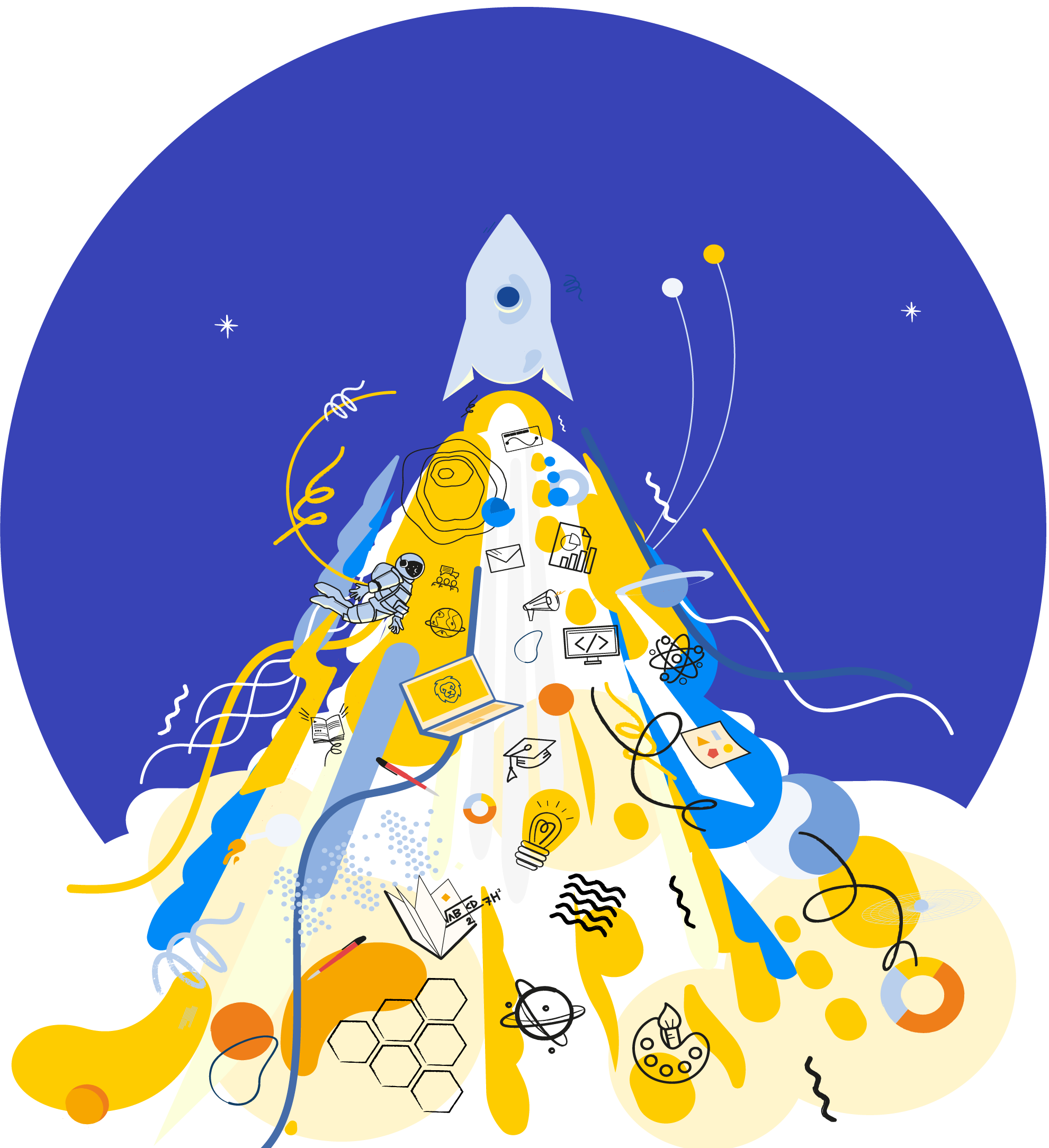
Once you are licensed, you may find that employers prefer to hire candidates with practical experience. Many schools offer programs that allow students to study part-time or cooperative education. Online job search is also possible. You might be interested in joining professional organizations, like the American Society of Safety Engineers. You may also want to join the Institute of Hazardous Materials Management. This helps safety professionals gain leadership skills.
The exciting career of safety and health engineer is one that many people are interested in. It requires excellent skills in math, science, and communication. You also need to be innovative and have a knack for solving difficult problems.
FAQ
What is it like to manage a logistics company?
To be a successful businessman in logistics, you will need many skills and knowledge. You must have good communication skills to interact effectively with your clients and suppliers. You will need to know how to interpret data and draw conclusions. You must be able to work well under pressure and handle stressful situations. To improve efficiency, you must be innovative and creative. You will need strong leadership skills to motivate and direct your team members towards achieving their organizational goals.
You must be organized to meet tight deadlines.
What is the best way to learn about manufacturing?
Practical experience is the best way of learning about manufacturing. However, if that's not possible, you can always read books or watch educational videos.
What are manufacturing & logistics?
Manufacturing refers the process of producing goods from raw materials through machines and processes. Logistics includes all aspects related to supply chain management, such as procurement, distribution planning, inventory control and transportation. Manufacturing and logistics can often be grouped together to describe a larger term that covers both the creation of products, and the delivery of them to customers.
How can manufacturing efficiency be improved?
First, we need to identify which factors are most critical in affecting production times. The next step is to identify the most important factors that affect production time. If you don’t know how to start, look at which factors have the greatest impact upon production time. Once you've identified them, try to find solutions for each of those factors.
Statistics
- You can multiply the result by 100 to get the total percent of monthly overhead. (investopedia.com)
- It's estimated that 10.8% of the U.S. GDP in 2020 was contributed to manufacturing. (investopedia.com)
- In 2021, an estimated 12.1 million Americans work in the manufacturing sector.6 (investopedia.com)
- According to the United Nations Industrial Development Organization (UNIDO), China is the top manufacturer worldwide by 2019 output, producing 28.7% of the total global manufacturing output, followed by the United States, Japan, Germany, and India.[52][53] (en.wikipedia.org)
- Many factories witnessed a 30% increase in output due to the shift to electric motors. (en.wikipedia.org)
External Links
How To
How to Use the 5S to Increase Productivity In Manufacturing
5S stands for "Sort", "Set In Order", "Standardize", "Separate" and "Store". Toyota Motor Corporation created the 5S methodology in 1954. It allows companies to improve their work environment, thereby achieving greater efficiency.
This method aims to standardize production processes so that they are repeatable, measurable and predictable. It means tasks like cleaning, sorting or packing, labeling, and storing are done every day. Workers can be more productive by knowing what to expect.
Implementing 5S requires five steps. These are Sort, Set In Order, Standardize. Separate. And Store. Each step requires a different action, which increases efficiency. By sorting, for example, you make it easy to find the items later. You arrange items by placing them in an order. After you have divided your inventory into groups you can store them in easy-to-reach containers. Labeling your containers will ensure that everything is correctly labeled.
Employees need to reflect on how they do their jobs. Employees need to understand the reasons they do certain jobs and determine if there is a better way. To be successful in the 5S system, employees will need to acquire new skills and techniques.
The 5S method not only increases efficiency but also boosts morale and teamwork. Once they start to notice improvements, they are motivated to keep working towards their goal of increasing efficiency.